La più grande quantità di stampaggio a iniezione di plastica che può essere iniettata durante un ciclo di stampaggio è nota come dimensione del colpo. I pellet vengono immessi nella canna e nel gruppo coclea attraverso la tramoggia.
Utilizzando la tecnica dello stampaggio ad iniezione, il materiale fuso viene iniettato nella cavità dello stampo per creare grandi quantità di parti in plastica.
Nel processo di stampaggio ad iniezione della plastica, la materia prima viene introdotta nella canna, si scioglie e la plastica viene quindi iniettata nella cavità dello stampo per il raffreddamento e la solidificazione dopo che lo stampo è stato chiuso. Infine, lo stampo si apre e i componenti vengono espulsi.
Come calcolare la dimensione dello scatto
La durata dei tempi di permanenza è influenzata dalle dimensioni dei pallini e della canna, che possono influire anche sulla qualità del prodotto finale. Lunghe durate di permanenza e degradazione del polimero possono derivare da piccole dimensioni di stampaggio che richiedono una capacità del cilindro ridotta.
Piccole dimensioni di pallini che occupano meno di 20% della capacità del cilindro spesso comportano tempi di permanenza prolungati, che a loro volta causano il degrado del polimero e un controllo del processo inadeguato.
D'altra parte, grani di grandi dimensioni e livelli di riempimento della canna superiori a 50% possono causare una fusione non uniforme e un lento recupero della vite.
Inoltre, le viti più grandi in genere hanno capacità di pressione della plastica inferiori. I granuli di grandi dimensioni, che occupano più di 65% della capacità della canna, spesso causano problemi di qualità del fuso, come non fondere, scarsa uniformità del fuso e lunghi tempi di recupero della vite.
Per sicurezza, puoi considerare di effettuare un ordine a due barili. Ancora di più, gli stampi possono essere utilizzati con due botti. Quando ordini una seconda canna con la nuova macchina, puoi essere piacevolmente soddisfatto dal suo costo economico. Le botti possono essere cambiate in meno di 30 minuti con le giuste specifiche e un operatore esperto, anche se la canna è calda.
Formula per la dimensione del colpo dello stampo nello stampaggio ad iniezione
La formula più semplice per calcolare la dimensione del colpo dello stampo è:
Ritiro + Volume abete rosso + Volume prodotto + Volume canaletta = Dimensione stampata
Capacità di colpo della macchina da formula / dimensione del colpo
Il peso totale o il volume che la vite inietta durante un ciclo di stampaggio è espresso come capacità di iniezione della macchina (g)/dimensione dell'iniezione di macchina (mm), nota anche come capacità di iniezione della macchina.
I tuoi calcoli quando consideri la pressione dovrebbero essere i seguenti:
Corsa X Superficie pistone vite = volume iniezione
Forza di iniezione/superficie del pistone a vite = pressione di iniezione
Dunque:
Volume massimo di iniezione per unità cubica X pressione massima di iniezione (bar per unità cubica)/1000 = capacità di stampaggio dell'unità di iniezione.
I calcoli quando si utilizza il peso della vite e la densità del materiale dovrebbero essere i seguenti:
Massa/densità= volume
ᴨ*D2*Dimensione pallini/4= Canna/Volume colpi
Fattori che influenzano le dimensioni dello scatto del prodotto
Ci sono diversi fattori che devi considerare quando calcoli la dimensione dello scatto. Questi fattori sono i seguenti:
- È necessario considerare il volume dell'abete rosso, il volume del canaletto e il volume del prodotto mentre si determina la dimensione del colpo. Questo perché il polimero deve riempire l'abete rosso, il canale di scorrimento e il volume del prodotto quando viene iniettato nello stampo.
- Un altro problema importante che influisce sui calcoli per la dimensione della stampata è il restringimento del polimero. Il ritiro deriva dal raffreddamento del polimero fuso. A causa delle diverse densità dei polimeri, il ritiro dello stampo varia.
- Il tipo e la quantità di additivi di un polimero possono modificarne la densità e le caratteristiche di fluidità.
Questi fattori possono aiutarti a stimare la dimensione del colpo, il volume e la capacità della canna.
Unità di iniezione
Lo scopo del gruppo di iniezione è quello di fondere uniformemente il materiale plastico prima di iniettarlo nello stampo ad una pressione e portata prefissate. Si tratta di attività impegnative perché i fluoropolimeri hanno una conducibilità termica limitata, un elevato calore specifico e un'elevata viscosità del fuso.
