Le moulage par injection est un procédé de fabrication largement utilisé pour produire des pièces en plastique par injection de matière fondue dans un moule. Le processus repose sur un composant essentiel appelé porte, qui contrôle le flux de plastique fondu dans la cavité du moule. Avoir la bonne conception de porte est essentiel pour le succès de vos pièces moulées par injection, car cela affecte leur esthétique, leurs temps de cycle et leurs diverses caractéristiques.
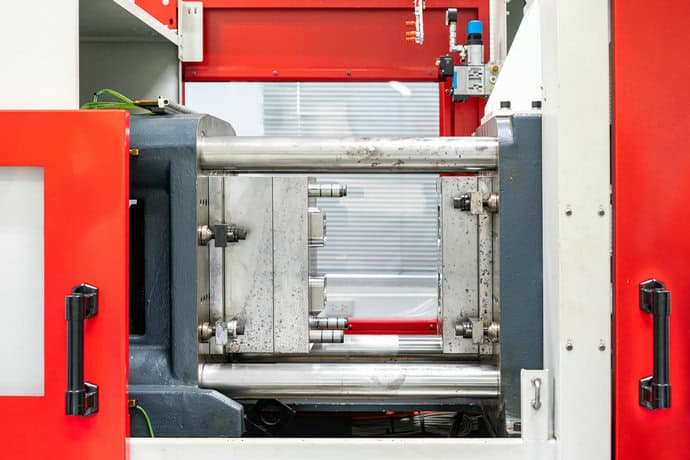
Dans le moulage par injection à porte, le plastique fondu s'écoule à travers une ouverture spécialement conçue, souvent petite, avant d'entrer dans la cavité du moule. Cette passerelle agit comme un chemin pour le matériau fondu depuis la buse jusqu'au cœur de l'outil. La conception de la porte d'injection doit être adaptée au projet spécifique pour éviter les défauts potentiels et garantir un produit final de haute qualité.
Points clés à retenir
- Les portes de moulage par injection contrôlent le flux de plastique fondu dans la cavité du moule, contribuant ainsi au succès des pièces moulées.
- La bonne conception de porte garantit des produits finaux de haute qualité et minimise les défauts potentiels.
- Le moulage par injection de porte a un impact sur divers aspects d'une pièce, notamment l'esthétique, les temps de cycle et les caractéristiques spécifiques.
Bases du moulage par injection
Le moulage par injection est un processus de fabrication largement utilisé dans lequel un matériau, généralement du plastique ou de la résine, est fondu et injecté dans une cavité de moule sous haute pression. Le matériau refroidit et se solidifie dans le moule, prenant la forme de la cavité. Une fois que la pièce a suffisamment refroidi, elle est éjectée du moule et le processus est répété pour la pièce suivante.
Différents types de portes sont utilisés, tels que les portes latérales, les portes à disque ou à diaphragme, les portes en anneau et les portes à rayons. Le choix du bon type de porte dépend de la géométrie de la pièce, de l'application et de la concentricité requise.
Matériaux jouent un rôle important dans le processus de moulage par injection. Les matériaux couramment utilisés dans ce processus comprennent les polymères thermoplastiques, les polymères thermodurcissables, les élastomères et même les métaux dans certains cas. Le choix du matériau dépend de facteurs tels que la conception de la pièce, l'utilisation prévue et les propriétés du matériau telles que la solidité, la flexibilité et la résistance aux produits chimiques ou à la chaleur.
La qualité La qualité de la pièce moulée est influencée par plusieurs facteurs, notamment la conception du moule, la qualité du matériau utilisé et les paramètres du processus. Un examen attentif de ces facteurs peut contribuer à garantir un résultat réussi, avec des pièces répondant aux caractéristiques souhaitées telles que la précision dimensionnelle, la finition de surface et les propriétés mécaniques.
Le moulage par injection peut être adapté à diverses exigences de fabrication en utilisant différents processus, tels que le moulage par co-injection, le moulage par injection de noyau fusible, le moulage par injection assisté par gaz et le moulage par injection-compression. Chaque processus présente des avantages et des limites, et le choix dépend de facteurs tels que la complexité des pièces, les exigences en matériaux et les volumes de production.
