Was ist eine Oberflächenbeschaffenheit beim Spritzgießen?
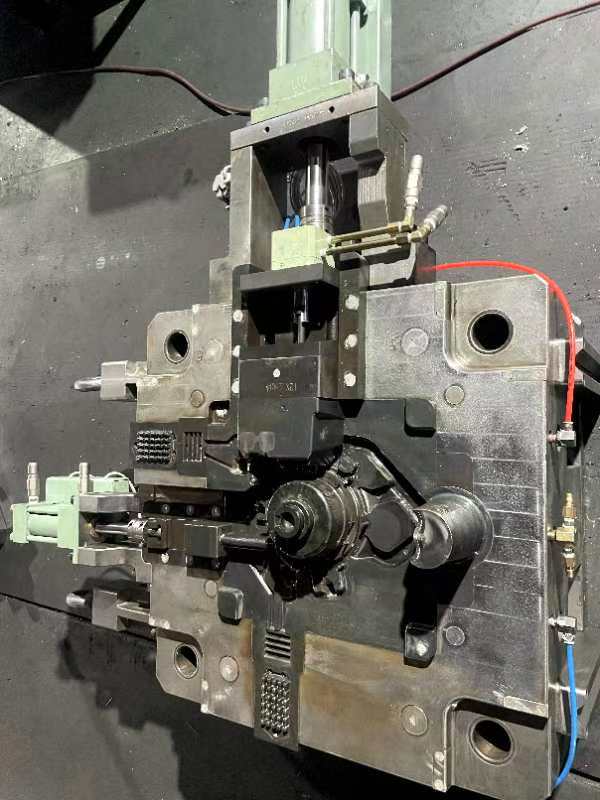
Im Bereich des Spritzgussverfahrens kann die gewählte Oberflächenbeschaffenheit sowohl das Aussehen als auch die Funktionalität des Endprodukts erheblich beeinflussen.
Definition der Oberflächenbeschaffenheit
A Oberflächenfinish bezieht sich auf die Textur der Oberfläche eines Teils, das hergestellt wurde durch Spritzguss. Es umfasst den Glanzgrad, die Rauheit und das Muster, das der Oberfläche des Formteils verliehen wird. Diese Oberflächenbeschaffenheit wird durch die Qualität der Form selbst sowie durch die im Spritzgussverfahren verwendeten Materialien bestimmt. Es können verschiedene Oberflächenbeschaffenheiten erzielt werden, darunter matte, strukturierte oder hochglänzende Oberflächen, die durch verschiedene Nachformungsprozesse wie Polieren oder das Auftragen von Texturen auf die Form vor der Produktion erzielt werden.
Bedeutung der Oberflächenbeschaffenheit beim Spritzgießen
Die Oberflächenbeschaffenheit beim Spritzgießen ist von größter Bedeutung, da sie direkten Einfluss auf die Aussehen Und Funktionalität des Teils.
Bedeutung für die visuelle Attraktivität
- Eine glatte, glänzende Oberfläche (SPI-Klasse A) sorgt für ein hochwertiges, poliertes Aussehen, das für kosmetische Teile, Linsen usw. geeignet ist.
- Halbglänzende (SPI-Klassen B) und matte (SPI-Klassen C) Oberflächen können Unvollkommenheiten wie Fließlinien, Schweißnähte und Werkzeugspuren verbergen und so das Erscheinungsbild verbessern.
- Strukturierte Oberflächen (SPI D-Klassen) bieten einzigartige ästhetische Optionen wie Ledermaserung, Holzmaserung, geometrische Muster usw.
Bedeutung für die Funktionalität
- Strukturierte Oberflächen können bei Produkten wie Handgeräten, Lenkrädern usw. für bessere Griffigkeit und Rutschfestigkeit sorgen.
- Durch spezielle Oberflächenbehandlungen kann die Haftung von Farbe und Etiketten auf der Oberfläche des Formteils verbessert werden.
- Durch die Texturierung können Gase aus der Form entweichen und Hinterschnitte erzeugt werden.
