Lo stampaggio a iniezione è un processo di produzione ampiamente utilizzato per produrre parti in plastica iniettando materiale fuso in uno stampo. Il processo si basa su un componente critico chiamato punto di iniezione, che controlla il flusso della plastica fusa nella cavità dello stampo. Avere il giusto design del punto di iniezione è essenziale per il successo delle parti stampate a iniezione poiché ne influenza l'estetica, i tempi di ciclo e varie caratteristiche.
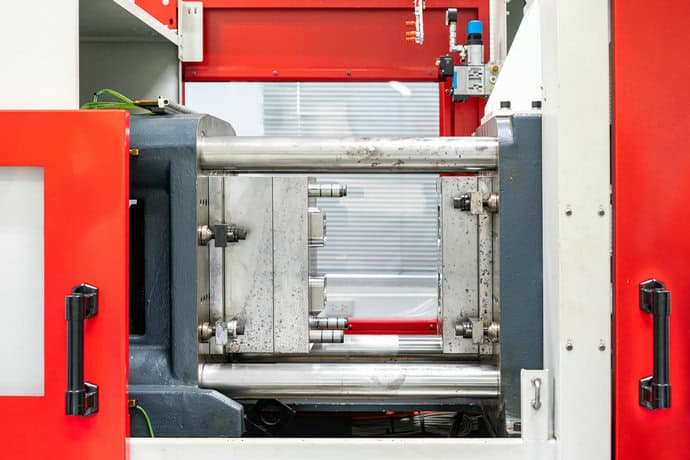
Nello stampaggio a iniezione, la plastica fusa scorre attraverso un'apertura appositamente progettata, spesso piccola, prima di entrare nella cavità dello stampo. Questo passaggio funge da percorso per il materiale fuso dall'ugello al nucleo dell'utensile. Il design del punto di iniezione deve adattarsi al progetto specifico per evitare potenziali difetti e garantire un prodotto finale di alta qualità.
Punti chiave
- Gli ingressi di stampaggio a iniezione controllano il flusso della plastica fusa nella cavità dello stampo, contribuendo al successo delle parti stampate.
- Il giusto design del cancello garantisce prodotti finali di alta qualità e riduce al minimo i potenziali difetti.
- Lo stampaggio a iniezione a iniezione influisce su vari aspetti di una parte, inclusi aspetti estetici, tempi di ciclo e caratteristiche specifiche.
Nozioni di base sullo stampaggio ad iniezione
Lo stampaggio a iniezione è un processo di produzione ampiamente utilizzato in cui un materiale, tipicamente plastica o resina, viene fuso e iniettato nella cavità dello stampo ad alta pressione. Il materiale si raffredda e solidifica all'interno dello stampo, assumendo la forma della cavità. Una volta che la parte si è sufficientemente raffreddata, viene espulsa dallo stampo e il processo viene ripetuto per la parte successiva.
Vengono utilizzati vari tipi di porte, come porte laterali, porte a disco o a diaframma, porte ad anello e porte a raggi. La scelta del tipo di punto di iniezione corretto dipende dalla geometria del pezzo, dall'applicazione e dalla concentricità richiesta.
Materiali svolgono un ruolo significativo nel processo di stampaggio a iniezione. I materiali comuni utilizzati in questo processo includono polimeri termoplastici, polimeri termoindurenti, elastomeri e in alcuni casi persino metalli. La scelta del materiale dipende da fattori quali la progettazione della parte, l'uso previsto e le proprietà del materiale quali robustezza, flessibilità e resistenza agli agenti chimici o al calore.
Il qualità della parte stampata è influenzata da diversi fattori, tra cui la progettazione dello stampo, la qualità del materiale utilizzato e i parametri di processo. Un'attenta considerazione di questi fattori può aiutare a garantire un risultato positivo, con parti che soddisfano le caratteristiche desiderate come precisione dimensionale, finitura superficiale e proprietà meccaniche.
Lo stampaggio a iniezione può essere adattato per soddisfare diverse esigenze di produzione utilizzando diversi processi, come stampaggio a coiniezione, stampaggio a iniezione con nucleo fusibile, stampaggio a iniezione assistita da gas e stampaggio a iniezione-compressione. Ciascun processo presenta vantaggi e limiti e la scelta dipende da fattori quali la complessità delle parti, i requisiti di materiale e i volumi di produzione.
