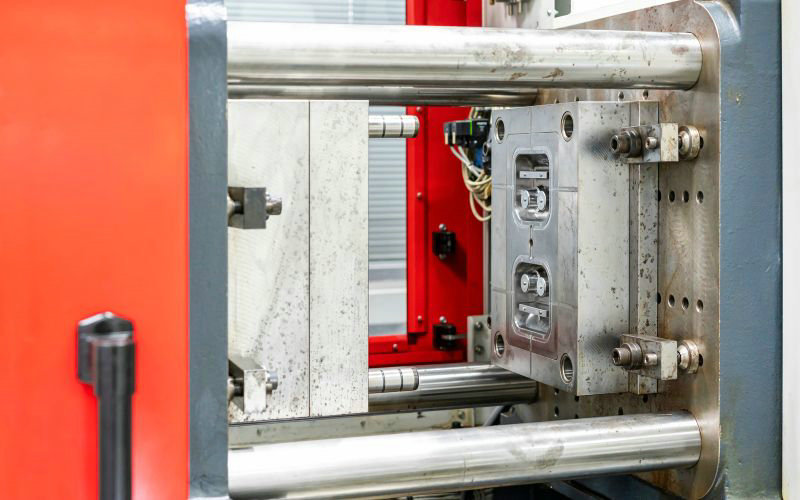
Classificazione dello stampo ad iniezione
Se stai valutando stampi a iniezione, è essenziale comprendere il sistema di classificazione che ne differenzia le capacità e le applicazioni. In questo articolo ti forniremo una guida semplice per comprendere i vari tipi di stampi:
- Di Geometria
- Di Numero di cavità
- Di Piastra dello stampo
- Di Principio di espulsione
- Di Materiale plastico
- Di Sistema di alimentazione
La scelta tra questi tipi di stampi a iniezione spesso bilancia la portata del progetto, la complessità delle parti e le implicazioni sui costi operativi. Esploriamo insieme vari tipi di stampi per iniezione plastica!
Per geometria
- Geometrie semplici:
- Più facile da progettare e produrre.
- Spesso hanno meno sezioni cave.
- Geometrie complesse:
- Consentire una maggiore flessibilità di progettazione.
- Può ospitare sezioni cave necessarie per funzioni specifiche.
Le parti complesse spesso includono caratteristiche come sottosquadri, ovvero rientranze o sporgenze che possono complicare la progettazione dello stampo. La progettazione dei sottosquadri richiede un'attenta considerazione per garantire che i componenti dello stampo possano separarsi correttamente durante la fase di espulsione senza danneggiare la parte.
Per progetti di componenti complessi, potrebbe essere necessario utilizzare tecnologie di stampo avanzate, come cursori o sollevatori, per creare e rilasciare con successo la parte dallo stampo. Sebbene questo approccio offra un'elevata flessibilità di progettazione, aumenta anche la complessità e il costo dello stampo.
La scelta tra una geometria dello stampo semplice o complessa dipenderà in ultima analisi dal design della parte desiderata, dalla funzionalità, dalla fattibilità del processo di produzione dello stampo e dal budget del progetto. Bilancia sempre la necessità di geometrie complesse con considerazioni pratiche sulla produzione.