Ancora una volta, sono state sviluppate numerose varianti per affrontare le complesse questioni a portata di mano. Una classificazione generale delle varianti può essere fatta in quattro concetti di unità di iniezione primaria:
- Stantuffo o pistone monostadio
- Ram a doppio stadio
- Vite con uno stadio
- Vite/pistone a due stadi
Sebbene esista ancora in minuscole macchine e in alcune apparecchiature specializzate, l'unità pistone monostadio è essenzialmente obsoleta a causa della sua inefficacia nel riscaldamento, nella miscelazione e nella trasmissione della pressione. Beneficia della semplicità e della convenienza.
Inoltre, il ram a due stadi è quasi obsoleto. Il pistone è ancora un miscelatore e riscaldatore inefficace nonostante il tentativo di migliorarlo separando le operazioni di riscaldamento e flusso di pressione.
L'unità vite/pistone a due stadi separa ulteriormente i ruoli di flusso e calore utilizzando un pistone per l'iniezione invece di una vite per la miscelazione e il riscaldamento. L'idea è allettante perché entrambi sono strumenti efficaci per i rispettivi compiti.
Inoltre, l'unità di iniezione viene spesso valutata utilizzando la pressione di iniezione massima e il volume di iniezione disponibile. La massima pressione possibile all'estremità a valle della vite è chiamata pressione di iniezione. Questo dipende dal diametro della vite e dalla forza che spinge contro di essa.
Attenzione però a non confonderla con la pressione della linea idraulica agente sul cilindro di iniezione, che aziona la vite, né va interpretata come la pressione necessaria per riempire le cavità dello stampo. A causa delle perdite di pressione negli ugelli e nei sistemi di alimentazione dello stampo, questo è sostanzialmente inferiore.
La serie principale di azioni del gruppo di iniezione è la seguente:
- Il materiale viene riscaldato e fuso mentre la vite gira, quindi trasportato lungo i voli della vite fino all'estremità a valle della vite. L'ugello della canna viene chiuso utilizzando una valvola meccanica o termica o l'esistenza di uno stampaggio precedente.
Fino a quando non si è accumulata una massa fusa sufficiente per produrre lo stampaggio successivo, la massa fusa che si raccoglie spinge indietro la vite ancora in rotazione contro una resistenza controllata (la contropressione). La rotazione della vite si ferma qui. È ora di essere pronti per lo scioglimento.
- Quando l'ugello della canna viene aperto, la vite avanza in direzione assiale senza ruotare, agendo come un pistone. Di conseguenza, il materiale fuso raccolto davanti all'estremità a valle della vite viene forzato (iniettato) attraverso l'ugello e nello stampo.
Per impedire al fuso di rifluire lungo i voli della vite, è possibile installare un sistema di valvole all'estremità a valle della vite. Questa è la fase di iniezione o riempimento dello stampo.
- Dopo che lo stampo è stato riempito, la pressione della vite viene mantenuta per un breve periodo per compensare il ritiro volumetrico del fuso di raffreddamento all'interno dello stampo. La fase di imballaggio o mantenimento è ora.
- Infine si passa alla fase di attesa, dove il ciclo del gruppo di iniezione riprende con la rotazione della vite e la preparazione dei fusi mentre lo stampo viene tenuto chiuso per permettere allo stampaggio di raffreddarsi fino alla temperatura di espulsione.
Si verificano perdite di carico significative quando la plastica fusa viene forzata nell'ugello di iniezione e successivamente attraverso il sistema di alimentazione dello stampo e le cavità. Non è possibile utilizzare regole semplici per calcolare queste perdite di carico.
Unità di bloccaggio
La chiusura dello stampo viene mantenuta contro le forze create quando la plastica viene spinta in uno stampo chiuso dalla pressione di iniezione utilizzando un'unità di bloccaggio per una IMM. Dispone di un sistema di azionamento in grado di spostare il piano mobile della pressa a iniezione in almeno una direzione.
