La tecnica dello stampaggio a iniezione viene utilizzata nella produzione di stampi a iniezione per parti identiche, note come componenti stampati. Questo processo richiede un'alta pressione e la plastica fusa o altro materiale viene iniettato in una cavità dello stampo per lo stampaggio a iniezione della plastica.
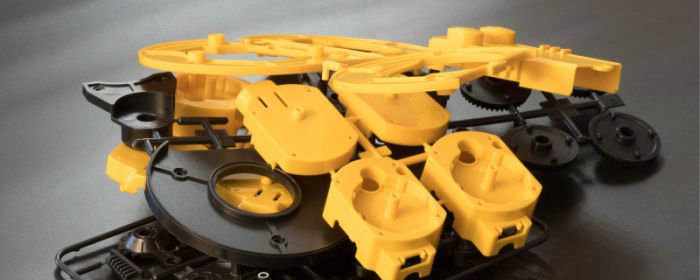
Il secondo passaggio avviene all'interno dello stampo, dove la sostanza si raffredda e si solidifica, conformandosi ai contorni della cavità. La parte stampata viene quindi rimossa dopo l'apertura dello stampo. La procedura viene ripetuta più volte per creare tanti pezzi identici.
Inoltre, l'acciaio immensamente resistente viene comunemente utilizzato per gli stampi a iniezione, costruiti per resistere all'alta pressione e al calore generati durante il processo di stampaggio a iniezione. Per realizzare parti accurate e coerenti, gli stampi devono essere precisi.
La qualità del prodotto finito è notevolmente influenzata dalla progettazione dello stampo, che può essere complicata a causa di considerazioni quali il tipo di materiale da stampare, la forma prevista dell'articolo finito e le procedure di produzione coinvolte.
Le parti stampate sono utilizzate in vari prodotti, dai semplici articoli per la casa alle complesse parti meccaniche utilizzate in settori quali l'industria automobilistica, elettronica e dei dispositivi medici. Lo stampaggio a iniezione è un metodo di produzione molto apprezzato per vari prodotti grazie alla sua adattabilità e convenienza.
Prodotti per stampaggio ad iniezione: attrezzature e processo
Utilizzando macchinari specializzati, il processo industriale di stampaggio ad iniezione crea componenti stampati da materiali termoplastici o termoindurenti. I seguenti componenti sono essenziali nella fabbricazione di prodotti stampati a iniezione:
Attrezzatura
Durante il processo di stampaggio ad iniezione vengono utilizzate le seguenti attrezzature:
- Macchina per lo stampaggio ad iniezione: Questa macchina contiene componenti come una tramoggia, un cilindro di riscaldamento, una vite alternativa e un morsetto per stampi che costituiscono la parte principale della procedura di stampaggio a iniezione. I pellet di plastica vengono fusi dalla macchina e iniettati sotto pressione solida nello stampo per realizzare un pezzo stampato.
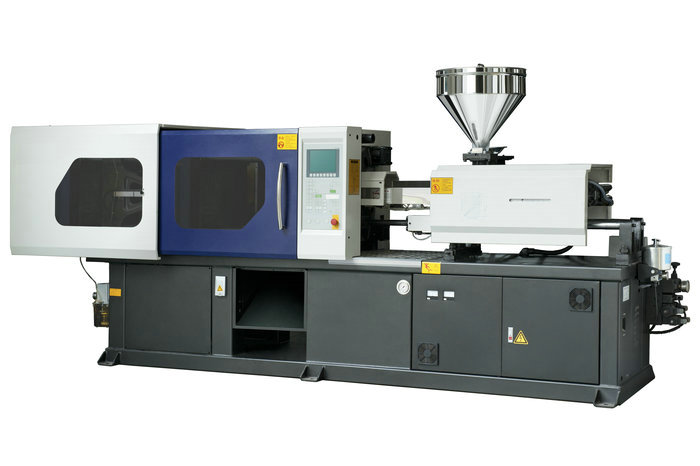
- Cavità dello stampo: Questo strumento, spesso composto da acciaio o alluminio, dà forma alla plastica. Due pezzi dello stampo vengono fissati insieme durante la procedura di stampaggio ad iniezione.
- Tramoggia materiale: Prima di essere immessi nel cilindro di riscaldamento della pressa ad iniezione, i pellet di plastica vengono conservati qui.
- Canna di riscaldamento: I pellet di plastica vengono fusi in questa parte del processo di stampaggio ad iniezione in modo che siano pronti per essere iniettati nello stampo.