Per numero di cavità
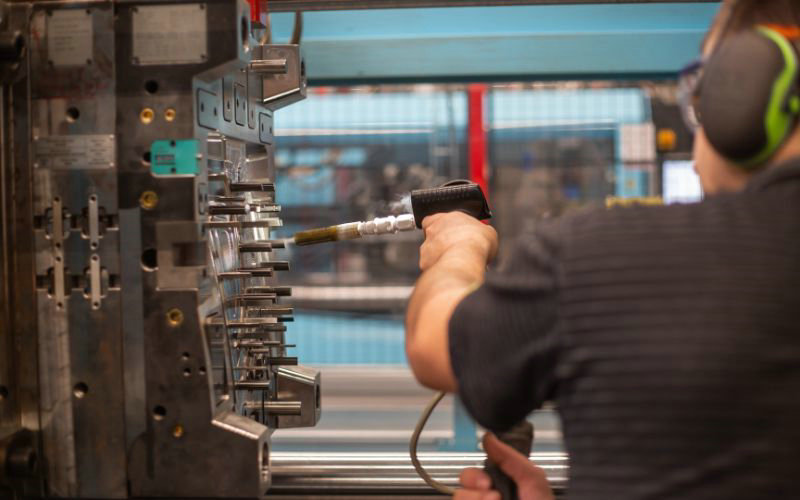
Stampi a cavità singola
- Produrre un solo prodotto per ciclo di iniezione
- Ideale per parti grandi, complesse o a basso volume
- Consentire maggiore attenzione alle singole parti per ridurre al minimo i difetti
- Costi di attrezzaggio inferiori rispetto agli stampi multi-cavità per la stessa parte
- Adatto per la prototipazione e la fornitura di nuovi progetti
Stampi multicavità
- Contengono più cavità identiche per produrre diverse parti per ciclo
- Consenti tempi di consegna più brevi e maggiore efficienza produttiva per volumi elevati
- Riduci i costi per pezzo per lotti di grandi dimensioni
- Richiedono un'attenta progettazione per garantire un riempimento uniforme e una qualità costante in tutte le cavità
- Potrebbe avere costi di attrezzaggio iniziali più elevati rispetto agli stampi a cavità singola
- I numeri di cavità tipici vanno da 2 a 64 o più, a seconda delle dimensioni della parte e dell'applicazione
Stampi per famiglie
- Incorpora più cavità con forme diverse per produrre varie parti in un ciclo
- Consenti lo stampaggio di componenti correlati o varianti di prodotto in un'unica operazione
- Utile per prototipare o produrre kit con parti assortite
- Limitato alle parti che utilizzano lo stesso materiale e colore
- Spesso presentano un riempimento sbilanciato a causa delle diverse geometrie della cavità, aumentando il rischio di difetti
- Richiede più manodopera post-stampaggio per separare e gestire parti diverse
Dalla piastra dello stampo
Stampo ad iniezione a due piastre
- Design dello stampo a iniezione più semplice e più comune, composto da due parti principali (lato A e lato B)
- Ha un'unica linea di divisione in cui lo stampo si divide in due metà
- Il lato cavità è fisso, mentre il lato anima è mobile durante il processo di stampaggio
- Guida e pezzo si trovano sullo stesso piano di divisione ed espulsi insieme
- Vantaggi: costo inferiore, tempi ciclo più brevi, facilità di installazione e funzionamento
- Svantaggi: minore flessibilità nella posizione del punto di iniezione, richiede la delega manuale, rischio di scatti brevi negli stampi a più cavità
Stampo ad iniezione a tre piastre
- Conosciuto anche come stampo per piastre di estrazione, è costituito da due piani di divisione e si divide in tre sezioni
- Dispone di una piastra flottante aggiuntiva tra la cavità e il nucleo per accogliere il sistema di guida
- Consente il degasaggio automatico del canale dal pezzo
- Offre maggiore flessibilità nella posizione del punto di iniezione rispetto agli stampi a due piastre
- Vantaggi: adatto per pezzi di grandi dimensioni che richiedono più accessi, consente la discussione automatica
- Svantaggi: più complesso e costoso, tempi ciclo più lunghi, meno stabile a causa del maggior numero di parti in movimento
Stampo per iniezione a pila
- Speciale struttura dello stampo con più superfici di divisione, ciascuna delle quali può ospitare una o più cavità
- È costituito da uno stampo mobile, uno stampo intermedio e uno stampo fisso che si aprono simultaneamente
- Può raddoppiare la produttività di uno stampo standard senza richiedere macchine aggiuntive
- Adatto per la produzione in grandi volumi di parti piatte e a pareti sottili
