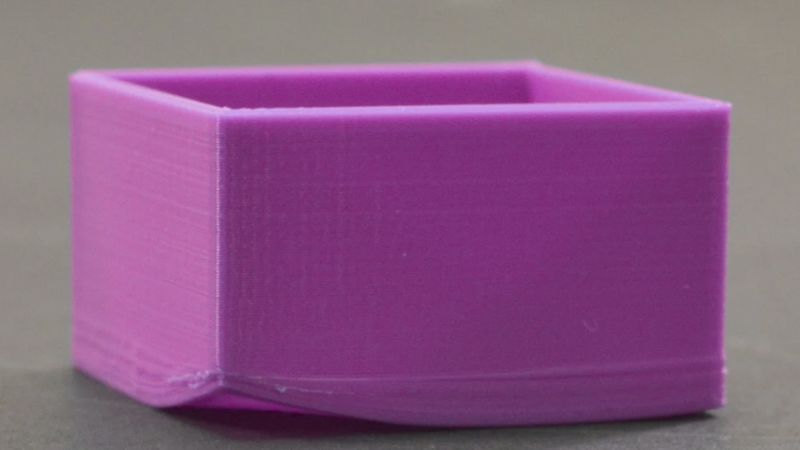
Verzug kann ärgerlich sein. Für Hersteller und Produktdesigner gleichermaßen ist es wichtig, die Grundursachen für Verzug zu verstehen. Die Umsetzung effektiver Präventionsstrategien ist entscheidend, um eine hohe Qualität der Produkte aufrechtzuerhalten und die Produktionskosten zu minimieren.
In diesem umfassenden Leitfaden untersuchen wir die Hauptfaktoren, die zum Verzug beim Spritzgießen beitragen, und bieten praktische Lösungen zur Minderung dieses Problems.
Durch die Anwendung dieser Erkenntnisse können Hersteller ihre Produktionseffizienz verbessern, die Ausschussquote senken und letztendlich qualitativ hochwertige Spritzgussteile liefern.
Was ist Formverzug?
Verzug ist eines der entscheidenden Qualitätsprobleme beim Kunststoff-Spritzguss und führt oft zu Maßinstabilitäten bei Kunststoffteilen.
Unter Verzug versteht man die unerwünschte Abweichung von der beabsichtigten Produktgeometrie, die bei Kunststoffteilen während des Spritzgussverfahrens auftreten kann. Dieser Defekt äußert sich in Verformungen wie Verdrehen, Verbiegen oder Kräuseln des Formteils.
Die Schwere der Verformung reicht von leichten, mit bloßem Auge kaum erkennbaren Deformationen bis hin zu erheblichen Verzerrungen, die die Funktion oder Montage des Teils beeinträchtigen.
Die Auswirkungen von Verzug auf Formprodukte
Das Auftreten von Verzug beim Spritzgießen hat erhebliche Auswirkungen auf die Qualität und Funktionalität von Kunststoffteilen:
- Ästhetische Qualität: Die optische Attraktivität wird beeinträchtigt, wodurch die Endprodukte auf dem Markt weniger wettbewerbsfähig werden.
- Dimensionsstabilität: Verformte Teile passen möglicherweise nicht in Baugruppen oder weisen nicht die genauen Abmessungen auf, die für die Schnittstelle mit anderen Komponenten erforderlich sind.
- Funktionsdefizite: Über die Ästhetik hinaus kann Verzug die mechanische Leistung und strukturelle Integrität des Bauteils beeinträchtigen.
Was ist die Ursache für Verzug beim Spritzgießen?
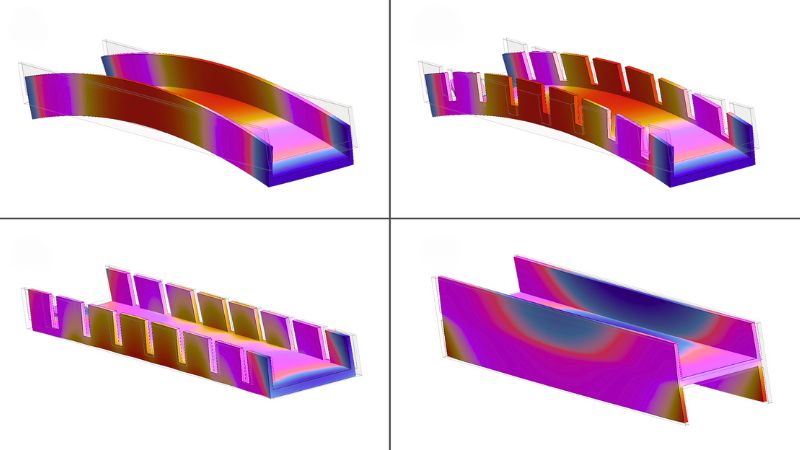
Dieser Abschnitt untersucht die Feinheiten von Maschine, Form, Und Wesentliche Faktoren trägt zur Verformung bei und bietet einige praktische Lösungen zur Minderung dieser Probleme.
