La plus grande quantité de moule d'injection plastique pouvant être injectée au cours d'un cycle de moulage est connue sous le nom de taille de la grenaille. Les granulés sont introduits dans le canon et l'ensemble vissé à travers la trémie.
En utilisant la technique de moulage par injection, le matériau fondu est injecté dans la cavité du moule pour créer de grandes quantités de pièces en plastique.
Dans le processus de moulage par injection de plastique, la matière première est introduite dans le fût, fond, et le plastique est ensuite injecté dans la cavité du moule pour refroidissement et solidification après la fermeture du moule. Enfin, le moule s'ouvre et les composants sont expulsés.
Comment calculer la taille du tir
La durée des temps de séjour est influencée par la taille de la grenaille et du canon, ce qui peut également avoir un impact sur la qualité du produit final. Les longues durées de séjour et la dégradation des polymères peuvent provenir de petites tailles de grenaille nécessitant une faible capacité de barillet.
Les petites tailles de grenaille qui occupent moins de 20% de la capacité du canon entraînent fréquemment des temps de séjour prolongés, qui à leur tour provoquent une dégradation du polymère et un contrôle inadéquat du processus.
D'un autre côté, les grosses tailles de grenaille et les niveaux de remplissage du baril supérieurs à 50% peuvent provoquer une fusion inégale et une récupération lente de la vis.
De plus, les vis plus grandes ont généralement des capacités de pression plastique inférieures. Les grosses grenailles, qui occupent plus de 651 TP3T de la capacité du canon, causent fréquemment des problèmes de qualité de la fusion, tels que la non-fusion, une mauvaise uniformité de la fusion et de longs temps de récupération des vis.
Pour être sûr, vous pouvez envisager de passer une commande à deux barils. De plus, les moules peuvent être utilisés avec deux fûts. Lorsque vous commandez un deuxième baril avec la nouvelle machine, vous pouvez être agréablement satisfait de son coût peu élevé. Les barils peuvent être changés en moins de 30 minutes avec les bonnes spécifications et un opérateur expérimenté, même si le baril est chaud.
Formule pour la taille de la grenaille de moule dans le moulage par injection
La formule la plus simple pour calculer la taille de la grenaille de moule est :
Retrait + volume de l'épicéa + volume du produit + volume du canal = taille de la grenaille du moule
Capacité d'injection de la machine de formule/taille d'injection
Le poids total ou le volume que la vis injecte au cours d'un cycle de moulage est exprimé en capacité de tir de la machine (g)/taille de tir de la machine (mm), également appelée capacité d'injection de la machine.
Vos calculs lorsque vous considérez la pression doivent être les suivants :
Course X surface du piston à vis = volume d'injection
Force d'injection/surface du piston à vis = pression d'injection
Ainsi:
Volume d'injection maximal par unité cubique X pression d'injection maximale (bar par unité cubique)/1000 = capacité d'injection de l'unité d'injection.
Les calculs lors de l'utilisation du poids de la vis et de la densité du matériau doivent être les suivants :
Masse/densité= volume
ᴨ*D2*Taille de coup/4= Volume du canon/coup
Facteurs qui affectent la taille de la photo du produit
Il y a plusieurs facteurs dont vous devez tenir compte lors du calcul d'une taille de tir. Ces facteurs sont les suivants :
- Vous devez tenir compte du volume de l'épicéa, du volume des coureurs et du volume du produit lors de la détermination de la taille de la grenaille. En effet, le polymère doit remplir le volume de l'épicéa, du canal d'alimentation et du produit lorsqu'il est injecté dans le moule.
- Un autre problème important qui affecte les calculs de la taille de la grenaille est le retrait du polymère. Le retrait résulte du refroidissement du polymère fondu. En raison des densités variées des polymères, le retrait au moule varie.
- Le type et la quantité d'additifs d'un polymère peuvent modifier sa densité et ses caractéristiques d'écoulement.
Ces facteurs peuvent vous aider à estimer la taille, le volume et la capacité du canon.
Unité d'injection
Le but de l'unité d'injection est de fondre uniformément la matière plastique avant de l'injecter dans le moule à une pression et un débit prédéterminés. Ce sont des activités exigeantes car les fluoropolymères ont une conductivité thermique limitée, une chaleur spécifique élevée et une viscosité à l'état fondu élevée.
