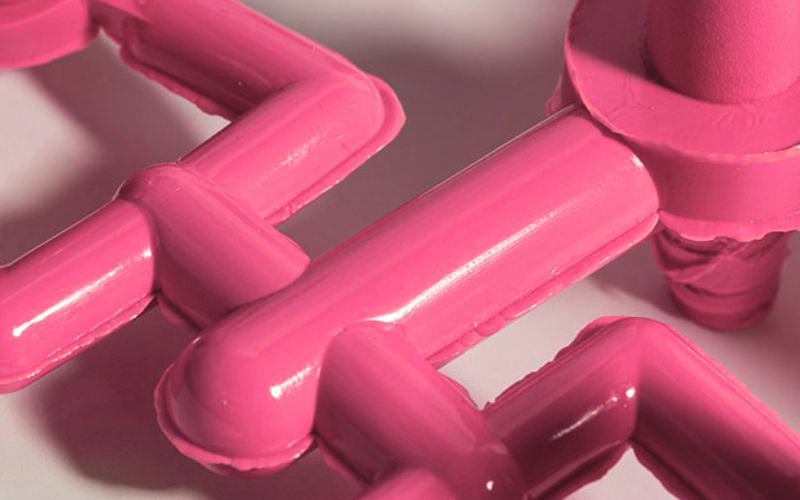
Flash é um defeito comum na fabricação de plástico que pode impactar significativamente a eficiência da produção. À medida que o plástico derretido é injetado na cavidade do molde para formar as peças, o excesso de plástico geralmente vaza pelas bordas. Esse excesso de plástico, chamado flash, forma peças finas e indesejadas ao redor do componente moldado. Se não for controlada, a rebarba se acumula ao longo de vários ciclos de produção, obstruindo as aberturas de ventilação do molde e causando defeitos nos produtos finais. A implementação de locais de gate otimizados, sistemas de corredor e parâmetros de injeção pode minimizar o flash. Isso ajuda os fabricantes a melhorar a qualidade e reduzir o desperdício.
Este artigo irá desvendar o mistério da causa do flash e como prevenir a situação ao iniciar a moldagem.
Principais vantagens:
- Flash é o excesso de plástico que vaza do molde durante a moldagem por injeção, formando abas finas nas peças.
- Normalmente, o flash ocorre nas lacunas da linha de partição, ventilação deficiente, baixa força de fixação, baixa viscosidade, excesso de embalagem e alta pressão de injeção.
- Flash causa processamento adicional, desperdício, danos ao molde e defeitos nas peças, prejudicando a eficiência.
- As soluções envolvem a otimização da localização da porta, dos canais, das configurações do processo e do uso de moldes sem rebarbas.
- A prevenção de flash requer projeto de molde, suporte, força de fixação, configurações de processo e controle de qualidade adequados.
- O padrão é limitar a espessura do flash a menos de 0,1 mm, necessitando de controle e refinamento rígidos do processo.
Introdução ao Flash para Moldagem por Injeção
Quando você está se aventurando no mundo da moldagem por injeção de plástico, é crucial compreender os diversos defeitos que podem ocorrer durante o processo de produção. Um problema comum que você pode encontrar é conhecido como moldagem por injeção instantânea. Flash é essencialmente um excesso de plástico que vaza da cavidade do molde, formando pedaços finos indesejados ao redor das bordas da peça moldada.
Você pode se perguntar por que isso ocorre. Bem, o flash pode ser atribuído a várias causas e geralmente é um sinal revelador de um problema no processo de moldagem ou no projeto do molde. Alguns dos principais culpados incluem:
- Força de fixação inadequada: Pressão insuficiente para vedar as metades do molde pode criar lacunas, permitindo que o plástico escape.
- Desgaste ou danos no molde: Com o tempo, um molde pode sofrer desgaste ou danos, o que pode causar desalinhamento e rebarbas.
- Velocidade ou pressão de injeção excessiva: Muita velocidade ou alta pressão podem forçar a saída do plástico pelas linhas de separação.
