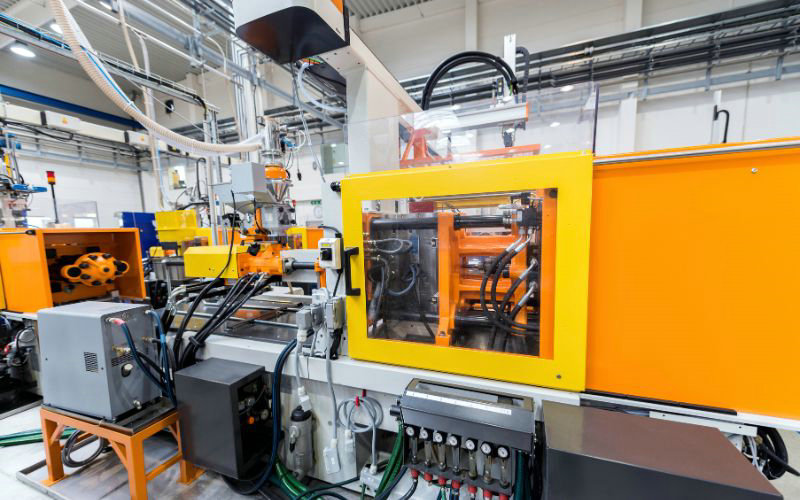
Projekt układu chłodzenia formy wtryskowej
Układ chłodzenia zapewnia równomierne chłodzenie i skuteczną kontrolę temperatury podczas projektowania formy wtryskowej. Wpływa to nie tylko na jakość wypraski, ale także znacząco wpływa na czas cyklu i wydajność chłodzenia. Przegrody, bełkotki i kołki termiczne to specjalistyczne strategie chłodzenia stosowane w celu optymalizacji rozkładu temperatury w formach wtryskowych, szczególnie w trudnych obszarach, do których nie można skutecznie dotrzeć zwykłymi wywierconymi kanałami. Poprawiają odprowadzanie ciepła poprzez zwiększenie powierzchni styku chłodziwa lub wykorzystanie wymiany ciepła ze zmianą fazową. Prawidłowe zaprojektowanie tych elementów ma kluczowe znaczenie dla uzyskania równomiernego chłodzenia części i zminimalizowania czasu cykli. Zagłębmy się teraz w ich unikalne funkcje:
Przegrody
- Przegroda to kanał chłodzący wywiercony prostopadle do głównego przewodu chłodzącego, wyposażony w ostrze dzielące kanał na dwa półkoliste kanały.
- Chłodziwo przepływa jedną stroną ostrza z przewodu głównego, obraca się wokół końcówki na drugą stronę, a następnie przepływa z powrotem do przewodu głównego.
- Przegrody zwiększają powierzchnię, do której może dotrzeć chłodziwo w obszarach, w których normalnie nie byłoby chłodzenia.
- Blachę tworzącą przegrodę można skręcić w kształcie spirali o średnicy 12–50 mm, aby zapewnić bardziej jednorodny rozkład temperatury.
- Kolejnym rozwinięciem przegród są rdzenie spiralne o pojedynczym lub podwójnym zwoju.
Bąbelki
- Bubbler jest podobny do przegrody, ale zastępuje ostrze małą rurką.
- Czynnik chłodzący wpływa do dolnej części rury i „bulgocze” u góry, a następnie spływa po zewnętrznej stronie rury z powrotem do głównego kanału.
- Bubblery zapewniają najskuteczniejsze chłodzenie smukłych rdzeni.
- Stosunek średnicy wewnętrznej i zewnętrznej bełkotki powinien wynosić 0,707, aby uzyskać jednakowy opór przepływu.
- Pęcherzyki można również stosować do chłodzenia płaskich sekcji formy, w których nie mieszczą się wywiercone kanały.
Kołki termiczne
- Kołek termiczny jest alternatywą dla przegród i bełkotek, które składają się z uszczelnionego cylindra wypełnionego płynem.