Maschinenfehler
Unzureichender Einspritzdruck oder unzureichende Einspritzzeit
Unzureichender Einspritzdruck oder eine unzureichende Haltezeit können zu einer unzureichenden Füllung der Form führen. Dies kann dazu führen, dass das Kunststoffmaterial abkühlt und erstarrt, bevor die Form richtig gefüllt ist.
In beiden Fällen kommt es während der Abkühlung zu einer unkontrollierten Bewegung der Moleküle, was zu ungleichmäßiger Schrumpfung und Verformung führt.
Falsche Fasstemperatur
Wenn die Zylindertemperatur zu niedrig ist, erreicht das Harz nicht die richtige Fließtemperatur, was zu vorzeitiger Verfestigung, unzureichender Formfüllung und schließlich zu ungleichmäßiger Schrumpfung und Verformung führt.
Unsachgemäße Verweilzeit
Eine unzureichende Verweilzeit verhindert eine gleichmäßige Wärmeabsorption im gesamten Harz. Dies kann dazu führen, dass unterhitzte Teile des Materials steif werden und vorzeitig erstarren, was zu unvollständiger Formfüllung und Verformung führt.
Übermäßige innere Belastung
Durch hohen Einspritzdruck können im Formteil innere Spannungen entstehen, die sich nach dem Entformen als Verzug bemerkbar machen können.
Falsche Schraubenvorlaufzeit
Wenn die Schneckenvorwärtszeit zu lang ist, kann es zu einer Überfüllung der Form kommen, wodurch innere Spannungen entstehen, die Verzug zur Folge haben.
Unzureichende Abkühlzeit
Eine unzureichende Abkühlzeit kann dazu führen, dass das Teil vor dem Auswerfen nicht gleichmäßig und vollständig abkühlt. Dies kann zu ungleichmäßiger Schrumpfung und Verformung führen, da das Teil außerhalb der Form weiter abkühlt.
Schimmelpilz-Fehler
Unsachgemäße Platzierung und Konstruktion des Tors
Eine falsche Platzierung des Angusses kann zu einer ungleichmäßigen Füllung und Verdichtung des Formhohlraums führen. Dies führt zu einer ungleichmäßigen Druckverteilung und Abkühlungsgeschwindigkeit und damit zu Verformungen.
Unzureichende Platzierung des Auswerferstifts
Schlecht positionierte oder unzureichende Auswerferstifte können zu ungleichmäßiger Spannung beim Auswerfen des Teils aus der Form führen. Dies kann insbesondere bei Teilen mit komplexer Geometrie zu Verzug führen.
Unausgeglichene Kühlkreisläufe
Unsachgemäß ausbalancierte Kühlkreisläufe können eine ungleichmäßige Kühlung in den Hohlräumen verursachen, was zu Verformungen einiger Teile führt, während andere davon unberührt bleiben.
Fehler bei der Materialauswahl
Hohe Schrumpfungsraten
Materialien mit hoher Schrumpfungsrate neigen eher zum Verziehen.
Beispielsweise weisen teilkristalline Polymere wie Polyethylen (PE) und Polypropylen (PP) höhere Schrumpfungsraten auf als amorphe Polymere wie Polycarbonat (PC) oder Polystyrol (PS).
Uneinheitliche Schrumpfung
Einige Werkstoffe schrumpfen in Fließrichtung anders als quer zur Fließrichtung. Diese anisotrope Schrumpfung kann insbesondere bei Teilen mit langen Fließwegen zu Verformungen führen.
Kristallinität
Hochkristalline Werkstoffe neigen eher zu Verzügen, da sie beim Abkühlen zu einer stärkeren Schrumpfung neigen.
Feuchtigkeitsempfindlichkeit
Einige Materialien, wie Nylon, sind hygroskopisch und können Feuchtigkeit aus der Luft aufnehmen. Dies kann zu inkonsistenten Formergebnissen und möglichem Verziehen führen, wenn es vor der Verarbeitung nicht richtig getrocknet wird.
Wie lässt sich Verzug beim Spritzgießen reduzieren?
