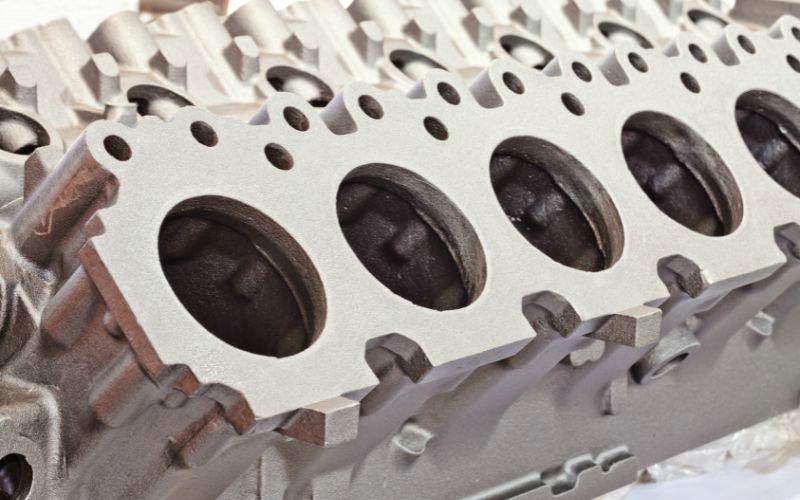
Was ist Druckguss?
Druckguss ist ein Herstellungsverfahren, bei dem geschmolzenes Metall in Formen gegossen oder eingespritzt wird, bekannt als stirbt. Die in diesem Verfahren typischerweise verwendeten Metalle sind Zink, Aluminium und deren Legierungen. Sie nehmen Sie mit auf eine Reise durch ein Verfahren, das aufgrund seiner Effizienz bei der Produktion großer Stückzahlen weit verbreitet ist.
Beim Druckguss wird Metall in einem Ofen geschmolzen und dann unter hohem Druck in die Formen gespritzt. Dieses Verfahren ist beliebt, weil es Teile mit Präzision, komplizierten Details und hervorragender Oberflächengüte produzieren kann – Eigenschaften, die in Branchen wie der Automobil-, Luft- und Raumfahrt- und Elektronikindustrie gefragt sind.
Druckguss ist bei Herstellern sehr gefragt, da sich damit einheitliche Teile in gleichbleibender Qualität herstellen lassen. Ob Sie damit komplexe Getriebekomponenten für Fahrzeuge oder schlanke, langlebige Gehäuse für Elektronik herstellen, Druckguss ist eine Säule der modernen Fertigung, insbesondere wenn es auf Präzision und Volumen ankommt.
Druckgussverfahren
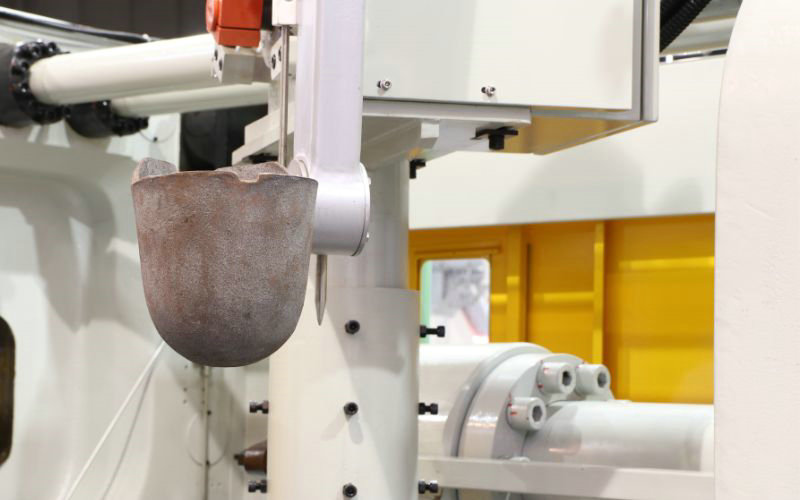
Es gibt drei Hauptarten von Druckgussverfahren: Schwerkraft-Kokillenguss, Kaltkammer-Druckguss und Warmkammer-Druckguss.
Kokillenguss
Beim Kokillenguss wird geschmolzenes Metall direkt aus einer Pfanne in eine halbpermanente oder permanente Form gegossen. Der Hohlraum füllt sich ohne andere Kraft als die Schwerkraft. Zu den Vorteilen des Kokillengusses gehört die Möglichkeit, dichte, hochwertige Gussteile mit hervorragenden mechanischen Eigenschaften herzustellen, die für die Wärmebehandlung geeignet sind. Es ist kostengünstig für die Produktion kleiner bis mittlerer Stückzahlen.
