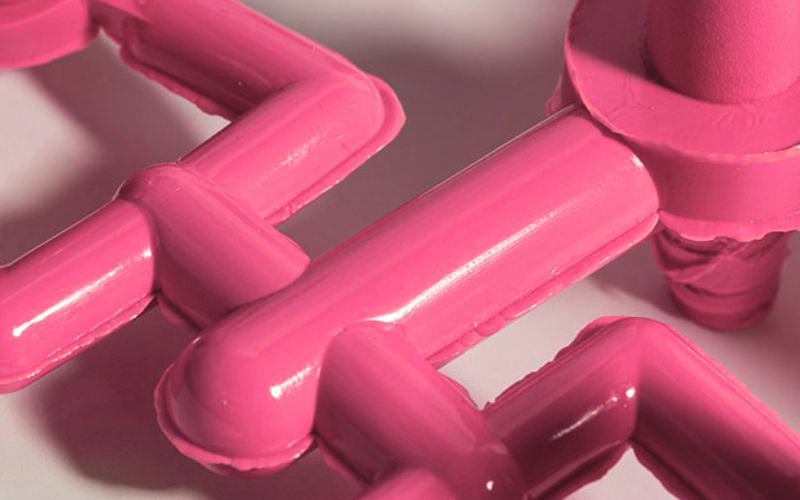
La inflamación es un defecto común en la fabricación de plástico que puede afectar significativamente la eficiencia de la producción. A medida que se inyecta plástico fundido en la cavidad de un molde para formar piezas, el exceso de plástico a menudo se escapa por los bordes. Este exceso de plástico, llamado rebaba, forma finas piezas no deseadas alrededor del componente moldeado. Si no se controla, las rebabas se acumulan a lo largo de múltiples ciclos de producción, obstruyendo las rejillas de ventilación del molde y provocando defectos en los productos finales. La implementación de ubicaciones de compuerta optimizadas, sistemas de canales y parámetros de inyección puede minimizar la rebaba. Esto ayuda a los fabricantes a mejorar la calidad y reducir el desperdicio.
Este artículo revelará el misterio de la causa del flash y cómo prevenir la situación al comenzar a moldear.
Conclusiones clave:
- La rebaba es el exceso de plástico que se escapa del molde durante el moldeo por inyección, formando aletas delgadas en las piezas.
- Por lo general, la rebaba ocurre en los espacios de las líneas de separación, ventilación deficiente, fuerza de sujeción baja, viscosidad baja, empaquetamiento excesivo y presión de inyección alta.
- La rebaba provoca procesamiento adicional, desperdicio, daños en el molde y defectos en las piezas, lo que perjudica la eficiencia.
- Las soluciones implican optimizar la ubicación de la puerta, los canales, la configuración del proceso y el uso de moldes sin rebabas.
- La prevención de rebabas requiere un diseño de molde, soporte, fuerza de sujeción, configuración de proceso y control de calidad adecuados.
- El estándar es limitar el espesor de las rebabas a menos de 0,1 mm, lo que requiere un estricto control y refinamiento del proceso.
Introducción al flash de moldeo por inyección
Cuando se aventura en el mundo del moldeo por inyección de plástico, es fundamental comprender los diversos defectos que pueden ocurrir durante el proceso de producción. Un problema común que puede encontrar se conoce como moldeo por inyección flash. La rebaba es esencialmente un exceso de plástico que se filtra fuera de la cavidad del molde, formando piezas delgadas no deseadas alrededor de los bordes de la pieza moldeada.
Quizás te preguntes por qué ocurre esto. Bueno, la rebaba se puede atribuir a varias causas y, a menudo, es una señal reveladora de un problema en el proceso de moldeo o en el diseño del molde. Algunos de los principales culpables incluyen:
- Fuerza de sujeción inadecuada: Una presión insuficiente para sellar las mitades del molde puede crear espacios que permitan que el plástico se escape.
- Desgaste o daño del molde: Con el tiempo, un molde puede sufrir desgaste o daños, lo que puede provocar desalineación y rebabas.
- Velocidad o presión de inyección excesiva: Demasiada velocidad o presión alta pueden expulsar el plástico a través de las líneas de separación.