En résumé, le moulage par injection est un procédé de fabrication polyvalent et efficace permettant de produire des pièces à partir de divers matériaux, en utilisant différents types de portes et procédés adaptés à des applications spécifiques. En comprenant les bases du moulage par injection, vous serez mieux équipé pour prendre des décisions éclairées lors de la conception et de la fabrication de pièces avec ce processus.
Composants structurels du moulage par injection
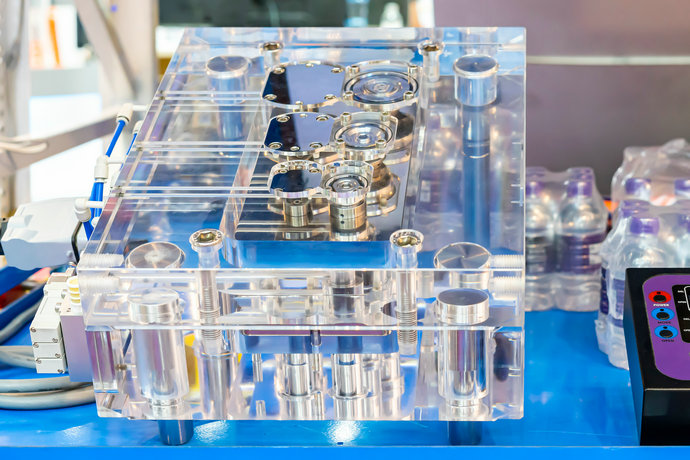
Lorsqu'il s'agit de moulage par injection, il est crucial de comprendre clairement ses composants fondamentaux. Cette section explorera les principaux éléments structurels, notamment le moule, la cavité, la carotte, le canal et la cavité du moule.
La mouler est essentiel dans le processus de moulage par injection, car il donne à la matière plastique la forme souhaitée. Les moules peuvent avoir une ou plusieurs cavités, selon la complexité et la taille du produit final.
La cavité est l'espace à l'intérieur du moule où la matière plastique fondue est injectée. C’est là que la matière plastique prend la forme du produit final. Le nombre de cavités dans un moule affecte la cadence de production et le coût global.
La sprue est le passage qui relie la buse de la machine de moulage par injection au système de glissières. Il est responsable du transport du plastique fondu dans le moule. Il est essentiel d'avoir une carotte bien conçue pour garantir un bon débit et minimiser le risque de défauts de matériaux.
Coureurs sont des canaux dans le moule qui guident le plastique fondu vers les cavités du moule. Ils jouent un rôle crucial dans la répartition uniforme du matériau et dans le maintien d’une pression constante tout au long du processus de moulage. Le système de canaux peut être conçu comme un canal chaud ou un canal froid, chacun présentant des avantages et des inconvénients.
La cavité du moule C'est là que la matière plastique se solidifie et forme le produit final. Il est essentiel de concevoir la cavité du moule en tenant compte des dimensions, tolérances et finitions de surface souhaitées pour le produit final. Cela affecte directement la qualité et les performances du produit.
En acquérant une solide compréhension de ces composants structurels, vous pouvez vous assurer que votre processus de moulage par injection est efficace, précis et aboutit à des produits de haute qualité.
Comprendre la porte
En moulage par injection, portes sont des composants cruciaux qui garantissent le bon écoulement du plastique fondu dans la cavité du moule. Ces portes, ouvertures spécialement conçues, contrôlent le débit, l’apparence et le refroidissement des pièces moulées par injection. Choisir le bon porte de moulage par injection est impératif pour maintenir la qualité, la précision et les performances de votre produit final.
Plusieurs types de portes à considérer pour votre projet de moulage par injection, chacune présentant des avantages et des applications spécifiques. Comprendre ces différents types de portails est essentiel pour sélectionner l’option la plus adaptée.
