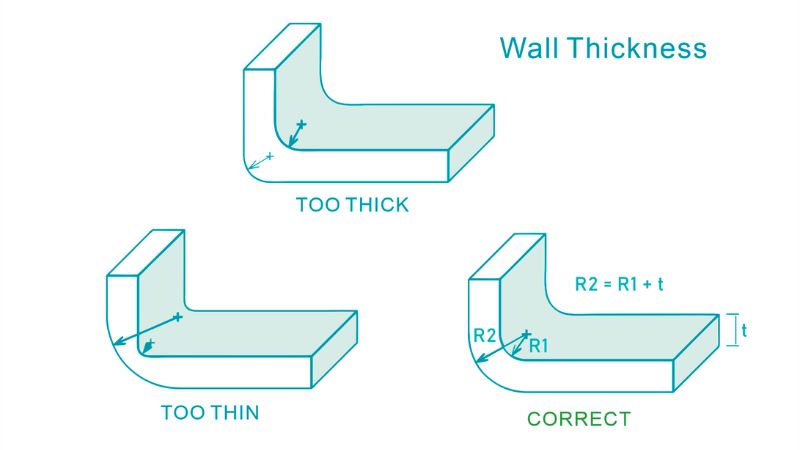
Od zrozumienia podstawowych zagadnień dotyczących grubości ścianek po poruszanie kwestii związanych z konkretnymi materiałami, ten przewodnik obejmuje istotne aspekty, które powinni znać projektanci, inżynierowie i producenci.
W tym kompleksowym przewodniku omówiono znaczenie prawidłowej grubości ścianek w procesie formowania wtryskowego, oferując informacje na temat najlepszych praktyk, typowych wyzwań i rozwiązań umożliwiających optymalizację produkcji części.
Jaka jest grubość ścianki w formowaniu wtryskowym
Grubość ścianki jest kluczowym czynnikiem projektowym w procesie formowania wtryskowego i oznacza grubość przekroju poprzecznego formowanej części z tworzywa sztucznego.
Jest to jeden z najważniejszych czynników branych pod uwagę przy projektowaniu metodą formowania wtryskowego, gdyż ma on znaczący wpływ na możliwość produkcji, koszt, jakość i wydajność finalnej części.
Co wpływa na grubość ścianki
Na grubość ścianek tworzyw sztucznych formowanych wtryskowo oraz strukturę części wpływają dwa główne czynniki.
- Rozmiar i kształt – Większe części zazwyczaj wymagają grubszych ścianek dla integralności strukturalnej, podczas gdy mniejsze części mogą mieć cieńsze ścianki. Złożone kształty mogą wymagać różnych grubości.
- Materiał plastikowy – – Różne tworzywa sztuczne mają różne charakterystyki przepływu i szybkości chłodzenia. Materiały o niższej lepkości lub wyższych szybkościach przepływu stopu można na ogół stosować z cieńszymi ściankami.
Poniżej znajduje się tabela, która pomoże Ci sprawdzić optymalną grubość ścianki dla różnych materiałów:
Materiał | Zalecany zakres grubości ścianki |
ABS | 0,045 – 0,140 cala (1,14 – 3,56 mm) |
Acetal (POM) | 0,030 – 0,120 cala (0,76 – 3,05 mm) |
Akryl (PMMA) | 0,025 – 0,500 cala (0,64 – 12,7 mm) |
Nylon (PA) | 0,030 – 0,115 cala (0,76 – 2,92 mm) |
Poliwęglan (PC) | 0,040 – 0,150 cala (1,02 – 3,81 mm) |
Polietylen (PE) | 0,030 – 0,200 cala (0,76 – 5,08 mm) |
Polipropylen (PP) | 0,025 – 0,150 cala (0,64 – 3,81 mm) |
Polistyren (PS) | 0,035 – 0,150 cala (0,89 – 3,81 mm) |
Jakie są problemy z grubością ścianek?
