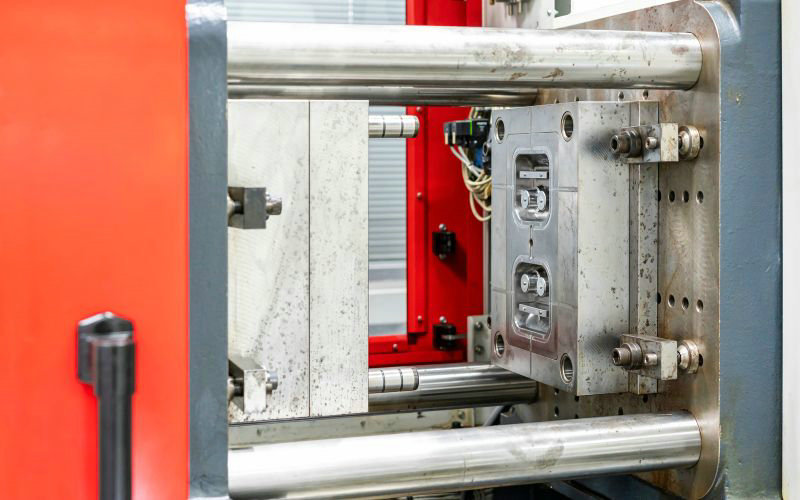
Klassifizierung von Spritzgussformen
Wenn Sie Spritzgussformen beurteilen, ist es wichtig, die Klassifizierungs-System das unterscheidet ihre Fähigkeiten und Anwendungen. In diesem Artikel bieten wir Ihnen einen einfachen Leitfaden zum Verständnis verschiedener Formentypen:
- Von Geometrie
- Von Anzahl der Kavitäten
- Von Formplatte
- Von Auswurfprinzip
- Von Plastik
- Von Fütterungssystem
Ihre Wahl unter diesen Arten von Spritzgussformen hängt häufig vom Umfang Ihres Projekts, der Komplexität der Teile und den Betriebskosten ab. Lassen Sie uns gemeinsam verschiedene Arten von Kunststoff-Spritzgussformen erkunden!
Nach Geometrie
- Einfache Geometrien:
- Einfacher zu entwerfen und herzustellen.
- Haben oft weniger Hohlprofile.
- Komplexe Geometrien:
- Ermöglicht eine größere Flexibilität beim Design.
- Kann Hohlprofile aufnehmen, die für bestimmte Funktionen benötigt werden.
Komplexe Teile enthalten oft Merkmale wie Hinterschnitte, also Vertiefungen oder Vorsprünge, die das Formendesign erschweren können. Das Design für Hinterschnitte erfordert sorgfältige Überlegungen, um sicherzustellen, dass sich die Formenkomponenten während der Auswerfphase richtig trennen können, ohne das Teil zu beschädigen.
Bei komplizierten Komponentendesigns kann der Einsatz moderner Formtechnologien wie Schiebern oder Hebern erforderlich sein, um das Teil erfolgreich herzustellen und aus der Form zu lösen. Dieser Ansatz bietet zwar eine hohe Designflexibilität, erhöht jedoch auch die Komplexität und die Kosten der Form.
Ihre Entscheidung zwischen einer einfachen oder komplexen Formgeometrie hängt letztendlich vom gewünschten Teiledesign, der Funktionalität, der Durchführbarkeit des Formherstellungsprozesses und dem Projektbudget ab. Wägen Sie den Bedarf an komplexen Geometrien immer gegen praktische Produktionsüberlegungen ab.