Embora lidar com flashes em suas peças plásticas possa parecer assustador, é importante manter uma aparência simplificada. Produção e garantir o design para a capacidade de fabricação. Afinal, você deseja que seu produto final tenha uma aparência elegante e funcione perfeitamente. O Flash não afeta apenas a qualidade estética, mas também o ajuste e a montagem dos produtos acabados.
Compreender e abordar as causas do flash são etapas fundamentais para otimizar seu processo de moldagem por injeção. Isto não só economiza tempo, mas também reduz o desperdício de material e ajuda a manter a qualidade do produto – elementos cruciais para qualquer operação de produção bem-sucedida.
Considerações sobre projeto e ferramentas
Ao projetar para moldagem por injeção, prestar muita atenção ao projeto do molde, ao fluxo do material e ao projeto geral para capacidade de fabricação é essencial para evitar defeitos como rebarbas.
Projeto de moldes e linhas de partição
O projeto do molde é fundamental, pois imperfeições na linha de partição podem causar rebarbas. Certifique-se de que as metades do molde estejam alinhadas com precisão para minimizar quaisquer lacunas ou incompatibilidades. Você vai querer se concentrar em:
- Tolerâncias restritas: Um alto grau de precisão evitará que a resina escorra do molde.
- Superfícies Lisas: As superfícies na linha de partição devem ser lisas para permitir que o molde feche de forma limpa.
Fluxo de material e viscosidade
Controlar o fluxo e a viscosidade do seu material de moldagem é fundamental. Alguns pontos a serem lembrados:
- Propriedades do material: Cada material possui uma viscosidade específica que afeta o fluxo; escolha aquele que se adapta ao design da sua ferramenta.
- Análise de Fluxo: Uma análise de fluxo computacional pode prever como o material preenche o molde, ajudando a prevenir possíveis rebarbas.
Design para Manufaturabilidade (DFM)
Projetar peças tendo em mente a capacidade de fabricação é essencial para um processo de moldagem sem rebarbas. Focar em:
- Ângulos de inclinação: Ângulos adequados facilitam a remoção do molde e reduzem o risco de rebarbas.
- Localização do portão: Isso afeta tudo, desde a estética até a integridade estrutural da peça. O posicionamento adequado é crucial.
Parâmetros do processo de moldagem por injeção
Na moldagem por injeção, o controle preciso dos parâmetros do processo é essencial para a qualidade do produto final. Temperatura, pressão e taxa de injeção são os pilares que definem a moldabilidade, resistência e aparência do item que você está criando.
Controle de temperatura
Gerenciar a temperatura é vital, pois afeta a viscosidade do material e o fluxo no molde. As temperaturas do cilindro e do bico precisam ser definidas com precisão dentro da faixa de temperatura especificada para o material que você está usando.
- Temperatura do barril: Geralmente é definida em uma faixa que garante que o material esteja fundido e flua facilmente, sem se degradar.
- Temperatura do bocal: Ligeiramente inferior à do cano para evitar solidificação prematura que pode levar a defeitos.
Pressão de injeção e força de fixação
A pressão de injeção ajuda a empurrar o material fundido para todas as partes do molde. Precisa ser alto o suficiente para preencher completamente o molde, mas equilibrado para evitar excessos:
- Pressão de fixação: Deve ser suficiente para manter o molde fechado contra a força do material injetado, evitando rebarbas.
Parâmetro | Propósito |
---|---|
Pressão de injeção | Força o material para dentro do molde. |
Pressão de fixação | Mantém as metades do molde juntas durante a injeção. |
Abaixo estão as funções específicas de cada tipo de pressão:
- Pressão de injeção: Garante o preenchimento completo da cavidade e a integridade estrutural.
- Pressão de fixação: Contraria a força externa para evitar separação e defeitos do molde.
Taxa de injeção e processo de retenção
A velocidade com que o material é injetado – a taxa de injeção – afeta a consistência e a qualidade do produto. Uma taxa adequada garante o enchimento suave do molde e reduz defeitos. Após o enchimento, o processo de retenção aplica pressão para compensar o encolhimento do material à medida que ele esfria, garantindo que o produto final mantenha as dimensões corretas.
