Zwei verschiedene Kunststoffharze werden während des Doppelspritzgussverfahrens, auch bekannt als Dual-Shot, Double-Shot, Multi-Shot und Umspritzen, in einem einzigen Bearbeitungszyklus zusammengeformt.
Eine hochmoderne Fertigungstechnik namens Doppelinjektion, auch bekannt als Zwei-Material-, Zwei-Schuss-Spritzguss oder Zwei-K-Spritzguss, wird verwendet, um komplizierte Formteile aus zwei verschiedenen Materialien herzustellen.
Während des 2-Schuss-Spritzgießens kontrollieren wir sorgfältig das Einspritzen zahlreicher Materialien, einschließlich zweier unterschiedlicher Harzarten, in eine einzige Mehrkammerform unter Verwendung einer hochspezialisierten und automatisierten Technik.
Zwei-Schuss-Formverfahren
Eine Spritzgussmaschine wird im Two-Shot-Molding-Verfahren verwendet, bei dem zwei Materialien in einem Spritzgusszyklus „umspritzt“ werden. Die in den Formhohlraum eingespritzte Materialmenge wird als „Schuss“ bezeichnet.
Beim Zweistufen-Spritzgießen wird ein erster Abschnitt geformt, und nachdem er fertig ist, wird ein zweiter Teil eingespritzt, um den letzten Abschnitt des Formteils zu erzeugen. Beide Teile müssen (chemisch) vergleichbar sein, damit das zweistufige Formverfahren erfolgreich ist, damit eine Verbindung stattfinden kann.
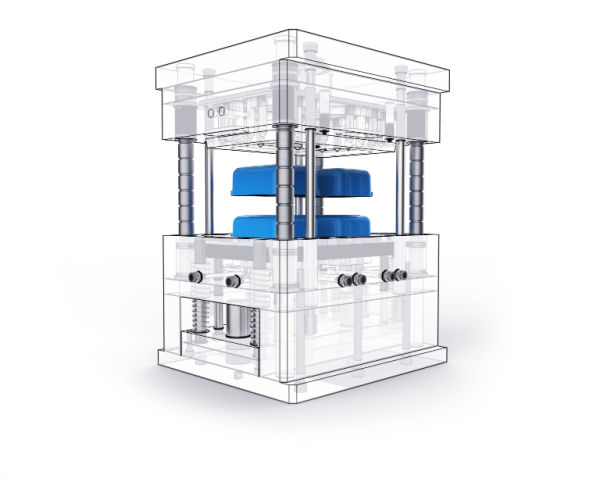
Ein Teil aus hartem Material kann mit einem Teil aus weichem Material durch zweistufiges Spritzgießen gefügt werden. In einer Form mit zwei Kavitäten kombiniert das Verfahren das Formen von zwei Komponenten. Es kann die Attraktivität des Produkts in Bezug auf Haptik, Farbe usw. erheblich verbessern. Mit dem Two-Shot-Molding gibt es viele verschiedene Gestaltungsmöglichkeiten.
Die Zwei-Schuss-Spritzgusstechnik ist in zwei Schritte unterteilt. Die erste beinhaltet das Einspritzen von Harz in eine Form, die dann gekühlt wird, um ein festes Objekt zu erzeugen, ähnlich wie beim herkömmlichen Spritzgießen.
Das neu geformte Objekt wird in der zweiten Stufe mithilfe einer rotierenden Platte oder eines Roboterarms zu einer zweiten Form transportiert. Je nach Design erhält das neu geformte Teil dann eine zweite Harzinjektion in, durch oder um bestimmte Bereiche der ersten Form.
Nach Bildung einer molekularen Verbindung zwischen den beiden Kunststoffharzen wird der aus mehreren Harzen geformte Gegenstand abgekühlt und ausgestoßen.
Obwohl das Verfahren einfach zu verstehen ist, ist es eine Herausforderung, es zu beherrschen. Selbst die kleinsten Fehler können aufgrund der erforderlichen hohen technischen Kompetenz und der erforderlichen Detailtreue zu erheblichen finanziellen Verlusten führen, insbesondere bei Massenproduktionen.
