Cea mai mare cantitate de matriță de injecție din plastic care poate fi injectată în timpul unui ciclu de turnare este cunoscută sub numele de dimensiunea împușcării. Peleții sunt introduși în butoi și ansamblul șurubului prin buncăr.
Folosind tehnica de turnare prin injecție, materialul topit este injectat în cavitatea matriței pentru a crea cantități mari de piese din plastic.
În procesul de turnare prin injecție a plasticului, materia primă este introdusă în butoi, se topește, iar plasticul este apoi injectat în cavitatea matriței pentru răcire și solidificare după ce matrița este închisă. În cele din urmă, matrița se deschide, iar componentele sunt expulzate.
Cum se calculează dimensiunea loviturii
Durata timpului de rezidență este influențată de dimensiunea împușcăturii și a țevii, ceea ce poate afecta și calitatea produsului final. Duratele lungi de rezidență și degradarea polimerului pot proveni de la dimensiuni mici ale împușcăturii care necesită o capacitate mică a țevii.
Dimensiunile mici de împușcare care ocupă mai puțin de 20% din capacitatea butoiului duc frecvent la timpi de rezidență prelungiți, care la rândul lor cauzează degradarea polimerului și controlul inadecvat al procesului.
Pe de altă parte, dimensiunile de împușcături mari și nivelurile de umplere a butoiului mai mari decât 50% pot provoca topirea neuniformă și recuperarea lentă a șurubului.
În plus, șuruburile mai mari au, de obicei, capacități mai mici de presiune din plastic. Dimensiunile mari de împușcare, care ocupă mai mult de 65% din capacitatea cilindrului, cauzează frecvent probleme de calitate a topiturii, cum ar fi netopirea, uniformitatea slabă a topiturii și timpii lungi de recuperare a șurubului.
Pentru a fi în siguranță, puteți lua în considerare plasarea unei comenzi cu două butoaie. Mai mult, matrițele pot fi folosite cu două butoaie. Când comandați un al doilea butoi cu noua mașină, puteți fi plăcut mulțumit de costul său ieftin. Butoaiele pot fi schimbate în mai puțin de 30 de minute cu specificațiile potrivite și un operator experimentat, chiar dacă butoiul este fierbinte.
Formula pentru dimensiunea mucegaiului în turnarea prin injecție
Cea mai simplă formulă pentru calcularea dimensiunii mucegaiului este:
Contracție + Volumul molid + Volumul produsului + Volumul canalului = Dimensiunea mucegaiului
Capacitatea tragerii mașinii de formule/Dimensiunea tragerii
Greutatea totală sau volumul pe care șurubul îl injectează în timpul unui ciclu de turnare este exprimată ca capacitate de împușcare a mașinii (g)/dimensiune de împușcare a mașinii (mm), cunoscută și sub denumirea de capacitatea de injecție a mașinii.
Calculele dvs. atunci când luați în considerare presiunea ar trebui să fie după cum urmează:
Cursa X Suprafața pistonului șurub = volumul de injecție
Forța de injecție/ suprafața pistonului șurub = presiunea de injecție
Prin urmare:
Volumul maxim de injecție pe unitate cubică X presiunea maximă de injecție (bar pe unitate cubică)/1000 = capacitatea de injectare a unității de injecție.
Calculele atunci când se utilizează greutatea șurubului și densitatea materialului ar trebui să fie după cum urmează:
Masa/densitate= volum
ᴨ*D2*Dimensiune fotografiere/4= Volum butoi/împușcare
Factori care afectează dimensiunea fotografiei produsului
Există mai mulți factori de care trebuie să luați în considerare atunci când calculați dimensiunea unei lovituri. Acești factori sunt după cum urmează:
- Trebuie să luați în considerare volumul molidului, volumul rulajului și volumul produsului în timp ce determinați dimensiunea dozei. Acest lucru se datorează faptului că polimerul trebuie să umple molidul, canalul și volumul produsului atunci când este injectat în matriță.
- O altă problemă importantă care afectează calculele pentru dimensiunea împușcăturii este contracția polimerului. Contracția rezultă din răcirea polimerului topit. Datorită densităților variate ale polimerilor, contracția mucegaiului variază.
- Tipul și cantitatea de aditivi ai unui polimer îi pot modifica densitatea și caracteristicile de curgere.
Acești factori vă pot ajuta să estimați dimensiunea loviturii, volumul și capacitatea butoiului.