Estágio | Impacto |
---|---|
Taxa de injeção | Determina a rapidez com que a cavidade do molde é preenchida. |
Processo de retenção | Mantém a pressão após a injeção para garantir a qualidade. |
Compreender e controlar esses parâmetros afetará significativamente a eficiência do seu processo de moldagem por injeção e a qualidade dos itens que você produz.
Causas e prevenção do Flash
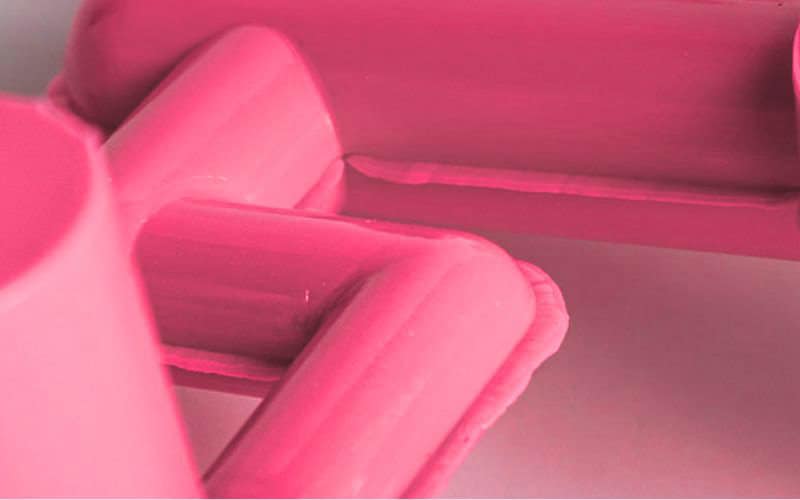
Ao abordar a questão das rebarbas na moldagem por injeção, compreender as causas é crucial para uma prevenção eficaz. Veja como você pode manter a integridade de suas peças moldadas concentrando-se nas principais áreas de preocupação.
Identificando causas comuns
Contaminantes Ambientais: Poeira e detritos podem impedir que o molde feche totalmente na linha de separação, permitindo que o plástico derretido escape.
Problemas de molde:
- Incompatibilidades nas linhas de partição: Isso acontece quando as duas metades do molde não se alinham perfeitamente.
- Componentes do molde desgastados: Com o tempo, os componentes do molde podem se desgastar, proporcionando oportunidades para a ocorrência de flashes.
Imperfeições no molde e o desalinhamento da linha de partição são os principais contribuintes para a formação de rebarbas. A manutenção regular e o manuseio cuidadoso dos componentes do molde são vitais para evitar esses problemas.
Estratégias eficazes de ventilação e vedação
Colocação e tamanho da ventilação:
- Posicione as aberturas de ventilação no final dos caminhos de fluxo para auxiliar no escape de ar.
- Certifique-se de que as aberturas estejam dimensionadas adequadamente; muito pequenos e são ineficazes, muito grandes e permitem que o plástico escape.
Componentes de vedação:
- Inspecione os anéis de vedação e as vedações regularmente quanto a desgaste e danos.
- Use os materiais certos que resistam às temperaturas e pressões envolvidas no processo.
Ventilação e vedação adequadas são essenciais para controlar o fluxo de plástico fundido. Ao permitir que o ar escape da cavidade do molde de forma eficiente, você ajuda a evitar o acúmulo de pressão que pode criar rebarbas.
Otimizando a pressão e a tonelagem de fixação
- Pressão de fixação: Ajuste a força de fixação para garantir que o molde permaneça fechado durante o processo de injeção.
- Tonelagem de fixação: Uma tonelagem mais alta pode ser aplicada para neutralizar as forças que separam as metades do molde.