Aus diesem Grund ist es wichtig, einen Lieferanten mit außergewöhnlichen Fähigkeiten zu wählen. Exzellente Lieferantenqualitäts-Scorecards etablierten Prozesse, um zu verhindern, dass Grate, Fließlinien, Short-Shots und Backup-Pläne die Kapazität erhöhen, da Ihr Unternehmen und Ihr Bedarf an einer Zwei-Schuss-Spritzguss-Erweiterung alles sind, worauf Sie achten sollten.
Dieses Verfahren macht das zweistufige Formen ideal für Schalter, Knöpfe, Zahnbürsten und Kappen für Behälter.
Anwendungen des Zwei-Schuss-Spritzgießens
Für komplizierte, mehrfarbige und aus mehreren Materialien bestehende Kunststoffwaren, insbesondere bei Massenproduktionen, ist das Zweikomponenten-Spritzgießen die beste Kunststoffformtechnik.
Darüber hinaus wird das Two-Shot-Molding-Verfahren im Automobilsektor zur Herstellung einer breiten Palette von Produkten und Teilen eingesetzt. Andere Artikel, die im Double-Shot-Verfahren hergestellt werden, sind Rasen- und Gartengeräte sowie landwirtschaftliche Geräte.
Zweikomponenten-Spritzgussteile werden in fast allen Branchen eingesetzt, von Konsumgütern bis hin zum Bauwesen, aber sie werden am häufigsten in Situationen eingesetzt, in denen Folgendes erforderlich ist:
- Teile oder Komponenten, die sich bewegen können
- starre Oberflächen mit flexiblen Griffen
- entweder akustische Dämpfung oder Vibration
- oberflächliche Erklärungen oder Identifikationen
- Komponenten mit mehreren Materialien oder Farben
Idealerweise wird das Zweikomponenten-Spritzgussverfahren für komplexe Teile verwendet, die aus mehreren Komponenten bestehen.
Vorteile des Two-Shot-Moulding-Prozesses
Kunststoffpolymere werden in einer Reihe von Produktionsprozessen verwendet, wie z. B. Extrusion, Duroplast-Formpressen und Zweikomponenten-Spritzguss. Obwohl jedes ein praktikables Herstellungsverfahren ist, verwenden viele Kunststoffhersteller dieses Verfahren aufgrund mehrerer Vorteile.
Um das erste Segment des Produkts herzustellen, wird zunächst ein Material in eine Form gespritzt. Daran schließt sich eine zweite Injektion eines mit dem ersten kompatiblen Sekundärmaterials an. Es gibt mehrere Gründe, warum sich viele Unternehmen dafür entscheiden, Kunststoffe oder Polymere auf diese Weise herzustellen.
Hier sind einige Vorteile des Two-Shot-Molding-Verfahrens:
Vielseitig
Produkthersteller bevorzugen Zweikomponenten-Spritzguss für eine Vielzahl von Anwendungen, darunter Fahrzeuginnenteile, medizinische Geräte, Werkzeuge und Spielzeug. Es ermöglicht Herstellern, eine Vielzahl von Komponenten und Farbtönen zu mischen, um ein robustes und ästhetisch ansprechendes Produkt herzustellen.
Materialien wie Silikon und Thermoplaste, Nylon und thermoplastische Elastomere oder steifes Nylon und Soft-Touch-Materialien sind einige Beispiele für Materialien, die mit diesem Verfahren erfolgreich gemischt werden können.
Kosteneffizient
Wenn die erste Form aus dem Weg gedreht und die zweite Form um das Produkt herum platziert wird, so dass der zweite kompatible Thermoplast in die zweite Form eingespritzt werden kann, erfordert das zweistufige Verfahren nur einen Maschinenzyklus.
Das Verfahren produziert bei jedem Durchlauf mehr Produkte für weniger Geld und erfordert weniger Arbeiter, um das fertige Produkt herzustellen, da es einen einzigen Maschinenzyklus anstelle mehrerer Maschinenzyklen verwendet. Darüber hinaus garantiert es eine feste Verbindung zwischen den Materialien, wodurch eine spätere Montage entfällt.