Encore une fois, de nombreuses variantes ont été développées pour résoudre les problèmes complexes à résoudre. Une classification générale des variations peut être faite en quatre concepts d'unité d'injection primaire :
- Piston ou bélier à un étage
- Bélier à deux étages
- Vis à un étage
- Vis/bélier à deux étages
Bien qu'il existe encore dans de minuscules machines et certains équipements spécialisés, l'unité de vérin à un étage est essentiellement obsolète en raison de son inefficacité dans le chauffage, le mélange et la transmission de la pression. Il bénéficie de la simplicité et de l'abordabilité.
De plus, le vérin à deux étages est tout sauf obsolète. Le piston reste un mélangeur et un réchauffeur inefficaces malgré une tentative de l'améliorer en séparant les opérations de chauffage et d'écoulement sous pression.
L'unité vis/bélier à deux étages sépare en outre les rôles de débit et de chaleur en utilisant un bélier pour l'injection au lieu d'une vis pour le mélange et le chauffage. L'idée est séduisante car les deux sont des outils efficaces pour leurs tâches respectives.
De plus, l'unité d'injection est souvent évaluée en utilisant la pression d'injection maximale et le volume d'injection disponible. La plus grande pression possible à l'extrémité aval de la vis est appelée pression d'injection. Cela dépend du diamètre de la vis et de la force qui la pousse.
Veillez toutefois à ne pas la confondre avec la pression dans la conduite hydraulique agissant sur le cylindre d'injection, qui entraîne la vis, ni à l'interpréter comme la pression nécessaire pour remplir les cavités du moule. En raison des pertes de pression dans les systèmes d'alimentation de la buse et du moule, cela est nettement inférieur.
La principale série d'actions de l'unité d'injection est la suivante :
- Le matériau est chauffé et fondu au fur et à mesure que la vis tourne, puis transporté le long des filets de la vis jusqu'à l'extrémité aval de la vis. La tuyère du fourreau est fermée par l'utilisation d'une vanne mécanique ou thermique ou par l'existence d'un moulage antérieur.
Jusqu'à ce que suffisamment de matière fondue se soit accumulée pour fabriquer le moulage suivant, la masse fondue collectrice force la vis toujours en rotation contre une résistance contrôlée (la contre-pression). La rotation de la vis s'arrête ici. Il est temps d'être prêt pour la fonte.
- Lorsque la buse du canon est ouverte, la vis avance dans une direction axiale sans tourner, agissant comme un vérin. En conséquence, la masse fondue rassemblée devant l'extrémité aval de la vis est forcée (injectée) à travers la buse et dans le moule.
Pour empêcher la fonte de refluer vers le bas des filets de la vis, un système de soupape peut être installé à l'extrémité aval de la vis. C'est l'étape d'injection ou de remplissage du moule.
- Une fois le moule rempli, la pression de la vis est maintenue pendant un court instant pour compenser le retrait volumétrique de la matière fondue de refroidissement à l'intérieur du moule. La phase d'emballage ou de maintien est maintenant.
- Enfin, il arrive à la phase de maintien, où le cycle de l'unité d'injection reprend avec la rotation de la vis et la préparation des fondus tandis que le moule est maintenu fermé pour permettre au moulage de refroidir à la température d'éjection.
Il y a des chutes de pression importantes lorsque le plastique fondu est forcé dans la buse d'injection et ensuite à travers le système d'alimentation du moule et les cavités. Des règles simples ne permettent pas de calculer ces pertes de charge.
Unité de serrage
La fermeture du moule est maintenue contre les forces créées lorsque le plastique est poussé dans un moule fermé par la pression d'injection à l'aide d'une unité de serrage pour un IMM. Il dispose d'un système d'entraînement qui peut déplacer le plateau mobile de la machine de moulage par injection dans au moins une direction.