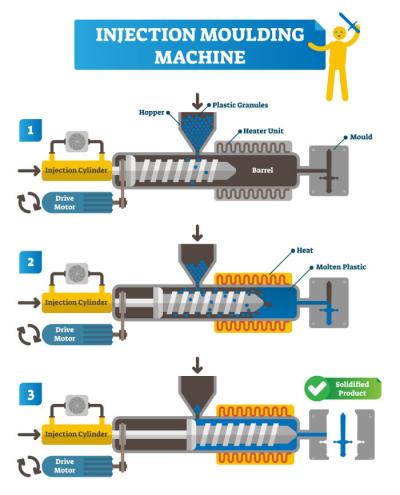
Tipi di unità di bloccaggio
Esistono diversi tipi di unità di chiusura nel processo di stampaggio a iniezione. Sono i seguenti:
Bloccaggio del tipo a ginocchiera
Un dispositivo meccanico che amplifica la forza è un interruttore. Due barre sono collegate e terminano con un perno in una formatrice. Un'estremità della barra è collegata ad un piano fisso, mentre l'altra è collegata ad un piano mobile. La levetta ha una forma a V quando lo stampo viene aperto. Le due barre formano una linea retta quando viene applicata pressione al perno.
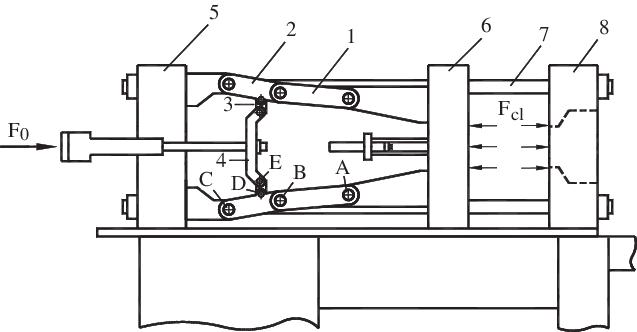
I vantaggi del bloccaggio a ginocchiera includono il fatto che richiede meno denaro e potenza e fornisce un piano positivo dello stampo. Inoltre, gli inconvenienti del bloccaggio del tipo a ginocchiera sono che richiede un'elevata manutenzione ed è difficile da eseguire.
Bloccaggio idraulico
In questo caso, il pistone dell'impianto idraulico è vincolato al piano mobile e un gruppo di chiusura azionato da un cilindro idraulico è collegato direttamente allo stampo mobile chiuso. Il cilindro idraulico ha due sezioni: l'ingresso dell'olio e l'uscita.
L'olio spinge il pistone in avanti quando entra nel cilindro sotto pressione, provocando la chiusura della piastra mobile e dello stampo. Inoltre, il ritorno della RAM e lo stampo sono aperti quando l'olio viene rilasciato dal cilindro.
Alcuni vantaggi del bloccaggio idraulico includono un facile controllo della velocità di bloccaggio e del supporto a qualsiasi angolazione, una semplice misurazione della forza di bloccaggio, una facile configurazione della modalità e regolazione della forza di bloccaggio e la sua semplicità di manutenzione.
Gli svantaggi di questo tipo di bloccaggio sono che costa di più ed è più costoso di un sistema a ginocchiera e di un morsetto a nome positivo.
Unità di bloccaggio di tipo magnetico
I moduli magnetici all'interno delle piastre o piani di bloccaggio dello stampo magnetico producono la forza di bloccaggio. Il pannello di interfaccia può controllare il bloccaggio dello stampo, il cambio dello stampo e la magnetizzazione e smagnetizzazione delle piastre.
I vantaggi di questa unità di bloccaggio includono l'elettricità richiesta solo durante le fasi di magnetizzazione e smagnetizzazione, non durante il bloccaggio, misurazione della forza di bloccaggio in tempo reale con molte caratteristiche di sicurezza e manutenzione gratuita.
Peso dello stampo
La quantità di materiale iniettato nello stampo per riempire lo stampo, compreso il sistema di alimentazione, è nota come "peso della stampata dello stampo" o "peso della stampata del prodotto". Il peso dell'abete rosso, del corridore e del cancello sono invece i componenti del peso del pallino. La distanza percorsa dalla vite per riempire il prodotto, compreso il sistema di alimentazione, è nota come dimensione della stampata stampo/prodotto.
Conclusione
Utilizzando la tecnica dello stampaggio ad iniezione, la plastica grezza viene fusa, iniettata nello stampo, lasciata raffreddare e solidificare, quindi l'oggetto finito viene espulso. La dimensione dello sparo è fondamentale perché previene il riempimento insufficiente e il bagliore del polimero. Altri fattori, come la capacità della canna, influenzano anche il processo generale di stampaggio a iniezione.