Unitate de injecție
Scopul unității de injecție este de a topi materialul plastic în mod uniform înainte de a-l injecta în matriță la o presiune și debit predeterminate. Acestea sunt activități solicitante, deoarece fluoropolimerii au o conductivitate termică limitată, o căldură specifică ridicată și o vâscozitate ridicată la topire.
Din nou, au fost dezvoltate numeroase variante pentru a aborda problemele complexe aflate la îndemână. O clasificare generală a variațiilor poate fi făcută în patru concepte de unitate de injecție primară:
- Piston sau piston cu o singură treaptă
- Berbec cu două trepte
- Înșurubați cu o etapă
- Șurub/berbec cu două trepte
Deși încă există în mașini minuscule și în unele echipamente specializate, unitatea berbec cu o singură etapă este în esență învechită din cauza ineficienței sale în încălzire, amestecare și transmitere a presiunii. Beneficiază de simplitate și accesibilitate.
În plus, berbecul în două trepte este aproape învechit. Berbecul este încă un mixer și un încălzitor ineficient, în ciuda încercării de a-l îmbunătăți prin separarea operațiunilor de încălzire și debit de presiune.
Unitatea cu șurub/berbec în două etape separă în continuare rolurile fluxului și căldurii utilizând un berbec pentru injecție în loc de un șurub pentru amestecare și încălzire. Ideea este atrăgătoare, deoarece ambele sunt instrumente eficiente pentru sarcinile lor respective.
În plus, unitatea de injecție este adesea evaluată utilizând presiunea maximă de injecție și volumul de injecție disponibil. Cea mai mare presiune posibilă la capătul din aval al șurubului se numește presiune de injecție. Aceasta depinde de diametrul șurubului și de forța care îl împinge.
Cu toate acestea, asigurați-vă că nu o confundați cu presiunea din conducta hidraulică care acționează asupra cilindrului de injecție, care antrenează șurubul și nici nu trebuie interpretată ca presiunea necesară pentru umplerea cavităților matriței. Datorită pierderilor de presiune în sistemele de alimentare cu duză și matriță, aceasta este substanțial mai mică.
Principala serie de acțiuni a unității de injecție este următoarea:
- Materialul este încălzit și topit pe măsură ce șurubul se rotește, apoi transportat de-a lungul șuruburilor până la capătul din aval al șurubului. Duza cilindrica se inchide prin folosirea unei supape mecanice sau termice sau prin existenta unei turnari anterioare.
Până când s-a acumulat suficientă topitură pentru a fabrica următoarea turnare, topitura colectoare forțează șurubul care se rotește înapoi împotriva unei rezistențe controlate (contrapresiunea). Rotirea șurubului se oprește aici. Este timpul să fiți pregătiți pentru topire.
- Când duza cilindrului este deschisă, șurubul se deplasează înainte într-o direcție axială fără să se rotească, acționând ca un berbec. Ca urmare, topitura adunată în fața capătului din aval al șurubului este forțată (injectată) prin duză și în matriță.
Pentru a opri curgerea topiturii înapoi în josul șurubului, poate fi instalat un sistem de supape la capătul din aval al șurubului. Aceasta este etapa de injecție sau de umplere a matriței.
- După ce matrița a fost umplută, presiunea șurubului este menținută pentru o perioadă scurtă de timp pentru a compensa contracția volumetrică a topiturii de răcire în interiorul matriței. Faza de ambalare sau de păstrare este acum.
- În cele din urmă, se ajunge la faza de menținere, unde ciclul unității de injecție se reia cu rotirea șurubului și pregătirea topiturii în timp ce matrița este ținută închisă pentru a permite turnării să se răcească la temperatura de ejectare.
Există scăderi semnificative de presiune atunci când topitura de plastic este forțată în duza de injecție și, ulterior, prin sistemul de alimentare a matriței și cavități. Reguli simple nu pot fi folosite pentru a calcula aceste pierderi de presiune.
Unitate de prindere
Închiderea matriței este menținută împotriva forțelor create atunci când plasticul este împins într-o matriță închisă prin presiune de injecție folosind o unitate de prindere pentru un IMM. Are un sistem de antrenare care poate deplasa placa mobilă a mașinii de turnat prin injecție în cel puțin o direcție.