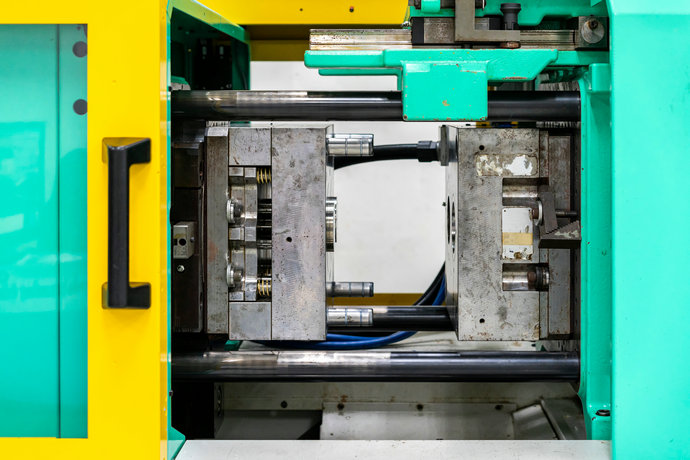
- Porte de coulée : Il s'agit du type de portillon le plus simple, qui relie la pièce moulée directement à la buse de la machine d'injection. Bien qu'il soit facile à concevoir et à utiliser, il peut entraîner des contraintes élevées et pourrait être meilleur pour les pièces complexes ou volumineuses en raison du gaspillage de matériaux.
- Porte sous-marine (également appelée porte du tunnel) : Ce type de porte est conçu pour cisailler automatiquement la pièce moulée lors de l'éjection. Ils sont avantageux pour l'automatisation et nécessitent un minimum de travail de post-moulage, ce qui les rend idéaux pour une production en grand volume.
- Accès pour les fans: Nommée pour sa forme en éventail, cette porte permet une répartition plus uniforme du matériau fondu, réduisant ainsi la probabilité de défauts des pièces.
- Porte de bord : Placée sur le bord de la pièce moulée, cette porte assure un meilleur écoulement à l'intérieur de la cavité du moule et est idéale pour les pièces plates et fines.
- Porte à onglets : Semblable à une porte de bord, ce type réduit le risque de fuite de matériau et est souvent utilisé pour les pièces plates et minces qui nécessitent un flux plus ciblé.
- Porte à diaphragme (porte en noix de cajou) : Cette porte contrôle le flux de matière depuis le centre d'une pièce moulée, permettant un meilleur contrôle du retrait et de la déformation de la pièce. Il est couramment utilisé pour les pièces de précision aux géométries complexes.
- Porte circulaire : Utilisées dans le moulage de pièces en forme de tube, les portes annulaires contrôlent le flux de matière sur toute la circonférence de la pièce, offrant ainsi une répartition uniforme.
En plus de ces types de portes principales, il existe sous-portes (portes plus petites utilisées conjointement avec une porte principale), vannes, qui aident à contrôler le flux par des moyens plus précis, et portes à pointe chaude, qui utilisent une buse chauffée pour des applications spécialisées de haute précision.
Un bien sélectionné système de portail et conception peut faire la distinction entre un projet de moulage par injection réussi et un autre en proie à des défauts de pièces, à des déchets de matériaux et à des inefficacités. Comprendre ces types de portes et leur impact potentiel sur vos pièces moulées par injection vous permettra de prendre des décisions éclairées et d'obtenir des résultats optimaux.
Facteurs influençant les performances du portail
Lorsque vous travaillez avec le moulage par injection de portail, il est essentiel de prendre en compte plusieurs facteurs qui peuvent influencer les performances du portail. En prêtant attention à ces facteurs, vous pouvez garantir la qualité de vos composants moulés et optimiser l’efficacité de votre processus.
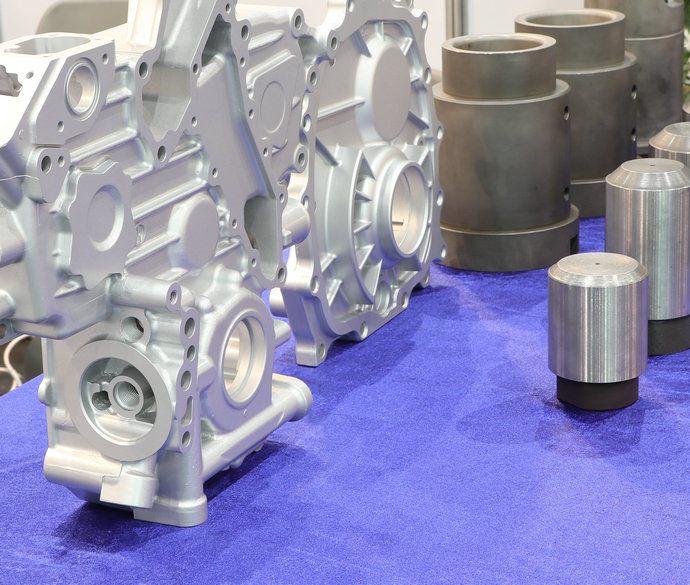
Contrôle de la pression et de la température : Un contrôle approprié de la pression et de la température d'injection est essentiel, car ces paramètres affectent l'écoulement du plastique dans le moule. Trouver le bon équilibre entre ces deux facteurs est essentiel pour obtenir un remplissage homogène et éviter les défauts tels que les déformations ou les traces d'affaissement.
