El moldeo por inyección es un proceso de fabricación que crea piezas de plástico inyectando material fundido en un molde. Un componente esencial de este proceso es el bebedero de plástico, que es crucial para la creación exitosa de piezas de plástico. El bebedero, a menudo hecho de poliestireno o cloruro de polivinilo, sirve como un pasaje a través del cual el material líquido ingresa al molde, navegando hasta las cavidades de la pieza donde se solidifica.
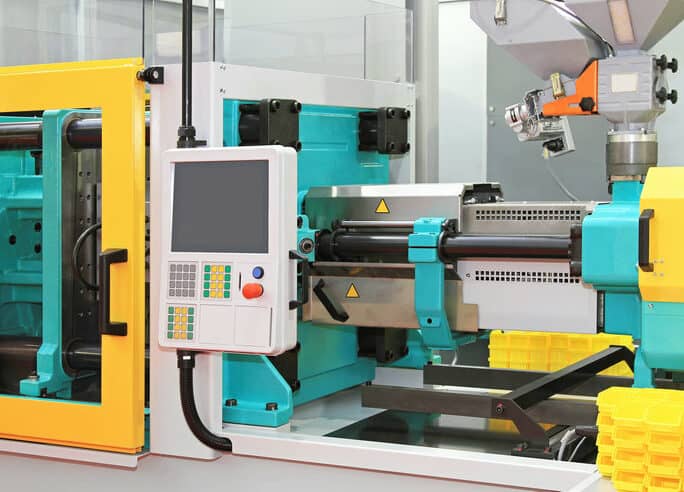
Comprender la función del bebedero de plástico es esencial para el diseño y la producción eficientes de piezas moldeadas. El bebedero suele estar conectado a una red de canales y compuertas que dirigen y gestionan el flujo de material fundido hacia las cavidades del molde. Colocar el bebedero en la sección más gruesa de la pieza puede proporcionar un llenado óptimo de la cavidad, reduciendo el riesgo de defectos como huecos, marcas de hundimiento y deformaciones.
Conclusiones clave
- El bebedero de plástico es esencial para dirigir el material fundido al molde en el proceso de moldeo por inyección.
- El bebedero se conecta a canales y compuertas para gestionar el flujo de material y optimizar la calidad de las piezas.
- Colocar el bebedero en la parte más gruesa del producto moldeado minimiza los defectos y mejora la eficiencia.
Comprensión del Sprue y su papel
En el moldeo por inyección, el bebedero es crucial para dirigir el plástico fundido hacia la cámara del molde. Es un pasaje que conecta la boquilla de la máquina de inyección con la cavidad del molde. El bebedero garantiza que el plástico fundido fluya de manera eficiente y efectiva, minimizando los defectos y produciendo un producto final consistente.
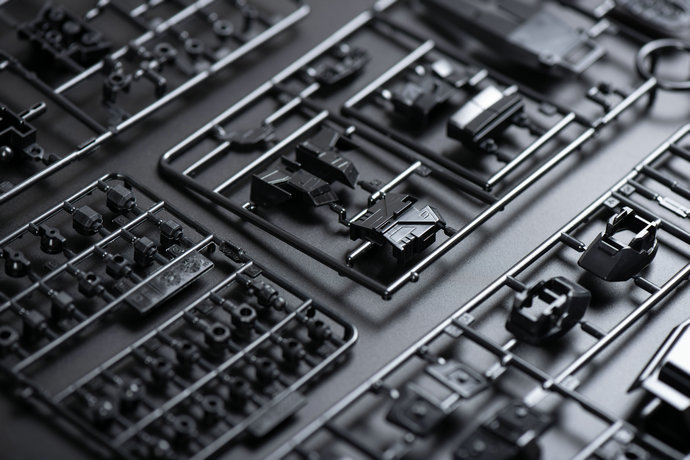
El bebedero trabaja con otros componentes, como el corredor y las puertas. El canal es un sistema de distribución que dirige el plástico fundido desde el bebedero a cada cavidad dentro del molde. Esto garantiza que un flujo constante y controlado de plástico llegue a cada pieza, facilitando el llenado y la formación adecuados.