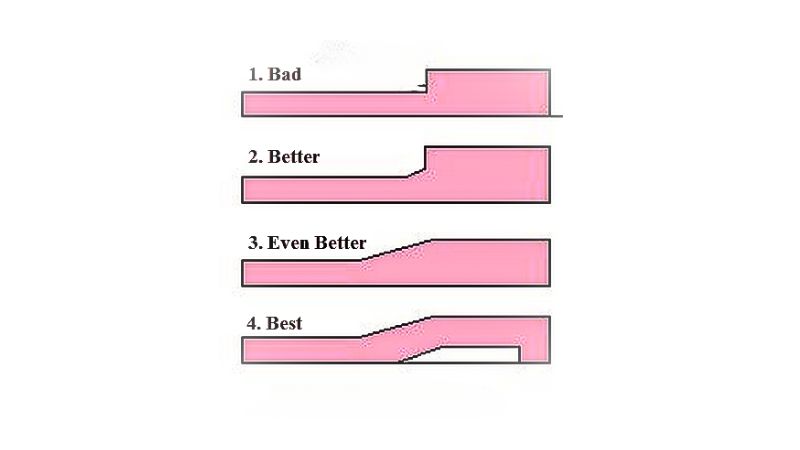
Nieprawidłowa grubość ścianki w przypadku formowania wtryskowego może prowadzić do szeregu wad w produkcie końcowym:
Wada | Przyczyna | Wynik |
Wypaczenie | Nierównomierna grubość ścianki | Różne szybkości chłodzenia prowadzą do naprężeń wewnętrznych, powodujących odkształcenia lub skręcanie. |
Ślady zlewu | Grubsze sekcje | Powolne chłodzenie pozwala powierzchni zapadać się do środka, tworząc małe zagłębienia |
Linie przepływu | Różnice w grubości ścianki | Różne szybkości przepływu stopionego plastiku powodują widoczne smugi lub linie na powierzchni |
Krótkie ujęcia | Przejścia od cienkich do grubych | Przedwczesne schłodzenie uniemożliwia całkowite wypełnienie grubszych obszarów |
Pustki | Grube sekcje | Uwięzienie powietrza lub kieszenie próżniowe tworzą wewnętrzne puste przestrzenie |
Odrzut | Zbyt cienkie ściany | Szybki przepływ tworzywa sztucznego powoduje powstawanie na powierzchni części wzorów przypominających węże |
Słabość konstrukcyjna | Nierównomierna grubość ścianki | Osłabia wytrzymałość i integralność części |
Niedokładności wymiarowe | Różnice w grubości | Nierównomierne chłodzenie powoduje, że części nie spełniają określonych wymiarów |
Zwiększone napięcie wewnętrzne | Różne grubości ścianek | Różne szybkości chłodzenia powodują większe naprężenia wewnętrzne |
Wady powierzchni | Niewłaściwa grubość ścianki | Powoduje niedoskonałości powierzchni, takie jak zmarszczki lub falistość |
Zagadnienia projektowe mające na celu uzyskanie jednolitej grubości ścianek
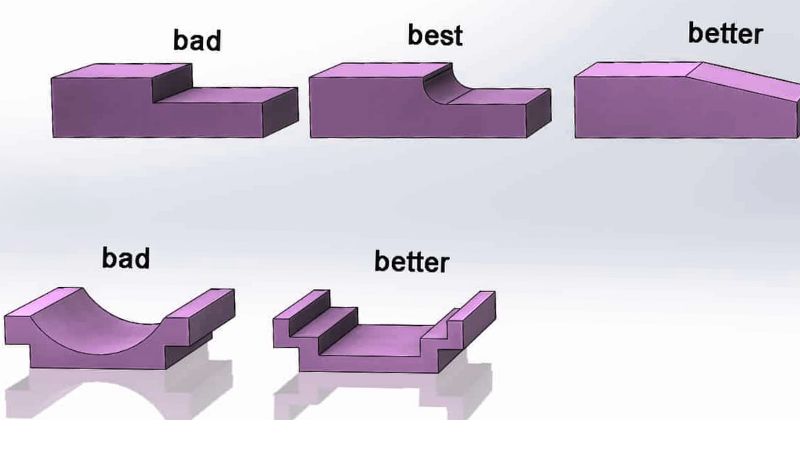
Analiza projektowania pod kątem możliwości produkcji (DFM) pomaga określić optymalną, jednorodną grubość, aby zminimalizować naprężenia wewnętrzne i poprawić spójność.
Wykorzystanie kątów pochylenia w celu poprawy wypełnienia formy
Kąty pochylenia są integralną częścią projektu elementów formowanych wtryskowo, służąc ułatwieniu uwalniania gotowej części z formy. Włączenie kąta pochylenia to nie tylko dobra praktyka; jest to kluczowe dla promowania jednolitej grubości ścianek.