Kaltkammer-Druckguss
Beim Kaltkammer-Druckguss ist der Schmelzofen getrennt von der Druckgussmaschine. Für jeden Zyklus wird eine genaue Menge geschmolzenen Metalls in die unbeheizte Schusskammer der Maschine geschöpft; dann presst ein hydraulischer Kolben das Metall unter hohem Druck zwischen 2.000 und 20.000 psi in die Form. Kaltkammer-Druckguss wird für Legierungen mit höheren Schmelzpunkten wie Aluminium verwendet. Dabei entstehen starke, langlebige Teile, die Zykluszeiten sind jedoch langsamer als bei einer Warmkammer.
Warmkammer-Druckguss
Beim Warmkammer-Druckguss wird der Einspritzmechanismus in ein Becken aus geschmolzenem Metall getaucht, das durch einen Schwanenhals und einen Kolben in die Form geleitet wird. Zu Beginn jedes Zyklus zieht sich der Kolben zurück, sodass sich der Schwanenhals mit geschmolzenem Metall füllt. Der Kolben presst das Metall dann mit einem Druck von 1.000–5.000 psi durch den Schwanenhals in die Form. Warmkammer-Druckguss wird für Legierungen mit niedrigem Schmelzpunkt wie Zink und Magnesium verwendet. Es ermöglicht schnellere Zykluszeiten und kann komplizierte Teile mit reduzierter Porosität herstellen.
Druckgussanwendungen
Automobilindustrie: Druckguss wird im Automobilsektor häufig eingesetzt. Sie finden Komponenten wie Motorblöcke, Getriebeteile und Strukturelemente, die mit diesem Verfahren hergestellt werden. Die Fähigkeit, schnell und effizient starke, langlebige Teile herzustellen, macht Druckguss zu einer bevorzugten Wahl für Automobilingenieure.
- Motorkomponenten
- Getriebe
- Autorahmen
Luft- und Raumfahrt: Die Luft- und Raumfahrtindustrie schätzt Druckguss für die Herstellung komplexer Teile, die Präzision und können rauen Bedingungen standhalten. Komponenten wie Fahrwerk, Cockpitinstrumente und Motorteile werden normalerweise im Druckgussverfahren hergestellt.
- Instrumentierungsgehäuse
- Fahrwerksteile
- Motorkomponenten
Elektronik: In der Elektronik wird Druckguss verwendet, um Teile wie Steckverbinder, Gehäuse und Kühlkörper herzustellen. Diese Teile profitieren von der Fähigkeit des Druckgusses, komplexe Designs mit hoher Wärmeleitfähigkeit zu bilden.
- Temperatur fällt
- Anschlüsse
- Gehäuse
Was ist Metallspritzguss?
Metal Injection Molding (MIM) bietet Ihnen ein Herstellungsverfahren zur Produktion komplexer Teile in mittleren bis großen Stückzahlen. MIM kombiniert die Gestaltungsfreiheit und Komplexität der Formen des Kunststoff-Spritzgusses mit der außergewöhnlichen Festigkeit und Integrität von Metall.
Hier ist ein kurzer Überblick über MIM:
- Materialien: Bei der Materialauswahl für MIM wählen Sie in der Regel Eisenmetalle wie Edelstahl, der dem Endprodukt erhebliche Festigkeit und Haltbarkeit verleiht.
- Stärke und Präzision: MIM-Teile sind für ihre beeindruckende Festigkeit und Präzision bekannt. Sie halten enge Toleranzen ein und eignen sich daher sowohl für industriell Und medizinisch Anwendungen.
- Komplexe Geometrien und dünne Wände: Mit MIM können Sie Teile mit komplexen Geometrien und dünnen Wänden herstellen, was mit herkömmlichen Metallbearbeitungsprozessen schwierig oder unmöglich wäre.