Si bien lidiar con el flash en las piezas de plástico puede parecer desalentador, es importante para mantener un producción y garantizar el diseño para la capacidad de fabricación. Después de todo, desea que su producto final luzca elegante y funcione perfectamente. Flash no sólo afecta la calidad estética sino también el ajuste y montaje de los productos terminados.
Comprender y abordar las causas de la rebaba son pasos clave para optimizar su proceso de moldeo por inyección. Esto no solo le ahorra tiempo sino que también reduce el desperdicio de material y ayuda a mantener la calidad del producto, elementos cruciales para cualquier operación de producción exitosa.
Consideraciones de diseño y herramientas
Al diseñar para moldeo por inyección, es esencial prestar mucha atención al diseño del molde, el flujo de material y el diseño general para la capacidad de fabricación para evitar defectos como la rebaba.
Diseño de moldes y líneas de separación
El diseño de su molde es fundamental, ya que las imperfecciones en la línea de separación pueden provocar rebabas. Asegúrese de que las mitades del molde se alineen con precisión para minimizar cualquier espacio o desajuste. Querrás concentrarte en:
- Tolerancias estrictas: un alto grado de precisión evitará que la resina se salga del molde.
- Superficies lisas: Las superficies en la línea de separación deben ser lisas para permitir que el molde se cierre limpiamente.
Flujo de materiales y viscosidad
Controlar el flujo y la viscosidad de su material de moldeo es fundamental. Algunos puntos a tener en cuenta:
- Propiedades del material: Cada material tiene una viscosidad específica que afecta el flujo; elija uno que se adapte al diseño de su herramienta.
- Análisis de flujo: un análisis de flujo computacional puede predecir cómo el material llena el molde, lo que ayuda a prevenir posibles rebabas.
Diseño para la fabricabilidad (DFM)
Diseñar piezas teniendo en cuenta la capacidad de fabricación es esencial para un proceso de moldeo sin rebabas. Concentrarse en:
- Ángulos de desmoldeo: Los ángulos adecuados facilitan la extracción del molde y reducen el riesgo de rebabas.
- Ubicación de la puerta: esto afecta todo, desde la estética hasta la integridad estructural de la pieza. La colocación adecuada es crucial.
Parámetros del proceso de moldeo por inyección
En el moldeo por inyección, el control preciso de los parámetros del proceso es esencial para la calidad del producto final. La temperatura, la presión y la velocidad de inyección son los pilares que definen la moldeabilidad, la resistencia y la apariencia del artículo que estás creando.
Control de temperatura
Controlar la temperatura es vital, ya que afecta la viscosidad del material y el flujo hacia el molde. Las temperaturas del cilindro y de la boquilla deben ajustarse con precisión dentro del rango de temperatura especificado para el material que esté utilizando.
- Temperatura del barril: generalmente se establece en un rango que garantiza que el material se funda y fluya fácilmente, sin degradarse.
- Temperatura de la boquilla: Ligeramente inferior a la del cañón para evitar una solidificación prematura que podría provocar defectos.
Presión de inyección y fuerza de sujeción
La presión de inyección ayuda a empujar el material fundido hacia todas las partes del molde. Tiene que ser lo suficientemente alto para llenar el molde por completo pero equilibrado para evitar excesos:
- Presión de sujeción: Debe ser suficiente para mantener el molde cerrado contra la fuerza del material inyectado, evitando la rebaba.
Parámetro | Objetivo |
---|---|
Presión de inyección | Fuerza el material hacia el molde. |
Presión de sujeción | Mantiene juntas las mitades del molde durante la inyección. |
A continuación se detallan las funciones específicas de cada tipo de presión:
- Presión de inyección: Garantiza el llenado completo de la cavidad y la integridad estructural.
- Presión de sujeción: Contrarresta la fuerza hacia afuera para evitar la separación del molde y defectos.
Tasa de inyección y proceso de retención
La velocidad a la que se inyecta el material (la velocidad de inyección) afecta la consistencia y la calidad del producto. Una tasa adecuada garantiza un llenado suave del molde y reduce los defectos. Después del llenado, el proceso de retención aplica presión para compensar la contracción del material a medida que se enfría, lo que garantiza que el producto final mantenga las dimensiones correctas.
