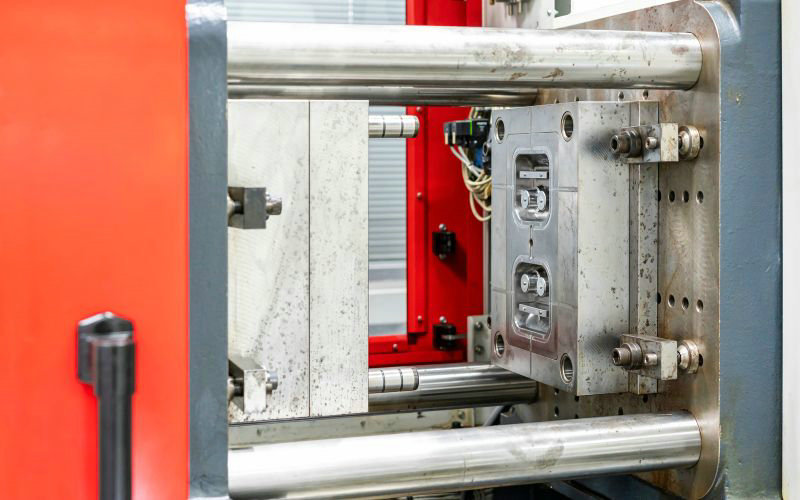
Clasificación de moldes de inyección
Si está evaluando moldes de inyección, es esencial comprender la sistema de clasificación que diferencia sus capacidades y aplicaciones. En este artículo, le proporcionaremos una guía sencilla para comprender varios tipos de moldes:
- Por Geometría
- Por Número de cavidades
- Por Placa de molde
- Por Principio de eyección
- Por Material de plastico
- Por Sistema de alimentación
Su elección entre estos tipos de moldes de inyección a menudo equilibra la escala de su proyecto, la complejidad de las piezas y las implicaciones de los costos operativos. ¡Exploremos juntos varios tipos de moldes de inyección de plástico!
Por geometría
- Geometrías simples:
- Más fácil de diseñar y fabricar.
- Suelen tener menos secciones huecas.
- Geometrías complejas:
- Permitir una mayor flexibilidad de diseño.
- Puede acomodar secciones huecas necesarias para funciones específicas.
Las piezas complejas suelen incluir características como socavaduras, que son muescas o proyecciones que pueden complicar el diseño del molde. El diseño de socavados requiere una consideración cuidadosa para garantizar que los componentes del molde puedan separarse adecuadamente durante la fase de expulsión sin dañar la pieza.
Para diseños de componentes complejos, puede ser necesario utilizar tecnologías de moldes avanzadas, como controles deslizantes o elevadores, para crear y liberar la pieza del molde con éxito. Si bien este enfoque ofrece una alta flexibilidad de diseño, también aumenta la complejidad y el costo del molde.
La elección entre una geometría de molde simple o compleja dependerá en última instancia del diseño de la pieza deseada, la funcionalidad, la viabilidad del proceso de fabricación del molde y el presupuesto del proyecto. Equilibre siempre la necesidad de geometrías complejas con consideraciones prácticas de producción.
Por número de cavidades
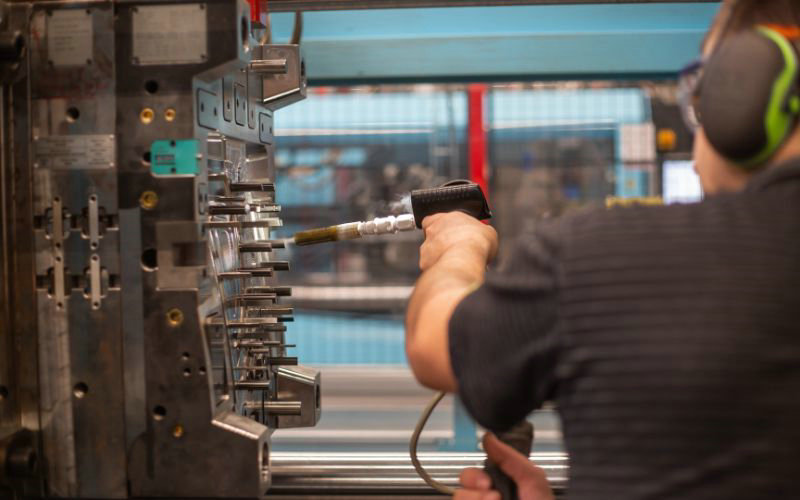
Moldes de una sola cavidad
- Produzca solo un producto por ciclo de inyección.