- Die Oberflächenrauheit beeinflusst die Reibung und Verschleißfestigkeit, was bei mechanischen Teilen von Bedeutung sein kann.
Wie werden die Oberflächengütestandards SPI, VDI und Mold-tech angewendet?
Oberflächengütestandards wie SPI und VDI definieren die kosmetische Qualität und Funktionalität der Formteile, indem sie die Parameter Glanz, Textur und Rauheit festlegen. Diese Standards stellen sicher, dass die Oberflächen vorgegebene Kriterien erfüllen, die für die Leistung und Ästhetik des Produkts entscheidend sind.
Übersicht über die SPI-Formoberflächenstandards
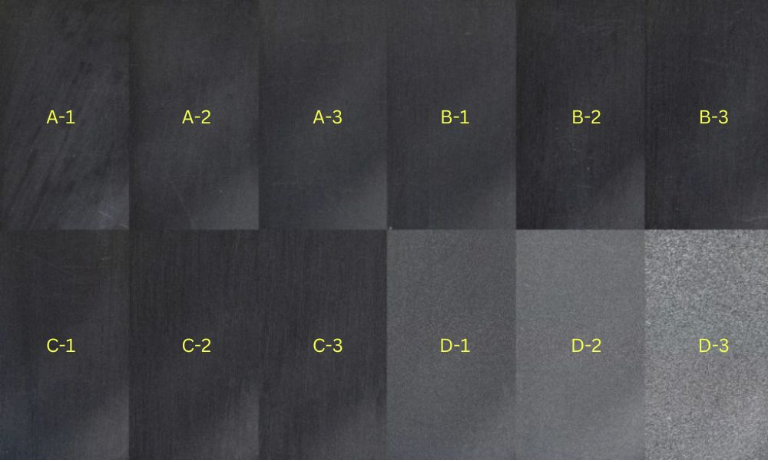
Das Gesellschaft der Kunststoffindustrie (SPI) hat ein Klassifizierungssystem für Oberflächen von Spritzgussformen entwickelt. Dieses System kategorisiert Oberflächen in glänzend (A), halbglänzend (B), matt (C), und strukturierte (D) Qualitäten, jeweils mit angegebenen Glanz- und Rauheitsgraden:
- SPI A ist der Höhepunkt und sorgt für hochglanzpolierte, glänzende Oberflächen. Oft ist dafür der arbeitsintensive Einsatz von Diamantpoliermitteln erforderlich. Geeignet für Teile, bei denen ein erstklassiges Aussehen von größter Bedeutung ist.
- SPI B bietet halbglänzende Oberflächen, die durch feineres Schleifen und weniger intensives Polieren erreicht werden. Diese Oberflächen sind ein Gleichgewicht zwischen Ästhetik und Kosteneffizienz.
- SPI C spiegelt ein standardmäßiges mattes Finish wider, das typischerweise mit Steinschleifmitteln erzeugt wird.
- SPI D Erzeugt die strukturiertesten, nicht glänzenden Oberflächen, geeignet für Teile, bei denen Griffigkeit oder nicht reflektierende Eigenschaften erwünscht sind.
Über dieses Spektrum hinweg werden der Formoberfläche exakte Rauheitswerte verliehen, die sicherstellen, dass das Teil das gewünschte Aussehen behält.