In sintesi, lo stampaggio a iniezione è un processo di produzione versatile ed efficiente per la produzione di parti di vari materiali, utilizzando diversi tipi di punti di iniezione e processi adatti ad applicazioni specifiche. Comprendendo le nozioni di base dello stampaggio a iniezione, sarai meglio equipaggiato per prendere decisioni informate durante la progettazione e la produzione di parti con questo processo.
Componenti strutturali dello stampaggio ad iniezione
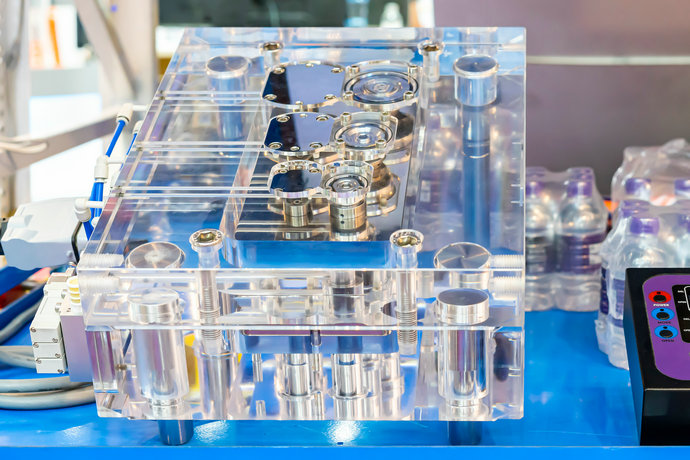
Quando si parla di stampaggio a iniezione, è fondamentale comprenderne chiaramente i componenti fondamentali. Questa sezione esplorerà i principali elementi strutturali, inclusi lo stampo, la cavità, il canale di colata, il canale e la cavità dello stampo.
Il muffa è fondamentale nel processo di stampaggio a iniezione, poiché modella il materiale plastico nella forma desiderata. Gli stampi possono avere cavità singole o multiple, a seconda della complessità e delle dimensioni del prodotto finale.
Il cavità è lo spazio all'interno dello stampo dove viene iniettato il materiale plastico fuso. È qui che il materiale plastico assume la forma del prodotto finale. Il numero di cavità in uno stampo influisce sulla velocità di produzione e sul costo complessivo.
Il canale di colata è il passaggio che collega l'ugello della pressa ad iniezione al sistema di canali. È responsabile del trasporto della plastica fusa nello stampo. È essenziale disporre di un canale di colata ben progettato per garantire un flusso adeguato e ridurre al minimo il rischio di difetti del materiale.
Corridori sono canali nello stampo che guidano la plastica fusa alle cavità dello stampo. Svolgono un ruolo cruciale nella distribuzione uniforme del materiale e nel mantenimento di una pressione costante durante tutto il processo di stampaggio. Il sistema di canali può essere progettato come canale caldo o freddo, ciascuno con vantaggi e svantaggi.
Il cavità dello stampo è dove il materiale plastico si solidifica e forma il prodotto finale. È fondamentale progettare la cavità dello stampo considerando le dimensioni, le tolleranze e le finiture superficiali desiderate del prodotto finale. Ciò influisce direttamente sulla qualità e sulle prestazioni del prodotto.
Acquisendo una solida conoscenza di questi componenti strutturali, è possibile garantire che il processo di stampaggio a iniezione sia accurato ed efficiente e si traduca in prodotti di alta qualità.
Comprendere la Porta
Nello stampaggio ad iniezione, cancelli sono componenti cruciali che garantiscono il corretto flusso della plastica fusa nella cavità dello stampo. Questi cancelli, aperture appositamente progettate, controllano il flusso, l'aspetto e il raffreddamento delle parti stampate a iniezione. Scegliere il corretto cancello di stampaggio ad iniezione è fondamentale per mantenere la qualità, la precisione e le prestazioni del prodotto finale.
Diversi tipi di punti di accesso da considerare per il tuo progetto di stampaggio a iniezione, ciascuno con vantaggi e applicazioni specifici. Comprendere questi diversi tipi di cancello è essenziale per selezionare l'opzione più adatta.
