Beim Druckguss werden bei der Herstellung geschmolzener Metalle und Legierungen hohe Temperaturen und Drücke eingesetzt, um die gewünschte Form zu erzeugen. Dabei werden niedrig schmelzende Metalle geschmolzen und in Druckgussformen eingebracht.
Normalerweise wird Druckguss nach der Temperatur und dem Druck klassifiziert, die zum Einbringen des geschmolzenen Metalls in die Druckgussform erforderlich sind. Dennoch lässt es sich auch nach der Art des im Prozess verwendeten Materials klassifizieren und Zink gehört zu den am häufigsten verwendeten Druckgussmetallen. Vor diesem Hintergrund finden Sie hier alles, was Sie über das Gießen von Zinklegierungen wissen müssen:
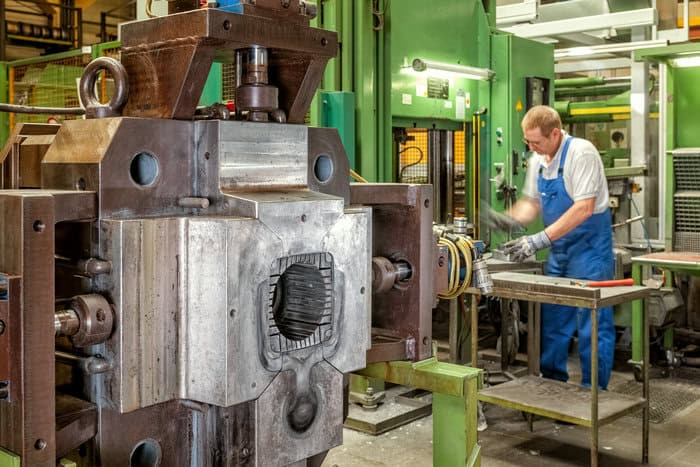
Was ist Zinkdruckguss?
Zinkdruckguss ist ein Verfahren, bei dem flüssiges Zinkmetall unter Druck in eine Form eingespritzt und erstarren gelassen wird. Der Formhohlraum besteht aus zwei Formen aus gehärtetem Werkzeugstahl, die auf die gewünschte Form zugeschnitten sind.
Zinklegierungen haben niedrige Schmelzpunkte, daher erfolgt der Guss bei geringerer Hitze. Darüber hinaus eignen sie sich aufgrund ihrer Schlagzähigkeit und Duktilität für die Teilefertigung.
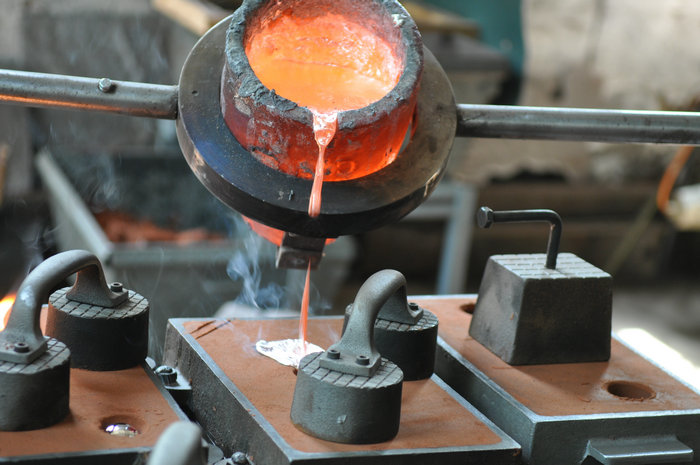
Schritte des Zinkdruckgussprozesses
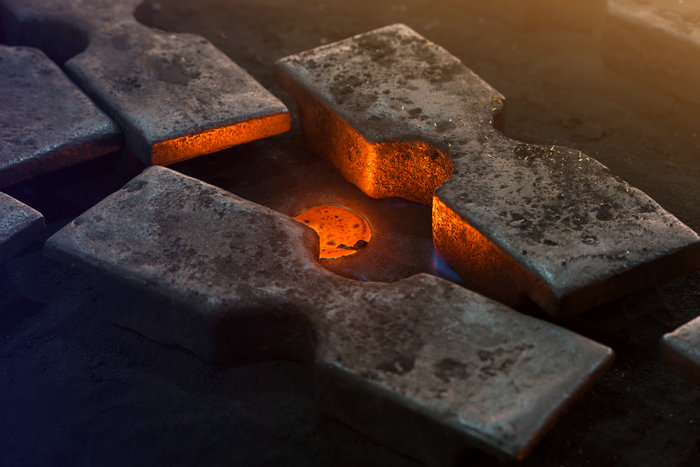
Der Druckgussprozess für Zinklegierungen kann je nach Größe und Typ der von Ihnen verwendeten Maschinen unterschiedlich sein. Es gibt jedoch ein allgemeines Verfahren, das Sie wie folgt befolgen können:
- Schritt 1: Vorbereiten der Matrize
Bevor Sie mit dem Gussprozess beginnen, müssen Sie zunächst die Gussform selbst vorbereiten. Hier müssen Sie die Druckgussform reinigen, indem Sie sie reinigen. Schmieren Sie dann die Form, um das Einführen des Gussteils nach dem Abkühlen zu verbessern. Sie können auch die Innenwände der Formen schmieren, um die Temperatur der Form zu kontrollieren und das einfache Entfernen des Abdrucks zu erleichtern.