- Ideal para piezas grandes, complejas o de bajo volumen
- Permitir más atención a las piezas individuales para minimizar los defectos.
- Costos de herramientas más bajos en comparación con los moldes de cavidades múltiples para la misma pieza
- Adecuado para crear prototipos y ofrecer nuevos diseños.
Moldes de cavidades múltiples
- Contiene múltiples cavidades idénticas para producir varias piezas por ciclo.
- Permita plazos de entrega más cortos y una mayor eficiencia de producción para grandes volúmenes
- Reduzca los costos por pieza para lotes grandes
- Requieren un diseño cuidadoso para garantizar un llenado uniforme y una calidad constante en todas las cavidades.
- Puede tener costos de herramientas iniciales más altos que los moldes de una sola cavidad.
- Los números de cavidades típicos varían de 2 a 64 o más, según el tamaño de la pieza y la aplicación.
Moldes familiares
- Incorpora múltiples cavidades con diferentes formas para producir varias piezas en un ciclo.
- Permitir el moldeado de componentes relacionados o variantes de productos en una sola toma
- Útil para crear prototipos o producir kits con piezas variadas
- Limitado a piezas que utilizan el mismo material y color.
- A menudo tienen un llenado desequilibrado debido a diferentes geometrías de las cavidades, lo que aumenta el riesgo de defectos.
- Requiere más mano de obra posterior al moldeado para separar y manipular diferentes piezas.
Por placa de molde
Molde de inyección de dos placas
- Diseño de molde de inyección más simple y común, que consta de dos partes principales (lado A y lado B)
- Tiene una única línea de separación donde el molde se divide en dos mitades.
- El lado de la cavidad es fijo, mientras que el lado del núcleo es móvil durante el proceso de moldeo.
- El canal y la pieza se encuentran en el mismo plano de separación y se expulsan juntos
- Ventajas: menor costo, tiempos de ciclo más cortos, más fácil de configurar y operar
- Desventajas: menos flexibilidad en la ubicación de la puerta, requiere delegación manual, riesgo de disparos cortos en moldes de múltiples cavidades
Molde de inyección de tres placas
- También conocido como molde de placa separadora, consta de dos planos de separación y se divide en tres secciones.
- Tiene una placa flotante adicional entre la cavidad y el núcleo para acomodar el sistema de guías.
- Permite la desgasificación automática del corredor de la pieza.
- Ofrece más flexibilidad en la ubicación de la puerta en comparación con los moldes de dos placas.
- Ventajas: adecuado para piezas grandes que requieren múltiples puertas, permite el debate automático
- Desventajas: más complejo y caro, tiempos de ciclo más largos, menos estable debido a más piezas móviles
Molde de inyección de pila
- Estructura de molde especial con múltiples superficies de separación, cada una con capacidad para una o más cavidades
- Consta de un molde móvil, un molde intermedio y un molde fijo que se abren simultáneamente
- Puede duplicar la producción de un molde estándar sin requerir máquinas adicionales
- Adecuado para la producción de grandes volúmenes de piezas planas de paredes delgadas
- Ventajas: productividad significativamente mayor, costos reducidos, tiempos de fabricación más cortos
- Desventajas: diseño más complejo, requiere un equilibrio cuidadoso entre el llenado y el enfriamiento de la cavidad
Por principio de eyección
1. Expulsión del pasador
- Utiliza pasadores eyectores para empujar la pieza moldeada fuera de la cavidad del molde.
- Los pasadores están ubicados en la mitad eyectora del molde y están diseñados para soportar fuerzas de expulsión.
- El diámetro, la longitud, el material, la ubicación y la forma del pasador son consideraciones de diseño críticas
- Adecuado para la mayoría de piezas moldeadas por inyección, pero puede dejar marcas visibles del pasador de expulsión.
2. Expulsión de la manga
- Emplea un eyector en forma de manga que rodea el núcleo para expulsar la pieza.
- Proporciona una fuerza de expulsión uniforme y estable sin dejar marcas visibles.
- Adecuado para productos cilíndricos, de paredes delgadas o con forma de concha
- Más complejo y costoso que la expulsión del pasador
3. Eyección de la placa extractora
- Utiliza una placa extractora para empujar la pieza fuera del núcleo.
- La fuerza de expulsión es alta, uniforme y estable, lo que minimiza la deformación de la pieza.
