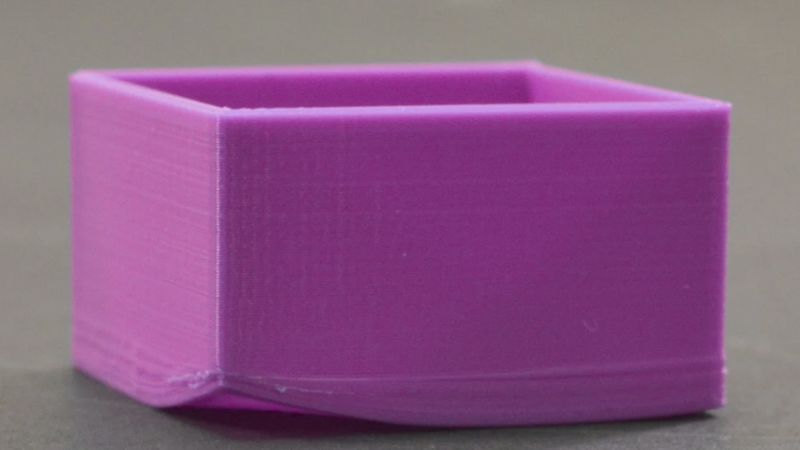
Odkształcenia mogą być irytujące. Zarówno dla producentów, jak i projektantów produktów ważne jest zrozumienie przyczyn powstawania odkształceń, a wdrażanie skutecznych strategii zapobiegania jest kluczowe dla utrzymania wysokiej jakości wyników i minimalizacji kosztów produkcji.
W tym kompleksowym przewodniku przyjrzymy się głównym czynnikom przyczyniającym się do odkształceń w procesie formowania wtryskowego i przedstawimy praktyczne rozwiązania pozwalające złagodzić ten problem.
Dzięki zastosowaniu tych spostrzeżeń producenci mogą zwiększyć wydajność produkcji, zmniejszyć liczbę braków i ostatecznie dostarczać lepsze części formowane wtryskowo.
Czym jest deformacja formy?
Odkształcenia stanowią jeden z najistotniejszych problemów jakościowych w procesie formowania wtryskowego tworzyw sztucznych, często prowadzący do niestabilności wymiarowej części z tworzyw sztucznych.
Odkształcenie odnosi się do niepożądanego odchylenia od zamierzonej geometrii produktu, które może wystąpić w częściach z tworzyw sztucznych podczas procesu formowania wtryskowego. Ta wada objawia się jako zniekształcenia, takie jak skręcanie, zginanie lub zwijanie się formowanej części.
Skala odkształceń waha się od niewielkich deformacji, ledwo zauważalnych gołym okiem, do znacznych zniekształceń, które zakłócają działanie części lub jej montaż.
Wpływ odkształceń na produkty formowane
Obecność odkształceń podczas formowania wtryskowego ma istotny wpływ na jakość i funkcjonalność części z tworzyw sztucznych:
- Jakość estetyczna:Atrakcyjność wizualna ulega pogorszeniu, co sprawia, że produkty końcowe są mniej konkurencyjne na rynku.
- Stabilność wymiarowa:Zniekształcone części mogą nie pasować do zespołów lub nie spełniać precyzyjnych wymiarów wymaganych do połączenia z innymi komponentami.
- Niedobory funkcjonalne:Oprócz kwestii estetycznych, odkształcenia mogą pogorszyć parametry mechaniczne i integralność strukturalną komponentu.
Jaka jest przyczyna powstawania odkształceń podczas formowania wtryskowego?
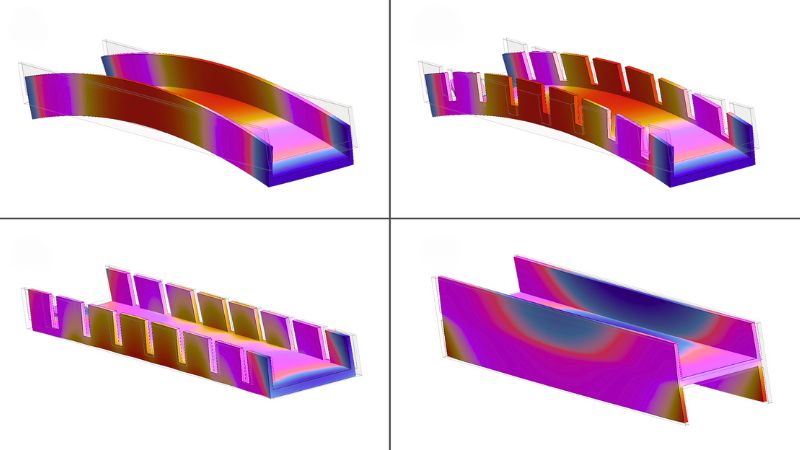
W tej sekcji przyjrzymy się zawiłościom maszyna, forma, I czynniki materialne przyczyniając się do powstawania odkształceń i przedstawia praktyczne rozwiązania łagodzące te problemy.
