Le moulage par injection est un processus de fabrication qui crée des pièces en plastique en injectant un matériau fondu dans un moule. Un composant essentiel de ce processus est la carotte de coulée en plastique, qui est cruciale pour la création réussie de pièces en plastique. La carotte, souvent fabriquée à partir de polystyrène ou de chlorure de polyvinyle, sert de passage par lequel le matériau liquide pénètre dans le moule, se dirigeant vers les cavités des pièces où il se solidifie.
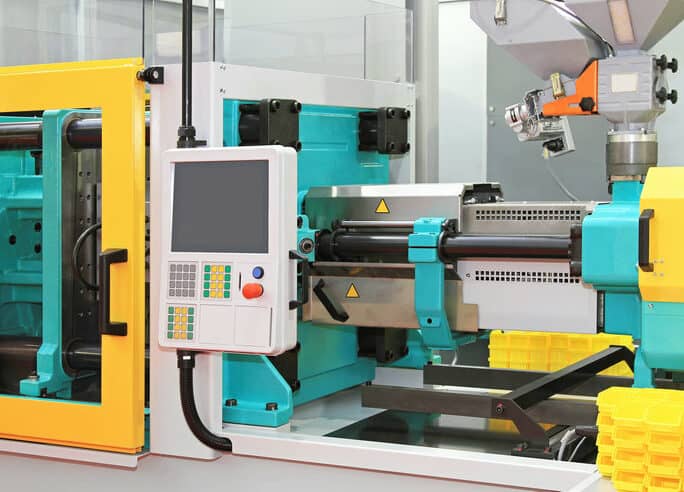
Comprendre la fonction de la carotte de coulée en plastique est essentiel pour une conception et une production efficaces de pièces moulées. La carotte est généralement connectée à un réseau de canaux et de portes qui dirigent et gèrent le flux de matière fondue dans les cavités du moule. Placer la carotte dans la section la plus épaisse de la pièce peut fournir un remplissage optimal de la cavité, réduisant ainsi le risque de défauts tels que des vides, des marques d'enfoncement et des déformations.
Points clés à retenir
- Les carottes de plastique sont essentielles pour diriger le matériau fondu dans le moule lors du processus de moulage par injection.
- La carotte se connecte aux canaux et aux portes pour gérer le flux de matériaux et optimiser la qualité des pièces.
- Le positionnement de la carotte dans la partie la plus épaisse du produit moulé minimise les défauts et améliore l'efficacité.
Comprendre Sprue et son rôle
Dans le moulage par injection, la carotte est cruciale pour diriger le plastique fondu dans la chambre du moule. C'est un passage qui relie la buse de la machine d'injection à la cavité du moule. La carotte garantit que le plastique fondu s'écoule de manière efficace et efficiente, minimisant les défauts et produisant un produit final cohérent.
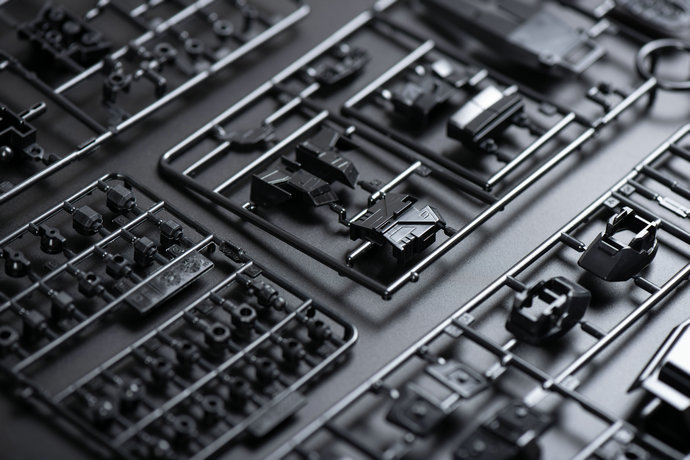
La grappe fonctionne avec d'autres composants, tels que le canal d'alimentation et les portes. Le canal est un système de distribution qui dirige le plastique fondu de la carotte vers chaque cavité du moule. Cela garantit qu’un flux constant et contrôlé de plastique atteint chaque pièce, facilitant ainsi un remplissage et une formation appropriés.