Hohe Produktqualität
Die meisten thermoplastischen Produkte profitieren auf vielfältige Weise vom Zweikomponenten-Spritzguss:
- Verbesserte Ästhetik. Wenn Produkte aus verschiedenfarbigen Kunststoffen oder Polymeren hergestellt werden, sehen sie schöner aus und sind für Verbraucher verlockender. Das Produkt erscheint teurer, wenn mehr als eine Farbe oder Textur verwendet wird.
- Bessere Ergonomie. Das Verfahren ermöglicht Soft-Touch-Oberflächen; So können die fertigen Produkte Griffe oder andere ergonomisch gestaltete Abschnitte haben. Dies ist entscheidend für Werkzeuge, medizinische Geräte und andere tragbare Gegenstände.
- Die Abdichtung wird verbessert, wenn Silikonpolymere und andere gummiartige Materialien für Dichtungen und andere Teile verwendet werden, die eine dichte Abdichtung benötigen.
- Es ermöglicht harten und weichen Polymeren, Gegenstände von kleinster Größe herzustellen, die außergewöhnlichen Komfort und Nutzen bieten.
- Im Vergleich zum Umspritzen oder zu konventionelleren Einlegemethoden kann die Anzahl der Fehlausrichtungen erheblich verringert werden.
- Es ermöglicht Herstellern, mehrere Materialien zu verwenden, die mit anderen Verfahren nicht effizient verbunden werden können, um kompliziertere Formmuster zu erstellen.
- Die gebildete Bindung ist unglaublich stark und macht das Endprodukt robuster, zuverlässiger und langlebiger.
Das Two-Shot-Molding-Verfahren hilft Herstellern, qualitativ hochwertige Produkte zu erzielen.
Teilkonsolidierung
Die Anzahl der Teile in einer fertigen Baugruppe wird durch den Zweikomponenten-Spritzguss verringert, wodurch durchschnittlich $40.000 USD an Entwicklungs-, Konstruktions- und Validierungsausgaben für jede erhöhte Teilenummer eingespart werden.
Effizient
Beim Zwei-Schuss-Spritzguss können mehrere Komponenten mit einem einzigen Werkzeug geformt werden, was weniger Arbeit zur Herstellung Ihrer Teile erfordert und kein nachträgliches Schweißen oder Verbinden der Komponenten erfordert.
Arten von Zwei-Schuss-Formstrukturen
Die Auswahl und Ausführung der richtigen Formstruktur ist entscheidend, um Kosten zu sparen und die Qualität sicherzustellen. Hier sind einige Arten von Zwei-Schuss-Spritzguss-Strukturen:
Core Toggle Two-Shot-Form
Da der Kern und die Kavität der Form nicht versetzt werden müssen, ist das Multi-Shot-Formverfahren mit Kernknebel das einfachste. Alternativ ändert das Verschieben des Schiebers die Geometrie des Formhohlraums.
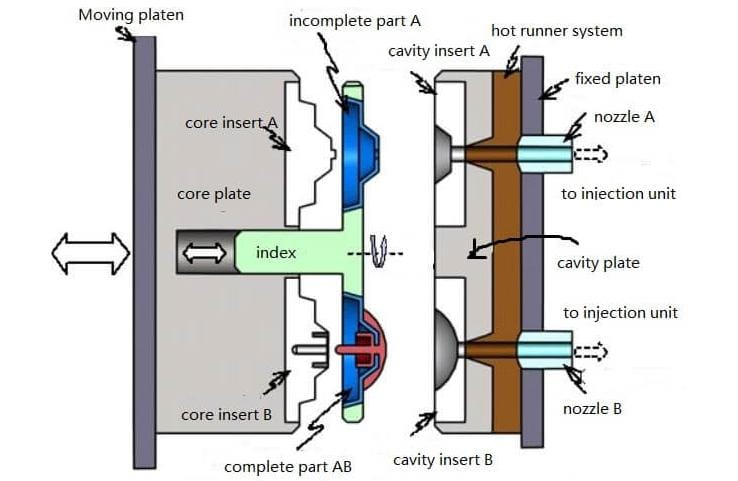
Die Substanz A wird zuerst in den Hohlraum eingespritzt, wenn sich der Schieber während des Spritzgussverfahrens unter Verwendung der Kern-Kniehebel-Zweikomponenten-Form in seiner expandierten Position befindet. Ziehen Sie dann den Schieber zurück, um einen neuen Bereich der Kavität freizulegen.