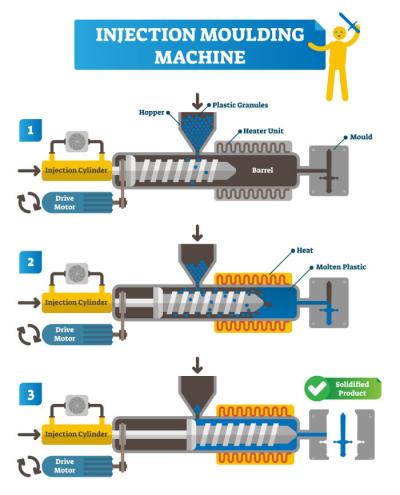
Tipuri de unități de prindere
Există mai multe tipuri de unități de prindere în procesul de turnare prin injecție. Acestea sunt după cum urmează:
Comutați prindere tip
Un dispozitiv mecanic care amplifică forța este o comutare. Două bare sunt conectate și se termină cu un pivot într-o mașină de turnat. Un capăt al barei este conectat la o plată fixă, în timp ce celălalt este conectat la o plată mobilă. Comutatorul are o formă în formă de V când matrița este deschisă. Cele două bare formează o linie dreaptă când se aplică presiune asupra pivotului.
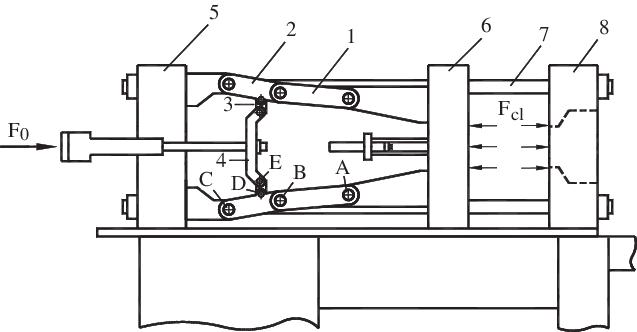
Avantajele strângerii tip basculă includ faptul că necesită mai puțini bani și cai putere și oferă un plan pozitiv al matriței. În plus, dezavantajele strângerii tip basculă sunt că necesită întreținere ridicată și este dificil de realizat.
Prindere hidraulică
În acest caz, RAM-ul sistemului hidraulic este legat de placa mobilă, iar o unitate de prindere alimentată de un cilindru hidraulic este conectată direct la matrița mobilă închisă. Cilindrul hidraulic are două secțiuni: intrarea uleiului și ieșirea.
Uleiul împinge RAM înainte când intră în cilindru sub presiune, determinând închiderea plăcii în mișcare și a matriței. În plus, revenirea RAM și matrița sunt deschise atunci când uleiul este eliberat din cilindru.
Unele avantaje ale strângerii hidraulice includ controlul ușor al vitezei de strângere și al suportului în orice unghi, măsurarea simplă a forței de strângere, configurarea ușoară a modului și ajustarea forței de strângere și simplitatea sa în întreținere.
Dezavantajele acestui tip de prindere sunt că costă mai mult și este mai scump decât un sistem de comutare și o clemă de substantiv pozitiv.
Unitate de prindere de tip magnetic
Modulele magnetice din interiorul plăcilor sau plăcilor de prindere a matriței magnetice produc forța de strângere. Panoul de interfață poate controla strângerea matriței, schimbarea matriței și magnetizarea și demagnetizarea plăcilor.
Beneficiile acestei unități de prindere includ energia electrică necesară doar în timpul fazelor de magnetizare și demagnetizare, nu în timpul prinderii, măsurarea forței de prindere în timp real cu multe caracteristici de siguranță și întreținere gratuită.
Greutatea mucegaiului
Cantitatea de material injectată în matriță pentru a umple matrița, inclusiv sistemul de alimentare, este cunoscută sub denumirea de „greutate împușcare a matriței” sau „greutate împușcare a produsului”. Pe de altă parte, molidul, runnerul și greutatea porții sunt componentele greutății de împușcare. Distanța pe care o acoperă șurubul pentru a umple produsul, inclusiv sistemul de alimentare, este cunoscută sub numele de dimensiunea matriței/produsului.
Concluzie
Folosind tehnica de turnare prin injecție, plasticul brut este topit, injectat în matriță, lăsat să se răcească și să se solidifice, iar apoi obiectul finit este expulzat. Dimensiunea împușcăturii este crucială deoarece previne umplerea insuficientă cu polimeri și flash-ul. Alți factori, cum ar fi capacitatea butoiului, afectează și procesul general de turnare prin injecție.