Lors de la détermination du diamètre de la carotte, il est essentiel de prendre en compte la taille et l'épaisseur de la pièce moulée. Le diamètre doit être suffisamment grand pour accueillir le flux de plastique fondu, mais pas au point de créer une pression excessive et de provoquer des défauts. Il est généralement conçu pour être effilé, devenant progressivement plus étroit vers l'extrémité pour aider à réduire la quantité de matériau utilisé et assurer un écoulement plus fluide.
La douille d'injection est un autre élément essentiel lors de l'utilisation d'une carotte. Il est conçu pour sécuriser la carotte et maintenir un bon alignement avec le moule. Il est généralement fixé avec deux boulons pour empêcher la dissociation provoquée par des pressions d'injection élevées. En outre, la douille d'injection contribue à garantir une injection précise et cohérente du plastique fondu dans le moule.
Processus de moulage par injection et carottes
Lors du moulage par injection pour créer des pièces en plastique, le plastique fondu s'écoule à travers une carotte, un canal ou un passage reliant l'unité d'injection à la cavité du moule. Il sert de principal point d’entrée pour que le matériau fondu s’écoule dans les cavités du moule.
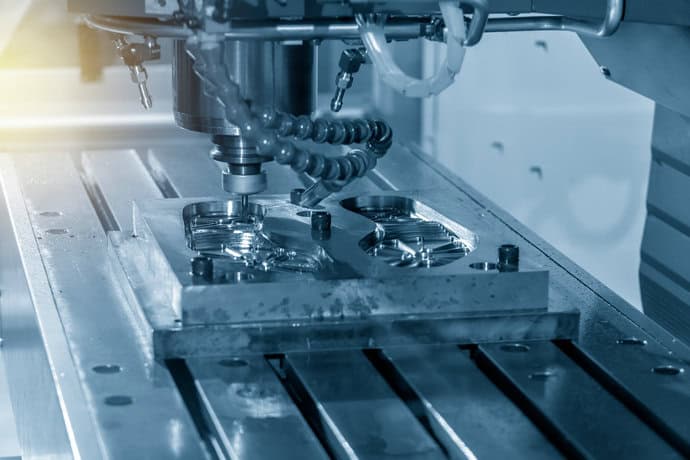
Pendant le processus, l’unité d’injection chauffe la matière plastique jusqu’à ce qu’elle atteigne un état fondu. Il force ensuite ce matériau à travers la carotte, guidant le flux dans les cavités du moule. À mesure que le matériau refroidit et se solidifie, il prend la forme de la pièce spécifiée par la conception de votre moule.
En optimisant la conception et l'emplacement des carottes, vous pouvez réduire le temps de cycle, minimiser le gaspillage de matériaux et prévenir les défauts de pièces tels que les déformations ou les marques d'affaissement qui peuvent survenir lorsque le matériau ne remplit pas uniformément les cavités.
Lors de la conception de la carotte de coulée et de la cavité du moule, gardez à l'esprit les considérations suivantes :
- Emplacement des carottes: Positionner la carotte au niveau de la section la plus épaisse de la pièce pour remplir efficacement la cavité et éviter les vides ou les défauts.
- Diamètre de carotte: Assurez-vous que la carotte est suffisamment grande pour permettre un débit adéquat, mais pas au point de provoquer des chutes de pression excessives ou des problèmes de retrait.
- Longueur des carottes: Ajustez la longueur de la carotte pour équilibrer la pression d'injection et minimiser le risque de gel du matériau ou de tirs courts.
En abordant ces facteurs, vous pouvez réussir à intégrer la carotte dans votre processus de moulage par injection et obtenir des pièces en plastique de haute qualité. N'oubliez pas que la fonction principale de la carotte est de faciliter l'écoulement fluide et efficace du plastique fondu de l'unité d'injection vers la cavité de votre moule. Portez donc une attention particulière à la conception et aux dimensions de la carotte pour garantir le succès de vos efforts de moulage par injection.
