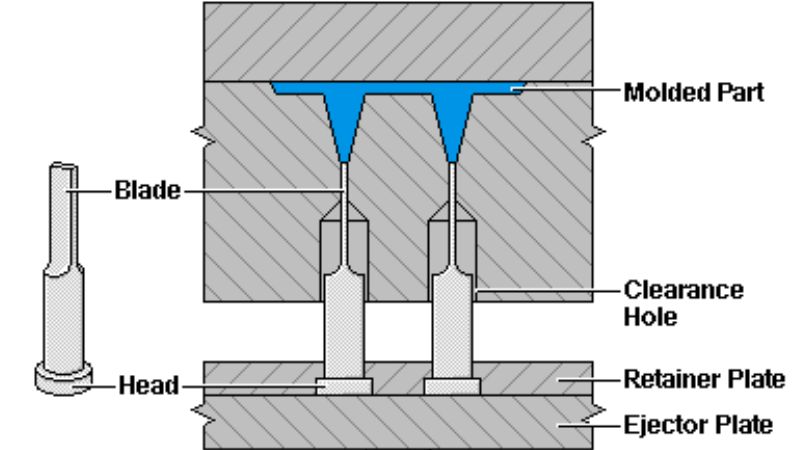
Spritzguss ist eine beliebte Methode zur Herstellung von Kunststoffteilen durch Einspritzen von geschmolzenem Kunststoff in eine Form. Schlüsselkomponenten und die Art der verwendeten Kunststoffmaterialien spielen eine entscheidende Rolle bei der Gestaltung des Endprodukts.
Beim Spritzgussverfahren werden Teile hergestellt, indem geschmolzener Kunststoff in eine Form gespritzt wird. Der Prozess beginnt mit dem Erhitzen von Kunststoffgranulat, bis es schmilzt. Dieser geschmolzene Kunststoff wird dann unter hohem Druck in eine Form gespritzt. Die Form, die die Form und die Eigenschaften des endgültigen Teils bestimmt, kühlt den Kunststoff ab, sodass er aushärten und die gewünschte Form annehmen kann.
Schlüsselkomponenten von Spritzgussmaschinen
Eine Spritzgussmaschine besteht aus drei Hauptteilen: der Spritzeinheit, der Form und der Schließeinheit.
- Injektionseinheit: Dieser Teil schmilzt und spritzt den Kunststoff ein. Er umfasst einen Trichter, eine Heizung und eine Schraube/einen Kolben, der den geschmolzenen Kunststoff in die Form drückt.
- Schimmel: Es besteht aus zwei Hälften und formt den Kunststoff. Kern und Hohlraum bilden die Innen- und Außenflächen des Teils.
- Klemmeinheit: Es hält die Formhälften während der Einspritz- und Abkühlphase zusammen und gewährleistet so die präzise Form und Gestaltung des Teils.
Wie werden Formhohlräume gestaltet?
Bei der Gestaltung von Formhohlräumen müssen Sie mehrere Aspekte berücksichtigen, die die Qualität und Effizienz des Endprodukts beeinflussen. Das Verständnis der Rolle der Kern und Hohlraum, die Auswahl geeigneter Designfaktoren und die Entscheidung über den Formtyp sind wichtige Schritte im Prozess.
Was ist eine Formkavität beim Spritzgießen?
Ein Formhohlraum ist ein entscheidendes Element im Spritzgussverfahren. Er bezieht sich auf den Hohlraum innerhalb einer Form, der die Form und Abmessungen des herzustellenden Kunststoffteils definiert. Wichtige Punkte zu Formhohlräumen sind:
Der Formhohlraum ist ein Loch oder ein negativer Raum in der Form des gewünschten Endteils. Er besteht normalerweise aus rostfreiem Stahl.
Wenn geschmolzener Kunststoff in die Form gespritzt wird, füllt er den Hohlraum und nimmt seine Form an. Nach dem Abkühlen und Erstarren bildet sich das fertige Kunststoffteil.