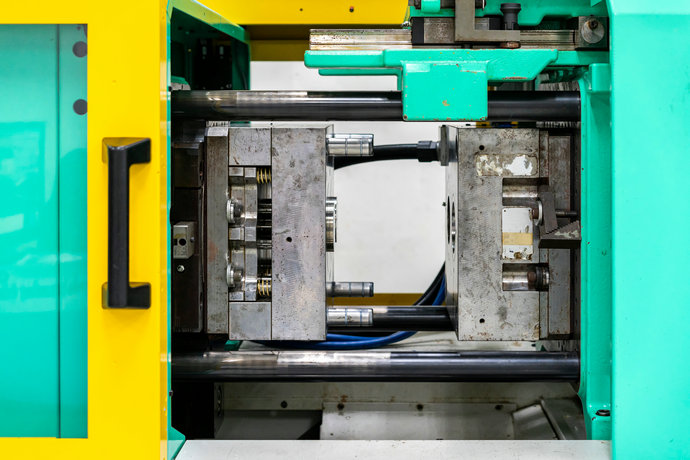
- Cancello di colata: Questo è il tipo di cancello più semplice, che collega il pezzo stampato direttamente all'ugello della macchina ad iniezione. Sebbene sia facile da progettare e utilizzare, può provocare stress elevati e potrebbe essere migliore per parti complesse o di grandi dimensioni a causa dello spreco di materiale.
- Porta sottomarina (nota anche come porta del tunnel): Questo tipo di cancello è progettato per tagliare automaticamente la parte stampata durante l'espulsione. Sono vantaggiosi per l'automazione e richiedono un lavoro post-stampaggio minimo, rendendoli ideali per la produzione in grandi volumi.
- Porta del ventilatore: Chiamato così per la sua forma a ventaglio, questo cancello consente una distribuzione più uniforme del materiale fuso, riducendo la probabilità di difetti delle parti.
- Cancello sul bordo: Posizionata sul bordo del pezzo stampato, questa porta garantisce un migliore flusso all'interno della cavità dello stampo ed è ideale per pezzi piatti e sottili.
- Cancello a schede: Simile a un punto di iniezione, questo tipo riduce la possibilità di fuoriuscita di materiale e viene spesso utilizzato per parti piatte e sottili che necessitano di un flusso più mirato.
- Porta a diaframma (porta anacardi): Questo cancello controlla il flusso del materiale dal centro di una parte stampata, consentendo un migliore controllo sul restringimento e sulla deformazione della parte. È comunemente usato per parti di precisione con geometrie complesse.
- Porta ad anello: Utilizzati nello stampaggio di parti a forma di tubo, i cancelli ad anello controllano il flusso del materiale attorno all'intera circonferenza della parte, fornendo una distribuzione uniforme.
Oltre a questi tipi di gate primari, ci sono sotto-porte (cancelli più piccoli utilizzati insieme a un cancello principale), otturatori a valvola, che aiutano a controllare il flusso attraverso mezzi più precisi, e cancelli a punta calda, che utilizzano un ugello riscaldato per applicazioni specializzate e di alta precisione.
Un ben selezionato sistema di cancelli E progetto è in grado di distinguere tra un progetto di stampaggio a iniezione di successo e uno afflitto da difetti dei componenti, sprechi di materiale e inefficienze. Comprendere questi tipi di punti di accesso e il loro potenziale impatto sulle parti stampate a iniezione ti consentirà di prendere decisioni informate e ottenere risultati ottimali.
Fattori che influenzano le prestazioni del cancello
Quando si lavora con lo stampaggio a iniezione del cancello, è essenziale considerare diversi fattori che possono influenzare le prestazioni del cancello. Prestando attenzione a questi fattori, potrete garantire la qualità dei vostri componenti stampati e ottimizzare l'efficacia del vostro processo.
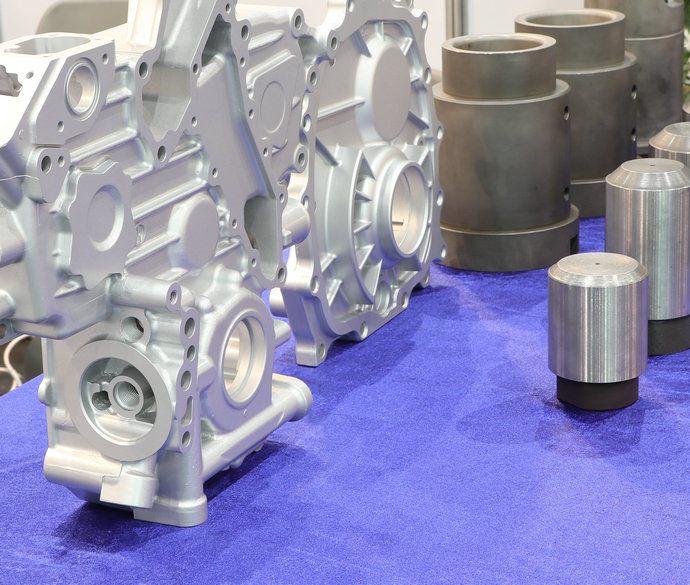
Controllo della pressione e della temperatura: Il controllo adeguato della pressione e della temperatura di iniezione è fondamentale, poiché questi parametri influenzano il flusso della plastica nello stampo. Trovare il giusto equilibrio tra questi due fattori è essenziale per ottenere un riempimento uniforme ed evitare difetti come deformazioni o avvallamenti.