- Vite alternativa: Questa parte della pressa ad iniezione riscalda la plastica prima di dirigerla verso lo stampo.
- Morsetto per stampi: Questo sistema applica la pressione necessaria per iniettare la plastica fusa nello stampo mantenendo lo stampo chiuso durante il processo di stampaggio a iniezione.
- Sistema di raffreddamento: Questo viene utilizzato per raffreddare i componenti stampati ad iniezione una volta che sono stati creati. Ciò può essere ottenuto raffreddando il sistema con aria, acqua o una combinazione dei due.
Questi sono gli elementi essenziali di un impianto per lo stampaggio ad iniezione. A seconda delle particolari esigenze del processo di stampaggio ad iniezione, possono essere impiegate anche attrezzature ausiliarie aggiuntive, come granulatori, essiccatori di materiale e unità di controllo della temperatura.
Unità di iniezione plastica
La fusione e l'iniezione del materiale plastico nella cavità dello stampo viene eseguita dall'unità di iniezione della plastica nello stampaggio a iniezione. Il materiale plastico viene fuso e iniettato nello stampo utilizzando una canna riscaldata, una vite e un ugello.
La sostanza plastica viene quindi inserita nella canna, dove la vite mobile la riscalda e la mescola. Nella fase successiva, l'ugello inietta il materiale plastico nella cavità dello stampo una volta raggiunta la giusta temperatura e consistenza, dove si raffredda e si indurisce per creare il risultato desiderato.
Per mantenere una produzione costante e di alta qualità, l'unità di iniezione plastica, che è una parte cruciale del processo di stampaggio ad iniezione, deve essere gestita in modo appropriato.
Unità di chiusura dello stampo
Le due metà dello stampo devono essere ben chiuse e tenute insieme durante i processi di iniezione e raffreddamento dal dispositivo di bloccaggio dello stampo nello stampaggio a iniezione. La forza di serraggio necessaria per tenere saldamente insieme le metà dello stampo e impedire la fuoriuscita di qualsiasi materiale plastico dalla cavità dello stampo viene applicata e mantenuta dall'unità.
Un piano fisso ed un piano mobile accoppiati ad un sistema idraulico o meccanico costituiscono il gruppo chiusura stampo. Le due piastre vengono tirate insieme quando lo stampo viene inserito nella macchina e viene quindi applicata una forza di serraggio per mantenere lo stampo chiuso.
La quantità di forza di serraggio necessaria varia a seconda delle dimensioni, della complessità e del tipo di plastica utilizzata e dello stampo. Per garantire una produzione sicura ed efficace, l'unità di chiusura dello stampo, una parte cruciale del processo di stampaggio a iniezione, deve essere attentamente monitorata.
Processi: Stampaggio ad iniezione di polimeri termoplastici
Il processo per lo stampaggio a iniezione di polimeri termoplastici prevede tipicamente quanto segue:
La muffa
Lo stampaggio ad iniezione di polimeri termoplastici dipende fortemente dallo stampo ad iniezione. È un dispositivo utilizzato per modellare la plastica fusa nell'oggetto finito desiderato. La cavità e il nucleo, i due componenti principali dello stampo, sono tipicamente costruiti per adattarsi insieme per creare una forma tridimensionale.
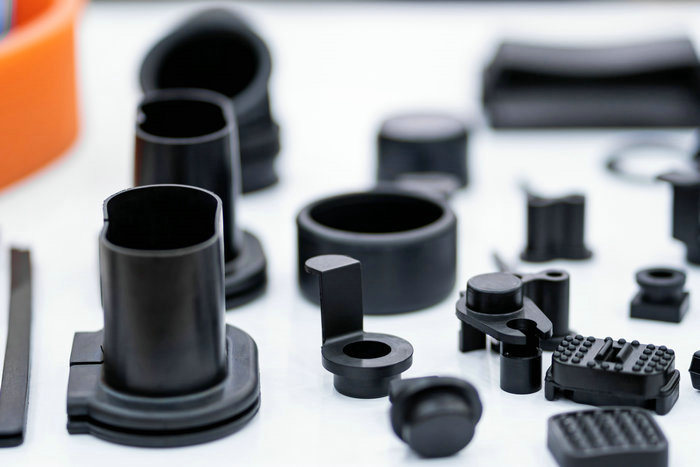
Dopo essere stato iniettato nella cavità dello stampo, il materiale plastico si raffredda e si indurisce assumendo la forma dello stampo. La forma e le dimensioni finali del prodotto sono determinate dal design dello stampo, che lo rende un componente critico del processo di stampaggio a iniezione.