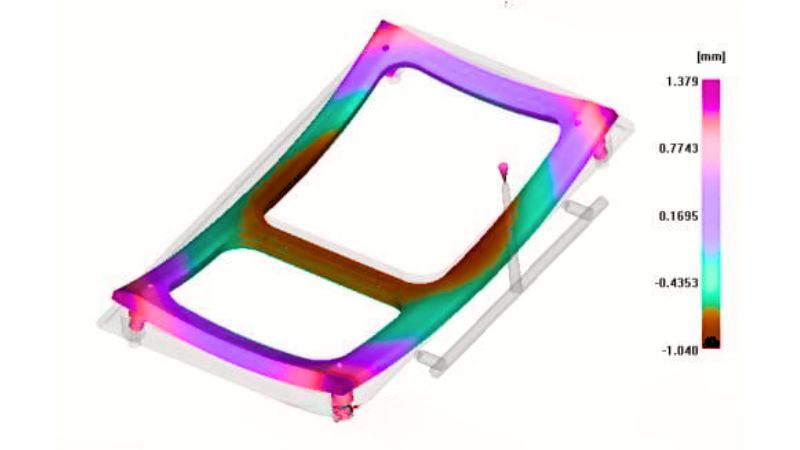
Die Optimierung der Verarbeitungsparameter ist entscheidend. Beginnen Sie mit der Anpassung des Einspritzdrucks und der Haltezeit, um eine ordnungsgemäße Füllung der Formhöhle sicherzustellen. Dadurch werden die Kunststoffmoleküle eingeschränkt und unkontrollierte Bewegungen während der Abkühlung verhindert.
Eine längere Abkühlzeit ermöglicht eine vollständige und gleichmäßige Abkühlung und trägt dazu bei, unterschiedliche Schrumpfungsraten zu verhindern, die häufig zu Verzügen führen.
Ebenso wichtig ist die Feinabstimmung der Temperatureinstellungen. Eine Erhöhung der Zylindertemperatur gewährleistet den richtigen Materialfluss, während eine Anpassung der Formtemperatur auf Grundlage der Empfehlungen des Harzlieferanten für eine gleichmäßige Temperatur sorgt.
Sofern möglich, kann durch die Implementierung konturnaher Kühlkanäle eine gleichmäßigere Kühlung des gesamten Teils weiter verbessert werden.
Überlegungen zum Formdesign und Material
Durch die Optimierung von Angusskanälen und Eingusskanälen durch die Verwendung geeigneter Angusstypen für bestimmte Kunststoffe und Produktdesigns, die Implementierung mehrerer Angusskanäle für flache Teile und die Verbreiterung von Angusskanälen und Eingusskanälen kann die Formfüllung erheblich verbessert werden.
Auch die richtige Platzierung der Auswerferstifte ist entscheidend. Stellen Sie sicher, dass sie weit genug entfernt und gut verteilt sind und sich in der Nähe der Bereiche mit dem größten Auswerferwiderstand befinden. So können Sie Verformungen beim Entfernen der Teile verhindern.
Die Auswahl und Handhabung des Materials sind Schlüsselfaktoren. Die Wahl von weniger verzugsanfälligen Harzen, wie amorphen Kunststoffen wie Polycarbonat und Polystyrol anstelle von kristallinen Kunststoffen, kann einen erheblichen Unterschied machen.
Bei Teilen mit Metalleinsätzen hilft das Vorwärmen auf etwa 100 °C dabei, Schrumpfungsunterschiede zwischen Metall und Kunststoff auszugleichen und so Spannungen und mögliche Verformungen zu reduzieren.
Designoptimierung und Qualitätskontrolle
Ein weiterer wichtiger Aspekt ist die Optimierung des Teiledesigns. Die Beibehaltung einer gleichmäßigen Wandstärke im gesamten Teil fördert eine gleichmäßige Abkühlung und Schrumpfung, während das Hinzufügen von Verstärkungsrippen die Steifigkeit des Teils verbessern und die Verformungsneigung verringern kann.
Zusammenarbeit mit Profis — Moldie
Zusammenarbeit mit Moldie kann zu Qualität und Effizienz im Spritzgussverfahren für Kunststoff führen. Wir verfügen über das erforderliche Fachwissen, um mit einer Vielzahl von Kunststoffmaterialien umzugehen und sicherzustellen, dass die daraus resultierenden Kunststoffprodukte Haltbarkeit und Ästhetik vereinen.
Moldie legt bei seinen Fertigungstechniken Wert auf Präzision. Unser Ansatz umfasst:
- Fortschrittliches Formendesign: Durch die Optimierung von Angussgröße und -form trägt Moldie zur Aufrechterhaltung eines gleichmäßigen Durchflusses und einer gleichmäßigen Kühlung bei, was zu weniger innerer Spannung und reduziertem Verzug führt.
- Materialauswahl: Ihre Kenntnisse über verschiedene Kunststoffe ermöglichen eine fundierte Materialauswahl, wobei die Eigenschaften auf die beabsichtigte Anwendung abgestimmt und Mängel gemindert werden.
- Prozessoptimierung: Moldie optimiert die Formtemperatur und die Abkühlraten, da diese Variablen bei der Herstellung hochwertiger, verzugsfreier Komponenten eine entscheidende Rolle spielen.
Wir sind davon überzeugt, dass eine solche Zusammenarbeit den Standard der hergestellten Kunststoffkomponenten deutlich steigern und so letztlich die Funktionalität und das Erscheinungsbild des Endprodukts verbessern kann.