Spessore e riempimento: Lo spessore del punto di iniezione gioca un ruolo cruciale nella rapidità e nell'uniformità con cui la plastica riempie la cavità dello stampo. Un cancello più spesso può comportare un riempimento più rapido ma può aumentare lo stress da taglio e potenziali danni alla parte in plastica. D'altro canto, un cancello più sottile può comportare un riempimento più lento e possibili colpi brevi.
Posizione del cono e del cancello: Anche il design del cancello può influire sul flusso della plastica. Un'apertura rastremata consente un flusso più fluido, che può aiutare a prevenire punti deboli o fratture nella parte finale. Inoltre, la scelta della giusta posizione del punto di iniezione è essenziale per ridurre al minimo i difetti come le bave dello stampaggio a iniezione o lo spessore irregolare.
Posizionamento del cancello: Il corretto posizionamento del punto di iniezione è fondamentale per garantire un buon flusso e un corretto riempimento della cavità dello stampo. Posizionare l'accesso in una posizione che consenta alla plastica di fluire attorno alle caratteristiche dello stampo può aiutare a evitare difetti e creare una parte più uniforme.
Resine a flusso rapido: L'utilizzo di resine a flusso rapido può migliorare l'efficienza del processo di stampaggio a iniezione riducendo il tempo di ciclo. Tuttavia, lavorare con resine a flusso rapido può richiedere un controllo più preciso di pressione, temperatura e altri parametri di processo per ottenere i risultati desiderati evitando difetti.
Considerando questi fattori, è possibile ottimizzare le prestazioni del processo di stampaggio a iniezione e ottenere componenti stampati di alta qualità. Trovare il giusto equilibrio tra pressione, temperatura, spessore del punto di iniezione e posizione è essenziale per il successo in questo settore produttivo specializzato.
Difetti del cancello e controllo di qualità
Nello stampaggio a iniezione, i difetti di accesso possono avere un impatto significativo sulla qualità del pezzo finito. Comprendere le varie problematiche relative al gate e implementare le opportune misure di controllo della qualità è fondamentale per ottenere un prodotto finale di alta qualità.
Un difetto comune del cancello è la presenza di vestigia. Le vestigia sono resti del cancello lasciati sul pezzo finito dopo la rifilatura, che possono essere antiestetici e influenzare negativamente l'aspetto finale. Per ridurre al minimo le tracce, assicurati che il tuo cancello sia tagliato in modo pulito e preciso. Anche la scelta del tipo di cancello giusto, come un cancello a punta calda o un cancello sottomarino, può aiutare a ridurre l'aspetto dei residui.
Il getto è un altro difetto dello stampaggio a iniezione talvolta associato alla progettazione del cancello. Il getto si verifica quando il materiale fuso viene proiettato nello stampo ad alta velocità, causandone la solidificazione prematura e causando imperfezioni o punti deboli nella parte finita. Regola la velocità di iniezione o modifica i canali di flusso all'interno del design del tuo cancello per risolvere i problemi di getto.
I tempi ciclo svolgono un ruolo cruciale nel controllo della qualità delle parti stampate a iniezione. Tempi di ciclo più lunghi possono portare a un aumento delle fratture da stress, mentre cicli più brevi possono comportare un riempimento incompleto, creando imperfezioni e influenzando negativamente la qualità delle parti. Il bilanciamento dei tempi di ciclo può aiutare a garantire che le parti soddisfino gli standard di qualità desiderati.
L'ispezione e il monitoraggio meticolosi del processo di stampaggio a iniezione possono aiutare a identificare tempestivamente i difetti legati al punto di iniezione, consentendo di risolverli tempestivamente e mantenere una qualità ottimale delle parti.
Inoltre, l'implementazione di vari metodi di controllo della qualità, come ispezioni visive, sistemi di ispezione automatizzati e test distruttivi e non distruttivi, fornirà preziose informazioni sull'efficacia della progettazione del cancello e del processo di stampaggio.
Domande frequenti
1. Quali sono i diversi tipi di punti di accesso nello stampaggio a iniezione?
Nello stampaggio a iniezione vengono utilizzati diversi tipi di cancelli, come cancelli diretti o di materozza, cancelli sui bordi, cancelli sottomarini e cancelli a ventola. Ciascun tipo presenta vantaggi e applicazioni unici, a seconda del design e dei requisiti del componente.