Fase | Impacto |
---|---|
Tasa de inyección | Determina la rapidez con la que se llena la cavidad del molde. |
Proceso de retención | Mantiene la presión después de la inyección para garantizar la calidad. |
Comprender y controlar estos parámetros afectará significativamente la eficiencia de su proceso de moldeo por inyección y la calidad de los artículos que produzca.
Causas y prevención del flash
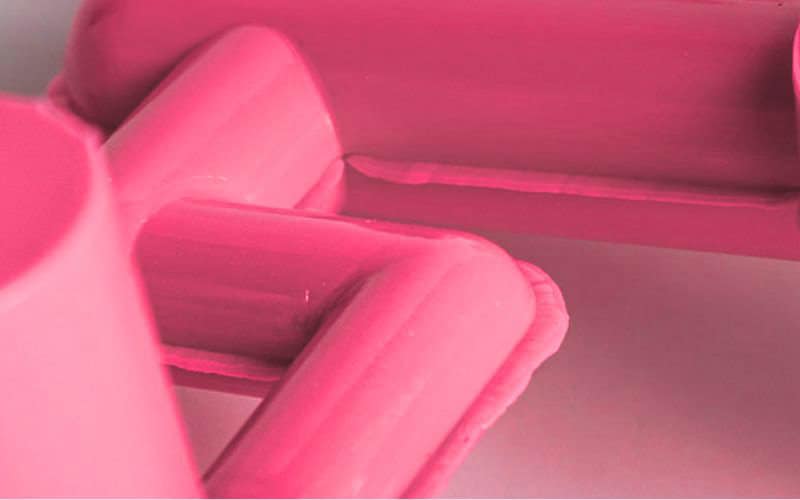
Al abordar el problema de la rebaba en el moldeo por inyección, comprender las causas es fundamental para una prevención eficaz. A continuación le mostramos cómo puede mantener la integridad de sus piezas moldeadas centrándose en áreas clave de preocupación.
Identificar causas comunes
Contaminantes ambientales: El polvo y los escombros pueden impedir que el molde se cierre completamente en la línea de separación, permitiendo que se escape el plástico fundido.
Problemas de moho:
- Faltas de coincidencia en la línea de separación: esto sucede cuando las dos mitades del molde no se alinean perfectamente.
- Componentes desgastados del molde: con el tiempo, los componentes del molde pueden desgastarse, lo que genera oportunidades para que se produzcan rebabas.
Las imperfecciones en el molde y la desalineación de la línea de separación son los principales contribuyentes a la formación de rebabas. El mantenimiento regular y el manejo cuidadoso de los componentes del molde son vitales para prevenir estos problemas.
Estrategias efectivas de ventilación y sellado
Ubicación y tamaño de ventilación:
- Coloque las rejillas de ventilación al final de las vías de flujo para facilitar el escape del aire.
- Asegúrese de que los respiraderos tengan el tamaño adecuado; demasiado pequeños y son ineficaces, demasiado grandes y dejan escapar el plástico.
Componentes de sellado:
- Inspeccione periódicamente las juntas tóricas y los sellos para detectar desgaste y daños.
- Utilice materiales adecuados que resistan las temperaturas y presiones involucradas en el proceso.
La ventilación y el sellado adecuados son esenciales para controlar el flujo de plástico fundido. Al permitir que el aire escape de la cavidad del molde de manera eficiente, ayuda a prevenir la acumulación de presión que puede generar rebabas.
Optimización de la presión de sujeción y el tonelaje
- Presión de sujeción: ajuste la fuerza de sujeción para garantizar que el molde permanezca cerrado durante el proceso de inyección.
- Tonelaje de sujeción: Se puede aplicar un tonelaje más alto para contrarrestar las fuerzas que separan las mitades del molde.