Błędy maszynowe
Niewystarczające ciśnienie lub czas wtrysku
Niewystarczające ciśnienie wtrysku lub czas przetrzymywania mogą prowadzić do niewystarczającego wypełnienia formy. Może to spowodować ochłodzenie i zestalenie się materiału z tworzywa sztucznego przed prawidłowym wypełnieniem formy.
Oba scenariusze skutkują niekontrolowanym ruchem cząsteczek podczas chłodzenia, co prowadzi do nierównomiernego kurczenia się i odkształcania.
Nieprawidłowa temperatura lufy
Jeśli temperatura cylindra jest zbyt niska, żywica nie osiągnie właściwej temperatury przepływu, co prowadzi do przedwczesnego zestalenia, nieodpowiedniego wypełnienia formy i ostatecznie do nierównomiernego skurczu i odkształceń.
Niewłaściwy czas przebywania
Niewystarczający czas przebywania uniemożliwia równomierne wchłanianie ciepła w całej żywicy. Może to spowodować, że niedogrzane części materiału staną się sztywne i przedwcześnie zestalą się, co doprowadzi do niepełnego wypełnienia formy i odkształcenia.
Nadmierne obciążenie wewnętrzne
Wysokie ciśnienie wtrysku może powodować powstawanie naprężeń wewnętrznych w uformowanej części, co może objawiać się deformacją po wyjęciu z formy.
Nieprawidłowy czas dokręcania śruby
Jeżeli czas przesuwania ślimaka jest zbyt długi, może to doprowadzić do nadmiernego upakowania formy, co z kolei może powodować naprężenia wewnętrzne, które z kolei prowadzą do odkształceń.
Niewystarczający czas chłodzenia
Niewystarczający czas chłodzenia może uniemożliwić równomierne i całkowite schłodzenie części przed jej wyrzuceniem, co może prowadzić do nierównomiernego kurczenia się i odkształcania w miarę stygnięcia poza formą.
Błędy formy
Niewłaściwa lokalizacja i konstrukcja bramy
Nieprawidłowe umiejscowienie wlewu może prowadzić do nierównomiernego wypełnienia i upakowania wnęki formy. Powoduje to nierównomierny rozkład ciśnienia i szybkości chłodzenia, powodując odkształcenia.
Niewłaściwe umiejscowienie sworznia wyrzutnika
Źle umiejscowione lub niewystarczające kołki wyrzutnika mogą powodować nierównomierne naprężenie podczas wyrzucania części z formy. Może to prowadzić do odkształceń, szczególnie w przypadku części o złożonej geometrii.
Niezrównoważone obwody chłodzące
Nieprawidłowo wyważone obwody chłodzące mogą powodować nierównomierne chłodzenie poszczególnych komór, co może prowadzić do odkształceń niektórych części, podczas gdy inne pozostaną nienaruszone.
Błędy w doborze materiałów
Wysokie wskaźniki skurczu
Materiały o dużym współczynniku kurczliwości są bardziej podatne na odkształcenia.
Na przykład polimery półkrystaliczne, takie jak polietylen (PE) i polipropylen (PP), charakteryzują się większym współczynnikiem skurczu w porównaniu do polimerów amorficznych, takich jak poliwęglan (PC) lub polistyren (PS).
Niespójny skurcz
Niektóre materiały kurczą się inaczej w kierunku przepływu niż w kierunku przepływu poprzecznego. To anizotropowe kurczenie się może prowadzić do odkształceń, szczególnie w częściach o długich ścieżkach przepływu.
Krystaliczność
Materiały o wysokiej strukturze krystalicznej są bardziej podatne na odkształcenia ze względu na tendencję do kurczenia się podczas chłodzenia.
Wrażliwość na wilgoć
Niektóre materiały, takie jak nylon, są higroskopijne i mogą absorbować wilgoć z powietrza. Może to prowadzić do niespójnych wyników formowania i potencjalnych odkształceń, jeśli nie zostaną odpowiednio wysuszone przed przetworzeniem.
Jak ograniczyć odkształcenia podczas formowania wtryskowego?
