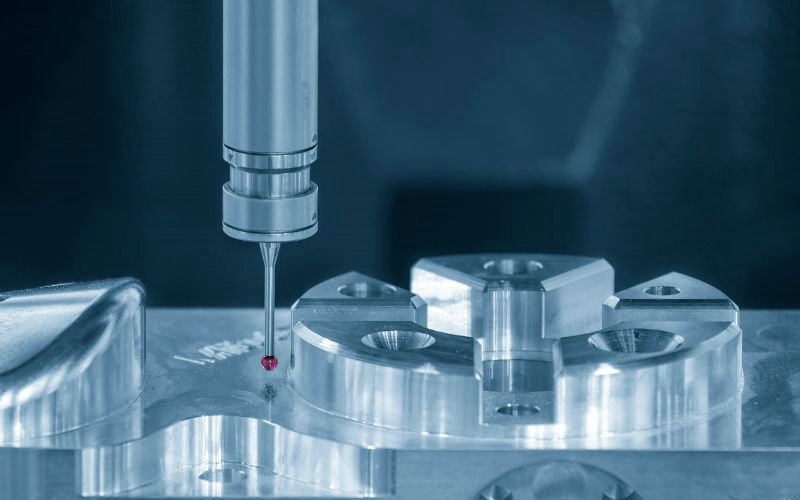
Spritzguss ist eines der am häufigsten verwendeten Fertigungsverfahren zur Herstellung großer Stückzahlen von Kunststoffteilen. Um eine gleichbleibende Teilequalität und optimale Produktionseffizienz zu gewährleisten, Formtemperatur ist einer der kritischsten Faktoren, die kontrolliert werden müssen. Die Temperatur der Form hat einen erheblichen Einfluss auf das Fließverhalten der Kunststoffschmelze während des Füllens und die Abkühlgeschwindigkeit des Teils. Wenn die Form zu kalt ist, kann die Schmelze die Kavität nur schwer vollständig füllen, was zu kurzen Spritzern oder anderen Defekten führt. Umgekehrt dauert es länger, bis der Kunststoff fest wird, wenn die Form zu heiß ist, was die Zykluszeiten verlängert. In diesem Beitrag helfen wir Ihnen, tiefere Einblicke in die Auswirkungen der Temperatur auf das Spritzgießen zu gewinnen und spezifische Maßnahmen zu ergreifen, um die Formtemperatur besser zu kontrollieren.
Erläuterung von Werkzeugtemperatur-Regelsystemen
Komponenten eines Werkzeugtemperatur-Kontrollsystems
Ein Formtemperatur-Regelsystem besteht aus mehreren Schlüsselkomponenten, die zusammenarbeiten:
- Elektronisches Steuerungssystem: Verarbeitet Informationen aus anderen Systemen und gibt Befehle aus
- Mechanisches System (Umwälzpumpe): Überträgt Wärme vom Heizsystem zur Form
- Füllstandsüberwachungssystem: Überwacht den Kühlmittelstand und signalisiert Nachfüllungen
- Heizsystem: Erwärmt das Kühlmittel auf die eingestellte Temperatur
- Kühlsystem: Entfernt überschüssige Wärme, oft durch den Einsatz von Plattenwärmetauschern zur indirekten Kühlung.
- Temperatursensorsystem: Misst die Formtemperatur und leitet die Daten an das Steuerungssystem weiter
- Druckentlastungs-Sicherheitssystem: Lässt den Druck ab und entlastet ihn, wenn er zu hoch wird
Arten von Formtemperaturreglern
Abhängig vom verwendeten Heizmedium gibt es zwei Haupttypen von Werkzeugtemperaturreglern:
1. Wassertemperaturregler
– Temperaturbereich im Allgemeinen innerhalb 180°C
– Normale Ausführung: bis 120°C, Hochtemperaturausführung: bis 180°C
2. Öltemperaturregler
– Wird für Temperaturen über 180°C bis 350°C verwendet
– Normale Ausführung: bis 200°C, Hochtemperaturausführung: bis 350°C
Arbeitsprinzip
Hier ist eine vereinfachte Erklärung der Funktionsweise eines Wasser-Formtemperaturreglers:
1. Die Umwälzpumpe pumpt Wasser durch das System
2. Das Heizsystem erwärmt das Wasser auf die eingestellte Temperatur
3. Heißes Wasser fließt durch Kanäle in der Form und überträgt Wärme
4. Das Temperatursensorsystem misst die Formtemperatur
5. Wenn die Temperatur zu niedrig ist, signalisiert das Steuersystem der Heizung, sich einzuschalten
6. Wenn die Temperatur zu hoch ist, entfernt das Kühlsystem überschüssige Wärme
7. Das Druckentlastungssystem lässt Kühlmittel ab, wenn der Druck gefährlich hoch wird
Durch die präzise Steuerung der Formtemperatur tragen diese Systeme dazu bei, Defekte zu minimieren, Zykluszeiten zu optimieren und die Gesamtqualität und -konsistenz der Teile beim Spritzgießen zu verbessern. Die Investition in ein gutes, auf Ihre spezifischen Formanforderungen zugeschnittenes System zur Formtemperaturregelung kann zu erheblichen Effizienzsteigerungen in der Fertigung führen.