Ajuste la presión de sujeción y el tonelaje para adaptarlos al material y al diseño del molde con el que esté trabajando. La baja presión de sujeción puede ser una causa de rebaba, ya que es posible que las secciones del molde no se mantengan lo suficientemente juntas contra la fuerza del material entrante. Es fundamental encontrar un equilibrio: demasiada presión puede dañar el molde, mientras que muy poca puede provocar defectos.
Formas de reparar el flash en el proceso de moldeo por inyección
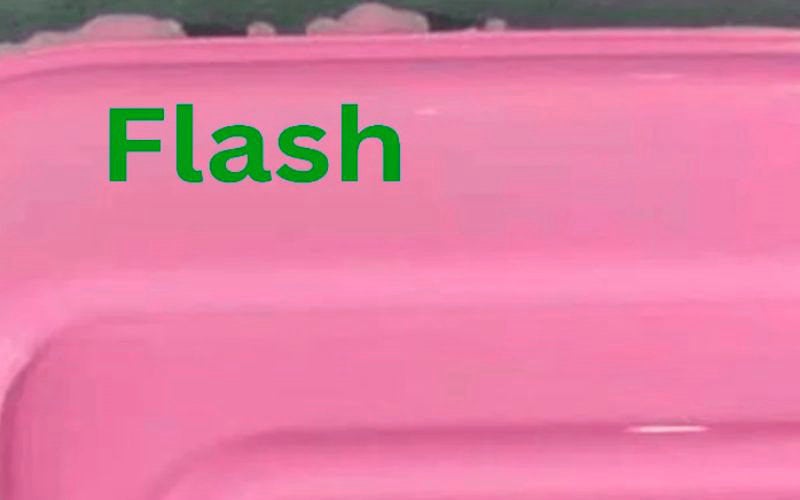
La rebaba en el moldeo por inyección suele ser una señal de un problema dentro del proceso de moldeo, donde el exceso de material se escapa de la cavidad del molde, creando solapas o protuberancias no deseadas. Aquí hay estrategias efectivas para mitigar este problema:
Modificaciones de diseño
Realizar cambios de diseño puede ser un paso importante hacia la prevención del flash. Considere optimizar su diseño para la capacidad de fabricación (DFM), lo que garantiza que el diseño de su producto se pueda fabricar sin problemas y sin defectos como flash.
Mantenimiento de moldes
Es menos probable que un molde bien mantenido produzca rebabas. Asegúrese de que sus moldes se limpien con regularidad y de que cualquier daño o desgaste se solucione de inmediato. Un programa de mantenimiento adecuado puede ayudar a prolongar la vida útil del molde y mejorar la calidad de sus piezas moldeadas.
Optimización de procesos
Ajuste los parámetros del proceso de moldeo por inyección, como la temperatura y la velocidad de inyección, para reducir la aparición de rebabas. Una presión de sujeción baja o un ajuste incorrecto de los parámetros de procesamiento podrían provocar que el material fundido se filtrara fuera del molde.
Fuerza de sujecion
Aumente la fuerza de sujeción para garantizar que las mitades del molde estén cerradas de forma segura. Esto es fundamental porque si el molde no se cierra correctamente, el plástico puede filtrarse y provocar rebabas.
Viscosidad del material
Es fundamental garantizar la viscosidad correcta del material. Una viscosidad más baja aumenta la probabilidad de que el material fluya fuera del molde, lo que resulta en rebabas. Puede controlar la viscosidad mediante ajustes de temperatura y selección de materiales.
Recuerde, diagnosticar y corregir rebabas en su proceso de moldeo por inyección puede ahorrar costos y mejorar la calidad de su producto final. Consulte a expertos y aproveche recursos integrales, como los conocimientos proporcionados en "Qué causas y cómo evitar la inflamación en el proceso de moldeo por inyección”, para comprender y resolver mejor los problemas relacionados con el flash.
Defectos y solución de problemas
En el moldeo por inyección, abordar los defectos con prontitud garantiza la longevidad de sus moldes y la calidad de sus productos. Exploremos los problemas comunes y sus soluciones.