Zum Schluss die Matrize unter hohem Druck einspannen.
- Schritt 2: Injektion
Im nächsten Schritt wird die Zinklegierung in die Schusskammer der Maschine eingebracht. Hier müssen Sie Ihre Zinklegierung vor dem Einspritzen schmelzen. Da es sich beim Druckguss von Zinklegierungen um ein Heißkammer-Druckgussverfahren handelt, ist die Schusskammer heiß. Als nächstes geben Sie das geschmolzene Zinkmetall unter hohem Druck in die Form.
- Schritt 3: Abkühlen und Auswerfen
Nachdem Sie das geschmolzene Zink in die Kammer eingespritzt haben, können Sie es abkühlen und erstarren lassen. Geben Sie Ihrem Metall ausreichend Zeit, um zu gelieren und die Form der Form anzunehmen. Stellen Sie außerdem sicher, dass es vollständig ausgehärtet ist, bevor Sie die Matrize lösen. Denken Sie daran, dass ein vorzeitiges Abwerfen des Gipsverbandes zu bleibenden Schäden führen kann.
Sobald Ihre Gussform abgekühlt und erstarrt ist, können Sie die Gussformhälften ausspannen, öffnen und die Gussteile vorsichtig entnehmen.
- Schritt 4: Trimmen
Der letzte Schritt im Zinkdruckgussprozess ist das Beschneiden. Während das Metall abkühlt, können Sie Metallreste wie Gussgrate, Angüsse und Angusskanäle sorgfältig aus dem Zinkguss entfernen. Sie können Werkzeuge wie eine Säge, eine Stanzform usw. verwenden, um die gewünschte Bauteilform zu erreichen. Stellen Sie sicher, dass Sie jedes Teil reinigen, bevor Sie es an Ihre Kunden versenden.
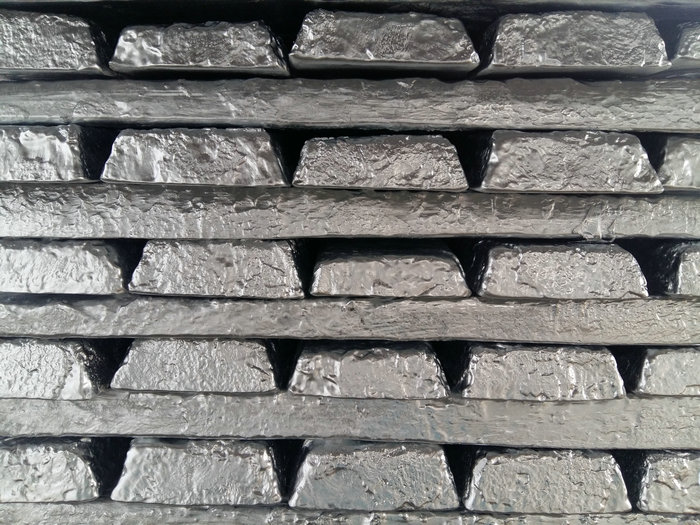
Zinklegierungen für den Druckguss
Nachfolgend sind die gängigsten Zinklegierungen aufgeführt, die für den Druckguss geeignet sind:
- Zamak 2
Zamak 2, auch Zinklegierung 2 oder Kirksite genannt, weist die höchste Festigkeit und Härte aller Zamak-Legierungen auf. Aus diesem Grund wird es in Gussbereichen eingesetzt, die eine hohe strukturelle Integrität erfordern, beispielsweise in der Automobil- und Maschinenbranche.