Nach Anzahl der Hohlräume
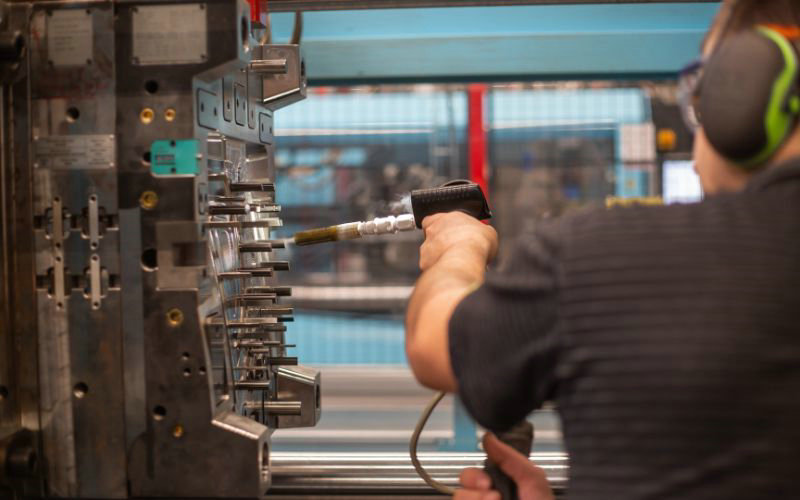
Einzelkavitätenformen
- Produzieren Sie nur ein Produkt pro Spritzzyklus
- Ideal für große, komplexe oder kleinvolumige Teile
- Konzentrieren Sie sich stärker auf einzelne Teile, um Defekte zu minimieren
- Geringere Werkzeugkosten im Vergleich zu Mehrfachformen für dasselbe Teil
- Geeignet für Prototyping und die Bereitstellung neuer Designs
Mehrfach-Werkzeuge
- Enthält mehrere identische Hohlräume, um mehrere Teile pro Zyklus herzustellen
- Ermöglichen Sie kürzere Vorlaufzeiten und eine höhere Produktionseffizienz bei hohen Stückzahlen
- Reduzieren Sie die Stückkosten bei großen Chargen
- Erfordert eine sorgfältige Konstruktion, um eine gleichmäßige Füllung und gleichbleibende Qualität in allen Hohlräumen sicherzustellen
- Möglicherweise sind die anfänglichen Werkzeugkosten höher als bei Einzelkavitätenformen
- Die typische Kavitätenanzahl reicht von 2 bis 64 oder mehr, je nach Teilegröße und Anwendung
Familienformen
- Integrieren Sie mehrere Hohlräume mit unterschiedlichen Formen, um verschiedene Teile in einem Zyklus herzustellen
- Ermöglichen Sie das Formen verwandter Komponenten oder Produktvarianten in einem einzigen Schuss
- Nützlich für die Prototypenentwicklung oder die Herstellung von Bausätzen mit verschiedenen Teilen
- Beschränkt auf Teile aus gleichem Material und gleicher Farbe
- Aufgrund unterschiedlicher Kavitätengeometrien kommt es häufig zu einer ungleichmäßigen Füllung, was das Defektrisiko erhöht
- Erfordert mehr Arbeit nach dem Formen, um verschiedene Teile zu trennen und zu handhaben
Durch Formplatte
Zwei-Platten-Spritzgussform
- Einfachste und gebräuchlichste Spritzgussformkonstruktion, bestehend aus zwei Hauptteilen (A-Seite und B-Seite)
- Verfügt über eine einzige Trennlinie, an der sich die Form in zwei Hälften teilt
- Die Hohlraumseite ist fest, während die Kernseite während des Formprozesses beweglich ist
- Angusskanal und Teil liegen auf der gleichen Trennebene und werden gemeinsam ausgeworfen
- Vorteile: geringere Kosten, kürzere Zykluszeiten, einfachere Einrichtung und Bedienung
- Nachteile: geringere Flexibilität bei der Angusspositionierung, manuelles Delegieren erforderlich, Risiko von Fehlschüssen bei Mehrfachformen
Drei-Platten-Spritzgussform
- Auch als Abstreifplattenform bekannt, besteht aus zwei Trennebenen und teilt sich in drei Abschnitte
- Verfügt über eine zusätzliche schwimmende Platte zwischen Hohlraum und Kern zur Aufnahme des Angusssystems
- Ermöglicht die automatische Entgasung des Angusskanals vom Bauteil