Defectos comunes del moldeo por inyección
El moldeo por inyección es susceptible a varios defectos que pueden afectar el acabado de la superficie y la calidad del producto. El flasheo, también conocido como tapajuntas de molde, es particularmente problemático. Es el exceso de material no deseado que aparece a lo largo de la línea de separación u otras áreas de separación en el molde, lo que a menudo resulta en una fina aleta de plástico en el producto terminado. Otros defectos frecuentes incluyen:
- Warping: Distorsión que se produce debido a un enfriamiento desigual.
- Marcas de hundimiento: Pequeños cráteres o depresiones debido a un enfriamiento o llenado insuficiente.
- Planos cortos: Piezas incompletas por inyección insuficiente de material.
Identificar estos defectos en las primeras etapas del proceso de producción es crucial para mantener el más alto nivel de calidad del producto.
Solución de problemas de flash
Para solucionar problemas de flash, estos son pasos específicos que puede seguir:
- Inspección del molde: verifique si hay daños o residuos que puedan impedir que el molde se cierre por completo.
- Integridad de la línea de separación: asegúrese de que la línea de separación coincida correctamente sin ninguna desalineación.
- Presión de sujeción del molde: ajuste la presión de sujeción; una presión demasiado baja permite que se produzca un destello.
- Material y proceso: Verifique que la viscosidad del material sea adecuada y optimice la presión y velocidad de inyección.
En el caso de contaminantes, como polvo o suciedad, una limpieza profunda del molde podría solucionar el problema. Para eliminar las rebabas, se pueden utilizar diversas técnicas, como el recorte manual o procesos químicos, pero siempre es preferible la prevención. Recuerde, un enfoque coherente y atento a la resolución de problemas puede ahorrar tiempo y reducir significativamente la aparición de defectos.
Postprocesamiento y Control de Calidad
Una vez que las piezas moldeadas por inyección salen del molde, no siempre están listas para el cliente. Es probable que deba realizar un posprocesamiento para eliminar el exceso de material y garantizar que las piezas cumplan con los estándares de calidad. Las siguientes subsecciones brindan información sobre las técnicas de desbarbado y las medidas para garantizar la calidad.
Técnicas y equipos de desbarbado
El desbarbado es un paso fundamental en el posprocesamiento para eliminar cualquier rebaba no deseada de las piezas moldeadas por inyección. A continuación se ofrece un vistazo conciso a algunos métodos comunes:
- Desbarbado manual: Puedes utilizar tijeras o cuchillos para tareas sencillas de desbarbado, lo que lo convierte en una opción directa y asequible. Sin embargo, requiere precisión y puede requerir mucha mano de obra.
- Desbarbado criogénico: esta técnica implica congelar las piezas con nitrógeno líquido para hacer que el destello se vuelva quebradizo, que luego se puede quitar fácilmente. Es eficaz para piezas complejas y materiales de policarbonato.
El equipo que elija depende de la geometría de los componentes, el material y el grado de calidad de la superficie requerido.
Garantía de calidad para piezas moldeadas por inyección
El aseguramiento de la calidad es vital para garantizar la funcionalidad y estética de sus piezas:
- Inspección visual: realice una verificación visual exhaustiva para detectar defectos e imperfecciones en la superficie.
- Inspección dimensional: utilice calibradores y micrómetros para asegurarse de que sus piezas cumplan con sus especificaciones dimensionales.
Recuerde, las piezas moldeadas por inyección de alta calidad están libres de defectos como rebabas y exhiben una calidad superficial constante, lo que refleja bien su marca y ayuda a evitar costosas repeticiones.
En conclusión, abordar adecuadamente los problemas de diseño de procesos de moldeo ofrece beneficios sustanciales para la eficiencia y. Al minimizar la generación de destellos se reducen los recortes y los residuos de plástico. También previene la acumulación de moldes, extendiendo el tiempo de inactividad del utillaje. Los moldes con mínima rebaba pueden funcionar durante más tiempo entre ciclos de mantenimiento con un alto rendimiento. Combinado con el ajuste del proceso de velocidad de inyección y presión de empaque, los fabricantes obtienen costos por pieza producida. Al adoptar un enfoque holístico para la reducción de rebabas, los fabricantes de productos plásticos pueden optimizar la producción durante todo el ciclo de vida de los componentes.