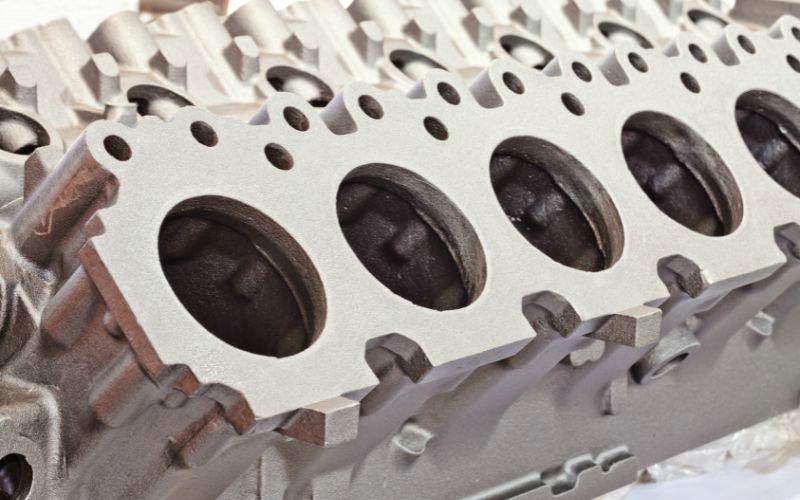
Qu’est-ce que le moulage sous pression ?
Le moulage sous pression est un processus de fabrication qui consiste à verser ou à injecter du métal en fusion dans des moules, appelé meurt. Le métal généralement utilisé dans ce processus peut inclure le zinc, l'aluminium et leurs alliages. Le vôtre est un voyage à travers une procédure largement adoptée pour son efficacité dans les séries de production à haut volume.
Lorsque vous lancez le moulage sous pression, le métal est fondu dans un four puis injecté dans les matrices sous haute pression. Cette méthode est populaire pour sa capacité à produire des pièces avec précision, des détails complexes et une excellente finition de surface, des qualités exigées dans des secteurs comme l'automobile, l'aérospatiale et l'électronique.
Le moulage sous pression est très recherché par les fabricants en raison de sa capacité à produire des pièces uniformes et de qualité constante. Que vous l'utilisiez pour créer des composants complexes de boîte de vitesses pour véhicules ou des boîtiers élégants et durables pour l'électronique, le moulage sous pression constitue un pilier de la fabrication moderne, en particulier lorsque la précision et le volume sont essentiels.
Processus de moulage sous pression
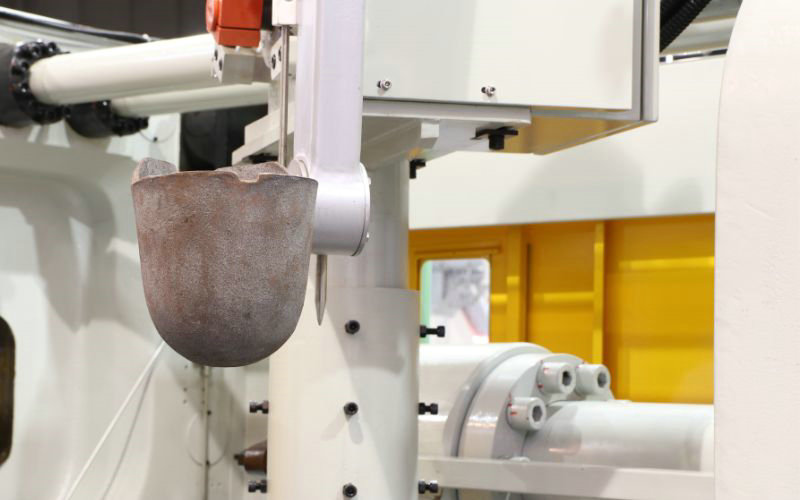
Il existe trois principaux types de procédés de moulage sous pression : le moulage sous pression par gravité, le moulage sous pression en chambre froide et le moulage sous pression en chambre chaude.