- Bietet mehr Flexibilität bei der Angussposition im Vergleich zu Zweiplattenformen
- Vorteile: geeignet für große Teile, die mehrere Tore erfordern, ermöglicht automatisches Diskutieren
- Nachteile: komplexer und teurer, längere Zykluszeiten, weniger stabil durch mehr bewegliche Teile
Stapel-Spritzgussform
- Spezieller Formaufbau mit mehreren Trennflächen, die jeweils eine oder mehrere Kavitäten aufnehmen
- Besteht aus einer beweglichen Form, einer mittleren Form und einer festen Form, die sich gleichzeitig öffnen
- Kann die Leistung einer Standardform verdoppeln, ohne dass zusätzliche Maschinen erforderlich sind
- Geeignet für die Großserienfertigung flacher, dünnwandiger Teile
- Vorteile: deutlich gesteigerte Produktivität, reduzierte Kosten, kürzere Fertigungszeiten
- Nachteile: komplexeres Design, erfordert sorgfältiges Ausbalancieren der Hohlraumfüllung und der Kühlung
Nach dem Auswurfprinzip
1. Stiftauswurf
- Verwendet Auswerferstifte, um das Formteil aus der Formhöhle zu drücken
- Die Stifte befinden sich in der Auswerferhälfte der Form und sind so konstruiert, dass sie den Auswerferkräften standhalten
- Stiftdurchmesser, Länge, Material, Platzierung und Form sind wichtige Designüberlegungen
- Geeignet für die meisten Spritzgussteile, kann aber sichtbare Spuren am Auswerferstift hinterlassen
2. Hülsenauswurf
- Verwendet einen hülsenförmigen Auswerfer, der den Kern umgibt, um das Teil auszuwerfen
- Sorgt für gleichmäßige und stabile Auswurfkraft, ohne sichtbare Spuren zu hinterlassen
- Geeignet für zylindrische, dünnwandige oder schalenförmige Produkte
- Komplexer und teurer als die Stiftauswurftechnik
3. Auswurf der Abstreifplatte
- Verwendet eine Abstreifplatte, um das Teil vom Kern abzustoßen
- Die Auswurfkraft ist hoch, gleichmäßig und stabil, wodurch die Verformung der Teile minimiert wird
- Ideal für zylindrische Teile, dünnwandige Behälter und schalenförmige Produkte
- Vermeidet sichtbare Auswerferspuren, hat jedoch eine komplexere Formstruktur und höhere Kosten
4. Klingenauswurf
- Verwendet rechteckige Auswerferklingen anstelle von Stiften
- Geeignet für Teile mit speziellen Geometrien oder Anforderungen
5. Luftausstoß
- Führt Druckluft zwischen Teil und Form ein, um das Teil auszuwerfen
- Vereinfacht den Formaufbau und ermöglicht das Entformen an jeder beliebigen Stelle
- Wird häufig zur Unterstützung anderer Auswerfermethoden für große, tiefe oder dünnwandige Teile verwendet
6. Heberauswurf
- Verwendet Heber, die sich seitlich bewegen, um Hinterschnitte oder interne Merkmale freizugeben
- Ermöglicht das Auswerfen von Teilen mit komplexen Geometrien oder Seitenbewegungen
