Die größte Menge an Kunststoffspritzguss, die während eines Formzyklus eingespritzt werden kann, ist als Schussgröße bekannt. Pellets werden durch den Trichter in die Zylinder- und Schneckenanordnung eingeführt.
Bei der Spritzgusstechnik wird geschmolzenes Material in den Hohlraum der Form gespritzt, um große Mengen an Kunststoffteilen herzustellen.
Beim Kunststoffspritzguss wird das Rohmaterial in den Zylinder eingebracht, schmilzt und der Kunststoff wird dann zum Abkühlen und Erstarren nach dem Schließen der Form in den Hohlraum der Form eingespritzt. Schließlich öffnet sich die Form und die Bauteile werden ausgestoßen.
So berechnen Sie die Schussgröße
Die Dauer der Verweilzeiten wird durch die Größe des Schusses und des Laufs beeinflusst, was sich auch auf die Qualität des Endprodukts auswirken kann. Lange Verweildauern und Polymerabbau können von kleinen Schussgrößen herrühren, die eine geringe Zylinderkapazität erfordern.
Kleine Schussgrößen, die weniger als 201 TP3T der Zylinderkapazität einnehmen, führen häufig zu verlängerten Verweilzeiten, die wiederum zu Polymerabbau und unzureichender Prozesskontrolle führen.
Andererseits können Big-Shot-Größen und Zylinderfüllgrade von mehr als 50% zu ungleichmäßigem Schmelzen und langsamer Schneckenerholung führen.
Außerdem haben größere Schnecken typischerweise eine geringere Kunststoffdruckfähigkeit. Große Schrotgrößen, die mehr als 651 TP3T der Zylinderkapazität beanspruchen, verursachen häufig Qualitätsprobleme der Schmelze, wie z.
Sicherheitshalber können Sie erwägen, eine Bestellung mit zwei Fässern aufzugeben. Darüber hinaus können Formen mit zwei Fässern verwendet werden. Wenn Sie mit der neuen Maschine ein zweites Fass bestellen, können Sie sich über den günstigen Preis freuen. Fässer können mit den richtigen Spezifikationen und einem erfahrenen Bediener in weniger als 30 Minuten gewechselt werden, selbst wenn das Fass heiß ist.
Formel für Formschussgröße beim Spritzgießen
Die einfachste Formel zur Berechnung der Formschussgröße lautet:
Schwindung + Fichtenvolumen + Produktvolumen + Angussvolumen = Formschussgröße
Formula Machine Schusskapazität / Schussgröße
Das Gesamtgewicht oder -volumen, das die Schnecke während eines Formzyklus einspritzt, wird als Maschinenschusskapazität (g)/Maschinenschussgröße (mm) ausgedrückt, auch bekannt als Maschineneinspritzkapazität.
Ihre Berechnungen bei der Berücksichtigung des Drucks sollten wie folgt aussehen:
Hub X Schneckenkolbenfläche = Einspritzvolumen
Einspritzkraft/ Schneckenkolbenfläche = Einspritzdruck
Deshalb:
Maximales Injektionsvolumen pro Kubikeinheit X maximaler Injektionsdruck (bar pro Kubikeinheit)/1000 = Schusskapazität der Injektionseinheit.
Berechnungen unter Verwendung von Schraubengewicht und Materialdichte sollten wie folgt sein:
Masse/Dichte = Volumen
ᴨ*D2*Schussgröße/4= Lauf/Schussvolumen
Faktoren, die sich auf die Produktschussgröße auswirken
Es gibt mehrere Faktoren, die Sie bei der Berechnung einer Schussgröße berücksichtigen müssen. Diese Faktoren sind wie folgt:
- Bei der Bestimmung der Schussgröße müssen Fichtenvolumen, Angussvolumen und Produktvolumen berücksichtigt werden. Dies liegt daran, dass das Polymer beim Einspritzen in die Form das Fichten-, Anguss- und Produktvolumen ausfüllen muss.
- Ein weiteres wichtiges Problem, das sich auf die Berechnungen der Schussgröße auswirkt, ist die Polymerschrumpfung. Die Schrumpfung resultiert aus dem Abkühlen des geschmolzenen Polymers. Aufgrund der unterschiedlichen Dichten von Polymeren variiert die Formschwindung.
- Art und Menge der Zusatzstoffe eines Polymers können dessen Dichte und Fließeigenschaften verändern.
Diese Faktoren können Ihnen helfen, die Schussgröße, das Volumen und die Laufkapazität abzuschätzen.
Injektionseinheit
Der Zweck der Einspritzeinheit besteht darin, das Kunststoffmaterial gleichmäßig zu schmelzen, bevor es mit einem vorbestimmten Druck und einer vorbestimmten Durchflussrate in die Form eingespritzt wird. Dies sind anspruchsvolle Aktivitäten, da Fluorpolymere eine begrenzte Wärmeleitfähigkeit, eine hohe spezifische Wärme und eine hohe Schmelzviskosität aufweisen.