Moulage sous pression par gravité
Dans le moulage sous pression par gravité, le métal en fusion est versé directement d'une poche dans une filière semi-permanente ou permanente. La cavité se remplit sans autre force que la gravité. Les avantages du moulage sous pression par gravité incluent la capacité de produire des pièces moulées denses et de haute qualité avec d'excellentes propriétés mécaniques adaptées au traitement thermique. Il est rentable pour la production de petits et moyens volumes.
Moulage sous pression en chambre froide
Dans le moulage sous pression en chambre froide, le four de fusion est situé séparément de la machine de moulage sous pression. Pour chaque cycle, une quantité précise de métal en fusion est versée dans la chambre de tir non chauffée de la machine ; Ensuite, un piston hydraulique force le métal dans la matrice sous des pressions élevées comprises entre 2 000 et 20 000 psi. Le moulage sous pression en chambre froide est utilisé pour les alliages ayant des points de fusion plus élevés comme l’aluminium. Elle produit des pièces solides et durables, mais ses temps de cycle sont plus lents qu’une chambre chaude.
Moulage sous pression en chambre chaude
Dans le moulage sous pression en chambre chaude, le mécanisme d'injection est immergé dans un bain de métal en fusion, qui est introduit dans la matrice par un col de cygne et un piston. Au début de chaque cycle, le piston se rétracte, permettant au col de cygne de se remplir de métal en fusion. Le piston force ensuite le métal à travers le col de cygne dans la matrice à des pressions de 1 000 à 5 000 psi. Le moulage sous pression en chambre chaude est utilisé pour les alliages à bas points de fusion comme le zinc et le magnésium. Il permet des temps de cycle plus rapides et peut produire des pièces complexes avec une porosité réduite.
Applications de moulage sous pression
Automobile: Le moulage sous pression est largement utilisé dans le secteur automobile. Vous trouverez des composants tels que des blocs moteurs, des pièces de transmission et des éléments structurels fabriqués selon ce processus. La capacité de produire des pièces solides et durables rapidement et efficacement fait du moulage sous pression un choix incontournable pour les ingénieurs automobiles.
- Composants du moteur
- Boîtes de vitesses
- Cadres de voiture
Aérospatial: L'industrie aérospatiale valorise le moulage sous pression pour créer des pièces complexes qui nécessitent précision et peut résister à des conditions difficiles. Les composants tels que le train d'atterrissage, les instruments du cockpit et les pièces du moteur sont généralement moulés sous pression.
- Boîtiers d'instruments
- Pièces de train d'atterrissage
- Composants du moteur
Électronique: En électronique, le moulage sous pression est utilisé pour créer des éléments tels que des connecteurs, des boîtiers et des dissipateurs thermiques. Ces pièces bénéficient de la capacité du moulage sous pression à former des conceptions complexes avec un niveau élevé de conductivité thermique.
- Dissipateurs de chaleur
- Connecteurs
- Boîtiers
Qu’est-ce que le moulage par injection de métal ?
Le moulage par injection de métal (MIM) vous propose un processus de fabrication permettant de produire des pièces complexes en volumes moyens à élevés. MIM combine la liberté de conception et la complexité des formes du moulage par injection plastique avec la résistance et l'intégrité exceptionnelles du métal.
Voici un aperçu concis de MIM :
- Matériaux: Votre choix de matériaux dans le MIM comprend généralement des métaux ferreux tels que l'acier inoxydable, qui confèrent une résistance et une durabilité significatives au produit final.
- Force et précision: Les pièces MIM sont connues pour leur résistance et leur précision impressionnantes. Ils maintiennent des tolérances strictes, ce qui les rend adaptés à la fois industriel et médical applications.
- Géométries complexes et parois minces: Avec MIM, vous êtes en mesure de créer des pièces avec des géométries complexes et des parois minces, ce qui pourrait être difficile, voire impossible, avec les processus traditionnels de travail des métaux.