Metallspritzgussverfahren
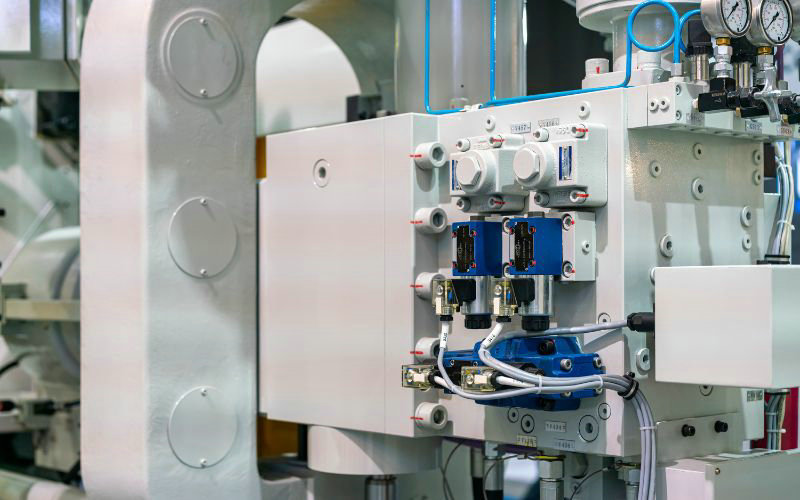
Ihr Verständnis von MIM beginnt mit seinem Primärmaterial — einem Rohstoffe das aus feinem Metallpulver und einem Polymerbindemittel besteht. Zu den in diesem Verfahren verwendeten Metallen gehören Edelstahl, Titan, Nickellegierungen und Kupferlegierungen. In seinen Anfangsphasen ähnelt MIM dem Kunststoffspritzguss; das Ausgangsmaterial wird erhitzt, bis es zähflüssig wird und in eine Formhöhle eingespritzt werden kann.
Sobald Ihr Formteil fest ist, beginnt der Entbinderungsprozess. Dabei wird der Großteil des Bindemittels entfernt, wodurch das Teil für das Sintern vorbereitet wird. Während des Sinterns wird Ihr Teil hohen Temperaturen ausgesetzt, die die Metallpartikel zusammenbinden und ihre Integrität gewährleisten.
Nach dem Sintern werden Sie feststellen, dass das Teil erheblich geschrumpft ist – normalerweise um 15–201 TP3T. Der Sinterprozess ermöglicht Ihnen jedoch, eine hervorragende Maßgenauigkeit und Oberflächengüte zu erzielen, wodurch die Notwendigkeit einer anschließenden Bearbeitung häufig minimiert wird. MIM ist bei der Herstellung kleiner Teile in großen Mengen äußerst kosteneffizient, da weniger Materialabfall entsteht und enge Toleranzen ohne umfangreiche Nachbearbeitung eingehalten werden können.
Letztendlich bietet das Metallspritzgießen eine einzigartige Kombination aus Qualität, Effizienz und Vielseitigkeit innerhalb von Fertigungsprozessen. Die Möglichkeit, eine Vielzahl von Metallen zu verwenden und spezifische Materialeigenschaften wie Härte, Zugfestigkeit und Temperaturbeständigkeit zu erreichen, macht es zu einem wertvollen Verfahren in zahlreichen Branchen.
Anwendungen für Metallspritzguss (MIM)
Metallspritzguss (MIM) ist präzise und kostengünstig und eignet sich besonders für die Massenproduktion kleiner bis mittelgroßer Komponenten. MIM wird in verschiedenen Branchen eingesetzt, da sich damit komplexe Formen mit hervorragender Oberflächengüte herstellen lassen.
Luft- und Raumfahrt und Automobil:
- Aufgrund seiner hohen Festigkeit und Haltbarkeit eignet sich MIM ideal für die Herstellung von Teilen wie Türgriffen, Scharnieren und Motorkomponenten.
Medizin und Zahnmedizin:
- Die medizinische Industrie profitiert von der Präzision von MIM bei der Herstellung chirurgischer Instrumente, Implantate und Klammern, die Biokompatibilität erfordern.
Unterhaltungselektronik:
- Kleine Komponenten wie Mobiltelefonteile oder Kamerabaugruppen nutzen die Leistungsfähigkeit von MIM hinsichtlich Miniaturisierung und detaillierter Designmöglichkeiten.
Waffenindustrie:
- MIM wird zur Herstellung verschiedener Schusswaffenkomponenten verwendet, einschließlich Abzügen, Hämmern und Visierteilen, die enge Toleranzen und Festigkeit erfordern.
Allgemeine Industrieausrüstung:
- Aufgrund der Möglichkeit und Konsistenz großer Stückzahlen wird MIM bei der Herstellung von Pumpenkomponenten, Verbindungselementen und Ventilen eingesetzt.