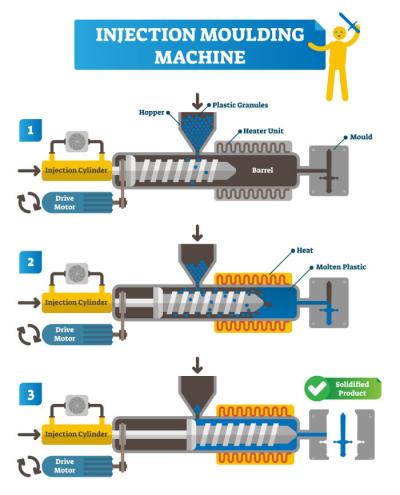
Types d'unités de serrage
Il existe plusieurs types d'unités de serrage dans le processus de moulage par injection. Ils sont les suivants :
Serrage à bascule
Un dispositif mécanique qui amplifie la force est une bascule. Deux barres sont reliées et se terminent par un pivot dans une machine à mouler. Une extrémité de barre est reliée à un plateau fixe, tandis que l'autre est reliée à un plateau mobile. La bascule a une forme en V lorsque le moule est ouvert. Les deux barres forment une ligne droite lorsqu'une pression est appliquée sur le pivot.
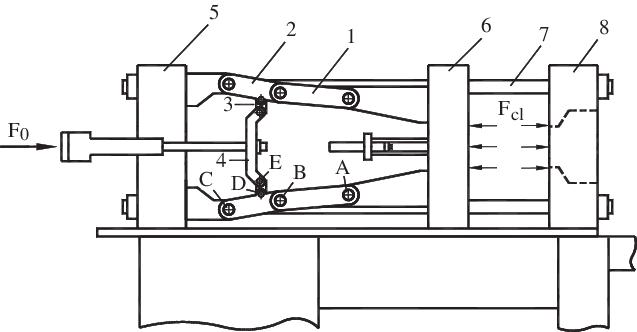
Les avantages du serrage à genouillère incluent qu'il nécessite moins d'argent et de puissance et fournit un plan positif du moule. En outre, les inconvénients du serrage du type à genouillère sont qu'il nécessite un entretien élevé et qu'il est difficile à réaliser.
Serrage hydraulique
Dans ce cas, la RAM du système hydraulique est liée au plateau mobile, et une unité de serrage alimentée par un vérin hydraulique est directement connectée au moule mobile fermé. Le vérin hydraulique a deux sections : l'entrée d'huile et la sortie.
L'huile pousse la RAM vers l'avant lorsqu'elle pénètre dans le cylindre sous pression, provoquant la fermeture du plateau mobile et du moule. De plus, le retour RAM et le moule sont ouverts lorsque l'huile est libérée du cylindre.
Certains avantages du serrage hydraulique incluent un contrôle facile de la vitesse de serrage et du support à n'importe quel angle, une mesure simple de la force de serrage, une configuration facile du mode et un réglage de la force de serrage, et sa simplicité d'entretien.
Les inconvénients de ce type de serrage sont qu'il coûte plus cher et est plus cher qu'un système à genouillère et qu'une pince à nom positif.
Unité de serrage de type magnétique
Des modules magnétiques à l'intérieur des plaques ou plateaux de serrage magnétiques du moule produisent la force de serrage. Le panneau d'interface peut contrôler le serrage du moule, le changement de moule et la magnétisation et la démagnétisation des plateaux.
Les avantages de cette unité de serrage incluent l'électricité requise uniquement pendant les phases de magnétisation et de démagnétisation, pas pendant le serrage, la mesure de la force de serrage en temps réel avec de nombreuses fonctions de sécurité et une maintenance gratuite.
Poids de la grenaille de moule
La quantité de matière injectée dans le moule pour remplir le moule, y compris le système d'alimentation, est connue sous le nom de « poids d'injection du moule » ou « poids d'injection du produit ». Le poids de l'épicéa, du coureur et de la porte sont les composants du poids du tir, d'autre part. La distance parcourue par la vis pour remplir le produit, y compris le système d'alimentation, est connue sous le nom de taille de moule/produit.
Conclusion
En utilisant la technique de moulage par injection, le plastique brut est fondu, injecté dans le moule, laissé refroidir et se solidifier, puis l'objet fini est expulsé. La taille de la grenaille est cruciale car elle empêche le sous-remplissage de polymère et le flash. D'autres facteurs, tels que la capacité du baril, affectent également le processus général de moulage par injection.