Der verbleibende Raum wird gefüllt, indem der Schieber bewegt wird, nachdem Material B durch einen anderen Anschnitt (oberhalb der mittleren Düse) in die modifizierte Kavität eingespritzt wurde.
Das Kunststoffbauteil wird dann nach dem Aushärten aus der Form gedrückt. Umgewälzt in der gleichen Reihenfolge wie oben, um das Formen fortzusetzen.
Obwohl der Preis des Werkzeugs steigt, wenn der Form ein Schieber hinzugefügt wird, kann es immer noch deutlich günstiger sein als Formen mit rotierender Platte oder rotierender Welle. Leider ist es nicht möglich, komplizierte, mehrfarbige Plastikteile herzustellen.
Rotationsplatten-Zwei-Schuss-Form
Auf der Mittellinie der Aufspannplatte, die parallel zur Rotationsachse verläuft, hat die Formkernplatte zwei identische Kerne, die zueinander spiegelbildlich sind. Zwei Kavitäten mit verschiedenen Geometrien sind in der Kavitätenplatte enthalten, die an der festen Platte befestigt ist.
Der Drehteller vervollständigt das Wechseln der Formteile in jedem Zyklus, und zwar ohne menschliches Wechseln.
Die Form, die mehr Materialien aufnehmen kann, ist hier nur bei den beiden Materialien zu sehen. Je nach Materialverbrauch kann der Drehteller um 90°, 120° oder 180° gedreht werden. Außerdem ist eine spezielle Spritzmaschine erforderlich, um die notwendige Rotation auf der Kernseite zu erzeugen.
Wippen-Zwei-Schuss-Formstruktur
Wenn sich eine Seite nach oben bewegt, die andere Seite nach unten usw., besteht die Plattenstruktur aus zwei Seiten, die sich um die Mitte drehen. Die meisten Tastaturformdesigns mit Zahlen und Buchstaben verwenden die Wippenstruktur.
Die Struktur enthält geschlossene numerische oder alphabetische Zeichen wie 0, 4, 8, A, B, D und O. Das Sekundärmaterial kann nur dann leicht in den begrenzten Bereich eindringen, wenn eine Wippenkonstruktion verwendet wird, wodurch ein schönes Erscheinungsbild entsteht.
Die Wippenstruktur funktioniert wie folgt:
- Nach einer Injektion wird die Form geöffnet.
- Die gebrochene Nadel wird durch die Schubstange abgesenkt, wodurch sich die Wippe um die rotierende Welle dreht.
- Die obere Platte wird durch Schieben der Wippe nach oben gedrückt, wodurch die abgebrochene Nadel aus der Form heraustritt.
Ein gebrochenes Loch wird erzeugt, wenn die Nadel am Rand des abgedichteten Abschnitts des Primärprodukts ansteigt. Um das Sekundärmaterial aus dem gebrochenen Loch in den geschlossenen Bereich zu bohren, wird die Nadel während des doppelten Spritzgussvorgangs durch den zurückkehrenden Stift der gebrochenen Platte nach unten bewegt.
Hohlraum-Gleitstruktur
Der männliche Modellhohlraum gleitet unter dem Einfluss des Motors, wenn die Form nach einer Injektion geöffnet wird. Vor dem zweiten Spritzgießvorgang wird die Form mit einem vorgegebenen Abstand zur Urform ausgerichtet.