Darüber hinaus verfügt Zamak 2 im Vergleich zu anderen Metalllegierungen über herausragende Gusseigenschaften wie hohes Kriechvermögen, hervorragende Dämpfungskapazität und Vibrationsbeständigkeit.
- Zamak 3
Die Zinklegierung Zamak 3 ist aus verschiedenen Gründen eine der beliebtesten Legierungen für den Druckguss, darunter die folgenden:
- Hervorragende Gießbarkeit und dauerhafte Dimensionsstabilität
- Perfektes Gleichgewicht zwischen den physikalischen und mechanischen Eigenschaften
- Hervorragende Kompatibilität mit verschiedenen Veredelungsoptionen wie Galvanisieren, Chromatieren und Lackieren
- Gute Kombination aus Kraft und Flexibilität
- Zamak 7
Zamak 7, auch Zinklegierung 7 genannt, ist ein modifiziertes Zamak 3 mit hoher Reinheit und geringerem Magnesiumgehalt als andere Zamak-Legierungen. Es verfügt außerdem über eine feste Spezifikation für Verunreinigungen, was die Gussflexibilität, Fließfähigkeit und Oberflächenbeschaffenheit verbessert.
Diese Zinklegierung wird für einzigartige Hardware-Anwendungen verwendet oder wenn das Gießen während nachfolgender Montagevorgänge wie Vernieten und Crimpen zusätzliche Formbarkeit erfordert.
- ZA 8
ZA-8, eine Zink-Aluminium-Legierung, enthält einen höheren Aluminiumgehalt als andere Mitglieder der Zamak-Familie. Im Vergleich zu anderen ZA-Legierungen ist ZA-8 die einzige ZA-Legierung, die im Warmkammer-Druckgussverfahren hergestellt werden kann.
Darüber hinaus bietet ZA-8 deutlich verbesserte Härte-, Festigkeits- und Kriecheigenschaften. Es wird hauptsächlich zu dekorativen Zwecken verwendet.
- ACuZink5
General Motors hat diese Zinklegierung erforscht und entwickelt. Es ist auch als Zink-, Kupfer- und Aluminiumlegierung bekannt und weist aufgrund seines geringen Aluminium- und hohen Kupfergehalts eine verbesserte Festigkeit und Härte auf. Darüber hinaus verfügt es über hervorragende Lagereigenschaften wie z. B. Schmierfähigkeit.
ACuZinc5 wird in Teilen verwendet, die eine hohe strukturelle Integrität erfordern und unter heißen Bedingungen eingesetzt.
- EZAC
Die EZAC-Legierung bietet maximale Kriechfestigkeit, höhere Streckgrenze und Härte als andere Zinklegierungen. Es bietet eine bessere Leistung als Zamak 2 und hält länger als ACuZinc 5.
- ZA 27 – Zink-Aluminium
ZA-27 enthält im Vergleich zu anderen ZA-Legierungen den höchsten Aluminiumgehalt, Schmelzpunkt, Festigkeit und Dichte. Idealerweise besteht diese ZA-Legierung aus 27%-Aluminium und weist perfekte Lagereigenschaften auf, sodass Lager in Gussteilen für spezifische Anwendungen hergestellt werden können.
Vorteile von Zinkdruckguss
Zinkdruckguss bietet eine Vielzahl von Vorteilen. Zu den wichtigsten Vorteilen gehören die folgenden:
Einfache Montage
Einer der wesentlichen Vorteile des Zinkdruckgusses besteht darin, dass die Montagevorgänge minimiert werden. Im Allgemeinen wird der Zinklegierungs-Druckgussprozess in einer einzigen Einheit durchgeführt, sodass keine kostspieligen manuellen Montagetätigkeiten erforderlich sind.
Hohe Präzision mit dünner Wand
Zinkdruckguss erzeugt im Vergleich zu anderen Gussverfahren komplexe Formen mit mehreren Hohlräumen und engeren Toleranzen. Darüber hinaus werden Großserien nahezu identischer und verschleißfester Teile mit hoher Dimensionsstabilität hergestellt.
Bessere mechanische Eigenschaften
Zinklegierungen haben gegenüber anderen Materialien wie Aluminium und Zink zahlreiche Vorteile hinsichtlich mechanischer Eigenschaften wie Festigkeit, Festigkeit, Widerstandsfähigkeit, Zähigkeit und Haltbarkeit. Aus diesem Grund werden Zinkdruckgussteile in Teilen verwendet, die eine höhere Festigkeit erfordern.