- Ideal para piezas cilíndricas, contenedores de paredes delgadas y productos con forma de concha
- Evita marcas visibles de expulsión pero tiene una estructura de molde más compleja y un costo mayor
4. Expulsión de la hoja
- Utiliza hojas eyectoras rectangulares en lugar de pasadores.
- Adecuado para piezas con geometrías o requisitos específicos
5. Expulsión de aire
- Introduce aire comprimido entre la pieza y el molde para expulsar la pieza.
- Simplifica la estructura del molde y permite la expulsión en cualquier ubicación.
- A menudo se utiliza para respaldar otros métodos de expulsión de piezas grandes, con cavidades profundas o de paredes delgadas.
6. Expulsión del elevador
- Emplea elevadores que se mueven lateralmente para liberar socavaduras o características internas.
- Permite la expulsión de piezas con geometrías complejas o acciones laterales.
Por material plástico
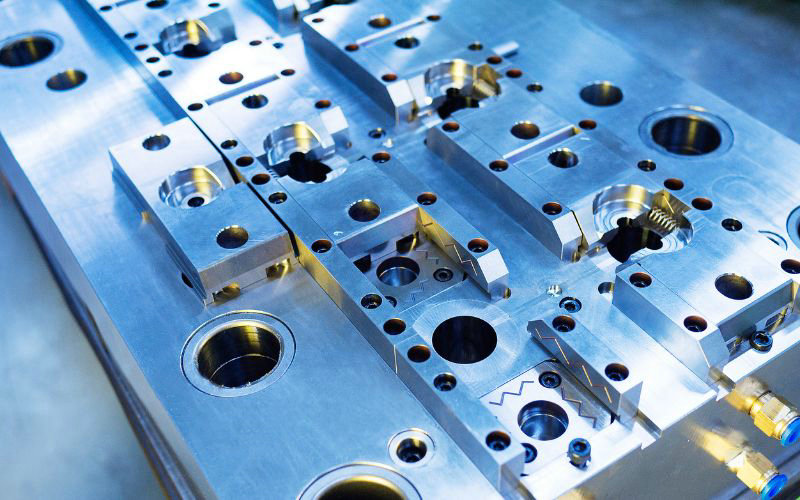
1. Acrílico (PMMA)
- Termoplástico fuerte y transparente con excelente claridad óptica y resistencia a los rayos UV.
- Alternativa al vidrio ligera y resistente a roturas.
- Se utiliza para lentes, pantallas, letreros y dispositivos médicos.
2. Acrilonitrilo butadieno estireno (ABS)
- Termoplástico resistente, rígido y resistente a los impactos.
- Buena resistencia química y fácil de pintar o pegar.
- Se utiliza para piezas de automóviles, electrodomésticos, juguetes y carcasas de productos electrónicos.
3. Nailon (Poliamida, PA)
- Termoplástico fuerte, flexible y resistente al desgaste.
- Alto punto de fusión y buena resistencia química.
- Se utiliza para piezas de automóviles, engranajes, rodamientos y componentes eléctricos.
4. Policarbonato (PC)
- Termoplástico resistente, transparente y resistente al calor.
- Buena estabilidad dimensional y propiedades de aislamiento eléctrico.
- Utilizado para componentes automotrices, dispositivos médicos y gafas de seguridad.
5. Polietileno (PE)
- Termoplástico ligero, flexible y resistente a productos químicos.
- Variantes de alta densidad (HDPE) y baja densidad (LDPE) disponibles
- Se utiliza para embalajes, contenedores, juguetes y componentes automotrices.
6. Polioximetileno (POM)
- Termoplástico fuerte, rígido y dimensionalmente estable.
- Excelente resistencia al desgaste y a los productos químicos.
- Utilizado para engranajes, rodamientos y piezas de precisión.
7. Polipropileno (PP)
- Termoplástico ligero, resistente y resistente a productos químicos.
- Buena resistencia a la fatiga y propiedades de aislamiento eléctrico.
- Se utiliza para embalaje, piezas de automóviles y artículos para el hogar.
8. Poliestireno (PS)
- Termoplástico rígido, transparente y de fácil procesamiento\
- Bajo costo y buena estabilidad dimensional.
- Se utiliza para embalajes, cubiertos desechables y juguetes.