In diesen Anwendungen bietet MIM unter anderem folgende Vorteile:
- Materialien mit hoher Dichte und hervorragenden mechanischen Eigenschaften
- Möglichkeit zur Integration von Funktionen wie Gewinden, Zahnrädern und internen Kanälen ohne sekundäre Operationen
- Produktion von Teilen nahe der endgültigen Form, wodurch Abfall minimiert wird
Druckguss vs. MIM: Vorteile und Nachteile
Vorteile von MIM gegenüber Druckguss
1. Mit MIM können kleine, komplexe Teile mit komplizierten Merkmalen und dünnen Wänden hergestellt werden, die beim Druckguss schwierig oder unmöglich wären.
2. MIM bietet eine größere Auswahl an Materialien, darunter Eisenmetalle, rostfreie Stähle, Titan und Nickellegierungen. Druckguss ist normalerweise auf Nichteisenmetalle wie Aluminium, Zink und Magnesium beschränkt.
3. MIM-Teile verfügen aufgrund des Sinterprozesses über hervorragende mechanische Eigenschaften, hohe Festigkeit und Verschleißfestigkeit.
4. MIM bietet engere Toleranzen und kann eine Genauigkeit von 0,3 mm erreichen.
5. Bei MIM entsteht praktisch kein Abfall, da das gesamte Material direkt in die Form gespritzt wird.
Nachteile von MIM gegenüber Druckguss
1. MIM ist aufgrund der komplexen Werkzeuge und mehrerer Verarbeitungsschritte im Allgemeinen teurer als Druckguss.
2. MIM hat eine geringere Lebensdauer der Form (150.000–300.000 Schuss) als Druckguss (über 1 Million Schuss).
3. MIM-Teile können beim Sintern erheblich schrumpfen (bis zu 30%), was eine sorgfältige Formgestaltung erfordert. Beim Druckguss ist die Schrumpfung viel geringer.
4. MIM ist mit hohen anfänglichen Automatisierungs- und Einrichtungskosten verbunden.
Vorteile des Druckgusses gegenüber MIM
1. Druckguss ist normalerweise billiger als MIM, in manchen Fällen bis zu 30% weniger.
2. Druckguss hat eine längere Lebensdauer der Form (über 1 Million Schuss) im Vergleich zu MIM (150.000 – 300.000 Schuss).
3. Beim Druckgießen sind nach dem Auswerfen des Teils aus der Form keine weiteren Arbeitsschritte erforderlich.
4. Beim Druckguss können Einsätze und Teile aus anderen Materialien in das Gussstück eingebettet werden.
Nachteile des Druckgusses im Vergleich zu MIM
1. Beim Druckguss ist die Herstellung kleiner, komplexer Teile mit feinen Strukturen und dünnen Wänden schwierig.
2. Druckguss ist hauptsächlich auf Nichteisenmetalle beschränkt. Eisenmetalle haben sehr hohe Schmelzpunkte, die die Lebensdauer der Form verkürzen.
3. Beim Druckguss ist Porosität aufgrund eingeschlossener Gase ein häufiges Problem und verringert die mechanische Festigkeit.
4. Beim Druckguss werden teure Formen benötigt, die dem hohen Druck und den Temperaturen des geschmolzenen Metalls standhalten.
Zusammenfassend lässt sich sagen, dass sich MIM hervorragend für die Herstellung kleiner, komplexer Teile mit hervorragenden mechanischen Eigenschaften aus einer Vielzahl von Materialien eignet. Es ist jedoch teurer und hat eine längere Zykluszeit als Druckguss. Druckguss ist wirtschaftlicher und eignet sich für einfachere, größere Teile aus Nichteisenmetallen mit schnelleren Produktionszeiten, hat jedoch Probleme mit komplizierten Merkmalen und Porosität.
Vergleich: Metallspritzguss vs. Druckguss
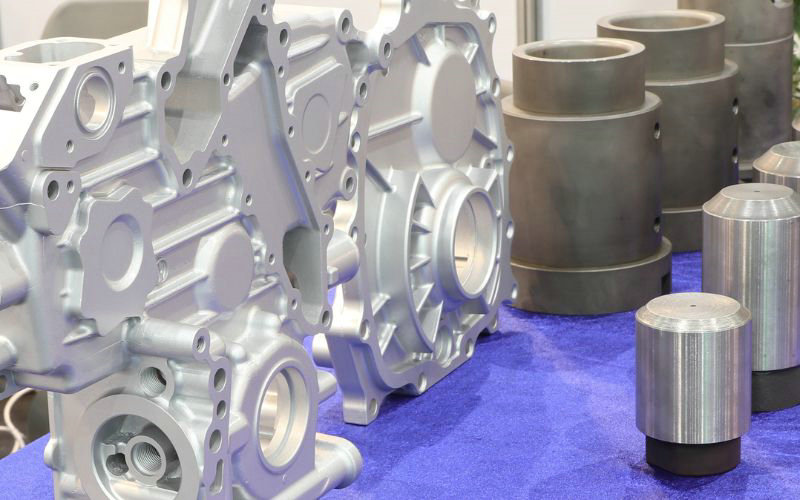
1. Genauigkeit und Toleranzen
Metallspritzguss (MIM): Mit MIM lassen sich sehr präzise Teile mit relativ engen Toleranzen herstellen, die normalerweise auf 0,3 mm genau sind. Diese Präzision ist auf die verwendeten feinen Metallpulver zurückzuführen, die detaillierte und komplexe Geometrien ermöglichen.