Komplexe Geometrien gießen
Aufgrund seiner hervorragenden Lager- und Verschleißeigenschaften kann Zink als Lager für bewegte Strukturen dienen. Darüber hinaus ermöglicht es die Herstellung von Druckgussteilen mit komplexen Geometrien, da es Verbindungen mit anderen Materialien bilden kann.
Längere Werkzeuglebensdauer
Ein weiterer wesentlicher Vorteil von Zinkdruckgussformen besteht darin, dass sie um ein Vielfaches länger halten können als Aluminium. Dies liegt daran, dass Zinklegierungen niedrigere Schmelzpunkte haben und weniger abrasiv sind. Aus diesem Grund werden Formenschäden verringert und die Lebensdauer des Werkzeugs erhöht, wodurch die Werkzeugkosten stärker gesenkt werden als bei anderen Materialien.
Schnellere Produktion
Wie oben dargelegt, erfordern schneller herstellbare Zinklegierungen niedrige Schmelztemperaturen und einen Kammerdruckgussprozess unter hohen Drücken. Dadurch wird die Zyklusrate des Zinkdruckgusses erhöht, was wiederum die Produktionsraten des Druckgusses erhöht.
Das Einspritzen von Zinkdruckguss ist unkompliziert, im Gegensatz zum Einspritzen von Aluminiumdruckguss, bei dem das Aluminium vor dem Einfüllen in einem anderen Behälter geschmolzen werden muss. Darüber hinaus weist das Gussstück eine hohe Erstarrungsrate auf, was die Anzahl der produzierten Teile erhöht und die Gusskosten senkt.
Verschiedene Veredelungsoptionen
Es gibt zahlreiche Veredelungsmöglichkeiten, die sich ideal für Druckgussmaterialien eignen. Im Folgenden sind einige beliebte Modelle aufgeführt, die für den Zinkdruckguss geeignet sind:
- Pulverbeschichtungen: Diese Veredelungsvariante ist aufgrund der breiten Farbpalette aus ästhetischen Gründen geeignet. Darüber hinaus sorgt es für eine langanhaltende und gleichmäßige Oberflächenbeschaffenheit der Gussteile.
- Malerei: Die Malerei ist für funktionale und ästhetische Eigenschaften verantwortlich. Wie die Pulverbeschichtung gibt es verschiedene Farben und wird für praktische Farbzwecke verwendet. Das Lackieren erfordert kurze Zeit und niedrige Produktionskosten.
- Überzug: Dies steigert die funktionellen Eigenschaften, unter anderem eine erhöhte Haltbarkeit und Korrosionsbeständigkeit des Zinkdruckgusses.
Entfernt Lager und Buchsen
Die hervorragenden Lager- und Verschleißeigenschaften von Zink ermöglichen eine höhere Designflexibilität und senken die Herstellungskosten durch den Wegfall kleiner Buchsen und Verschleißeinsätze.
Gute elektrische und thermische Leitfähigkeit
Zink ist ein besserer Wärme- und Stromleiter als Aluminium. Daher ist Zinkguss ideal für Anwendungen wie Kühlkörper und andere elektrische Komponenten.
Weniger Bearbeitung erforderlich
Ein großer Vorteil des Zinkdruckgusses ist der geringere Bearbeitungsaufwand. Zinkdruckguss weist engere Toleranzen auf, sodass keine zusätzliche Bearbeitung erforderlich ist.
Nachteile von Zinkdruckguss
Alles, was eine gute Seite hat, hat auch einige Nachteile. Zinkdruckguss bringt folgende Nachteile mit sich:
Ist anfällig für Mängel
Der Zinkdruckgussprozess ist schnell und die Abkühlung erfolgt schnell. Aus diesem Grund kann sich die Gasentladung verzögern, was zu folgenden Defekten führen kann:
- Blasen: Hierbei handelt es sich um dünne Filme, die sich auf der Oberfläche von Zinkdruckgussteilen bilden.
- Risse: Diese treten auf, wenn das Zinkmetall nicht ausreichend fest ist, um der Zugkraft während der Erstarrung standzuhalten.
- Schwellungen: Hierbei handelt es sich um Verlängerungen im Zinkguss, die zu einer glatten Ausbuchtung an der vertikalen Seite des Gusses führen.