Normalerweise gibt es drei Arten von Formhohlräumen:
- Einzelkavitätenwerkzeuge: Produzieren Sie ein Teil pro Zyklus
- Mehrfachwerkzeuge: Verfügt über mehrere identische Hohlräume und produziert mehrere identische Teile pro Zyklus
- Familienformen: Haben mehrere unterschiedliche Hohlräume und produzieren unterschiedliche Teile in einem Zyklus
Faktoren, die das Hohlraumdesign beeinflussen
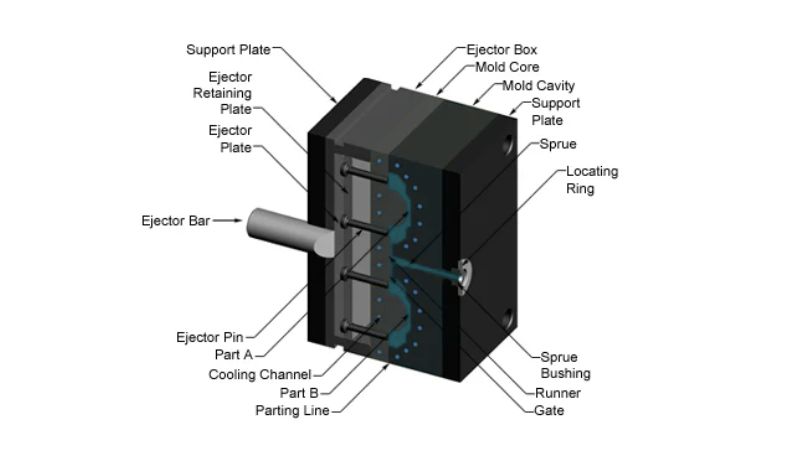
Die Gestaltung der Kavität in einer Form wird von mehreren Schlüsselfaktoren beeinflusst. Dabei beginnt man mit der Teilegeometrie. Komplexe Formen können erweiterte Konfigurationen erfordern, um alle Merkmale zu bilden und gleichzeitig die Funktionalität der Form präzise aufrechtzuerhalten. Und für ein einfaches Auswerfen sind geeignete Entformungsschrägen unverzichtbar.
Auch die Materialauswahl spielt eine entscheidende Rolle, da unterschiedliche Materialien unterschiedliche Fließeigenschaften, Schrumpfungsraten und thermische Eigenschaften aufweisen, sodass maßgeschneiderte Designs erforderlich sind, um eine ordnungsgemäße Befüllung und Kühlung zu gewährleisten.
Darüber hinaus ist die Integration effizienter Kühlkanäle entscheidend, um die Temperatur zu kontrollieren und die Zykluszeiten zu verkürzen, während gleichzeitig Verformungen oder Defekte vermieden werden. Die Fließdynamik muss berücksichtigt werden, um sicherzustellen, dass das geschmolzene Material die Kavität gleichmäßig und ohne Hohlräume füllt, und das Design von Anguss- und Angusskanälen ist für die Optimierung des Materialflusses von entscheidender Bedeutung.
Schließlich ist es wichtig, sekundäre Vorgänge wie die Bearbeitung oder Lackierung zu berücksichtigen, um sicherzustellen, dass das Hohlraumdesign allen zusätzlichen Verarbeitungsanforderungen gerecht wird. Durch sorgfältige Berücksichtigung dieser Faktoren können Hersteller effektive Formen erstellen, mit denen qualitativ hochwertige Teile effizient und wirtschaftlich hergestellt werden können.
Kern vs. Hohlraum: Was sind die Unterschiede?
Der Hohlraum formt die Außenseite des Teils, während der Kern die Innenseite definiert. Zusammen ergeben sie die vollständige Form des Produkts. Wenn die beiden Hälften der Form geschlossen werden, passen Kern und Hohlraum zusammen, um das endgültige Design zu erzeugen.
Bei einer typischen zweiteiligen Form befindet sich die Kavität häufig in der stationären Hälfte, während sich der Kern in der beweglichen Hälfte der Form befindet.
Auch die Auswurfmethode ist unterschiedlich. Nach dem Abkühlen wird das Teil normalerweise durch Trennen der Formhälften entfernt, sodass sich Hohlraum und Kern vom geformten Produkt lösen.
Einkavitäten- vs. Mehrkavitäten-Spritzgussformen: Was sind die Unterschiede?
Beim Kunststoffspritzguss ist die Wahl zwischen Einkavitäten- und Mehrfachkavitätenformen ausschlaggebend für die Produktionseffizienz, die Formenkosten und die Teilequalität.
A Einkavitätenform enthält eine Kavität und produziert ein Teil pro Zyklus. Dieses Design ist besonders vorteilhaft für geringe bis mittlere Produktionsmengen, da es geringere anfängliche Werkzeugkosten, eine einfachere Wartung der Form und die Flexibilität ermöglicht, Designs nach Bedarf zu ändern.