Lo stampo deve essere attentamente sviluppato per garantire che il materiale plastico scorra senza sforzo in ogni cavità e che il processo di raffreddamento sia rapido e uniforme. Inoltre, lo stampo deve essere costruito con materiali che resistono alle alte temperature e pressioni utilizzate nel processo di stampaggio a iniezione.
Poiché lo stampo è riutilizzabile durante l'iniezione, può essere utilizzato per creare numerose parti identiche. Per mantenerlo in buone condizioni e in grado di continuare a produrre parti di alta qualità, potrebbe essere necessario pulire e mantenere regolarmente lo stampo.
Stampo a due piastre
Nell'iniezione di polimeri termoplastici, lo stampo a due piastre è uno stile tipico di stampo. Si compone di due parti fissate sulle due piastre della formatrice, la metà cavità e la metà anima. Lo stampo a due piastre è così chiamato perché ha un design in due parti con una linea di divisione che separa le due parti dello stampo.
Il compito dello stampo a due piastre è modellare la plastica fusa nella forma finale richiesta. Il materiale plastico viene iniettato nella metà cavità dello stampo attraverso un cancello in corrispondenza della linea di separazione. La cavità viene riempita con materiale plastico, che viene poi lasciato raffreddare e solidificare. L'articolo finito viene rilasciato una volta che le due metà dello stampo sono state aperte.
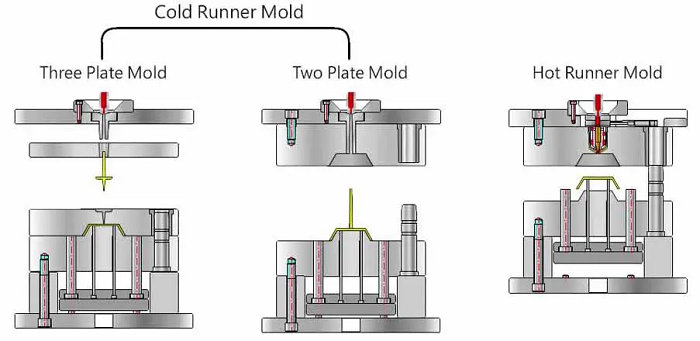
Poiché richiede solo due piastre e pochi semplici componenti, lo stampo a due piastre è un tipo di stampo ragionevolmente semplice ed economico. Funziona bene per i componenti con una geometria semplice, comprese le curve piatte o arrotondate.
Tuttavia, potrebbe non essere appropriato per le parti con geometrie più complesse perché in queste circostanze il riempimento della cavità con la plastica potrebbe essere difficile. Nello stampaggio ad iniezione, lo stampo a due piastre è versatile e spesso utilizzato, soprattutto per pezzi semplici e tirature modeste.
Stampo a tre piastre
Lo stampo a tre piastre è uno degli stampi utilizzati nello stampaggio ad iniezione di polimeri termoplastici. Rispetto allo stampo a due piastre ha più funzionalità e versatilità perché ha tre piastre; due mobili e uno stabile.
Lo scopo dello stampo a tre piastre è quello di modellare le parti stampate ad iniezione in plastica nella forma finale richiesta. Il materiale plastico viene iniettato nella metà della cavità dello stampo attraverso un cancello sulla linea di separazione.
Una volta che la plastica fusa è nella cavità dello stampo, le due piastre mobili si staccano dalla piastra fissa, consentendo l'espulsione dell'oggetto in plastica dallo stampo. La terza piastra nello stampo a tre piastre, inserita tra la cavità e la metà del nucleo, è denominata piastra guida o sottopiastra.
Con l'uso di questa piastra, è possibile creare un sistema di scorrimento unico che può essere utilizzato per dirigere il flusso di materiale plastico verso varie cavità o posizioni all'interno di una singola cavità. Di conseguenza, il processo di stampaggio a iniezione può essere più flessibile ed efficace.
Quando si producono articoli più grandi, dove l'utilizzo di uno stampo a due piastre comporterebbe una dimensione dello stampo maggiore o richiederebbe l'installazione di caratteristiche extra come i sollevatori, viene spesso impiegato lo stampo a tre piastre. Includendo diverse cavità nel design dello stampo, lo stampo a tre piastre può realizzare varie parti in un unico ciclo.
Lo stampo a tre piastre è un tipo di stampo versatile ed efficace frequentemente utilizzato nel processo di stampaggio a iniezione, in particolare per parti più grandi e cicli di produzione.