Zu berücksichtigende Faktoren bei der Verwendung von Two-Shot-Molding
Die folgenden Faktoren werden beim Double-Shot-Molding berücksichtigt:
Materialauswahl
Physikalische, mechanische, chemische, thermische, elektrische, Entflammbarkeit und UV-Beständigkeit sind wichtige Überlegungen bei der Auswahl eines Materials für Ihre Komponente. Sie müssen Antworten auf eine Reihe von Fragen geben, um Ihre Materialauswahl zu fokussieren, darunter:
- Welchen Temperaturen wird Ihr Produkt ausgesetzt?
- Wie flexibel oder steif muss das Material zum Biegen sein?
- Stoßfestigkeit: Wie robust muss seine Oberfläche sein?
- Wie gut hält es großen Belastungen in Bezug auf die Druckfestigkeit stand?
- Wird das Bauteil UV-Strahlen ausgesetzt, wie sie im Freien zu finden sind?
- Wird das Teil Chemikalien ausgesetzt, die seine Funktion beeinträchtigen, insbesondere im Laufe der Zeit?
- Welche Haltbarkeit ist für das Teil erforderlich?
Materialverträglichkeit
Die Chemie der Materialien ist von entscheidender Bedeutung bei der Entscheidung, welche Materialien für das Zweikomponenten-Spritzgießen verwendet werden sollen. Während einige Materialien nicht perfekt binden, arbeiten andere gut zusammen und erzeugen eine solide molekulare Haftung.
Führen Sie vor Beginn der Herstellung einen Haftungstest durch, wenn die Haftungseigenschaft zweier Verbindungen unklar ist. Wenn die Verbindung nicht ausreicht, können Fixierungen in das Design eingebaut werden, z. B. Hinterschneidungen, Rillen oder Schultern, um die Haftung zu erhöhen und die beiden Verbindungen miteinander zu verbinden.
Eine Materialkompatibilitätstabelle wird überprüft, um zu bestimmen, welche Polymere aneinander haften und welche Polymere unverträglich sind. Außerdem eliminiert es die Möglichkeit einer Kontamination, die ein Problem darstellt, wenn zwei verschiedene Formen verwendet werden.
Darüber hinaus führt das zweistufige Formverfahren im Vergleich zur Herstellung eines identischen Produkts oder Teils mit zwei verschiedenen Formverfahren zu einer viel stärkeren Verbindung. Die Möglichkeit, mehrfarbige Kunststoffartikel mit dem Zwei-Schuss-Spritzgussverfahren herzustellen, ist einer der zusätzlichen Vorteile des Verfahrens gegenüber dem Lackieren, das mit der Zeit an Wirksamkeit verlieren kann.
Mit dem Zwei-Schuss-Ansatz können Sie nützlichere, raffiniertere Elemente erstellen. Weiterhin kann weicherer Kunststoff mit hartem Kunststoff gemischt werden. Das Produkt hat eine deutlich höhere Integrität. Zwei-Schuss-Kunststoffformteile sind oft weitaus haltbarer und stoßfester.
Das Verfahren eignet sich auch hervorragend zur Herstellung von weichen Griffen für elektrische Geräte, Klimaanlagendichtungen und Dichtungen sowie rutschfesten Oberflächen. Mit dieser Methode können Logos erstellt werden, die im Gegensatz zu aufgemalten Logos niemals verblassen würden.
Abschaltungen
Um Löcher, Schnappmerkmale und lange Durchgangslöcher zu bilden, schließt die Form diese Stellen, um zu verhindern, dass Kunststoff in diese Stellen fließt.
In diesen Situationen dichten die beiden Hälften der Form gegeneinander ab. Dadurch können sich die Dichtflächen der Form öffnen und schließen, ohne miteinander zu kollidieren. Drei bis fünf Grad sollten der minimale Verzugswinkel sein. Je länger die Form lebt, desto höher ist die Lichtung und desto größer der Zug.
Gate-Typ
Beim Spritzgießen tritt das geschmolzene Harz durch einen Angusskanal in die Formkammer ein. Um die idealen Teileproportionen und das ästhetische Aussehen zu erreichen und gleichzeitig ein Verziehen zu vermeiden, müssen die Art des Angusses, das Design und die Position berücksichtigt werden.