SPI-Standard | Finish (Klasse) | Ausführung (Typ) | Fertigstellungsmethode | Typische Oberflächenrauheit (Ra µm) |
A-1 | Glänzend | Super Hochglanz | Diamant-Schwabbelscheibe, Güteklasse #3, Körnung 6000 | 0,012 bis 0,025 |
A-2 | Glänzend | Hochglanz | Diamant-Schwabbelscheibe, Güteklasse #6, Körnung 3000 | 0,025 bis 0,05 |
A-3 | Glänzend | Normal glänzend | Diamant-Schwabbelscheibe, Körnung 1200, Güteklasse #15 | 0,05 bis 0,10 |
B-1 | Halbglänzend | Fein Seidenmatt | 600er-Schleifpapier | 0,05 bis 0,10 |
B-2 | Halbglänzend | Mittel Seidenmatt | 400er-Schleifpapier | 0,10 bis 0,15 |
B-3 | Halbglänzend | Normal Halbglänzend | 320er-Schleifpapier | 0,28 bis 0,32 |
C-1 | Matt | Fein Matt | 600er-Körnung | 0,35 bis 0,40 |
C-2 | Matt | Mittelmatt | 400er-Körnung | 0,45 bis 0,55 |
C-3 | Matt | Normal Matt | 320er-Körnung, Stein | 0,63 bis 0,70 |
D-1 | Strukturiert | Satiniert | Trockenstrahlglasperlen | 0,80 bis 1,00 |
D-2 | Strukturiert | Stumpfe Textur | Trockenstrahl #240 Oxid | 1,00 bis 2,80 |
D-3 | Strukturiert | Grob strukturiert | Trockenstrahl #24 Oxid | 3,20 bis 18,0 |
Die VDI 3400-Standards verstehen
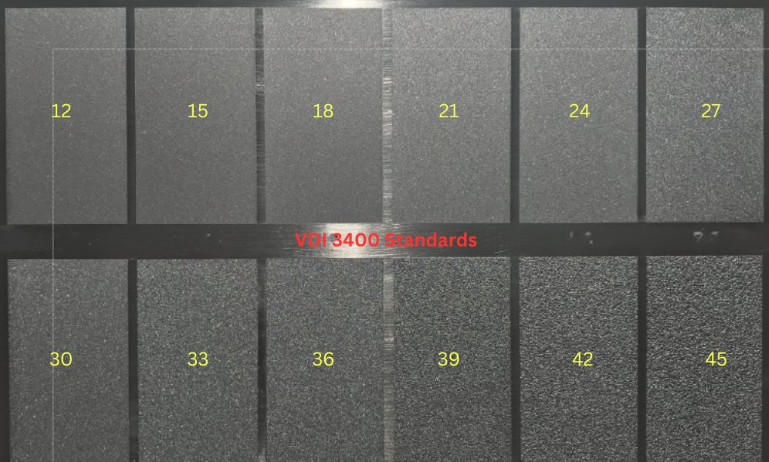
VDI 3400 Normen stammen aus der Verein Deutscher Ingenieure, der Verein Deutscher Ingenieure. Diese Normen umfassen eine Reihe von Texturen von sehr glatt bis stark strukturiert und ermöglichen eine präzise Kontrolle über die taktilen und visuellen Eigenschaften des Spritzgussteils. Im Gegensatz zu SPI verwendet VDI 3400 einen Satz 3D-Formen, die unterschiedliche Rauheitsgrade aufweisen, die bestimmten Qualitäten entsprechen, wie z. B. VDI 12 bis VDI 45. Diese physischen Muster ermöglichen einen einfachen Vergleich und eine einfache Auswahl. Die VDI 3400-Richtlinien gelten für verschiedene Materialien und Verarbeitungstechniken und eignen sich besonders zum Erzielen komplexer und detaillierter Texturen.