Druckguss: Druckguss bietet im Allgemeinen eine gute Maßgenauigkeit, die jedoch nicht so hoch ist wie bei MIM. Die typische Toleranz beim Druckguss liegt bei etwa ±0,0005 Zoll, was im Vergleich zu den Möglichkeiten von MIM weniger präzise ist. Maßabweichungen erfordern häufig zusätzliches Zuschneiden, um die Spezifikationen zu erfüllen.
2. Benötigte Materialien
Metallspritzguss (MIM): MIM kann eine breite Palette von Materialien verwenden, darunter Eisen- und Nichteisenmetalle, rostfreie Stähle, Titan und Nickellegierungen. Diese Vielseitigkeit ermöglicht die Herstellung von Teilen mit spezifischen Eigenschaften, die auf verschiedene Anwendungen zugeschnitten sind.
Druckguss: Verwendet werden hauptsächlich Nichteisenmetalle wie Aluminium, Zink und Magnesium. Beim Druckguss können zwar auch Eisenmetalle verwendet werden, diese Materialien haben jedoch einen sehr hohen Schmelzpunkt, was die Lebensdauer der Form erheblich verkürzen kann.
3. Geschwindigkeitsvergleich
Metallspritzguss (MIM): Der MIM-Prozess umfasst mehrere Schritte, darunter Mischen, Spritzgießen, Entbindern und Sintern, was ihn im Allgemeinen langsamer macht als Druckguss. Sobald die Produktion jedoch eingerichtet ist, kann MIM effizient große Mengen an Teilen produzieren.
Druckguss: Druckguss ist für seine schnelle Produktionsfähigkeit bekannt und ist schneller, was ihn besonders für die Produktion großer Stückzahlen geeignet macht. Das Verfahren ermöglicht dank seiner Hochdruck-Einspritztechnik die schnelle Herstellung großer Teile.
4. Oberflächenbeschaffenheit
Metallspritzguss (MIM): Bietet normalerweise eine hochwertige Oberflächenbeschaffenheit, die häufig keine zusätzliche Nachbearbeitung erfordert. Der Sinterprozess trägt dazu bei, eine glatte Oberfläche zu erzielen.
Druckguss: Teile kommen normalerweise mit einer guten Oberflächenbeschaffenheit aus der Form, müssen aber möglicherweise überschüssiges Metall abschneiden. Die Oberflächenqualität wird im Vergleich zu MIM allgemein als mittelmäßig angesehen.
5. Herstellungskosten
Metallspritzguss (MIM): Während die anfänglichen Einrichtungs- und Werkzeugkosten hoch sein können, kann MIM aufgrund des geringeren Abfalls und des minimalen Nachbearbeitungsbedarfs für die Herstellung komplexer Teile in großen Mengen kostengünstig sein.
Druckguss: Im Allgemeinen günstiger in Bezug auf die Anschaffungskosten und kostengünstiger bei größeren Teilen und Massenproduktion. Bei hochkomplexen oder kleineren Teilen sinkt die Kosteneffizienz jedoch.
6. Schimmelunterschiede
Metallspritzguss (MIM): Formen, die bei MIM verwendet werden, können im Vergleich zu Druckgussformen weniger haltbar sein und halten normalerweise etwa 150.000 bis 300.000 Spritzvorgänge aus. MIM-Formen ermöglichen jedoch eine komplexere Teilegestaltung.
Druckguss: Formen sind so konzipiert, dass sie hohen Drücken und Temperaturen standhalten, was sie langlebiger macht und eine Lebenserwartung von über 1 Million Schüssen hat. Allerdings bieten sie im Vergleich zu MIM-Formen weniger Flexibilität hinsichtlich der Teilekomplexität.