Ajuste a pressão de fixação e a tonelagem de acordo com o material e o projeto do molde com o qual você está trabalhando. A baixa pressão de fixação pode ser uma causa de rebarbas, pois as seções do molde podem não ser mantidas suficientemente unidas contra a força do material de entrada. É fundamental que você encontre um equilíbrio – muita pressão pode danificar o molde, enquanto pouca pressão pode causar defeitos.
Maneiras de consertar Flash no processo de moldagem por injeção
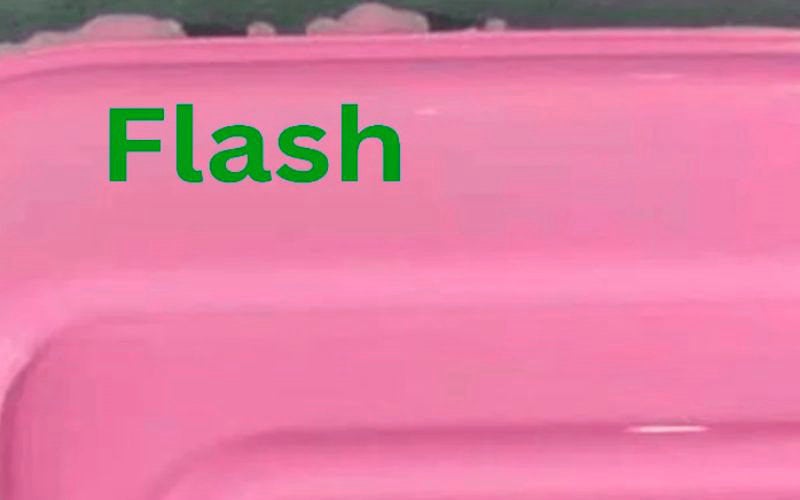
O flash na moldagem por injeção costuma ser um sinal de um problema no processo de moldagem, onde o excesso de material escapa da cavidade do molde, criando abas ou saliências indesejadas. Aqui estão estratégias eficazes para mitigar esse problema:
Modificações de projeto
Fazer alterações no design pode ser um passo significativo para evitar flashes. Considere otimizar seu design para capacidade de fabricação (DFM), o que garante que o design do seu produto possa ser fabricado perfeitamente, sem defeitos como flash.
Manutenção de Moldes
Um molde bem conservado tem menos probabilidade de produzir rebarbas. Certifique-se de que seus moldes sejam limpos regularmente e que qualquer dano ou desgaste seja resolvido imediatamente. Um cronograma de manutenção adequado pode ajudar a prolongar a vida útil do molde e melhorar a qualidade das peças moldadas.
Processo otimizado
Ajuste os parâmetros do processo de moldagem por injeção, como temperatura e velocidade de injeção, para reduzir a ocorrência de flash. A baixa pressão de fixação ou o ajuste incorreto dos parâmetros de processamento podem fazer com que o material fundido saia do molde.
Força de aperto
Aumente a força de fixação para garantir que as metades do molde estejam fechadas com segurança. Isto é fundamental porque se o molde não estiver devidamente fechado, o plástico pode vazar, causando rebarbas.
Viscosidade do Material
Garantir a viscosidade correta do material é essencial. Uma viscosidade mais baixa aumenta a probabilidade do material fluir para fora do molde, resultando em rebarbas. Você pode controlar a viscosidade por meio de configurações de temperatura e seleção de material.
Lembre-se de que diagnosticar e corrigir rebarbas em seu processo de moldagem por injeção pode economizar custos e melhorar a qualidade de seu produto final. Consulte especialistas e aproveite recursos abrangentes, como os insights fornecidos em “O que causa e como evitar flash no processo de moldagem por injeção,” para entender melhor e resolver problemas relacionados ao flash.
Defeitos e solução de problemas
Na moldagem por injeção, resolver prontamente os defeitos garante a longevidade dos seus moldes e a qualidade dos seus produtos. Vamos explorar os problemas comuns e suas soluções.