9. Elastómeros termoplásticos (TPE) y poliuretanos (TPU)
- Termoplásticos flexibles similares al caucho con buena resistencia al impacto y a la abrasión
- Los TPU ofrecen mejor resistencia química y a la temperatura que los TPE
- Se utiliza para empuñaduras, juntas, sellos y calzado de tacto suave.
Por sistema de alimentación
Molde de inyección de canal frío
- Consta del bebedero, canales, subcanales, compuertas y pozos de babosas frías.
- Sprue entrega la masa fundida desde la boquilla al sistema de canales.
- Los corredores transportan la masa fundida desde el bebedero hasta las puertas.
- Las compuertas son pequeños orificios que conectan el corredor con la cavidad.
- Los pozos fríos almacenan el material frío inicial producido durante los intervalos de inyección.
- Se puede dividir aún más en sistemas de puerta lateral y puerta puntual.
- Adecuado para la mayoría de aplicaciones de moldeo por inyección
Molde de inyección de canal caliente
- No tiene corredor principal ni subcorredor.
- El material fundido pasa a través de una placa colectora y una boquilla caliente directamente a la cavidad a través de compuertas.
- Utiliza moldes de canal aislado o de canal caliente.
- Elimina la necesidad de un sistema tradicional de canal frío.
- Reduce el desperdicio de material y los tiempos de ciclo en comparación con los sistemas de canal frío.
Molde de inyección sin corredor
- El material fundido fluye directamente desde la boquilla hacia la cavidad sin un sistema de canal
- Diseño de sistema de alimentación más simple
Molde de inyección recomendado en Moldie
Moldie es un proveedor líder de servicios de moldeo y moldes de inyección de plástico de precisión y alta calidad. Con años de experiencia y tecnología de punta, Moldie ofrece una amplia gama de soluciones de moldes de inyección para satisfacer sus necesidades específicas:
Molde de inyección de productos de moldes de plástico de precisión
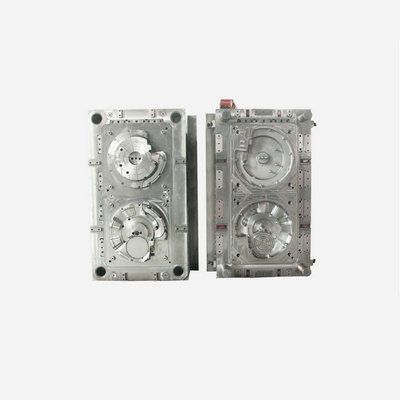
Descubra productos de moldeado de plástico de precisión que ofrecen opciones de materiales sólidas, experiencia en canales fríos/calientes y el brillo de los colores RAL PANTONE.
Piezas de plástico de alta precisión por encargo
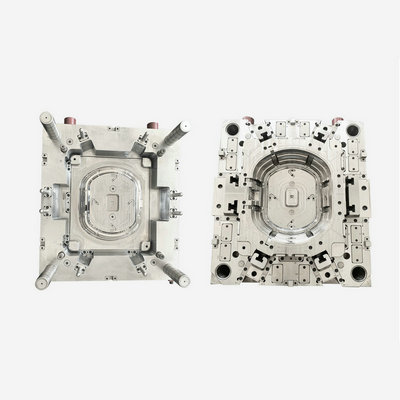
La complejidad de las operaciones primarias, secundarias y de acabado involucradas es la razón por la que solo debe contratar los servicios de expertos como los de nuestra empresa para manejar su proceso de producción.
Fabricante de moldeo de plástico personalizado
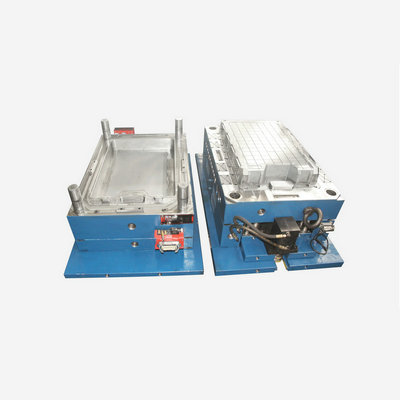
Con pesos de molde que van desde 50 kg hasta 15 toneladas y compatibilidad con máquinas de inyección de hasta 1500 toneladas, la adaptabilidad es el núcleo de lo que hacemos.
Elegir moho para sus necesidades de moldeo por inyección y experimente la diferencia que la precisión, la experiencia y el servicio centrado en el cliente pueden marcar. Contáctenos hoy para discutir su proyecto y aprender cómo podemos ayudarlo a hacer realidad su visión.