- Nichtübereinstimmung oder Verschiebung: Hierbei handelt es sich um eine horizontale Verschiebung eines Metalls aufgrund einer Verformung des oberen und unteren Abschnitts der Form.
- Verschmelzung: Es entsteht, wenn sich Sandpartikel mit geschmolzenem Metall verbinden.
- Blaslöcher: Lunker entstehen, wenn eine unsachgemäße Entlüftung dazu führt, dass das Metall bei der Flüssigkeitsbildung nicht ausreichend Gas aufnimmt.
- Warping: Dies verändert die Abmessungen des Endprodukts und kann während oder nach der Erstarrung auftreten.
- Tropfen: Dies geschieht, wenn Sandstücke in das Gussstück fallen, während das Metall noch in flüssiger Form ist.
Schwere Teile
Aus Zinkdruckguss entstehen wesentlich schwerere Teile als aus anderen Metallen wie Aluminium und Magnesium. Aus diesem Grund sind sie für Leichtbauanwendungen, etwa in der Luft- und Raumfahrtindustrie, nicht geeignet.
Nicht für die Kleinserienproduktion geeignet
Zinkdruckguss hat hohe Anfangsinvestitionskosten. Daher eignet es sich vor allem für die Massenfertigung von Teilen und ist in der Kleinserienfertigung nicht anwendbar.
Anwendungen von Zinkdruckgussteilen
Teile aus Zinkdruckguss werden in verschiedenen Branchen eingesetzt, darunter:
Automobilindustrie
Aufgrund ihrer unglaublichen Festigkeit und Härte, komplexen geometrischen Merkmale, guten Oberflächenqualität, hohen Maßtoleranz und Korrosionsbeständigkeit werden Zinkdruckgusskomponenten in der Automobilindustrie zur Herstellung von:
- Rückspiegel
- Gehäuse
- Fahrwerksteile
- Benutzer- und Fahrzeugsicherheitskomponenten wie Riemenscheiben und Zahnräder
- Getriebekomponenten
- Schiebedach, Scheibenwischer
- Klammern
- Lager
- Lenkung
- Bremsteile
Oben sind nur einige der aus Druckguss hergestellten Automobilkomponenten aufgeführt.
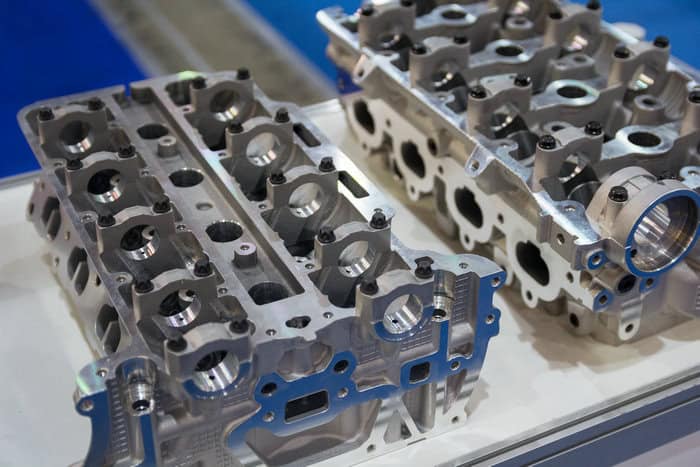
Elektronik
Zinkdruckguss bietet zahlreiche Vorteile in elektronischen Anwendungen. Eine seiner wesentlichen Eigenschaften ist seine Fähigkeit, in dünnere Wände und komplizierte Formen gegossen zu werden. Wie oben erläutert, sind Zinklegierungen härter als andere Druckgussmetalle.
Darüber hinaus verfügt die Zinklegierung über eine hervorragende elektromagnetische Abschirmung und Vibrationsdämpfung, die zum Schutz interner elektrischer Komponenten geeignet ist.
Haushaltsgeräte
Zinkdruckguss gehört zu den besten Druckgussmetallen für Haushaltsgeräte. Aufgrund seiner guten Oberflächenbeschaffenheit, Dimensionsstabilität und Festigkeit wird Zinkguss zur Herstellung von Haushaltsgeräten wie Türschlössern, Mixern, Gürteln, Handmixern, Schuhschnallen, Griffen, Schlüsselanhängern usw. verwendet.