A la hora de determinar el diámetro del bebedero, es fundamental tener en cuenta el tamaño y el espesor de la pieza moldeada. El diámetro debe ser lo suficientemente grande como para acomodar el flujo de plástico fundido, pero no tan grande como para crear una presión excesiva y causar defectos. Por lo general, está diseñado para ser cónico y volverse gradualmente más estrecho hacia el final para ayudar a reducir la cantidad de material utilizado y proporcionar un flujo más suave.
El casquillo del bebedero es otro componente crítico cuando se utiliza un bebedero. Está diseñado para asegurar el bebedero y mantener una alineación adecuada con el molde. Normalmente se fija con dos pernos para evitar la disociación provocada por altas presiones de inyección. Además, el casquillo del bebedero ayuda a garantizar una inyección precisa y consistente de plástico fundido en el molde.
Proceso de moldeo por inyección y bebedero
Durante el moldeo por inyección para crear piezas de plástico, el plástico fundido fluye a través de un bebedero, un canal o pasaje que conecta la unidad de inyección con la cavidad del molde. Sirve como punto de entrada principal para que el material fundido fluya hacia las cavidades dentro del molde.
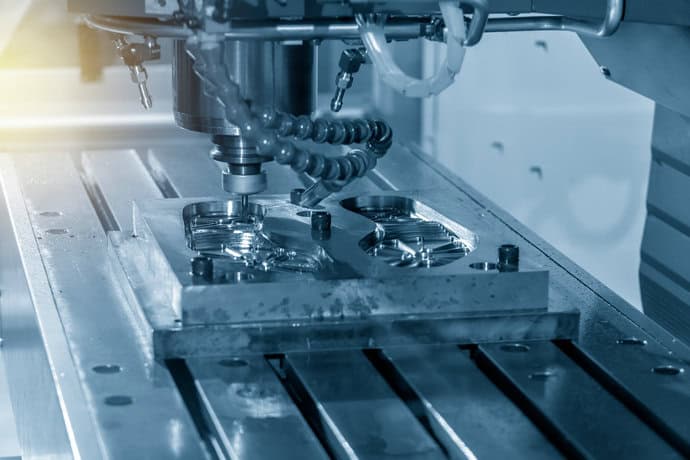
Durante el proceso, la unidad de inyección calienta el material plástico hasta alcanzar el estado fundido. Luego fuerza este material a través del bebedero, guiando el flujo hacia las cavidades del molde. A medida que el material se enfría y solidifica, adopta la forma de la pieza especificada por el diseño del molde.
Al optimizar el diseño y la ubicación del bebedero, puede reducir el tiempo del ciclo, minimizar el desperdicio de material y evitar defectos en las piezas, como deformaciones o marcas de hundimiento, que pueden ocurrir cuando el material no llena las cavidades de manera uniforme.
Al diseñar el bebedero y la cavidad del molde, tenga en cuenta las siguientes consideraciones:
- Ubicación del bebedero: Coloque el bebedero en la sección más gruesa de la pieza para llenar eficazmente la cavidad y evitar huecos o defectos.
- Diámetro del bebedero: Asegúrese de que el bebedero sea lo suficientemente grande como para permitir un flujo adecuado, pero no tan grande como para provocar caídas de presión excesivas o problemas de contracción.
- Longitud del bebedero: Ajuste la longitud del bebedero para equilibrar la presión de inyección y minimizar el riesgo de congelamiento del material o disparos cortos.
Al abordar estos factores, puede incorporar con éxito el bebedero en su proceso de moldeo por inyección y lograr piezas de plástico de alta calidad. Recuerde, la función principal del bebedero es facilitar el flujo suave y eficiente del plástico fundido desde la unidad de inyección hacia la cavidad del molde. Por lo tanto, preste mucha atención al diseño y las dimensiones del bebedero para garantizar el éxito en sus esfuerzos de moldeo por inyección.