Nach Kunststoffmaterial
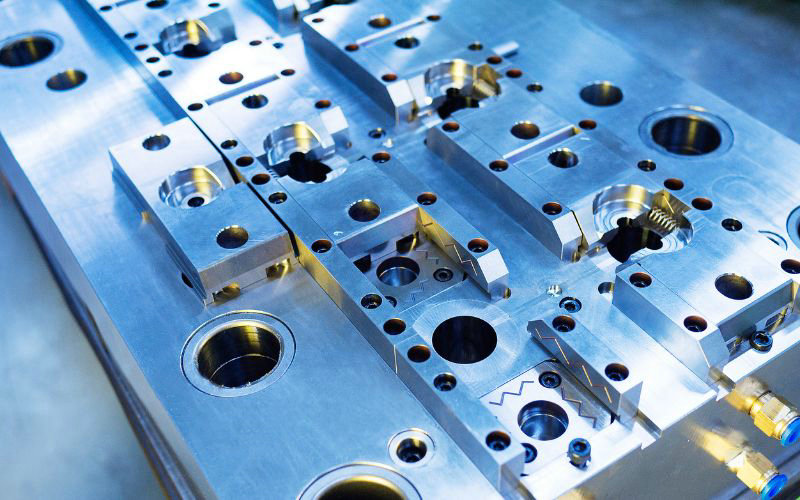
1. Acryl (PMMA)
- Starker, klarer Thermoplast mit ausgezeichneter optischer Klarheit und UV-Beständigkeit
- Leichte und bruchfeste Alternative zu Glas
- Wird für Linsen, Displays, Schilder und medizinische Geräte verwendet
2. Acrylnitril-Butadien-Styrol (ABS)
- Robuster, starrer und schlagfester Thermoplast
- Gute chemische Beständigkeit und leicht zu überstreichen oder zu verkleben.
- Wird für Autoteile, Haushaltsgeräte, Spielzeug und Elektronikgehäuse verwendet
3. Nylon (Polyamid, PA)
- Starker, flexibler und verschleißfester Thermoplast
- Hoher Schmelzpunkt und gute chemische Beständigkeit
- Wird für Autoteile, Zahnräder, Lager und elektrische Komponenten verwendet
4. Polycarbonat (PC)
- Robuster, transparenter und hitzebeständiger Thermoplast
- Gute Dimensionsstabilität und elektrische Isoliereigenschaften
- Wird für Automobilkomponenten, medizinische Geräte und Schutzbrillen verwendet
5. Polyethylen (PE)
- Leichter, flexibler und chemikalienbeständiger Thermoplast
- Varianten mit hoher Dichte (HDPE) und niedriger Dichte (LDPE) erhältlich
- Wird für Verpackungen, Behälter, Spielzeug und Automobilkomponenten verwendet
6. Polyoxymethylen (POM)
- Starker, starrer und formstabiler Thermoplast
- Ausgezeichnete Verschleiß- und Chemikalienbeständigkeit
- Wird für Zahnräder, Lager und Präzisionsteile verwendet
7. Polypropylen (PP)
- Leichter, robuster und chemikalienbeständiger Thermoplast
- Gute Ermüdungsbeständigkeit und elektrische Isoliereigenschaften
- Wird für Verpackungen, Autoteile und Haushaltswaren verwendet
8. Polystyrol (PS)
- Starrer, transparenter und leicht zu verarbeitender Thermoplast\
- Niedrige Kosten und gute Dimensionsstabilität
- Wird für Verpackungen, Einwegbesteck und Spielzeug verwendet
9. Thermoplastische Elastomere (TPE) und Polyurethane (TPU)
- Flexible, gummiartige Thermoplaste mit guter Schlag- und Abriebfestigkeit
- TPUs bieten eine bessere Chemikalien- und Temperaturbeständigkeit als TPEs
- Wird für Soft-Touch-Griffe, Dichtungen und Schuhe verwendet
Nach Fütterungssystem
Kaltkanal-Spritzgussform
- Besteht aus Anguss, Kanälen, Unterkanälen, Toren und Kaltplättchenschächten.
- Anguss transportiert die Schmelze von der Düse zum Kanalsystem
- Gießrinnen transportieren die Schmelze vom Anguss zu den Anschnitten
- Angussöffnungen sind kleine Öffnungen, die den Angusskanal mit der Kavität verbinden.
- Kalte Slug-Bohrungen speichern das anfängliche kalte Material, das während der Injektionsintervalle produziert wird.