Riutilizzo della materozza e del canale di colata in stampi a due e tre piastre
Il materiale utilizzato, la geometria del pezzo e le qualità desiderate del prodotto finito influiscono tutti sulla quantità di materozza e canale di colata che possono essere riutilizzati nello stampaggio a iniezione. Il riutilizzo della materozza e del canale di colata viene spesso effettuato nell'industria dello stampaggio a iniezione perché può ridurre i costi e gli scarti.
Inoltre, la materozza e il canale di scorrimento sono normalmente fissati all'oggetto stampato in uno stampo a due piastre e l'assieme nel suo insieme viene espulso dallo stampo. L'articolo può quindi essere staccato manualmente dalla materozza e dal canale, che possono essere utilizzati in altri cicli di stampaggio.
Il riutilizzo della materozza e del canale di colata potrebbe richiedere ulteriori procedure di lavorazione, inclusa la molatura o la rifusione, per garantire che il materiale sia in una forma appropriata per il riutilizzo. In uno stampo a tre piastre, la procedura di espulsione separa la materozza e il canale dall'oggetto stampato e la materozza viene spesso riutilizzata in cicli di stampaggio consecutivi.
La piastra del canale è in genere staccabile, facilitando l'accesso al sistema del canale e il riutilizzo della materozza e del canale. È fondamentale ricordare che il riutilizzo della materozza e del canale di colata può avere un impatto significativo sulla consistenza e sulla qualità del prodotto finale.
Tuttavia, i materiali riutilizzati potrebbero presentare impurità o problemi di consistenza che influenzano la resistenza o la durata del materiale plastico. Per ottenere prodotti uniformi e di alta qualità, è necessario un monitoraggio continuo del processo di stampaggio e della qualità del materiale riciclato.
In generale, l'industria dello stampaggio a iniezione riutilizza materozza e canale di colata in stampi a due e tre piastre, il che può aiutare a ridurre i costi e gli scarti. Garantire che la qualità e le qualità del prodotto finale non vengano compromesse richiede una riflessione e una gestione rigorose.
Macchine per lo stampaggio ad iniezione
Le macchine utilizzate per il processo di stampaggio a infezione comprendono:
Unità di iniezione
L'unità di iniezione, che fonde e inietta materiale plastico nello stampo, è una parte fondamentale di una pressa ad iniezione. I componenti tipici sono il cilindro, il riscaldatore, la vite o lo stantuffo, la tramoggia e l'unità di iniezione.
Prima di essere immesso nel fusto, il materiale plastico viene prima immesso nella tramoggia e ivi conservato. La vite o lo stantuffo in movimento e il calore del riscaldatore sciolgono e omogeneizzano la plastica all'interno della canna. Man mano che avanza, il materiale plastico fuso viene iniettato nello stampo attraverso una saracinesca dalla vite o dallo stantuffo.
Lo scopo dell'unità di iniezione è regolare con precisione la temperatura, la pressione e la portata del materiale plastico durante tutto il processo di stampaggio a iniezione. Questo garantisce che il materiale plastico sia uniformemente omogeneizzato, correttamente fuso ed iniettato nello stampo.
È anche possibile modificare la velocità, la pressione e il volume dell'unità di iniezione, il che è fondamentale quando si stampano oggetti con geometrie complesse o tolleranze rigorose. A seconda dell'applicazione esatta, il tipo e le dimensioni dell'unità di iniezione possono cambiare, con alcune macchine realizzate per la produzione di grandi volumi e altre per lo stampaggio preciso o su piccola scala.
L'unità di iniezione è fondamentale per la generazione di articoli in plastica di alta qualità ed è spesso uno dei componenti più significativi nella definizione delle prestazioni e delle capacità di una macchina per lo stampaggio a iniezione.
Macchina a vite alternativa
Un dispositivo di stampaggio ad iniezione, una macchina a vite alternativa, fonde e inietta materiale plastico nello stampo utilizzando una vite alternativa. Per la sua adattabilità, efficacia e capacità di creare articoli in plastica di alta qualità, questa attrezzatura è frequentemente utilizzata nel settore dello stampaggio ad iniezione.