Diseño y formación de bebederos de plástico.
En esta sección, aprenderá sobre el diseño y la formación de bebederos de plástico en moldeo por inyección.
En primer lugar, es fundamental garantizar el diseño adecuado del bebedero para optimizar el flujo de material plástico fundido. El bebedero necesita una inclinación, o un ligero ángulo, para facilitar su desmolde después de la solidificación.
Cuanto más amplio sea el tiro, más fácil será sacar el bebedero del molde. La corriente de aire también ayuda a reducir la resistencia durante la fase de llenado, lo que resulta en un flujo más suave de plástico fundido.
Al entrar en el molde, el plástico fundido fluye desde el bebedero a las cavidades individuales a través del sistema de canales. Este sistema de distribución requiere un diseño cuidadoso, ya que afecta la calidad y consistencia de las piezas moldeadas finales.
Se pueden utilizar diferentes tipos de compuertas para lograr la distribución de material deseada, como compuertas de borde, compuertas de abanico o compuertas de túnel. Cada tipo de puerta varía en tamaño y forma, por lo que es fundamental elegir la puerta adecuada para su aplicación específica.
Las puertas de borde, por ejemplo, son delgadas y estrechas, lo que garantiza una separación limpia y perfecta entre la pieza moldeada y el bebedero. Por otro lado, las compuertas del ventilador tienen una apertura más amplia, lo que permite un flujo más uniforme de material plástico fundido.
Esto da como resultado un llenado más uniforme de las cavidades del molde, lo que reduce las posibilidades de que el material se contraiga o deforme. Las compuertas de túnel se utilizan normalmente para moldear piezas más complejas o delicadas, ya que permiten un control preciso sobre el flujo de material plástico fundido.
Durante el proceso de diseño también se debe considerar la solidificación del material plástico dentro del bebedero. Se deben incorporar canales de enfriamiento adecuados al molde, asegurando que el material se enfríe adecuadamente. Esto ayuda a prevenir defectos y mejorar la calidad general de la pieza final.
Sistemas de canal de bebedero
En el moldeo por inyección, el sistema de canal de bebedero Es crucial para distribuir el material plástico fundido por todo el molde, llegando finalmente a cada cavidad.
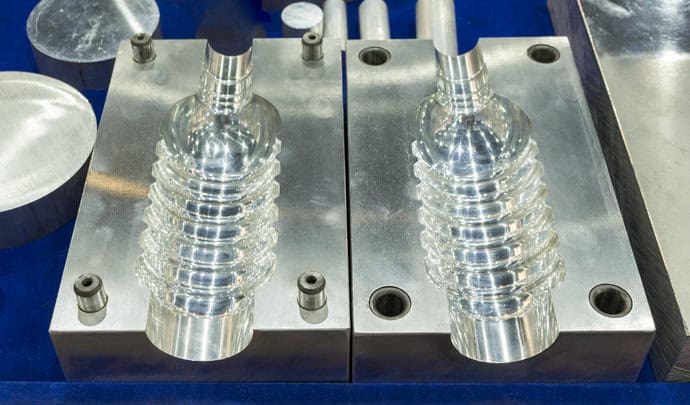
A medida que el plástico fundido ingresa al molde a través del bebedero, desemboca en el corredores. Los corredores son canales que transportan el material al puertas. Estas compuertas actúan como aberturas que permiten que el plástico ingrese a cada cavidad de manera controlada. Las compuertas y corredores contribuyen a un flujo suave y equilibrado para una calidad constante del producto.
Hay diferentes tipos de compuertas y corredores en un sistema de canales de bebedero. Por ejemplo, un subcorredor Puede desviarse del canal principal, proporcionando un control más preciso sobre la distribución del material en moldes de múltiples cavidades.
El uso de subcorredores facilita el ajuste del proceso de llenado, lo que reduce el tiempo del ciclo y mejora la eficiencia general del moldeo.