- Kann weiter in Seitentor- und Punkttorsysteme unterteilt werden
- Geeignet für die meisten Spritzgussanwendungen
Heißkanal-Spritzgussform
- Hat keinen Haupt- und Nebenläufer
- Die Schmelze gelangt über eine Verteilerplatte und eine heiße Düse direkt über Angussöffnungen in die Kavität.
- Verwendet isolierte Angusskanäle oder Heißkanalformen
- Macht ein herkömmliches Kaltkanalsystem überflüssig
- Reduziert Materialabfall und Zykluszeiten im Vergleich zu Kaltkanalsystemen
Angusslose Spritzgussform
- Schmelze fließt ohne Angusssystem direkt von der Düse in die Kavität
- Einfachstes Fütterungssystem-Design
Empfohlene Spritzgussform bei Moldie
Moldie ist ein führender Anbieter hochwertiger, präziser Kunststoff-Spritzgussformen und Formgebungsdienste. Mit jahrelanger Erfahrung und modernster Technologie bietet Moldie eine breite Palette an Spritzgusslösungen, die Ihren spezifischen Anforderungen gerecht werden:
Präzisions-Kunststoffformprodukte Spritzgussform
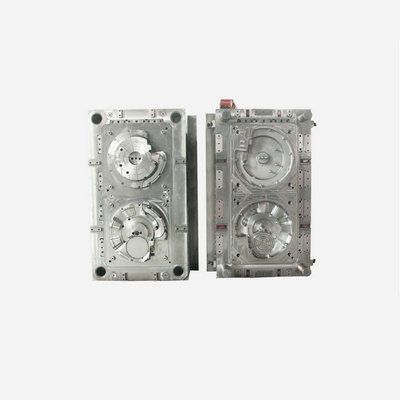
Entdecken Sie Präzisions-Kunststoffformprodukte mit robuster Materialauswahl, Kalt-/Heißkanal-Know-how und der Brillanz der RAL-PANTONE-Farben.
Maßgeschneiderte hochpräzise Kunststoffteile
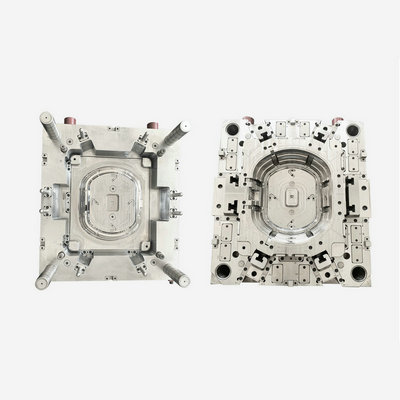
Aufgrund der Komplexität der anfallenden Primär-, Sekundär- und Endbearbeitungsvorgänge sollten Sie Ihren Produktionsprozess nur an Experten wie die aus unserem Unternehmen auslagern.
Hersteller kundenspezifischer Kunststoffformteile
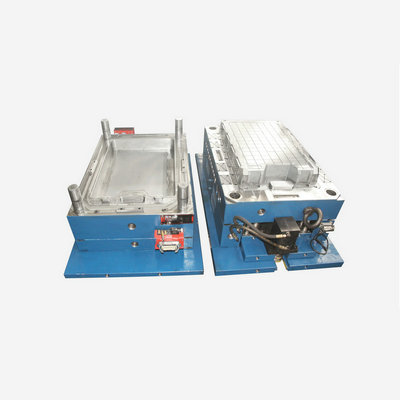
Mit Formgewichten von 50 kg bis 15 Tonnen und Kompatibilität mit Spritzgussmaschinen bis zu 1500 Tonnen steht die Anpassungsfähigkeit im Mittelpunkt unserer Arbeit.
Wählen Moldie für Ihre Spritzgussanforderungen und erleben Sie den Unterschied, den Präzision, Fachwissen und kundenorientierter Service ausmachen können. Kontaktieren Sie uns noch heute, um Ihr Projekt zu besprechen und zu erfahren, wie wir Ihnen helfen können, Ihre Vision zum Leben zu erwecken.