Conception et formation de carottes en plastique
Dans cette section, vous découvrirez la conception et la formation de carottes de plastique dans le moulage par injection.
Premièrement, il est essentiel de garantir la bonne conception de la carotte pour optimiser le flux de matière plastique fondue. La carotte a besoin d'une dépouille, ou d'un léger angle, pour faciliter son démoulage après solidification.
Plus le tirage est large, plus il est facile de retirer la carotte du moule. Le tirage contribue également à réduire la résistance pendant la phase de remplissage, ce qui permet un écoulement plus fluide du plastique fondu.
En entrant dans le moule, le plastique fondu s'écoule de la carotte vers les cavités individuelles via le système de canaux. Ce système de distribution nécessite une conception soignée, car il affecte la qualité et la cohérence des pièces moulées finales.
Différents types de portes peuvent être utilisés pour obtenir la distribution de matériaux souhaitée, telles que des portes de bord, des portes en éventail ou des portes de tunnel. Chaque type de portail varie en taille et en forme, il est donc crucial de choisir le portail approprié pour votre application spécifique.
Les portes de bord, par exemple, sont fines et étroites, garantissant une séparation nette et homogène entre la pièce moulée et la carotte. D’un autre côté, les vannes de ventilateur ont une ouverture plus large, permettant un flux plus uniforme de matière plastique fondue.
Cela se traduit par un remplissage plus uniforme des cavités du moule, réduisant ainsi les risques de retrait ou de déformation du matériau. Les portes de tunnel sont généralement utilisées lors du moulage de pièces plus complexes ou délicates, car elles permettent un contrôle précis du flux de matière plastique en fusion.
La solidification du matériau plastique à l’intérieur de la carotte doit également être prise en compte lors du processus de conception. Des canaux de refroidissement appropriés doivent être incorporés dans le moule, garantissant que le matériau refroidit correctement. Cela permet de prévenir les défauts et d’améliorer la qualité globale de la pièce finale.
Systèmes de coulées d'injection
Dans le moulage par injection, le système de coulée d'injection est crucial pour répartir la matière plastique fondue dans tout le moule, pour finalement atteindre chaque cavité.
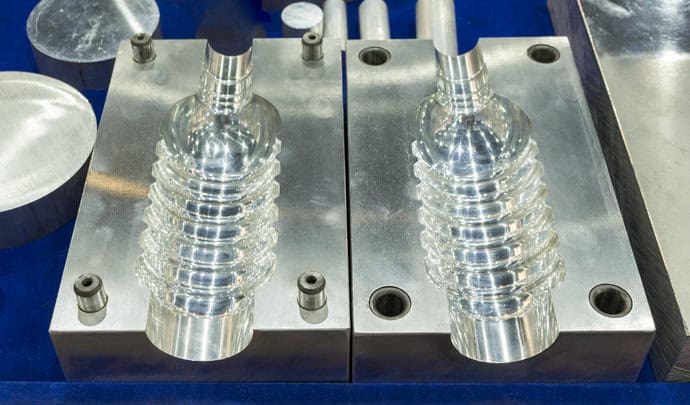
Lorsque le plastique fondu pénètre dans le moule par le sprue, il se jette dans le coureurs. Les coureurs sont des canaux qui transportent le matériau vers le portes. Ces portes agissent comme des ouvertures qui permettent au plastique de pénétrer dans chaque cavité de manière contrôlée. Les portes et les glissières contribuent à un flux fluide et équilibré pour une qualité de produit constante.
Il existe différents types de portes et de glissières dans un système de cheminées d'injection. Par exemple, un sous-coureur peut bifurquer du canal principal, offrant un contrôle plus précis de la répartition des matériaux dans les moules multi-empreintes.
L'utilisation de sous-canaux facilite le réglage précis du processus de remplissage, réduisant ainsi le temps de cycle et améliorant l'efficacité globale du moulage.