Al diseñar un sistema de canal de bebedero, es esencial considerar una flujo equilibrado. Esto significa que el material fundido debe llegar a cada cavidad del molde simultáneamente, con igual presión y volumen, lo que da como resultado un llenado constante y un enfriamiento uniforme de todas las piezas dentro del molde.
A continuación se detallan algunos factores clave a considerar en los sistemas de canales de bebedero:
- Dimensiones de los canales: El diámetro, la longitud y la forma de los canales deben diseñarse cuidadosamente para mantener un flujo equilibrado y minimizar las caídas de presión.
- Tipo y tamaño de compuerta: elija la compuerta adecuada para su aplicación, considerando factores como el diseño de la pieza, el material y las características de flujo deseadas. Asegúrese de que el tamaño de la compuerta sea adecuado para mantener un flujo de material constante.
- Flujo equilibrado: optimice el diseño del bebedero y del canal para lograr un flujo equilibrado en todas las cavidades, garantizando un llenado y enfriamiento uniformes.
Recuerde, un sistema de canal de bebedero eficiente es vital para un moldeo por inyección exitoso. Al considerar cuidadosamente cada uno de estos factores, puede diseñar un sistema que ofrezca el equilibrio deseado de flujo de material y mejore la eficiencia y la calidad de sus piezas moldeadas.
Desafíos y soluciones en el diseño de bebederos
Diseñar correctamente los bebederos es fundamental para conseguir productos de calidad y un proceso eficiente. Esta sección discutirá algunos desafíos comunes en el diseño de bebederos y posibles soluciones.
Uno de los principales desafíos que puede encontrar en el diseño de bebederos es la caída de presión. A medida que el plástico fluye a través del bebedero, se debe gestionar su velocidad para minimizar la pérdida de presión y garantizar un caudal óptimo.
Una solución a este desafío es seleccionar el tamaño y la forma del bebedero adecuados que permitan un flujo óptimo y reduzcan la resistencia.
Otro problema que puede surgir es un volumen insuficiente en el bebedero, lo que provoca una mala expulsión y la formación de huecos en las piezas acabadas. Para abordar este problema es necesario calcular cuidadosamente el volumen de material requerido y ajustar el diseño del bebedero para acomodarlo. Además, el uso de un sistema de expulsión adecuado evitará la deformación de la pieza y garantizará un enfriamiento uniforme en toda la pieza.
Regular el flujo de material en el bebedero también puede ayudar a evitar marcas de hundimiento y deformaciones en las piezas inyectadas.
Es posible que necesite ajustar el caudal optimizando el diámetro del bebedero, el tamaño del canal y la ubicación de la compuerta para lograrlo.
En lo que respecta al desperdicio de material y la sostenibilidad, el diseño del bebedero juega un papel importante. La optimización del diseño puede reducir la cantidad de material que es necesario rectificar, lo que ahorra recursos y mejora la eficiencia. La implementación de un sistema de canal frío para materiales fácilmente triturables también puede reducir el desperdicio.
Al abordar estos problemas con ajustes y optimización de diseño adecuados, puede garantizar la producción de piezas de plástico de alta calidad y mejorar la eficiencia general de su proceso de moldeo por inyección.
Preguntas frecuentes
1. ¿Cuáles son los tipos de corredores en el moldeo por inyección?
Hay dos tipos principales de canales en el moldeo por inyección: canales fríos y calientes. Los canales fríos son canales simples dentro del molde que dirigen el plástico fundido desde el bebedero hasta la cavidad del molde. Pueden ser del mismo material que el molde y, por tanto, enfriarse a medida que el plástico se solidifica, facilitando el desmolde de la pieza.
Por otro lado, los canales calientes son sistemas más complejos diseñados para mantener el plástico fundido a la temperatura deseada mientras viaja desde el bebedero hasta la cavidad del molde. Por lo general, incluyen calentadores o elementos calefactores que mantienen una temperatura constante, lo que reduce el desperdicio de material y mejora la eficiencia general del proceso.
2. ¿En qué se diferencia el bebedero del canal en el proceso de moldeo?