- Płyn odparowuje, pobierając ciepło z formy, i skrapla się, oddając ciepło do chłodziwa w sposób ciągły.
- Kołki termiczne mają wydajność wymiany ciepła prawie 10 razy większą niż wkładki z miedzi lub stopów miedzi.
- Należy unikać szczelin powietrznych pomiędzy kołkiem termicznym a formą lub wypełnić je wysoce przewodzącym uszczelniaczem w celu zapewnienia optymalnego przewodzenia ciepła.
Różne typy systemów chłodzenia form wtryskowych
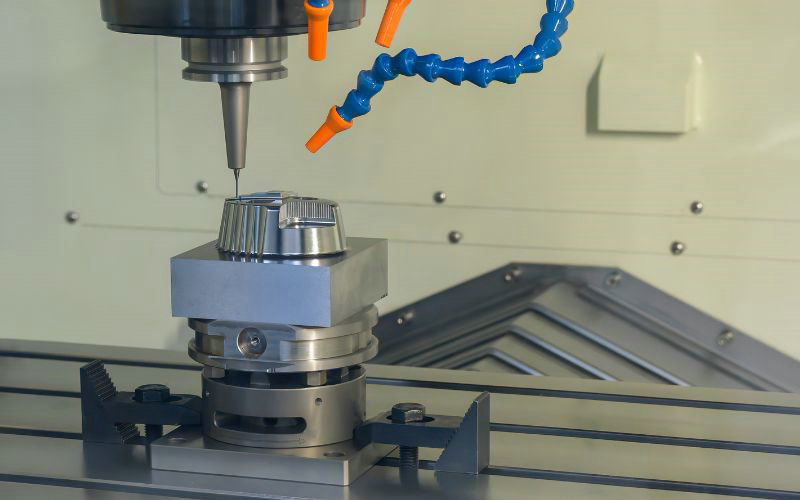
Właściwy system chłodzenia zapewnia równomierny rozkład temperatury, minimalizuje wypaczenia i skurcze oraz sprzyja efektywności energetycznej i efektywności chłodzenia.
Systemy chłodzone wodą
Układy chłodzone wodą są najczęściej stosowaną metodą chłodzenia przy formowaniu wtryskowym ze względu na ich wydajność i skuteczność w odprowadzaniu ciepła. Systemy te powodują cyrkulację schłodzonej wody przez kanały w formie, pochłaniając ciepło z formy i stopionego tworzywa sztucznego. Metoda ta jest szczególnie skuteczna w przypadku skomplikowanych form i materiałów wrażliwych na temperaturę, ponieważ zapewnia doskonałą kontrolę temperatury i zdolność pochłaniania ciepła.
Systemy chłodzone powietrzem
Systemy chłodzone powietrzem wykorzystują wentylatory lub dmuchawy do odprowadzania ciepła z powierzchni formy poprzez konwekcję. Metoda ta jest prostsza i tańsza w zastosowaniu w porównaniu z systemami chłodzonymi wodą. Chłodzenie powietrzem jest odpowiednie w przypadku mniej skomplikowanych konstrukcji form i materiałów, które są mniej wrażliwe na wahania temperatury. Jednak jest mniej skuteczny w absorpcji ciepła i kontroli temperatury w porównaniu z systemami chłodzonymi wodą.
Układy chłodzone olejem
Układy chłodzone olejem są stosowane w scenariuszach, w których wymagane jest bardzo szybkie chłodzenie. W tych systemach następuje cyrkulacja oleju, który może odprowadzać ciepło skuteczniej niż powietrze. Chłodzenie oleju jest na ogół droższe niż chłodzenie wodą lub powietrzem, ale jest preferowane w dużych operacjach formowania wtryskowego lub w przypadku materiałów wymagających bardzo szybkiego przejścia z wysokich do niskich temperatur.
Kriogeniczne systemy chłodzenia
Kriogeniczne systemy chłodzenia wykorzystują substancje o wyjątkowo niskiej temperaturze, takie jak ciekły azot, do szybkiego schłodzenia formy. Ta zaawansowana metoda może znacznie skrócić czas chłodzenia i zużycie energii, ale jest zwykle zarezerwowana dla zastosowań specjalnych ze względu na złożoność i koszty.