2. In che modo la progettazione del cancello influisce sul processo di stampaggio?
Il design del punto di iniezione svolge un ruolo cruciale nello stampaggio determinando il flusso di plastica fusa nella cavità dello stampo. Un cancello ben progettato garantisce un riempimento efficiente, riduce al minimo i difetti di stampaggio e riduce il tempo di ciclo. Diversi tipi di porte hanno vantaggi diversi, come promuovere un flusso più veloce, controllare i segni di avvallamento o consentire una migliore ventilazione.
3. Quali fattori determinano il posizionamento del punto di iniezione nello stampaggio a iniezione?
Diversi fattori influiscono sul posizionamento del punto di iniezione nello stampaggio a iniezione, tra cui la geometria della parte, la selezione del materiale e il percorso del flusso desiderato. In generale, il cancello dovrebbe essere posizionato in un'area che consenta un riempimento uniforme e una pressione minima del materiale, riducendo difetti e deformazioni. La posizione del punto di accesso dovrebbe inoltre ridurre al minimo lo stress sulle aree critiche e garantire che le linee di saldatura si trovino in sezioni non critiche.
4. Quali sono le principali funzioni dei cancelli nello stampaggio a iniezione?
I cancelli svolgono molteplici funzioni nello stampaggio a iniezione, come controllare il flusso di plastica fusa nella cavità dello stampo, garantire un riempimento adeguato e consentire alla plastica di solidificarsi a un ritmo ottimale. I cancelli hanno anche il compito di ridurre al minimo i difetti di stampaggio, come intrappolamenti d'aria, segni di avvallamento e colpi brevi, dirigendo la fusione della plastica in modo efficiente.
5. In che modo le dimensioni del cancello influenzano il prodotto finale?
Le dimensioni del cancello possono avere un impatto significativo sulla qualità e sull'aspetto del prodotto finale. Un cancello più piccolo in genere comporta una portata più lenta, riducendo il rischio di segni di avvallamento e deformazioni. Tuttavia, potrebbe anche aumentare la durata del ciclo e portare a un riempimento incompleto in scenari specifici. D'altro canto, un punto di accesso più grande consente un flusso più rapido e un riempimento più rapido dello stampo, ma può causare ulteriore stress o difetti all'interno della parte.
6. Quali sono i vantaggi dell'utilizzo dello stampaggio a iniezione con gate?
Lo stampaggio a iniezione con gate offre numerosi vantaggi, come un maggiore controllo sul flusso di plastica fusa, tempi di ciclo ridotti e difetti ridotti al minimo. La scelta del design e del posizionamento appropriati del punto di iniezione consente di ottimizzare il processo di stampaggio per produrre componenti di alta qualità con meno problemi. Inoltre, un sistema di colata adeguato può aiutare a ridurre gli sprechi di materiale e a migliorare l’efficienza complessiva della produzione.
Ordina da noi parti di iniezione in plastica di alta qualità
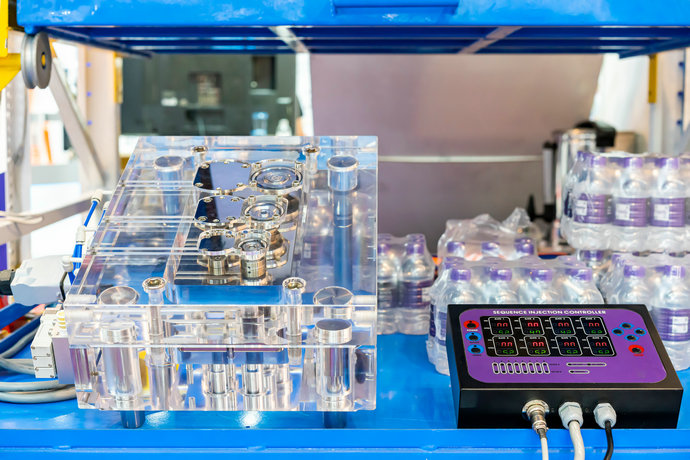
Vendiamo sfusi diversi tipi di parti in plastica per stampaggio a iniezione. Per ordinare è sufficiente inviarci un messaggio tramite il modulo di contatto cliente sul nostro sito web. Forniamo prodotti per lo stampaggio a iniezione di materie plastiche a livello globale e non vediamo l'ora di avviare un rapporto commerciale gratificante con la vostra azienda.