Einfluss der Formtemperatur auf das Spritzgießen
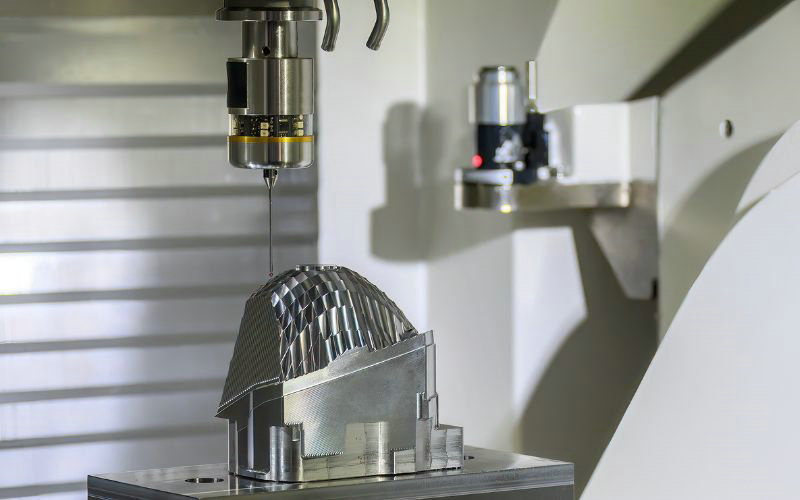
Auswirkungen niedriger Formtemperatur
1. Schlechtes Erscheinungsbild und Finish der Oberfläche
- Eine niedrige Formtemperatur verringert die Fließfähigkeit der Kunststoffschmelze, was insbesondere bei Materialien wie ABS zu einer unvollständigen Füllung und einer weniger glänzenden Oberflächenbeschaffenheit führen kann.
- Wenn die Formtemperatur für strukturierte Oberflächen zu niedrig ist, kann es sein, dass die Schmelze die feinen Details der Struktur nicht vollständig ausfüllt, was zu einer schlechten Nachbildung der Formoberfläche führt.
2. Erhöhte innere Spannungen und Verzug
- Eine niedrige Formtemperatur führt zu einer schnellen Abkühlung und zum „Einfrieren“ der Moleküle, wodurch sich im Teil innere Spannungen aufbauen.
- Ungleichmäßiges Abkühlen und Schrumpfen aufgrund niedriger Formtemperaturen können zu Verzug und Maßinstabilität des Formteils führen.
- Auf der Oberfläche des Teils können sich sichtbare Schweißnähte bilden, die die Festigkeit verringern.
3. Änderungen der mechanischen Eigenschaften
- Niedrige Formtemperaturen können die Zugfestigkeit des Formteils im Vergleich zu höheren Formtemperaturen verringern.
- Eine schnelle Abkühlung bei niedrigen Temperaturen kann die Sprödigkeit des Teils erhöhen und seine Schlagfestigkeit und Ermüdungsbeständigkeit verringern.
4. Längere Zykluszeiten
- Obwohl niedrige Formtemperaturen die Abkühlzeit verkürzen können, erfordern sie aufgrund der verringerten Fließfähigkeit der Schmelze einen höheren Einspritzdruck zum Füllen der Kavität.
- Dies kann die Gesamtzykluszeit verlängern, insbesondere bei kristallinen Materialien, die für die Dimensionsstabilität eine ausreichende Kühlung erfordern.