Processus de moulage par injection de métal
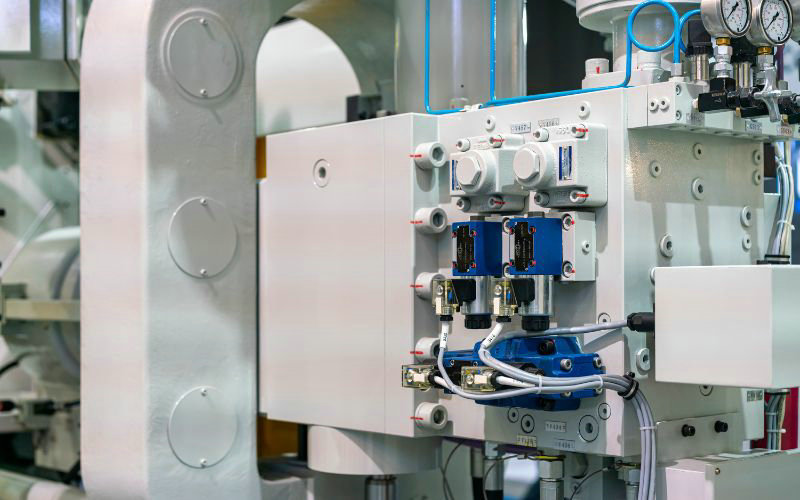
Votre compréhension du MIM commence par son matériel principal : un matière première composé d'une fine poudre de métal et d'un liant polymère. Les métaux couramment utilisés dans ce processus comprennent l'acier inoxydable, le titane, les alliages de nickel et les alliages de cuivre. À ses débuts, le MIM s’apparente au moulage par injection plastique ; la matière première est chauffée jusqu'à ce qu'elle devienne visqueuse et puisse être injectée dans une cavité de moule.
Une fois votre pièce moulée prise, le processus de déliantage commence. Il s'agit d'éliminer la majeure partie du liant, ce qui prépare la pièce au frittage. Lors du frittage, votre pièce est exposée à des températures élevées qui lient les particules métalliques entre elles et assurent leur intégrité.
Après le frittage, vous constaterez que la pièce a considérablement rétréci, généralement entre 15 et 201 TP3T. Cependant, le processus de frittage vous permet d'obtenir une excellente précision dimensionnelle et un excellent état de surface, minimisant souvent le besoin d'usinage ultérieur. Le MIM est très rentable lorsqu'il s'agit de produire de petites pièces en grands volumes grâce à la réduction des déchets de matériaux et à la capacité de maintenir des tolérances serrées sans travaux de finition importants.
En fin de compte, le moulage par injection de métal offre un mélange unique de qualité, d'efficacité et de polyvalence au sein des processus de fabrication. Sa capacité à utiliser une variété de métaux et à obtenir des caractéristiques de matériaux spécifiques, telles que la dureté, la résistance à la traction et la résistance à la température, en fait un processus précieux dans de nombreuses industries.
Applications de moulage par injection de métal (MIM)
Le moulage par injection de métal (MIM) est précis et économique, et convient particulièrement à la production en série de composants de petite et moyenne taille. Vous trouverez des applications MIM dans diverses industries en raison de sa capacité à produire des formes complexes avec une excellente finition de surface.
Aérospatiale et automobile :
- Le MIM est idéal pour fabriquer des pièces telles que des poignées de porte, des charnières et des composants de moteur en raison de sa haute résistance et de sa durabilité.
Médical et dentaire :
- L'industrie médicale bénéficie de la précision de MIM dans la création d'outils chirurgicaux, d'implants et de supports nécessitant une biocompatibilité.
Electronique grand public :
- Les petits composants tels que les pièces de téléphone portable ou les ensembles d'appareils photo exploitent les prouesses de MIM en matière de miniaturisation et de capacités de conception détaillée.
Industrie des armes à feu :
- MIM est utilisé pour fabriquer divers composants d’armes à feu, notamment des gâchettes, des marteaux et des pièces de visée qui exigent des tolérances et une résistance strictes.
Équipement industriel général :
- Vous trouverez MIM dans la production de composants de pompes, de connecteurs et de vannes en raison de ses capacités de production en grand volume et de sa cohérence.