Épaisseur et remplissage : L'épaisseur de la porte joue un rôle crucial dans la rapidité et l'uniformité du remplissage du plastique dans la cavité du moule. Une porte plus épaisse peut entraîner un remplissage plus rapide mais peut augmenter la contrainte de cisaillement et les dommages potentiels à la pièce en plastique. D’un autre côté, une porte plus fine peut entraîner un remplissage plus lent et d’éventuels tirs courts.
Emplacement du cône et de la porte : La conception du portail peut également avoir un impact sur le flux de plastique. Une porte conique permet un écoulement plus fluide, ce qui peut aider à prévenir les points faibles ou les fractures dans la pièce finale. De plus, le choix du bon emplacement de porte est essentiel pour minimiser les défauts tels que les bavures de moulage par injection ou les épaisseurs inégales.
Emplacement de la porte : Un placement correct des portes est essentiel pour garantir un bon écoulement et un remplissage correct de la cavité du moule. Placer la porte dans un endroit permettant au plastique de s'écouler autour des éléments du moule peut aider à éviter les défauts et à créer une pièce plus uniforme.
Résines à écoulement rapide : L'utilisation de résines à fluidité rapide peut améliorer l'efficacité du processus de moulage par injection en réduisant le temps de cycle. Cependant, travailler avec des résines à écoulement rapide peut nécessiter un contrôle plus précis de la pression, de la température et d'autres paramètres du processus pour obtenir les résultats souhaités tout en évitant les défauts.
En prenant en compte ces facteurs, vous pouvez optimiser les performances de votre processus de moulage par injection de grille et obtenir des composants moulés de haute qualité. Trouver le bon équilibre entre pression, température, épaisseur de porte et emplacement est essentiel pour réussir dans ce domaine de fabrication spécialisé.
Défauts de porte et contrôle qualité
Dans le moulage par injection, les défauts de seuil peuvent avoir un impact significatif sur la qualité de votre pièce finie. Comprendre les différents problèmes liés aux portes et mettre en œuvre les mesures de contrôle qualité appropriées sont essentiels pour obtenir un produit final de haute qualité.
Un défaut courant des portes est la présence de vestiges. Les vestiges sont des restes du portail laissés sur la pièce finie après le détourage, qui peuvent être inesthétiques et nuire à votre aspect final. Pour minimiser les vestiges, assurez-vous que votre portail est taillé proprement et avec précision. Choisir le bon type de porte, comme une pointe chaude ou une porte sous-marine, peut également contribuer à réduire l’apparence des vestiges.
Le jet est un autre défaut de moulage par injection parfois associé à la conception des portes. Le jet se produit lorsque du matériau en fusion pénètre dans le moule à des vitesses élevées, provoquant sa solidification prématurée et entraînant des imperfections ou des points faibles dans votre pièce finie. Ajustez la vitesse d'injection ou modifiez les canaux d'écoulement dans la conception de votre porte pour résoudre les problèmes de jet.
Les temps de cycle jouent un rôle crucial dans le contrôle de la qualité des pièces moulées par injection. Des temps de cycle plus longs peuvent entraîner une augmentation des fractures de contrainte, tandis que des cycles plus courts peuvent entraîner un remplissage incomplet, créant des imperfections et affectant négativement la qualité des pièces. Équilibrer vos temps de cycle peut vous aider à garantir que vos pièces répondent aux normes de qualité souhaitées.
Une inspection et une surveillance méticuleuses de votre processus de moulage par injection peuvent vous aider à identifier dès le début les défauts liés aux portes, vous permettant ainsi de les résoudre rapidement et de maintenir une qualité optimale des pièces.
En outre, la mise en œuvre de diverses méthodes de contrôle qualité, telles que des inspections visuelles, des systèmes d'inspection automatisés et des tests destructifs ou non destructifs, fournira des informations précieuses sur l'efficacité de la conception de votre portail et de votre processus de moulage.