Auswirkungen hoher Formtemperaturen
1. Verbesserte Oberflächenbeschaffenheit und Optik
- Bei einer höheren Formtemperatur kann der Kunststoff leichter fließen und feine Oberflächendetails ausfüllen. Das Ergebnis ist eine glänzendere, ansprechendere Oberflächenbeschaffenheit, insbesondere bei Materialien wie ABS.
- Bei höheren Temperaturen befindet sich die Kunststoffzusammensetzung näher an der Formoberfläche, was zu einer besseren Texturwiedergabe führt.
2. Verbesserte mechanische Eigenschaften
- Höhere Formtemperaturen können die Zugfestigkeit des Formteils im Vergleich zu niedrigeren Formtemperaturen verbessern.
- Bei kristallinen Kunststoffen steht durch eine hohe Formtemperatur mehr Zeit für die Kristallisation zur Verfügung, was wiederum die Steifigkeit und Hitzebeständigkeit des Teils erhöht.
3. Reduzierte innere Spannungen und Verzug
- Hohe Formtemperaturen verlangsamen den Abkühlungsprozess, sodass sich die Moleküle entspannen und gleichmäßiger ausrichten können. Dies führt zu einer Reduzierung der Restspannungen im Teil.
- Durch eine allmählichere Abkühlung bei höheren Formtemperaturen werden unterschiedliche Schrumpfungen und Verformungen des Formteils minimiert.
4. Längere Zykluszeiten und höheres Fehlerpotenzial
- Der Hauptnachteil hoher Formtemperaturen besteht in der längeren erforderlichen Abkühlzeit, die die Gesamtzykluszeit verlängert und die Produktivität verringert.
- Zu hohe Temperaturen können dazu führen, dass der Kunststoff an der Form kleben bleibt und helle Flecken oder andere Oberflächenfehler entstehen.
- Bei zu hoher Formtemperatur besteht ein größeres Risiko zur Gratbildung, da der Kunststoff länger geschmolzen bleibt.
5. Mögliche Verschlechterung der Materialeigenschaften
- Bei manchen Polymeren kann es bei der Verarbeitung bei zu hohen Formtemperaturen zu thermischem Abbau oder Oxidation kommen, was zu einer Verringerung des Molekulargewichts und der mechanischen Eigenschaften führt.
- Die Kombination aus hoher Formtemperatur, hoher Schmelztemperatur und langer Verweilzeit birgt das größte Risiko einer Materialzerstörung während des Formens.
Maßnahmen zur besseren Kontrolle der Formtemperatur
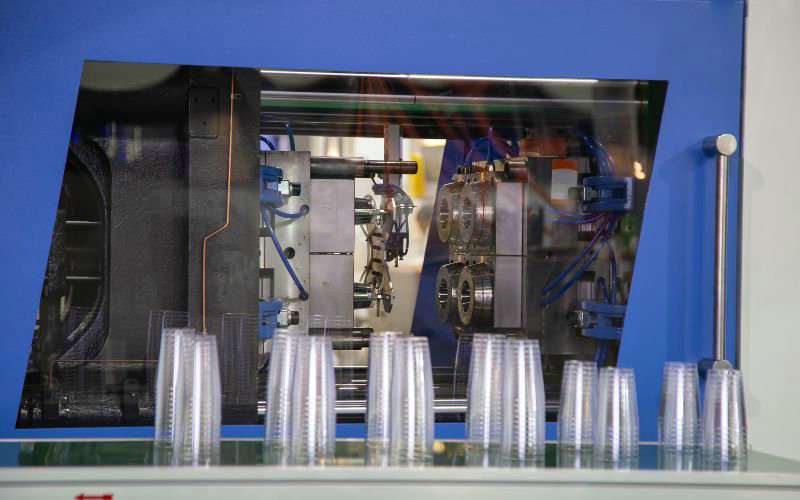
1. Verwenden Sie Formtemperaturregler
- Formtemperaturregler sind wichtige Geräte zur Regulierung und Aufrechterhaltung präziser Formtemperaturen. Sie dienen sowohl zum Heizen als auch zum Kühlen.
- Wählen Sie einen Formtemperaturregler mit ausreichender Durchflussrate und Druckkapazität, um die Anforderungen Ihrer spezifischen Form zu erfüllen.