Si bien tanto el bebedero como el canal son canales que transportan plástico fundido en el proceso de moldeo por inyección, cumplen funciones diferentes. El bebedero es el pasaje vertical inicial que conecta la boquilla de la máquina de moldeo por inyección con la cavidad del molde.
En cambio, el canal es un canal que distribuye el plástico a múltiples cavidades o diferentes partes del molde. El bebedero sirve como punto de entrada para el plástico fundido, mientras que la función principal del canal es distribuir el material uniformemente por todo el molde.
3. ¿Qué papel juega Sprue en el casting?
En la fundición, el bebedero desempeña un papel similar a su función en el moldeo por inyección. Es el paso vertical por el que se introduce en el molde material líquido, como metal fundido o plástico. El bebedero crea una ruta de flujo para que el material ingrese a la cavidad del molde, asegurando que el molde se llene uniformemente y que la pieza final esté libre de defectos y burbujas de aire. Esto elimina el exceso de material y los residuos.
En muchos procesos de fundición, el bebedero también ayuda a controlar el flujo de material fundido a través de la boquilla de la máquina de inyección, lo que lo convierte en un componente fundamental en la creación de piezas fundidas de alta calidad.
4. ¿Cuál es el significado de la forma del bebedero?
La forma del bebedero afecta significativamente la eficiencia y la calidad del proceso de moldeo por inyección. Un bebedero bien diseñado debe minimizar el desperdicio de material, facilitar el flujo suave del plástico fundido y reducir el riesgo de defectos, como huecos, marcas de hundimiento y deformaciones en la pieza final. Normalmente, lo mejor sería colocar el bebedero en la sección más gruesa de la pieza, lo que permitirá un llenado eficiente de la cavidad. Una forma cónica o cónica puede ayudar a minimizar las caídas de presión a medida que el material fluye a través del bebedero, lo que garantiza un proceso de inyección más suave y controlado.
5. ¿Cómo funciona un casquillo de bebedero de molde?
Un casquillo de bebedero de molde es un componente crítico en el proceso de moldeo por inyección, ya que conecta la boquilla de la máquina de inyección al sistema de canales del molde. Forma la interfaz entre la boquilla de la máquina de inyección y el bebedero, lo que permite un sellado hermético y evita fugas o pérdidas de material.
El casquillo del bebedero garantiza que el material plástico fundido se transfiera de manera eficiente y precisa desde la manguera de la máquina de inyección al bebedero del molde, lo que reduce el desperdicio y garantiza que el material llegue a la cavidad del molde en las condiciones deseadas para una producción óptima de la pieza.
Solicite piezas de plástico al por mayor
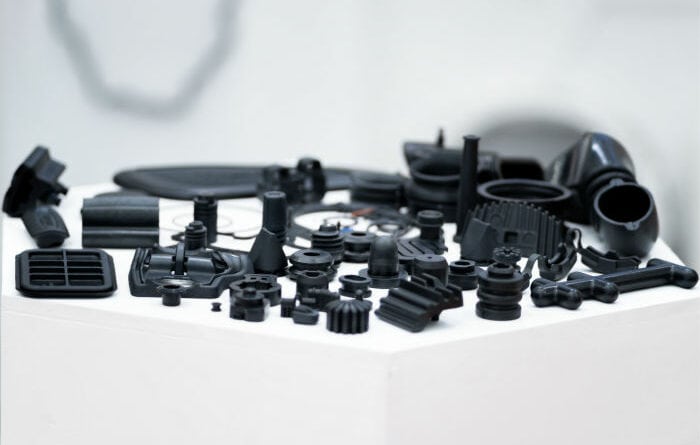
No tendrá que preocuparse por la calidad del bebedero de plástico cuando trate con nosotros. Puede solicitarnos piezas de moldeo por inyección de plástico de alta calidad. Independientemente de su ubicación, entregamos rápidamente, según nuestro acuerdo.
Envíenos un mensaje a través del formulario de contacto del cliente en el sitio para realizar su pedido hoy.