Defeitos comuns de moldagem por injeção
A moldagem por injeção é suscetível a vários defeitos que podem afetar o acabamento superficial e a qualidade do produto. Flash, também conhecido como flashing de molde, é particularmente problemático. É o excesso indesejado de material que aparece ao longo da linha de partição ou em outras áreas de separação no molde, muitas vezes resultando em uma fina aleta de plástico no produto acabado. Outros defeitos frequentes incluem:
- Warping: Distorção que ocorre devido ao resfriamento irregular.
- Marcas de afundamento: Pequenas crateras ou depressões devido a resfriamento ou enchimento insuficiente.
- Tiros Curtos: Peças incompletas devido à injeção insuficiente de material.
Identificar esses defeitos no início do processo de produção é crucial para manter o mais alto nível de qualidade do produto.
Solução de problemas do Flash
Para solucionar problemas de flash, aqui estão as etapas específicas que você pode seguir:
- Inspeção do Molde: Verifique se há danos ou detritos que possam impedir o fechamento completo do molde.
- Integridade da linha de partição: Certifique-se de que a linha de partição corresponda corretamente, sem qualquer desalinhamento.
- Pressão de fixação do molde: Ajuste a pressão de fixação; pressão muito baixa permite que ocorra flash.
- Material e Processo: Verifique se a viscosidade do material é apropriada e otimize a pressão e a velocidade de injeção.
No caso de contaminantes, como poeira ou sujeira, uma limpeza completa do molde pode resolver o problema. Para a remoção de rebarbas, várias técnicas como corte manual ou processos químicos podem ser utilizadas, mas a prevenção é sempre preferível. Lembre-se de que uma abordagem consistente e vigilante à solução de problemas pode economizar tempo e reduzir significativamente a ocorrência de defeitos.
Pós-processamento e controle de qualidade
Depois que suas peças moldadas por injeção emergem do molde, elas nem sempre estão prontas para o cliente. Provavelmente, você precisará realizar um pós-processamento para remover o excesso de material e garantir que as peças atendam aos padrões de qualidade. As subseções a seguir fornecem informações sobre as técnicas de rebarbação e as medidas para garantia de qualidade.
Técnicas e equipamentos de rebarbação
A rebarbação é uma etapa crítica no pós-processamento para remover qualquer rebarba indesejada de suas peças moldadas por injeção. Aqui está uma visão concisa de alguns métodos comuns:
- Rebarbação manual: Você pode usar tesouras ou facas para tarefas simples de rebarbação, tornando-a uma opção direta e acessível. No entanto, requer precisão e pode exigir muito trabalho.
- Rebarbação criogênica: Esta técnica envolve congelar as peças com nitrogênio líquido para tornar a rebarbação quebradiça, que pode ser facilmente removida. É eficaz para peças complexas e materiais de policarbonato.
O equipamento escolhido depende da geometria dos componentes, do material e do grau de qualidade da superfície necessária.
Garantia de qualidade para peças moldadas por injeção
A garantia de qualidade é vital para garantir a funcionalidade e estética das suas peças:
- Inspeção Visual: Realize uma verificação visual completa em busca de defeitos e imperfeições superficiais.
- Inspeção Dimensional: Use calibradores e micrômetros para garantir que suas peças atendam às especificações dimensionais.
Lembre-se de que peças moldadas por injeção de alta qualidade não apresentam defeitos como rebarbas e apresentam qualidade de superfície consistente, o que reflete bem em sua marca e ajuda a evitar retrabalhos dispendiosos.
Concluindo, abordar adequadamente as questões de moldagem no projeto do processo oferece benefícios substanciais para a eficiência e. Minimizar a geração de flash reduz o corte e o desperdício de plástico. Também evita o acúmulo de moldes, prolongando o tempo de inatividade do ferramental. Moldes com flash mínimo podem funcionar por mais tempo entre os ciclos de manutenção com alto rendimento. Combinado com o ajuste do processo de velocidade de injeção e pressão de empacotamento, os fabricantes ganham custos diretos por peça produzida. Ao adotar uma abordagem holística para a redução de rebarbas, os fabricantes de produtos plásticos podem agilizar a produção ao longo de todo o ciclo de vida do componente.