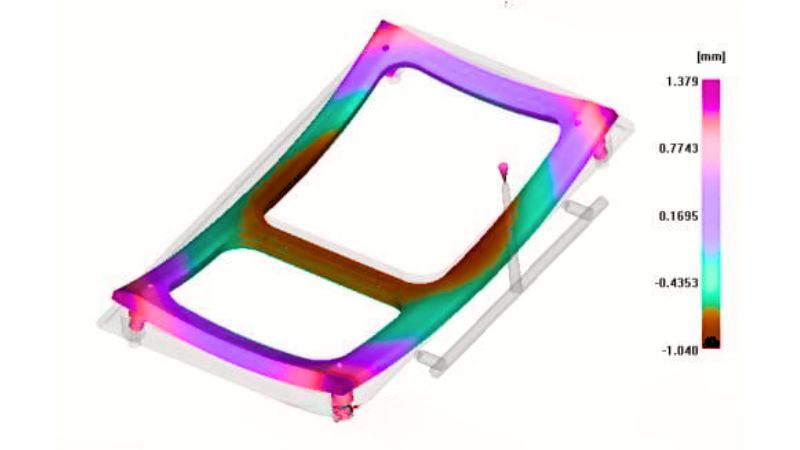
Optymalizacja parametrów przetwarzania jest kluczowa, zaczynając od dostosowania ciśnienia wtrysku i czasu przetrzymywania, aby zapewnić właściwe upakowanie wnęki formy. Ogranicza to cząsteczki plastiku i zapobiega niekontrolowanemu ruchowi podczas chłodzenia.
Wydłużenie czasu chłodzenia pozwala na całkowite i równomierne schłodzenie, co pomaga zapobiegać różnicom w szybkości skurczu, które często prowadzą do odkształceń.
Równie ważne jest precyzyjne ustawienie temperatury; podniesienie temperatury cylindra zapewnia odpowiedni przepływ materiału, natomiast dostosowanie temperatury formy na podstawie zaleceń dostawcy żywicy sprzyja jednorodności.
Jeżeli jest to możliwe, zastosowanie kanałów chłodzenia konformalnego może jeszcze bardziej poprawić równomierne chłodzenie całej części.
Projektowanie form i rozważania na temat materiałów
Optymalizacja wlewów i kanałów wtryskowych poprzez zastosowanie odpowiednich typów wlewów dla konkretnych tworzyw sztucznych i konstrukcji produktu, zastosowanie wielu wlewów dla części płaskich oraz poszerzenie wlewów i kanałów wtryskowych może znacząco poprawić napełnianie formy.
Właściwe umiejscowienie sworznia wyrzutnika ma również ogromne znaczenie. Należy upewnić się, że są one wystarczająco szerokie, dobrze rozmieszczone i umieszczone blisko miejsc o największym oporze wyrzutnika, co pozwoli zapobiec odkształceniom podczas wyjmowania części.
Wybór materiału i obróbka są kluczowymi czynnikami. Wybór żywic mniej podatnych na odkształcenia, takich jak tworzywa amorficzne, takie jak poliwęglan i polistyren, zamiast tworzyw krystalicznych, może mieć istotne znaczenie.
W przypadku części z wkładkami metalowymi ich wstępne podgrzanie do temperatury około 100°C pozwala zniwelować różnice w skurczu metalu i tworzywa sztucznego, redukując naprężenia i potencjalne odkształcenia.
Optymalizacja projektu i kontrola jakości
Kolejnym krytycznym aspektem jest optymalizacja projektu części. Utrzymanie jednolitej grubości ścianek w całej części sprzyja równomiernemu chłodzeniu i kurczeniu, podczas gdy dodanie wzmacniających żeber może poprawić sztywność części i zmniejszyć tendencję do wypaczania.
Współpracuj z profesjonalistą — Moldie
Praca z Moldie może prowadzić do jakości i wydajności w procesie wtrysku formowanego plastiku. Posiadamy wiedzę specjalistyczną wymaganą do obsługi różnorodnego asortymentu materiałów plastikowych, zapewniając, że powstałe produkty plastikowe łączą trwałość z estetyką.
Moldie kładzie nacisk na precyzję w swoich technikach produkcyjnych. Nasze podejście obejmuje:
- Zaawansowana konstrukcja form:Poprzez optymalizację wielkości i kształtu wlewu Moldie pomaga utrzymać równomierny przepływ i chłodzenie, co skutkuje mniejszymi naprężeniami wewnętrznymi i mniejszymi odkształceniami.
- Wybór materiału:Ich wiedza na temat różnych tworzyw sztucznych pozwala na świadomy wybór materiału, dostosowanie właściwości do zamierzonego zastosowania i ograniczenie wad.
- Optymalizacja procesu:Mollie precyzyjnie reguluje temperaturę formy i szybkość chłodzenia, ponieważ zmienne te odgrywają kluczową rolę w produkcji wysokiej jakości komponentów bez odkształceń.
Wierzymy, że taka współpraca może znacząco podnieść standard produkowanych elementów z tworzyw sztucznych, co ostatecznie przełoży się na poprawę funkcjonalności i wyglądu produktu końcowego.