- Vantaggi: produttività notevolmente aumentata, costi ridotti, tempi di produzione più brevi
- Svantaggi: design più complesso, richiede un attento bilanciamento tra riempimento e raffreddamento della cavità
Per principio di espulsione
1. Espulsione del perno
- Utilizza perni di espulsione per spingere la parte stampata fuori dalla cavità dello stampo
- I perni si trovano nella metà dell'espulsore dello stampo e sono progettati per resistere alle forze di espulsione
- Diametro, lunghezza, materiale, posizionamento e forma del perno sono considerazioni di progettazione critiche
- Adatto per la maggior parte delle parti stampate a iniezione, ma può lasciare segni visibili del perno di espulsione
2. Espulsione della manica
- Impiega un eiettore a forma di manicotto che circonda il nucleo per espellere la parte
- Fornisce una forza di espulsione uniforme e stabile senza lasciare segni visibili
- Adatto per prodotti cilindrici, a parete sottile o a forma di conchiglia
- Più complesso e costoso dell'espulsione del perno
3. Espulsione della piastra di estrazione
- Utilizza una piastra di estrazione per spingere la parte fuori dal nucleo
- La forza di espulsione è elevata, uniforme e stabile e riduce al minimo la deformazione della parte
- Ideale per parti cilindriche, contenitori a pareti sottili e prodotti a forma di conchiglia
- Evita i segni visibili dell'espulsore ma ha una struttura dello stampo più complessa e un costo più elevato
4. Espulsione della lama
- Utilizza lame di espulsione rettangolari invece di perni
- Adatto per parti con geometrie o requisiti specifici
5. Espulsione dell'aria
- Introduce aria compressa tra la parte e lo stampo per espellere la parte
- Semplifica la struttura dello stampo e consente l'espulsione in qualsiasi posizione
- Spesso utilizzato per supportare altri metodi di espulsione per parti grandi, con cavità profonde o con pareti sottili
6. Espulsione del sollevatore
- Impiega sollevatori che si muovono lateralmente per rilasciare sottosquadri o caratteristiche interne
- Consente l'espulsione di parti con geometrie complesse o azioni laterali
Per materiale plastico
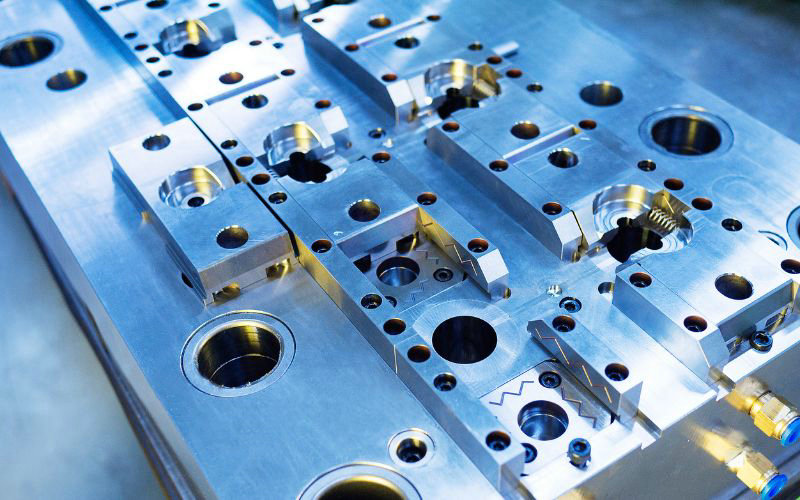
1. Acrilico (PMMA)
- Termoplastica forte e trasparente con eccellente chiarezza ottica e resistenza ai raggi UV
- Alternativa leggera e infrangibile al vetro
- Utilizzato per lenti, display, segnaletica e dispositivi medici
2. Acrilonitrile Butadiene Stirene (ABS)
- Materiale termoplastico robusto, rigido e resistente agli urti
- Buona resistenza chimica ed è facile da verniciare o incollare\
- Utilizzato per parti automobilistiche, elettrodomestici, giocattoli e alloggiamenti elettronici
3. Nylon (poliammide, PA)
- Termoplastica robusta, flessibile e resistente all'usura
- Alto punto di fusione e buona resistenza chimica
- Utilizzato per parti automobilistiche, ingranaggi, cuscinetti e componenti elettrici
4. Policarbonato (PC)
- Materiale termoplastico robusto, trasparente e resistente al calore
- Buona stabilità dimensionale e proprietà di isolamento elettrico
- Utilizzato per componenti automobilistici, dispositivi medici e occhiali di sicurezza
5. Polietilene (PE)
- Materiale termoplastico leggero, flessibile e resistente agli agenti chimici
- Disponibili varianti ad alta densità (HDPE) e a bassa densità (LDPE).