VDI-Wert | Beschreibung | Anwendungen | Oberflächenrauheit (Ra µm) |
VDI 12 | 600 Stein | Teile mit geringer Politur | 0.40 |
VDI 15 | 400 Stein | Teile mit geringer Politur | 0.56 |
VDI 18 | Trockenstrahlglasperlen | Satiniertes Finish | 0.80 |
VDI 21 | Trockenstrahl # 240 Oxid | Mattes Finish | 1.12 |
VDI 24 | Trockenstrahl # 240 Oxid | Mattes Finish | 1.60 |
VDI 27 | Trockenstrahl # 240 Oxid | Mattes Finish | 2.24 |
VDI 30 | Trockenstrahl # 24 Oxid | Mattes Finish | 3.15 |
VDI 33 | Trockenstrahl # 24 Oxid | Mattes Finish | 4.50 |
VDI 36 | Trockenstrahl # 24 Oxid | Mattes Finish | 6.30 |
VDI 39 | Trockenstrahl # 24 Oxid | Mattes Finish | 9.00 |
VDI 42 | Trockenstrahl # 24 Oxid | Mattes Finish | 12.50 |
VDI 45 | Trockenstrahl # 24 Oxid | Mattes Finish | 18.00 |
Mold-Tech-Standards für Oberflächenbeschaffenheit
Serie | Texturnummer | Texturtiefe (Zoll) | Strukturtiefe (mm) | Minimaler Entformungswinkel | Beschreibung |
MT-A | MT-11010 | 0.001″ | 0,0254 mm | 1,5° | Feines, mattes, sandähnliches Finish |
MT-A | MT-11020 | 0.0015″ | 0,0381 mm | 2,5° | Mittelmattes Finish |
MT-A | MT-11030 | 0.002″ | 0,0508 mm | 3° | Grobes, mattes Finish |
MT-A | MT-11040 | 0.003″ | 0,0762 mm | 4,5° | Sehr grobes, mattes Finish |
MT-A | MT-11050 | 0.0045″ | 0,1143 mm | 6,5° | Aggressives mattes Finish |
MT-B | MT-11200 | 0.003″ | 0,0762 mm | 4,5° | Geometrisches Muster |
MT-B | MT-11210 | 0.0035″ | 0,0889 mm | 5,5° | Geometrisches Muster |
MT-B | MT-11220 | 0.004″ | 0,1016 mm | 6° | Geometrisches Muster |
MT-D | MT-11550 | 0.0045″ | 0,1143 mm | 6,5° | Holzmaserung |
MT-D | MT-11555 | 0.006″ | 0,1524 mm | 9° | Grobe Holzmaserung |
Welchen Einfluss hat die Formstruktur auf das Spritzgussteil?
Die Formstruktur spielt eine entscheidende Rolle bei der Definition der Ästhetik und Funktionalität von Spritzgussteilen. Sie beeinflusst direkt die Oberflächenrauheit und kann bei unsachgemäßer Handhabung zu verschiedenen Produktionsproblemen führen.
Rolle der Formoberfläche beim Spritzgießen
Das Oberfläche einer Form ist ausschlaggebend für die Qualität eines Spritzgussteils. Während des Formprozesses überträgt das geschmolzene Kunststoffmaterial die Textur der Formoberfläche auf das Endprodukt. Der Grad der Politur auf der Formoberfläche kann die Lackhaftung beeinträchtigen; eine hochglanzpolierte Oberfläche führt zu einem glänzenden Finish, auf dem der Lack möglicherweise schwerer haftet, während eine strukturierte Oberfläche bietet eine bessere Farbhaftung. Ebenso können bestimmte Texturen das Auftreten von Unvollkommenheiten wie Fließlinien minimieren. Dabei handelt es sich um sichtbare Linien auf der Oberfläche des Formteils, die durch die unterschiedlichen Fließgeschwindigkeiten des geschmolzenen Kunststoffs entstehen.
Erreichen der gewünschten Oberflächenrauheit
Texturierungsprozesse erzeugen bestimmte Muster auf der Form, die auf die Teileoberfläche übertragen werden. Diese Muster können von sehr feinen Texturen, die den Glanz des Teils leicht verändern, bis zu starken Texturen reichen, die eine merkliche Rauheit erzeugen. Die Auswahl der Textur sollte mit dem Verwendungszweck des Teils und den Qualitätserwartungen an das Endprodukt übereinstimmen. Beispielsweise kann eine lederähnliche Textur im Autoinnenraum verwendet werden, um einen besseren Griff und ein luxuriöses Gefühl zu erzielen.
Häufige Probleme und Lösungen bei Formoberflächen
Fließlinien
Fließlinien erscheinen als wellenförmige Muster oder verfärbte Streifen auf der Oberfläche des Formteils. Sie entstehen durch Schwankungen in der Abkühlungsgeschwindigkeit des Materials, da es mit unterschiedlicher Geschwindigkeit durch die Form fließt.
Lösungen:
- Erhöhen Sie die Einspritzgeschwindigkeit, den Druck und die Materialtemperatur, um sicherzustellen, dass sich die Form vor dem Abkühlen füllt.