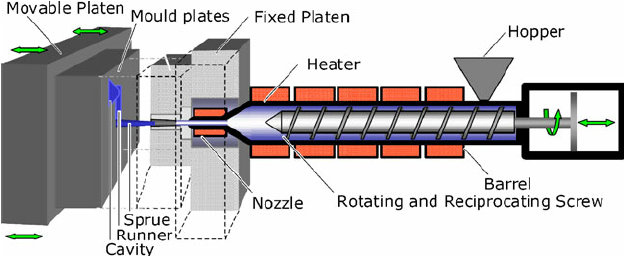
Idealmente, lo stampaggio a iniezione comporta la fusione e l'iniezione di materiali termoplastici in uno stampo utilizzando una macchina a vite alternativa. I pellet di plastica vengono inseriti nella canna della macchina dalla vite alternativa e fusi, quindi pressione e calore.
Dopo essere stata fusa, la plastica viene iniettata nello stampo mediante una vite ad alta pressione per conferire al prodotto finito la forma desiderata.
Macchina per plastificante a vite o macchina a due stadi
La macchina a due stadi è una pressa ad iniezione che utilizza due gruppi di iniezione indipendenti; uno per fondere il materiale plastico ed un altro per iniettarlo nello stampo.
La fusione e la preparazione per l'iniezione del materiale plastico sono indicate come la prima fase, o "plastificazione". In questa fase, una vite alternativa produce calore e pressione che fondono la plastica man mano che viene fornita all'unità di iniezione primaria della macchina.
Il materiale plastico fuso viene pompato nello stampo durante la seconda fase, detta anche fase di “dosaggio”. Questa fase comporta lo spostamento della plastica fusa dall'unità di iniezione primaria all'unità di iniezione secondaria, dove viene iniettata sotto pressione solida nello stampo.
I pezzi grandi e complessi vengono spesso prodotti utilizzando macchine a due stadi perché forniscono un controllo superiore del processo di stampaggio e consentono un'iniezione più accurata del materiale plastico nello stampo.
Unità di bloccaggio
Per la realizzazione di pezzi stampati ad iniezione vengono utilizzate le seguenti unità di chiusura:
Morsetti a ginocchiera
Per tenere insieme le due parti dello stampo durante il processo di iniezione, nello stampaggio a iniezione vengono impiegati morsetti a ginocchiera. I morsetti sono realizzati per generare una forte forza di chiusura per garantire che lo stampo rimanga chiuso e correttamente orientato durante l'iniezione del materiale plastico fuso.
I morsetti a ginocchiera aumentano la forza di serraggio fornita allo stampo attraverso un sistema di collegamento. Il sistema di collegamento produce un vantaggio meccanico quando il morsetto è innestato, aumentando la forza applicata allo stampo. Di conseguenza, i morsetti possono applicare molta forza con solo una piccola forza di input.
Inoltre, i morsetti a ginocchiera sono preferiti nello stampaggio a iniezione perché forniscono una forza di presa robusta e affidabile che può essere modificata per soddisfare le esigenze specifiche del processo di stampaggio. Inoltre, sono veloci da inserire e disinserire e sono semplici da usare, il che contribuisce a ridurre il tempo di ciclo complessivo per il processo di stampaggio.
Pinze idrauliche
I morsetti idraulici sono spesso impiegati nello stampaggio a iniezione per tenere insieme le due metà dello stampo durante il processo di iniezione. Per fornire una forte forza di serraggio allo stampo e mantenerlo saldamente chiuso e allineato durante l'iniezione del materiale plastico fuso, i morsetti idraulici utilizzano la pressione idraulica.
Una pompa idraulica, valvole di controllo e cilindri costituiscono il sistema idraulico convenzionale utilizzato nel meccanismo di bloccaggio. I cilindri spostano la piastra di bloccaggio o la piastra di montaggio dello stampo quando viene attivato il sistema idraulico, applicando pressione allo stampo durante il processo.
Morsetti idromeccanici
Per tenere insieme le due parti dello stampo durante il progetto di stampaggio a iniezione, lo stampaggio a iniezione utilizza morsetti idromeccanici, noti anche come morsetti a ginocchiera.
Combinando un sistema idraulico per avviare il processo di bloccaggio e un meccanismo a ginocchiera meccanico per aumentare e sostenere la forza di bloccaggio, i bloccaggi idromeccanici combinano i vantaggi dei metodi di bloccaggio idraulici e meccanici.
Un cilindro idraulico che sposta la piastra di bloccaggio verso la piastra fissa genera la forza di bloccaggio. Una volta raggiunta una determinata quantità di forza di serraggio, il cilindro idraulico si blocca e il meccanismo meccanico a ginocchiera subentra per continuare ad applicare la forza di serraggio.