Auch hier wurden zahlreiche Variationen entwickelt, um die vorliegenden komplexen Probleme anzugehen. Eine allgemeine Einteilung der Varianten kann in vier primäre Spritzeinheitenkonzepte erfolgen:
- Einstufiger Plunger oder Stößel
- Zweistufiger Stößel
- Schraube mit einer Stufe
- Schnecke/Stößel mit zwei Stufen
Obwohl es immer noch in winzigen Maschinen und einigen Spezialgeräten vorhanden ist, ist die einstufige Rammeinheit aufgrund ihrer Ineffektivität beim Erhitzen, Mischen und der Druckübertragung im Wesentlichen veraltet. Es profitiert von Einfachheit und Erschwinglichkeit.
Außerdem ist der zweistufige Stößel so gut wie veraltet. Der Stößel ist immer noch ein ineffektiver Mischer und Heizer, obwohl versucht wurde, ihn durch Trennen der Heiz- und Druckströmungsvorgänge zu verbessern.
Die zweistufige Schnecke/Stempel-Einheit trennt die Rollen von Strömung und Wärme weiter, indem ein Stempel zum Einspritzen anstelle einer Schnecke zum Mischen und Erhitzen verwendet wird. Die Idee ist reizvoll, weil beide effektive Werkzeuge für ihre jeweiligen Aufgaben sind.
Darüber hinaus wird die Injektionseinheit häufig anhand des maximalen Injektionsdrucks und des verfügbaren Injektionsvolumens bewertet. Der größtmögliche Druck am stromabwärtigen Ende der Schnecke wird als Einspritzdruck bezeichnet. Dies hängt vom Durchmesser der Schraube und der Kraft ab, die dagegen drückt.
Achten Sie jedoch darauf, dass Sie ihn nicht mit dem Druck in der Hydraulikleitung verwechseln, der auf den Einspritzzylinder wirkt, der die Schnecke antreibt, und auch nicht mit dem Druck zu interpretieren sind, der zum Füllen der Formkavitäten erforderlich ist. Aufgrund von Druckverlusten in den Düsen- und Formzuführungssystemen ist diese wesentlich geringer.
Die wichtigsten Aktionsreihen der Spritzeinheit sind wie folgt:
- Das Material wird erhitzt und geschmolzen, während sich die Schnecke dreht, und dann entlang der Schneckengänge zum stromabwärtigen Ende der Schnecke transportiert. Die Zylinderdüse wird durch die Verwendung eines mechanischen oder thermischen Ventils oder durch das Vorhandensein eines früheren Formteils geschlossen.
Bis sich genügend Schmelze zur Herstellung des nächsten Formteils angesammelt hat, drückt die sich sammelnde Schmelze die noch rotierende Schnecke gegen einen kontrollierten Widerstand (den Gegendruck) zurück. Die Drehung der Schnecke hält hier an. Es ist Zeit, bereit für die Schmelze zu sein.
- Beim Öffnen der Fassdüse bewegt sich die Schnecke ohne Drehung in axialer Richtung vorwärts und wirkt wie ein Stößel. Dadurch wird die vor dem stromabwärtigen Ende der Schnecke gesammelte Schmelze durch die Düse und in die Form gedrückt (eingespritzt).
Um zu verhindern, dass Schmelze die Schneckengänge hinunter zurückfließt, kann am stromabwärtigen Ende der Schnecke ein Ventilsystem installiert werden. Dies ist die Einspritz- oder Formfüllphase.
- Nach dem Füllen der Form wird der Schneckendruck noch kurz gehalten, um den Volumenschwund der erkaltenden Schmelze im Inneren der Form auszugleichen. Die Verpackungs- oder Haltephase ist jetzt.
- Schließlich kommt es zur Haltephase, in der der Zyklus der Einspritzeinheit mit der Schneckendrehung wieder aufgenommen wird und die Vorbereitung geschmolzen wird, während die Form geschlossen bleibt, damit das Formteil auf die Ausstoßtemperatur abkühlen kann.
Es gibt erhebliche Druckabfälle, wenn die Kunststoffschmelze in die Einspritzdüse und anschließend durch das Formzuführungssystem und die Kavitäten gedrückt wird. Mit einfachen Regeln lassen sich diese Druckverluste nicht berechnen.
Klemmeinheit
Die Formschließung wird gegen Kräfte aufrechterhalten, die entstehen, wenn Kunststoff durch Einspritzdruck unter Verwendung einer Schließeinheit für ein IMM in eine geschlossene Form gedrückt wird. Es hat ein Antriebssystem, das die bewegliche Platte der Spritzgießmaschine in mindestens einer Richtung bewegen kann.