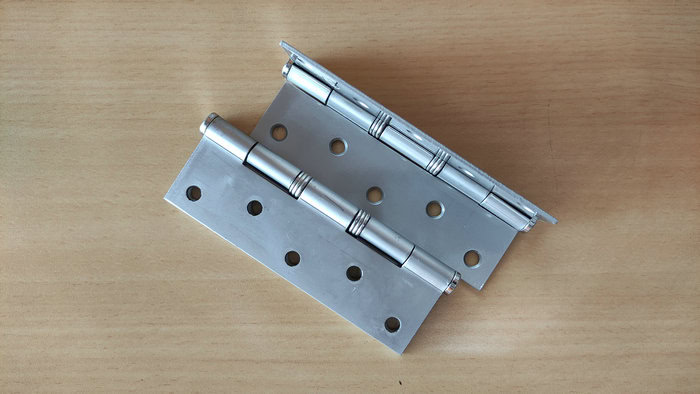
Mechanischer Sektor
Eine weitere bedeutende Anwendung des Zinkdruckgusses liegt im mechanischen Bereich. In diesem Bereich werden bei der Herstellung von Motorenteilen Zinkgussteile verwendet.
Fazit
Der Zinklegierungsguss gehört zu den beliebtesten Gussverfahren. Es bietet mehrere Vorteile gegenüber anderen Metallgussteilen, einschließlich der einfachen und direkten Injektion. Bevor Sie jedoch mit dem Gussprozess beginnen, ist es wichtig, die verschiedenen Verfahren, Legierungen, Anwendungen sowie Vor- und Nachteile zu verstehen.
Um bessere Ergebnisse zu erzielen, sollten Sie die Hilfe zuverlässiger Experten wie Moldie in Anspruch nehmen. Wir bieten hochwertige, maßgeschneiderte Zinkdruckguss-Dienstleistungen zu erschwinglichen Preisen.
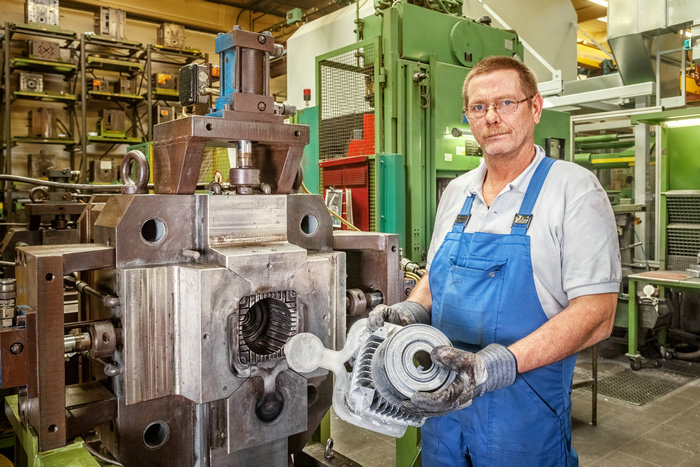
Häufig gestellte Fragen
Wie stabil sind Zinkdruckgussteile?
Zinkdruckguss ist sehr stabil. Sie bieten eine höhere Zugfestigkeit als die gängigsten Nichteisenlegierungen, die beim Druckguss verwendet werden. Beispielsweise haben Zinkdruckgusslegierungen eine etwa 2,5-mal höhere Festigkeit als Aluminium.
Wird Zinkdruckguss rosten?
Nein. Zinkdruckgussteile weisen eine hohe Korrosionsbeständigkeit auf. Wenn Zink Luft und Feuchtigkeit ausgesetzt wird, reagiert es mit Sauerstoff und bildet eine dünne Oxidschicht, die dann mit Feuchtigkeit zu Zinkhydroxid reagiert. Aus diesem Grund rosten Zinkdruckgussteile auch beim Einsatz in korrosiven Umgebungen nicht.
Wenn die Zinkoberfläche jedoch keine vollständige Schutzschicht entwickelt hat, zeigt sie Korrosion, die als Weißrost bezeichnet wird. Dies geschieht, wenn auf der Zinkoberfläche nicht genügend Sauerstoff vorhanden ist. Daher ist der Weißrost pudrig.
Kann Zinkdruckguss geschweißt werden?
Nein. Das Schweißen von Zinkdruckguss kann aufgrund seines niedrigen Schmelzpunkts eine Herausforderung darstellen. Wenn Sie jedoch Materialien wie Super Alloy 1 verwenden, können Sie das Druckgussteil löten.