- Utilizzato per imballaggi, contenitori, giocattoli e componenti automobilistici
6. Poliossimetilene (POM)
- Termoplastico resistente, rigido e dimensionalmente stabile
- Eccellente resistenza all'usura e agli agenti chimici
- Utilizzato per ingranaggi, cuscinetti e parti di precisione
7. Polipropilene (PP)
- Termoplastica leggera, resistente e resistente agli agenti chimici
- Buona resistenza alla fatica e proprietà di isolamento elettrico
- Utilizzato per imballaggi, componenti automobilistici e articoli per la casa
8. Polistirolo (PS)
- Termoplastico rigido, trasparente e facile da lavorare\
- Basso costo e buona stabilità dimensionale
- Utilizzato per imballaggi, posate usa e getta e giocattoli
9. Elastomeri Termoplastici (TPE) e Poliuretani (TPU)
- Materiale termoplastico flessibile, simile alla gomma, con buona resistenza agli urti e all'abrasione
- I TPU offrono una migliore resistenza chimica e alla temperatura rispetto ai TPE
- Utilizzato per impugnature, guarnizioni, tenute e calzature soft-touch
Per sistema di alimentazione
Stampo per iniezione a canale freddo
- È costituito da canale di colata, canali di scorrimento, canali secondari, cancelli e pozzi per lumache fredde\
- Il canale di colata fornisce la massa fusa dall'ugello al sistema di canali
- I corridori trasportano la massa fusa dal canale di colata ai cancelli
- Le porte sono piccoli orifizi che collegano il corridore alla cavità
- I pozzi di lumache fredde immagazzinano il materiale freddo iniziale prodotto durante gli intervalli di iniezione
- Può essere ulteriormente suddiviso in sistemi a cancello laterale e a cancello puntuale
- Adatto per la maggior parte delle applicazioni di stampaggio a iniezione
Stampo per iniezione a canale caldo
- Non ha corridore principale e secondario
- Il materiale fuso passa attraverso una piastra collettore e un ugello caldo direttamente nella cavità tramite cancelli
- Utilizza stampi a canale isolato o a canale caldo
- Elimina la necessità di un tradizionale sistema a canale freddo
- Riduce gli sprechi di materiale e i tempi di ciclo rispetto ai sistemi a canali freddi
Stampo ad iniezione senza guide
- Il materiale fuso scorre direttamente dall'ugello nella cavità senza sistema di canali
- Design del sistema di alimentazione più semplice
Stampo a iniezione consigliato da Moldie
Moldie è un fornitore leader di stampi per iniezione plastica e servizi di stampaggio di precisione e di alta qualità. Con anni di esperienza e tecnologia all'avanguardia, Moldie offre un'ampia gamma di soluzioni di stampi a iniezione per soddisfare le vostre esigenze specifiche:
Stampaggio ad iniezione di prodotti per stampi in plastica di precisione
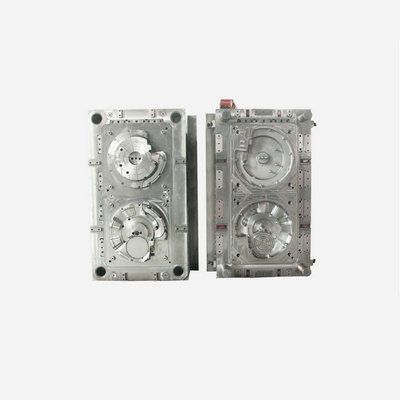
Scopri prodotti per lo stampaggio di plastica di precisione caratterizzati da una scelta di materiali robusti, competenza nei canali freddi/caldi e la brillantezza dei colori RAL PANTONE.
Parti in plastica di alta precisione su misura
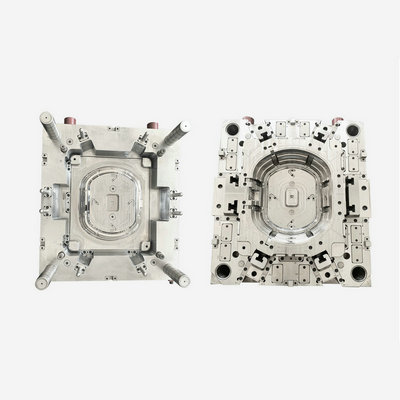
La complessità delle operazioni primarie, secondarie e di finitura coinvolte è il motivo per cui dovresti avvalerti solo dei servizi di esperti come quelli della nostra azienda per gestire il tuo processo di produzione.
Produttore di stampaggio plastica personalizzato
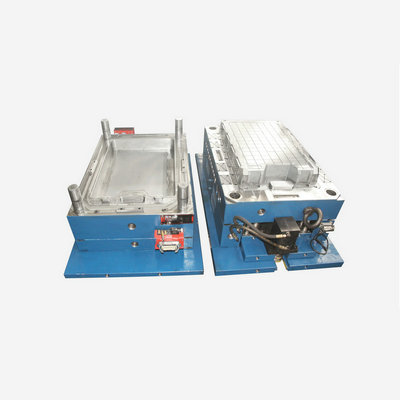
Con pesi degli stampi che vanno da 50 kg a 15 tonnellate e compatibilità con macchine a iniezione fino a 1500 tonnellate, l'adattabilità è al centro di ciò che facciamo.
Scegliere Molde per le vostre esigenze di stampaggio a iniezione e sperimentate la differenza che precisione, competenza e servizio incentrato sul cliente possono fare. Contattaci oggi per discutere del tuo progetto e scoprire come possiamo aiutarti a dare vita alla tua visione.