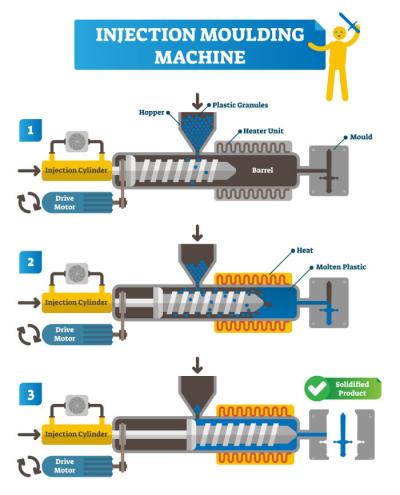
Arten von Spanneinheiten
Im Spritzgießprozess gibt es verschiedene Arten von Schließeinheiten. Sie sind wie folgt:
Kniehebel-Klemmung
Ein mechanisches Gerät, das die Kraft verstärkt, ist ein Knebel. Zwei Stangen werden verbunden und enden mit einem Drehpunkt in einer Formmaschine. Das Ende einer Stange ist mit einer festen Platte verbunden, während das andere mit einer beweglichen Platte verbunden ist. Der Knebel hat eine V-förmige Form, wenn die Form geöffnet ist. Die beiden Balken bilden eine gerade Linie, wenn Druck auf den Drehpunkt ausgeübt wird.
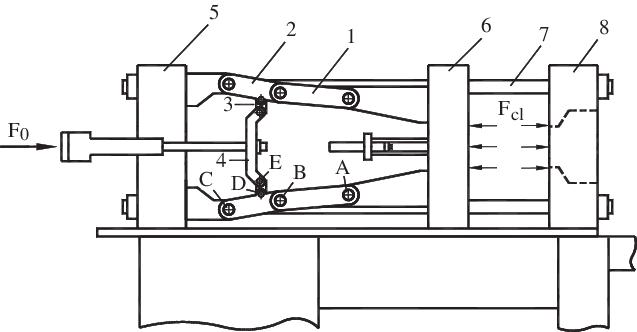
Zu den Vorteilen des Kniehebelspannens gehört, dass es weniger Geld und Pferdestärken erfordert und einen positiven Plan der Form bietet. Außerdem bestehen die Nachteile des Klemmens vom Kniehebeltyp darin, dass es eine hohe Wartung erfordert und schwierig durchzuführen ist.
Hydraulische Klemmung
In diesem Fall ist der RAM des Hydrauliksystems mit der beweglichen Platte verbunden, und eine von einem Hydraulikzylinder angetriebene Schließeinheit ist direkt mit der geschlossenen beweglichen Form verbunden. Der Hydraulikzylinder hat zwei Abschnitte: den Öleingang und den Ausgang.
Öl drückt den Stempel nach vorne, wenn es unter Druck in den Zylinder eintritt, wodurch sich die bewegliche Platte und die Form schließen. Außerdem sind das RAM-Comeback und die Form offen, wenn Öl aus dem Zylinder freigesetzt wird.
Zu den Vorteilen des hydraulischen Spannens gehören die einfache Steuerung der Spanngeschwindigkeit und -unterstützung in jedem Winkel, die einfache Messung der Spannkraft, die einfache Einrichtung des Modus und die Einstellung der Spannkraft sowie die einfache Wartung.
Die Nachteile dieser Klemmart bestehen darin, dass sie mehr kostet und teurer ist als ein Kniehebelsystem und eine Klemme mit positivem Hauptwort.
Magnetische Spanneinheit
Magnetmodule innerhalb der magnetischen Formaufspannplatten oder Aufspannplatten erzeugen die Schließkraft. Das Schnittstellenpanel kann das Klemmen der Form, den Formwechsel sowie das Magnetisieren und Entmagnetisieren der Platten steuern.
Zu den Vorteilen dieser Spanneinheit gehören, dass Strom nur während der Magnetisierungs- und Entmagnetisierungsphasen benötigt wird, nicht während des Spannens, die Echtzeit-Klemmkraftmessung mit vielen Sicherheitsfunktionen und die kostenlose Wartung.
Formschussgewicht
Die Menge an Material, die in die Form eingespritzt wird, um die Form einschließlich des Zuführsystems zu füllen, wird als „Formschussgewicht“ oder „Produktschussgewicht“ bezeichnet. Fichten-, Läufer- und Torgewicht sind dagegen die Bestandteile des Schussgewichts. Der Weg, den die Schnecke zurücklegt, um das Produkt zu füllen, einschließlich des Zufuhrsystems, wird als Form-/Produktschussgröße bezeichnet.
Fazit
Beim Spritzgussverfahren wird Rohkunststoff geschmolzen, in die Form gespritzt, abkühlen und erstarren lassen und dann das fertige Objekt ausgestoßen. Die Schussgröße ist entscheidend, da sie Polymer-Underfill und Flash verhindert. Auch andere Faktoren, wie z. B. die Zylinderkapazität, wirken sich auf den allgemeinen Spritzgießprozess aus.