Mieszane systemy chłodzenia
Aby dostosować zarządzanie ciepłem, możesz spotkać się z systemami chłodzenia wykorzystującymi mieszane media, które łączą różne czynniki chłodzące, takie jak powietrze i woda. Te systemy hybrydowe mają na celu wykorzystanie zalet każdego medium, takich jak szybkie chłodzenie wody przy prostocie systemów powietrznych, optymalizując wydajność dla określonych zastosowań formowania wtryskowego.
Wpływ chłodzenia formy wtryskowej na wyroby formowane

Faza chłodzenia w procesie formowania wtryskowego odgrywa kluczową rolę w określaniu jakości, wydajności i ogólnego sukcesu formowanych produktów. Ta faza ma bezpośredni wpływ na różne aspekty produktu końcowego, w tym cykl formowania, modalność, dokładność wymiarową i właściwości mechaniczne.
Cykl formowania
Czas chłodzenia stanowi znaczną część cyklu formowania wtryskowego i stanowi około 50% do 80% całkowitego czasu cyklu. Efektywne chłodzenie ma kluczowe znaczenie dla skrócenia czasu cyklu formowania, a tym samym zwiększenia wydajności i wydajności produkcji. Dobrze zaprojektowany system chłodzenia może znacznie skrócić czas chłodzenia bez pogorszenia jakości formowanego produktu, co prowadzi do szybszego tempa produkcji i niższych kosztów produkcji.
Modalność
Modalność uformowanego produktu odnosi się do jego właściwości fizycznych i estetycznych, w tym wykończenia powierzchni, wypaczeń i obecności defektów, takich jak zapadnięcia lub linie spawów. Faza chłodzenia wpływa na te właściwości, wpływając na sposób krzepnięcia materiału w formie. Równomierne i kontrolowane chłodzenie może zapobiec defektom i zapewnić wysoką jakość wykończenia powierzchni. I odwrotnie, nierównomierne chłodzenie może prowadzić do wypaczeń i innych wad pogarszających wygląd i funkcjonalność produktu.
Dokładność wymiarowa
Dokładność wymiarowa ma kluczowe znaczenie dla wydajności i montażu części formowanych wtryskowo. Faza chłodzenia bezpośrednio wpływa na skurcz i wypaczenie materiału, co z kolei wpływa na dokładność wymiarową produktu końcowego. Właściwe chłodzenie zapewnia równomierny skurcz i minimalizuje wypaczenia, dzięki czemu części spełniają dokładne specyfikacje wymiarowe. Czynniki takie jak temperatura formy, konstrukcja kanału chłodzącego i czynnik chłodzący można zoptymalizować w celu osiągnięcia pożądanej dokładności wymiarowej.
Właściwości mechaniczne
Faza chłodzenia wpływa również na właściwości mechaniczne wyrobów formowanych wtryskowo, takie jak wytrzymałość, sztywność i odporność na uderzenia. Szybkie lub nierównomierne chłodzenie może wywołać naprężenia szczątkowe w materiale, potencjalnie zmniejszając wytrzymałość i zwiększając podatność na pękanie lub uszkodzenie pod obciążeniem. Kontrolowane chłodzenie może sprzyjać jednolitej krystalizacji polimerów półkrystalicznych i minimalizować naprężenia szczątkowe, poprawiając w ten sposób właściwości mechaniczne produktu końcowego.
Podsumowując, faza chłodzenia podczas formowania wtryskowego ma kluczowe znaczenie dla zapewnienia wydajności cyklu formowania, jakości i modalności formowanych produktów, ich dokładności wymiarowej oraz właściwości mechanicznych. Dobrze zaprojektowany system chłodzenia, dostosowany do specyficznych wymagań materiału i formowanej części, jest niezbędny do wytwarzania wysokiej jakości produktów formowanych wtryskowo, które spełniają lub przekraczają standardy wydajności i estetyki.