Zalecany zewnętrzny kąt pochylenia wynoszący 0,5–1,5 stopnia i wewnętrzny kąt wynoszący 0,5 stopnia może znacznie usprawnić proces wypełniania formy.
Te niewielkie kąty pozwalają na płynniejszy przepływ materiału i zapobiegają powstawaniu nierównomiernej grubości ścianek, która często jest przyczyną różnych wad w danej części.
Rozwiązywanie problemów z naprężeniami wewnętrznymi spowodowanymi nierównomierną grubością ścianek
Różnice w grubości ścianek mogą prowadzić do naprężeń wewnętrznych w części podczas jej chłodzenia i krzepnięcia. Sekcje o grubszych ściankach stygną wolniej, powodując różnice w szybkościach kurczenia się, które mogą odkształcać lub deformować część.
Aby równomiernie rozłożyć naprężenia i zapobiec potencjalnym problemom z jakością, niezwykle ważne jest zachowanie jednakowej grubości całego elementu.
Projektując części, należy wziąć pod uwagę obszary o największym ryzyku i zastosować stałą grubość ścianek, aby ograniczyć powstawanie naprężeń wewnętrznych.
Zalecana grubość – minimalna
Minimalna grubość ścianki zależy od konkretnego rodzaju użytego tworzywa sztucznego i rozmiaru/złożoności części.
Zazwyczaj:
W przypadku małych części i wydajnej produkcji wielkoseryjnej zalecana jest minimalna grubość ścianki wynosząca 0,025–0,030 cala (0,64–0,76 mm).
W przypadku większych części zaleca się grubość co najmniej 0,040–0,050 cala (1,0–1,3 mm).
Praktyczna minimalna grubość ścianki w przypadku konwencjonalnego formowania wtryskowego wynosi 0,76–1,0 mm (0,030–0,040 cala).
Niektóre specjalistyczne metody formowania cienkościennego umożliwiają uzyskanie ścianek o grubości nawet 0,010 cala (0,25 mm), ale wymaga to wysokiego ciśnienia i ogranicza rozmiar części.
Zalecana grubość – maksymalna
W procesie formowania wtryskowego należy w miarę możliwości unikać stosowania zbyt grubych ścianek, ponieważ mogą one powodować wady i nieefektywność.
Ogólne wytyczne są następujące:
Większość formowanych wtryskowo części ma maksymalną grubość ścianki wynoszącą 3,2–6,4 mm (0,125–0,250 cala).
Ścianki o grubości większej niż 0,250 cala (6,4 mm) są bardziej narażone na występowanie zapadnięć, pustych przestrzeni, naprężeń szczątkowych i odkształceń.
W niektórych specjalistycznych zastosowaniach możliwa jest grubość ścianki do 4,5 cala (114 mm), ale wymaga to bardzo długich cykli obróbki.
Aby zapewnić najwyższą wydajność i jakość, w przypadku większości części zaleca się maksymalną grubość ścianki wynoszącą 3,2–4,0 mm (0,125–0,160 cala).
Jak rozwiązać problemy z grubością ścianek w formowanych częściach
Postępowanie z grubymi ściankami w częściach formowanych wtryskowo
Aby temu zaradzić, zaleca się utrzymanie grubości ścianki, która ułatwia szybkie chłodzenie, ale zapewnia również wystarczającą wytrzymałość. Na przykład przy materiale PA6 o grubości 8 mm całkowity cykl formowania wtryskowego wynosi około 93 sekund, a chłodzenie trwa około 70 sekund.
Aby pokonać wyzwanie wydłużonych cykli z powodu grubszych ścianek, korzystne może być zastosowanie techniki znanej jako core out. Polega ona na tworzeniu pustych sekcji w grubej ściance bez narażania integralności lub wytrzymałości części.
Jak radzić sobie z cienkimi ścianami bez narażania integralności części
Zaleca się, aby konstruktorzy produktów projektowali części o minimalnej grubości ścianek, bez narażania integralności części.
Projektowanie cieńszych ścianek wymaga gruntownego zrozumienia właściwości płynięcia materiału, aby zapobiec powstawaniu wad.
Czynniki takie jak ciśnienie wtrysku, temperatura formy i uwzględnienie elementów konstrukcyjnych, takich jak żebra lub wzmocnienia, mogą pomóc w podparciu elementów o cienkich ściankach, zwiększając ich podatność na formowanie i zmniejszając ryzyko wystąpienia odkształceń, zapadnięć lub pęcherzyków.