Laschen- und Heißkanalanschnitte sind die zwei Arten von Anschnitten, die beim Spritzgießen am häufigsten verwendet werden:
- Die beliebtesten und effizientesten Gates sind Tab-Gates; Da sie jedoch so unkompliziert sind, sind sie möglicherweise nicht für Ihre Anforderungen geeignet.
- Hot Tip Gates verfügen über winzige elliptische Öffnungen. Das Harz wird durch die thermostatgesteuerte Heizung, die an der Rückseite der Form angebracht ist, heiß genug gehalten, um durch das schmale Torloch zu gelangen.
Molekulare chemische Bindung
Damit eine starke molekulare Bindung möglich ist, sollten Ihr Substrat und das Second-Shot-Harz idealerweise chemisch kompatibel sein. Der längste Schenkel oder Oberflächenbereich ist ideal für die Verbindung zwischen den beiden Harzen. Der zweite Schuss ist durch die Auswahl der idealen Materialien und des Fugendesigns fast unmöglich zu entfernen.
Auch wenn eine hochgradige chemische Bindung erreicht werden kann, empfehlen wir dringend die Verwendung einer geeigneten mechanischen Bindung, wenn die Bindung für Ihre Anwendung wichtig ist.
Gate-Standort
Dies ist für die Herstellung von Solid-Surface-Kosmetika und einer homogenen Form unerlässlich. Beim Single-Shot-Spritzgießen kann die Schmelze dank der Platzierung des Anschnitts durch den dicksten Teil der Öffnung eintreten, bevor sie zu den kleineren Bereichen fließt.
Vorschläge für Zwei-Schuss-Spritzgießen
Hier sind einige Empfehlungen für das Zwei-Schuss-Spritzgießen:
Nummer 1
Der weiche Kunststoff wird ein zweites Mal geformt, nachdem er zuerst als harter Kunststoff geformt wurde. Das erste Mal ist transparent; das zweite mal nicht. Die erste Formung erfolgt mit einem Hochtemperaturkunststoff, während die Doppelformung mit einem Niedertemperaturkunststoff erfolgt.
Nummer 2
Testen Sie die Form, um ein fertiges Produkt vor der eigentlichen Produktion herzustellen.
Nummer 3
Bevor die Form hergestellt wird, finden Sie alle potenziellen Fehler und beheben Sie sie.
Nummer 4
Berücksichtigen Sie das Schrumpfen der beiden Materialien. Im Allgemeinen wirkt sich das anfänglich erzeugte Material auf die Schwindung aus.
Nummer 5
Eine zweite Injektion kann erst verabreicht werden, wenn die erste vollständig gewirkt hat.
Nummer 6
Um Beschädigungen während des Formprozesses zu vermeiden, berücksichtigen Sie die Formposition.
Nummer 7
Lassen Sie zu, dass der Rand des ersten Spritzgussteils zu groß ist. Dadurch wird sichergestellt, dass die zweite Einspritzung einen höheren Druck hat.
Nummer 8
Stellen Sie sicher, dass die Parameter der Injektionseinheit den erforderlichen Druck, die Durchflussrate und die Kühlkapazität ergeben.
Nummer 9
Stellen Sie sicher, dass die strukturelle Integrität des ersten Formteils den Einspritzdruck des zweiten Formteils überstehen kann.
Fazit
Personen, die mit dem Zwei-Schuss-Spritzgießen nicht vertraut sind, könnten denken, dass es schwierig ist. Es erfordert zwar ein zweites Material und Verfahren, was der Komponentenerstellung einen weiteren Faktor hinzufügt, aber es ist relativ einfach.
Das Zweikomponenten-Spritzgießen kann unter anderem mit einer Drehplatte, einem beweglichen Kern oder einer Umspritzung erfolgen. Die ersten beiden erfordern zwei Prozesse, zwei Angusssysteme und eine zweite Spritzeinheit.
Letzteres verwendet oft zwei verschiedene Formen, eine für jedes Material, kann aber auch mit nur einer Form, zwei Angusssystemen und manuellem oder automatisiertem Pick-and-Place-Teiletransfer durchgeführt werden.