Questions fréquemment posées
1. Quels sont les différents types de portes en moulage par injection ?
Plusieurs types de portes sont utilisés dans le moulage par injection, tels que les portes directes ou à carottes, les portes de bord, les portes sous-marines et les portes en éventail. Chaque type présente des avantages et des applications uniques, en fonction de la conception et des exigences du composant.
2. Quel est l’impact de la conception du portail sur le processus de moulage ?
La conception de la porte joue un rôle crucial dans le moulage en déterminant l'écoulement du plastique fondu dans la cavité du moule. Une porte bien conçue garantit un remplissage efficace, minimise les défauts de moulage et réduit le temps de cycle. Différents types de vannes présentent différents avantages, tels que favoriser un débit plus rapide, contrôler les traces d'évier ou permettre une meilleure ventilation.
3. Quels facteurs déterminent le placement des portes dans le moulage par injection ?
Plusieurs facteurs ont un impact sur le placement des portes dans le moulage par injection, notamment la géométrie de la pièce, la sélection des matériaux et le chemin d'écoulement souhaité. Généralement, la porte doit être placée dans une zone permettant un remplissage uniforme et une pression minimale du matériau, réduisant ainsi les défauts et les déformations. L'emplacement de la porte doit également minimiser les contraintes sur les zones critiques et garantir que toutes les lignes de soudure se trouvent dans des sections non critiques.
4. Quelles sont les principales fonctions des portes dans le moulage par injection ?
Les portes remplissent de multiples fonctions dans le moulage par injection, telles que contrôler le flux de plastique fondu vers la cavité du moule, garantir un remplissage correct et permettre au plastique de se solidifier à un rythme optimal. Les portes sont également chargées de minimiser les défauts de moulage, tels que les pièges à air, les marques d'évier et les projections courtes, en dirigeant efficacement la fonte du plastique.
5. Comment la taille du portail influence-t-elle le produit final ?
La taille du portail peut avoir un impact significatif sur la qualité et l’apparence du produit final. Une porte plus petite entraîne généralement un débit plus lent, réduisant ainsi le risque de traces d'évier et de déformation. Cependant, cela peut également augmenter la durée du cycle et conduire à un remplissage incomplet dans des scénarios spécifiques. D'un autre côté, une porte plus grande permet un écoulement et un remplissage du moule plus rapides, mais peut provoquer des contraintes supplémentaires ou des défauts au sein de la pièce.
6. Quels sont les avantages du moulage par injection à grille ?
Le moulage par injection à porte offre plusieurs avantages, tels qu'un contrôle accru du flux de plastique fondu, des temps de cycle réduits et une minimisation des défauts. Choisir la conception et le placement appropriés des portes vous permet d'optimiser votre processus de moulage afin de produire des composants de haute qualité avec moins de problèmes. De plus, un contrôle approprié peut contribuer à réduire le gaspillage de matériaux et à améliorer l’efficacité globale de la production.
Commandez chez nous des pièces d’injection plastique de haute qualité
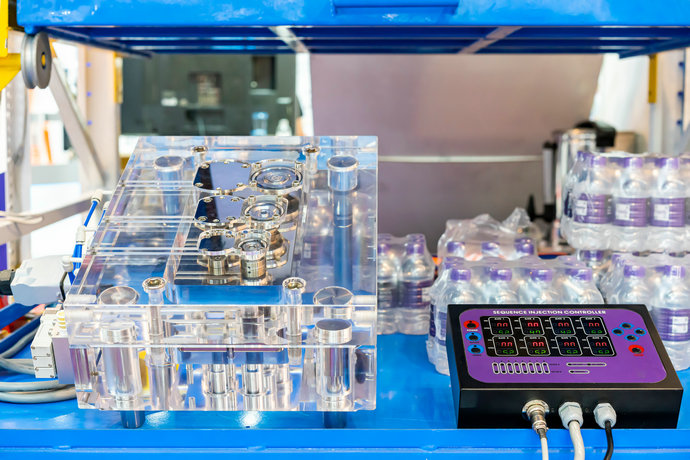
Nous vendons différents types de pièces en plastique moulées par injection en vrac. Pour commander, il vous suffit de nous envoyer un message via le formulaire de contact client de notre site internet. Nous livrons des produits de moulage par injection plastique dans le monde entier et sommes impatients de nouer une relation commerciale enrichissante avec votre entreprise.