Dans ces applications, MIM offre des avantages tels que :
- Matériaux haute densité avec de grandes propriétés mécaniques
- Possibilité d'intégrer des fonctionnalités telles que des threads, des engrenages et des canaux internes sans opérations secondaires
- Production de pièces proches de la forme finale, minimisant les déchets
Moulage sous pression vs MIM : avantages et inconvénients
Avantages du MIM par rapport au moulage sous pression
1. MIM peut produire de petites pièces complexes avec des caractéristiques complexes et des parois minces qui seraient difficiles, voire impossibles, avec le moulage sous pression.
2. MIM propose une gamme plus large de matériaux, notamment les métaux ferreux, les aciers inoxydables, le titane et les alliages de nickel. Le moulage sous pression est généralement limité aux métaux non ferreux comme l'aluminium, le zinc et le magnésium.
3. Les pièces MIM ont d'excellentes propriétés mécaniques, une résistance élevée et une résistance à l'usure grâce au processus de frittage.
4. MIM offre des tolérances plus strictes et peut être précis à 0,3 mm près.
5. MIM ne génère pratiquement aucun déchet car tout le matériau est injecté directement dans le moule.
Inconvénients du MIM par rapport au moulage sous pression
1. Le MIM est généralement plus cher que le moulage sous pression en raison de l'outillage complexe et des multiples étapes de traitement.
2. MIM a une durée de vie inférieure (150 000 à 300 000 tirs) par rapport au moulage sous pression (plus d'un million de tirs).
3. Les pièces MIM peuvent rétrécir considérablement (jusqu'à 30%) pendant le frittage, ce qui nécessite une conception minutieuse du moule. Le moulage sous pression a un retrait beaucoup plus faible.
4. MIM a des coûts initiaux d’automatisation et de configuration élevés.
Avantages du moulage sous pression par rapport au MIM
1. Le moulage sous pression est généralement moins cher que le MIM, jusqu'à 30% moins cher dans certains cas.
2. Le moulage sous pression a une durée de vie plus longue (plus d'un million de tirs) par rapport au MIM (150 000 à 300 000 tirs).
3. Le moulage sous pression ne nécessite aucune opération secondaire une fois la pièce éjectée du moule.
4. Le moulage sous pression peut accueillir des inserts et des pièces fabriqués à partir d'autres matériaux intégrés dans le moulage.
Inconvénients du moulage sous pression par rapport au MIM
1. Le moulage sous pression a du mal à produire de petites pièces complexes avec des caractéristiques fines et des parois minces.
2. Le moulage sous pression est limité aux métaux principalement non ferreux. Les métaux ferreux ont des points de fusion très élevés, ce qui réduit la durée de vie de la matrice.
3. La porosité due aux gaz piégés est un problème courant dans le moulage sous pression, réduisant la résistance mécanique.
4. Le moulage sous pression nécessite des matrices coûteuses pour résister aux hautes pressions et aux températures du métal en fusion.
En résumé, MIM excelle dans la production de petites pièces complexes dotées d'excellentes propriétés mécaniques dans une large gamme de matériaux. Cependant, il est plus coûteux et a un temps de cycle plus long que le moulage sous pression. Le moulage sous pression est plus économique et convient aux pièces plus simples et plus grandes en métaux non ferreux avec des temps de production plus rapides, mais se heurte à des caractéristiques complexes et à la porosité.