Lors de la conception d'un système de cheminées d'injection, il est essentiel de prendre en compte un flux équilibré. Cela signifie que le matériau fondu doit atteindre chaque cavité du moule simultanément, avec une pression et un volume égaux, ce qui entraîne un remplissage constant et un refroidissement uniforme de toutes les pièces du moule.
Voici quelques facteurs clés à prendre en compte dans les systèmes de coulées d'injection :
- Dimensions des canaux : le diamètre, la longueur et la forme des canaux doivent être soigneusement conçus pour maintenir un débit équilibré et minimiser les chutes de pression.
- Type et taille de vanne : choisissez la vanne adaptée à votre application, en tenant compte de facteurs tels que la conception des pièces, les matériaux et les caractéristiques d'écoulement souhaitées. Assurez-vous que la taille de la porte est adaptée pour maintenir un flux de matériaux constant.
- Débit équilibré : optimisez la conception de la carotte d'injection et du canal d'injection pour obtenir un débit équilibré dans toutes les cavités, garantissant ainsi un remplissage et un refroidissement uniformes.
N’oubliez pas qu’un système de carottes d’injection efficace est essentiel au succès du moulage par injection. En considérant attentivement chacun de ces facteurs, vous pouvez concevoir un système qui offre l’équilibre souhaité du flux de matières et améliore l’efficacité et la qualité de vos pièces moulées.
Défis et solutions dans la conception Sprue
Concevoir correctement les carottes est essentiel pour obtenir des produits de qualité et un processus efficace. Cette section abordera certains défis courants liés à la conception de grappes et les solutions potentielles.
L’un des principaux défis que vous pouvez rencontrer lors de la conception d’une carotte d’injection est la chute de pression. Lorsque le plastique s'écoule à travers la carotte, sa vitesse doit être gérée pour minimiser la perte de pression et garantir un débit optimal.
Une solution à ce défi consiste à sélectionner la bonne taille et la bonne forme de carotte qui permettent un débit optimal et réduisent la résistance.
Un autre problème qui peut survenir est un volume insuffisant dans la carotte, entraînant une mauvaise éjection et la formation de vides dans les pièces finies. Pour résoudre ce problème, il faut calculer soigneusement le volume de matériau requis et ajuster la conception de la carotte pour l'adapter. De plus, l’utilisation d’un système d’éjection approprié empêchera la déformation de la pièce et garantira un refroidissement uniforme dans toute la pièce.
La régulation du flux de matière dans la carotte peut également contribuer à éviter les traces d'enfoncement et les déformations dans les pièces injectées.
Pour y parvenir, vous devrez peut-être ajuster le débit en optimisant le diamètre de la carotte, la taille du canal et l'emplacement de la porte.
En ce qui concerne les déchets de matériaux et la durabilité, la conception des carottes joue un rôle important. L'optimisation de la conception peut réduire la quantité de matériau à rebroyer, ce qui permet d'économiser des ressources et d'améliorer l'efficacité. La mise en œuvre d'un système de canaux froids pour les matériaux facilement rebroyables peut également réduire les déchets.
En résolvant ces problèmes grâce à des ajustements et une optimisation appropriés de la conception, vous pouvez garantir la production de pièces en plastique de haute qualité et améliorer l’efficacité globale de votre processus de moulage par injection.
Questions fréquemment posées
1. Quels sont les types de glissières dans le moulage par injection ?
Il existe deux principaux types de canaux dans le moulage par injection : les canaux froids et chauds. Les canaux froids sont de simples canaux à l'intérieur du moule qui dirigent le plastique fondu de la carotte vers la cavité du moule. Ils peuvent être fabriqués à partir du même matériau que le moule et, par conséquent, refroidir à mesure que le plastique se solidifie, facilitant ainsi le démoulage de la pièce.
D'un autre côté, les canaux chauds sont des systèmes plus complexes conçus pour maintenir le plastique fondu à la température souhaitée lors de son déplacement de la carotte à la cavité du moule. Ils comprennent généralement des éléments chauffants ou des éléments chauffants qui maintiennent une température constante, réduisant ainsi le gaspillage de matériaux et améliorant l'efficacité globale du processus.