Einzelkavitätenformen eignen sich hervorragend für die Prototypenentwicklung und Herstellung kundenspezifischer Teile, bei denen es mehr auf Präzision als auf Quantität ankommt.
Auf der anderen Seite Mehrfachform integriert mehrere Hohlräume in eine einzige Form und ermöglicht so die gleichzeitige Produktion mehrerer identischer Teile mit jedem Spritzzyklus. Diese Methode erhöht nicht nur die Produktionsgeschwindigkeit, sondern senkt auch die Stückkosten und ist daher ideal für die Massenproduktion. Mehrfachhohlraumformen sind in Branchen unverzichtbar, die große Mengen identischer Teile benötigen, da sie Konsistenz gewährleisten und das Risiko von Produktfehlern minimieren.
Sie sind jedoch mit höheren anfänglichen Werkzeugkosten verbunden und erfordern eine anspruchsvollere Konstruktion. Darüber hinaus gibt es Überlegungen hinsichtlich der Zykluszeit. Mehrfachhohlraumformen können die Zykluszeit erheblich verkürzen, da sie mehrere Teile gleichzeitig produzieren. Die Komplexität dieser Formen kann jedoch zu längeren Rüstzeiten führen und erfordert erweiterte Wartungsprotokolle, um Probleme wie Hohlraumungleichgewicht und Verschleiß im Laufe der Zeit zu beheben. Im Gegensatz dazu ermöglichen Einzelhohlraumformen schnellere Anpassungen und Fehlerbehebungen, was sie bei der Verarbeitung einzigartiger oder einmaliger Teile einfacher handhabbar macht.
Ein weiterer wichtiger Aspekt ist die Skalierbarkeit der Produktion. Während Einzelhohlraumformen ideal für kleinere Chargen oder kundenspezifische Produkte sein können, können Unternehmen mit Mehrhohlraumformen ihre Produktion schnell steigern, um die Marktnachfrage zu erfüllen, ohne Kompromisse bei der Qualität eingehen zu müssen.
Warum Molide wählen?
Moldie wurde 2008 gegründet und hat sich als führender Hersteller von hochwertigen Kunststoff-Spritzgussformen, Druckgussformen und mechanischen Präzisionsteilen etabliert. Wir bieten eine komplette OEM/ODM-Lösung, die alles von Teiledesign und Prototyping bis hin zu Formendesign, Produktion und Großserienfertigung abdeckt.
Internationale Branchenführer vertrauen auf unser Know-how. Wir beliefern renommierte Automobilmarken wie Mercedes-Benz, Volkswagen, Audi, BMW und Ferrari sowie große Unternehmen anderer Branchen wie Schneider und Phillip.
Ob Sie Kunststoff-Spritzgussformen, Druckgussformen für Aluminium, Zamak und Magnesium oder mechanische Präzisionsteile benötigen, Moldie kann Ihre vielfältigen Fertigungsanforderungen erfüllen! Kontaktieren Sie uns noch heute!
Häufig gestellte Fragen
Wie lässt sich ein Kavitätsdiagramm einer Spritzgussform verstehen?
Um ein Formhohlraumdiagramm zu lesen, suchen Sie nach Beschriftungen, die die Hohlraum- und Kernseiten angeben. Achten Sie auf die Designelemente wie Formbasis, Anguss und Angusskanalsystem. Diese Diagramme helfen dabei, zu visualisieren, wie geschmolzener Kunststoff fließt und die Hohlräume füllt, um Teile zu formen.
Könnten Sie den Hohlraumformprozess erläutern?
Das Hohlraumformverfahren beginnt, wenn geschmolzener Kunststoff in die Formhöhle eingespritzt wird. Die Form wird dann abgekühlt, um das Teil zu verfestigen. Es ist entscheidend, dass die Form präzise konstruiert wird, da jeder Fehler die Qualität und Genauigkeit der produzierten Teile beeinträchtigen kann.
Welche Faktoren beeinflussen die Kosten einer Einzelkavität-Spritzgussform?
Die Kosten einer Einzelkavitätsform werden von mehreren Faktoren beeinflusst. Dazu gehören die Komplexität des Teils, das in der Form selbst verwendete Material und das Produktionsvolumen. Auch die Werkzeugpräzision und zusätzliche Funktionen wie automatisierte Funktionen spielen bei der Kostenbestimmung eine Rolle.