Comparaison : moulage par injection de métal et moulage sous pression
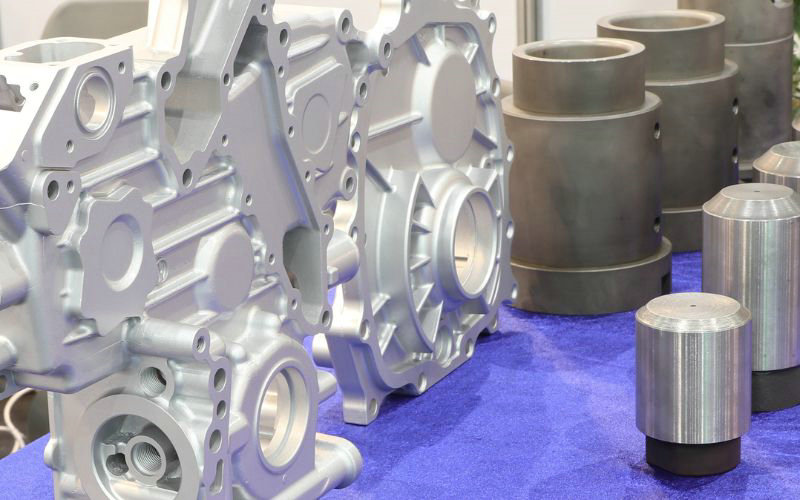
1. Précision et tolérances
Moulage par injection de métal (MIM): MIM réalise des pièces très précises avec des tolérances relativement serrées, généralement précises à 0,3 mm près. Cette précision est due aux fines poudres métalliques utilisées, qui permettent de réaliser des géométries détaillées et complexes.
Moulage sous pression: Le moulage sous pression offre généralement une bonne précision dimensionnelle mais pas aussi élevée que le MIM. La tolérance typique pour le moulage sous pression est d'environ ±0,0005 pouces, ce qui est moins précis que les capacités de MIM. Les variations de dimensions nécessitent souvent un rognage supplémentaire pour répondre aux spécifications.
2. Matériel nécessaire
Moulage par injection de métal (MIM): MIM peut utiliser une large gamme de matériaux, notamment les métaux ferreux et non ferreux, les aciers inoxydables, le titane et les alliages de nickel. Cette polyvalence permet la production de pièces aux propriétés spécifiques adaptées à diverses applications.
Moulage sous pression: Utilise principalement des métaux non ferreux tels que l'aluminium, le zinc et le magnésium. Bien que le moulage sous pression puisse utiliser des métaux ferreux, ces matériaux ont des points de fusion très élevés, ce qui peut réduire considérablement la durée de vie du moule.
3. Comparaison de vitesse
Moulage par injection de métal (MIM): Le processus MIM implique plusieurs étapes, notamment le mélange, le moulage par injection, le déliantage et le frittage, ce qui le rend généralement plus lent que le moulage sous pression. Cependant, une fois la production mise en place, MIM peut produire efficacement de gros volumes de pièces.
Moulage sous pression: Connu pour sa capacité de production rapide, le moulage sous pression est plus rapide, particulièrement adapté aux séries de production en grand volume. Le procédé permet la création rapide de grandes pièces grâce à ses techniques d’injection à haute pression.
4. Finition de surface
Moulage par injection de métal (MIM): Fournit généralement une finition de surface de haute qualité qui ne nécessite souvent pas de post-traitement supplémentaire. Le processus de frittage permet d’obtenir une finition lisse.
Moulage sous pression: Les pièces sortent généralement du moule avec une bonne finition de surface, mais peuvent nécessiter une coupe de l'excès de métal. La qualité de surface est généralement considérée comme moyenne par rapport au MIM.
5. Coûts de fabrication
Moulage par injection de métal (MIM): Bien que les coûts initiaux de configuration et d'outillage puissent être élevés, le MIM peut être rentable pour produire des pièces complexes en grands volumes en raison de la réduction des déchets et des besoins de post-traitement minimes.
Moulage sous pression: Généralement moins coûteux en termes de coûts initiaux et plus rentable pour les pièces plus grandes et la production en grand volume. Cependant, la rentabilité diminue pour les pièces très complexes ou plus petites.
6. Différences de moisissures
Moulage par injection de métal (MIM): Les moules utilisés dans le MIM peuvent être moins durables que ceux du moulage sous pression, supportant généralement environ 150 000 à 300 000 tirs. Cependant, les moules MIM permettent une plus grande complexité dans la conception des pièces.
Moulage sous pression: Les moules sont conçus pour résister à des pressions et des températures élevées, ce qui les rend plus durables, avec une durée de vie de plus d'un million de clichés. Cependant, ils offrent moins de flexibilité en termes de complexité des pièces par rapport aux moules MIM.