2. En quoi la carotte diffère-t-elle du canal dans le processus de moulage ?
Bien que la carotte et le canal soient des canaux qui transportent le plastique fondu dans le processus de moulage par injection, ils remplissent des fonctions différentes. La carotte est le passage vertical initial reliant la buse de la machine de moulage par injection à la cavité du moule.
En revanche, le canal est un canal qui distribue le plastique vers plusieurs cavités ou différentes parties du moule. La carotte sert de point d'entrée pour le plastique fondu, tandis que le rôle principal du canal est de répartir le matériau uniformément dans le moule.
3. Quel rôle Sprue joue-t-il dans le casting ?
En moulage, la carotte joue un rôle similaire à sa fonction en moulage par injection. C'est le passage vertical par lequel un matériau liquide, tel que du métal en fusion ou du plastique, est introduit dans le moule. La carotte crée un chemin d'écoulement pour que le matériau pénètre dans la cavité du moule, garantissant que le moule se remplit uniformément et que la pièce finale est exempte de défauts et de bulles d'air. Cela élimine les excès de matériaux et les déchets.
Dans de nombreux processus de coulée, la carotte aide également à contrôler le flux de matière fondue à travers la buse de la machine d'injection, ce qui en fait un élément essentiel dans la création de pièces coulées de haute qualité.
4. Quelle est la signification de la forme de la carotte ?
La forme de la carotte a un impact significatif sur l'efficacité et la qualité du processus de moulage par injection. Une carotte de fusion bien conçue doit minimiser le gaspillage de matériaux, faciliter l'écoulement fluide du plastique fondu et réduire le risque de défauts, tels que les vides, les marques d'évier et la déformation dans la pièce finale. En règle générale, il est préférable de placer la carotte au niveau de la section la plus épaisse de la pièce, ce qui permet un remplissage efficace de la cavité. Une forme effilée ou conique peut aider à minimiser les chutes de pression lorsque le matériau s'écoule à travers la carotte, garantissant ainsi un processus d'injection plus fluide et plus contrôlé.
5. Comment fonctionne une douille de coulée de moule ?
Une douille de coulée de moule est un composant essentiel dans le processus de moulage par injection, reliant la buse de la machine d'injection au système de canaux du moule. Il forme l'interface entre la buse de la machine d'injection et la carotte, permettant une étanchéité parfaite et évitant les fuites ou les pertes de matière.
La douille d'injection garantit que la matière plastique fondue est transférée efficacement et précisément du tuyau de la machine d'injection vers la carotte du moule, réduisant ainsi les déchets et garantissant que le matériau atteint la cavité du moule dans les conditions souhaitées pour une production optimale de pièces.
Commandez des pièces en plastique en gros
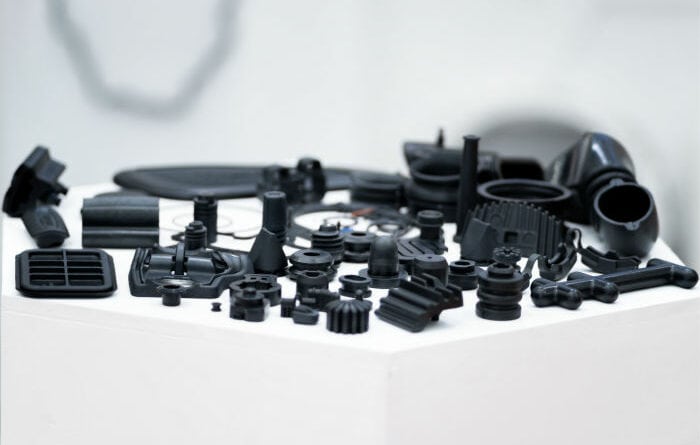
Vous n'avez aucun souci concernant la qualité des carottes en plastique lorsque vous faites affaire avec nous. Vous pouvez commander chez nous des pièces moulées par injection plastique de haute qualité. Quelle que soit votre localisation, nous livrons rapidement, selon notre accord.
Veuillez nous envoyer un message via le formulaire de contact client sur le site pour commander dès aujourd'hui.