- Runden Sie die Ecken der Form ab, wo die Wandstärke zunimmt, um die Durchflussrate konstant zu halten
- Verschieben Sie die Formöffnungen, um mehr Abstand zum Formkühlmittel zu schaffen und so eine frühzeitige Abkühlung während des Fließens zu verhindern.
Spritzen
Das Spritzen äußert sich in wurmartigen Wirbeln in der Nähe von dicken Angussbereichen. Es wird durch Temperaturschwankungen im Materialfluss verursacht, häufig aufgrund zu kleiner Angussöffnungen oder zu hoher Einspritzgeschwindigkeiten.
Lösungen:
- Erhöhen Sie die Torgröße und ändern Sie die Seitentore in Überlappungstore.
- Reduzieren Sie die Einspritzgeschwindigkeit, um eine übermäßige Schererhitzung des Materials zu verhindern
Einfallstellen
Einfallstellen sind kleine Vertiefungen oder Grübchen, die in dickeren Querschnitten des Teils auftreten. Sie entstehen, wenn der innere Teil schneller abkühlt und schrumpft als der äußere Teil.
Lösungen:
- Erhöhen Sie den Einspritzdruck und den Haltedruck, um eine ordnungsgemäße Verdichtung sicherzustellen
- Erhöhen Sie die Gate-Größe oder ändern Sie die Gate-Position
- Gestalten Sie das Teil neu, um eine gleichmäßigere Wandstärke zu erzielen, wobei Rippen und Vorsprünge 60% der Nennstärke nicht überschreiten dürfen.
Wie wählen Sie die richtige Oberflächenbeschaffenheit für Ihr Spritzgussteil?
Anpassung der Oberflächenbeschaffenheit an die Produktanforderungen
Die Endverwendung des Produkts bestimmt die Oberflächenausführungen. Bei Artikeln, die eine hohe Ästhetik erfordern, wie z. B. Konsumgüter, kann eine glänzende Oberfläche erforderlich sein. Umgekehrt können strukturierte Oberflächen für eine bessere Griffigkeit oder Farbhaftung bei Industrieteilen von Vorteil sein. SPI-Oberflächen (Normen der Society of the Plastics Industry) wie SPI A-2 werden häufig verwendet, wenn eine Hochglanzpolitur erforderlich ist, während für nicht kosmetische Komponenten eine SPI C-1-Beschichtung ausreichen kann.
Entformungsschräge
Um eine ordnungsgemäße Entformung zu gewährleisten, ist es unerlässlich, den richtigen Entformungswinkel in das Teiledesign einzubeziehen. Ein steilerer Entformungswinkel erleichtert das Entformen, was die Verwendung aggressiverer Texturen ermöglichen kann, ohne die Teileintegrität zu gefährden.
Formmaterial
Das gewählte Formmaterial beeinflusst die erreichbare Oberflächenbeschaffenheit. Härtere Kunststoffe können höhere Glanzgrade erreichen, während weichere Materialien möglicherweise einen anderen Ansatz erfordern, um ähnliche Effekte zu erzielen. Teiledesigner müssen verstehen, wie das Material mit der Oberfläche interagiert, um die gewünschte Qualität zu erreichen.
Werkzeugkosten
Höhere Oberflächengüten erhöhen die Werkzeugkosten aufgrund der längeren Bearbeitungs- und Polierzeit. Produktdesigner müssen die ästhetischen Anforderungen mit der wirtschaftlichen Machbarkeit in Einklang bringen und dabei bedenken, dass bestimmte Oberflächen komplexere und arbeitsintensivere Werkzeugprozesse erfordern.
Formwerkzeugmaterial
Das Material des Formwerkzeugs bestimmt seine Langlebigkeit und den Detailgrad, den es vermitteln kann. Für lange Produktionsläufe oder hochdetaillierte Oberflächen ist robuster Werkzeugstahl von Vorteil. In Szenarien, in denen Kosteneinsparungen von größter Bedeutung sind, können Aluminiumformen verwendet werden, mit der Einschränkung, dass sie schneller verschleißen oder nicht den gleichen Detailgrad wie Stahl erreichen können.