2. Kühlmitteldurchflussraten überwachen
- Eine ausreichende Kühlmitteldurchflussrate ist von entscheidender Bedeutung, da sie bestimmt, wie schnell die Form abgekühlt werden kann, was sich sowohl auf die Produktqualität als auch auf die Zykluszeit auswirkt.
- Überprüfen Sie, dass die Durchflussrate weder zu niedrig ist, da dies zu einer schlechten Temperaturregelung führen kann, noch zu hoch, da dies zu Verschwendung und Ineffizienz führen kann.
3. Richten Sie eine Temperaturgradientenkontrolle ein
- Halten Sie die Temperatur in der gesamten Form konstant, um Defekte zu vermeiden. Eine geeignete Temperaturgradientenregelung minimiert innere Spannungen im Formteil.
- Um Verzug zu vermeiden, sollten Formenkonstrukteure einen Temperaturunterschied von nicht mehr als 5 °C zwischen Kern und Hohlraum anstreben.
4. Optimieren Sie das Kühlkanaldesign
- Die Lage, Tiefe und Neigung der Kühlkanäle haben einen erheblichen Einfluss auf die Gleichmäßigkeit der Formoberflächentemperatur.
- Streben Sie eine gleichmäßige Oberflächentemperatur der Form an, indem Sie die Tiefe des Kühlkanals (idealerweise das 1- bis 2,5-fache des Kanaldurchmessers) und die Steigung (2,5- bis 3-fache des Kanaldurchmessers) optimieren.
5. Wählen Sie geeignete Formmaterialien
- Das Formmaterial hat einen erheblichen Einfluss auf den Wärmeaustausch. Berücksichtigen Sie bei der Auswahl des Formmaterials die Wärmeleitfähigkeit.
- Bei Anwendungen mit hohen Toleranzen können Kupferlegierungen erforderlich sein, um einen niedrigen Temperaturunterschied aufrechtzuerhalten und Verzug zu reduzieren, während für Teile mit niedrigeren Toleranzen weniger teure Materialien wie H13-Stahl verwendet werden können.
6. Implementieren Sie schnelle Heiz- und Kühltechniken
- Beim Rapid Heat Cycle Molding (RHCM) wird die Form schnell über den Schmelzpunkt erhitzt, um den Kunststofffluss zu erleichtern, und dann schnell abgekühlt, um die Verfestigung zu beschleunigen.
- RHCM kann die Oberflächenqualität und -präzision verbessern, ist jedoch energieintensiv und sollte speziellen Anwendungen vorbehalten bleiben.
Durch die Umsetzung dieser Maßnahmen und die kontinuierliche Überwachung der Formtemperatur können Spritzgießer diesen kritischen Prozessparameter besser kontrollieren. Dies führt zu einer verbesserten Teilequalität, weniger Defekten und optimierten Zykluszeiten für eine höhere Fertigungseffizienz.
Spritzgusstemperatur für verschiedene Kunststoffe
In der folgenden Tabelle sind die empfohlenen Spritzgusstemperaturen für verschiedene Kunststoffe zusammengefasst:
Kunststofftyp | Material | Schmelztemperatur (°C) | Formtemperatur (°C) |
---|---|---|---|
Amorphe Kunststoffe | Abs | 210-275 | 50-90 |
PS | 170-280 | 10-60 | |
PMMA | 180-260 | 50-80 | |
PC | 280-320 | 80-120 | |
Teilkristalline Kunststoffe | PP | 200-280 | 30-80 |
HDPE | 210-300 | 20-70 | |
aus LDPE | 160-260 | 20-70 | |
POM | 160-280 | 50-120 | |
PA6 | 230-290 | 40-120 | |
PA66 | 260-300 | 40-120 | |
PBT | 240-275 | 60-100 | |
Hochtemperatur-Kunststoffe | PES | 330-380 | 120-180 |
SPÄHEN | 340-390 | 120-160 |
Hinweis: Der optimale Formtemperaturbereich hängt von der jeweiligen Qualität, den Zusatzstoffen, der Teilegeometrie, dem gewünschten Eigenschaftsgleichgewicht und der Zykluszeit ab. Eine sorgfältige Kontrolle der Schmelze- und Formtemperatur ist entscheidend, um beim Spritzgießen eine hohe Teilequalität und Fertigungseffizienz zu erreichen.