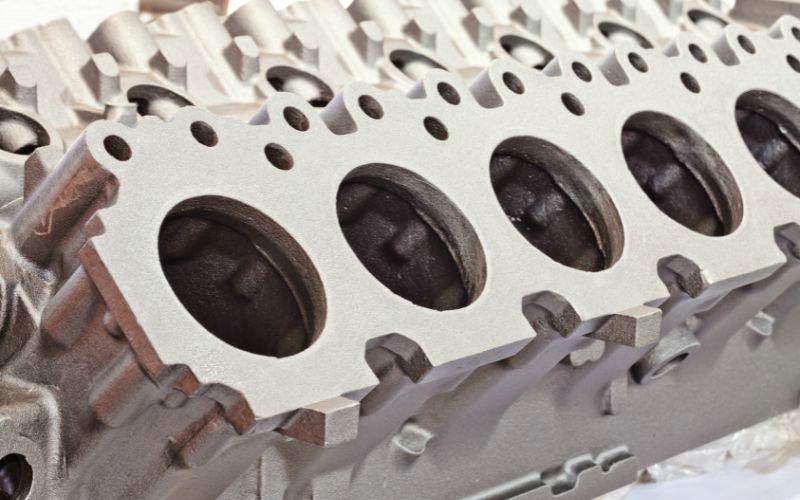
Шта је ливење под притиском?
Ливење под притиском је производни процес који укључује изливање или убризгавање растопљеног метала у калупе, познато као умире. Метал који се обично користи у овом процесу може укључивати цинк, алуминијум и њихове легуре. Ваше је путовање кроз процедуру која је широко прихваћена због своје ефикасности у великим серијама производње.
Када започнете ливење под притиском, метал се топи у пећи, а затим се убризгава у калупе под високим притиском. Ова метода је популарна због своје способности да производи делове са прецизношћу, замршеним детаљима и одличном завршном обрадом површине – квалитетима који се захтевају у секторима као што су аутомобилска индустрија, ваздухопловство и електроника.
Ливење под притиском је веома тражено од стране произвођача због своје способности да произведе уједначене делове доследног квалитета. Без обзира да ли га користите за креирање сложених компоненти мењача за возила или елегантних, издржљивих кућишта за електронику, постоља за ливење под притиском представљају стуб модерне производње, посебно када су прецизност и запремина од суштинске важности.
Процес ливења под притиском
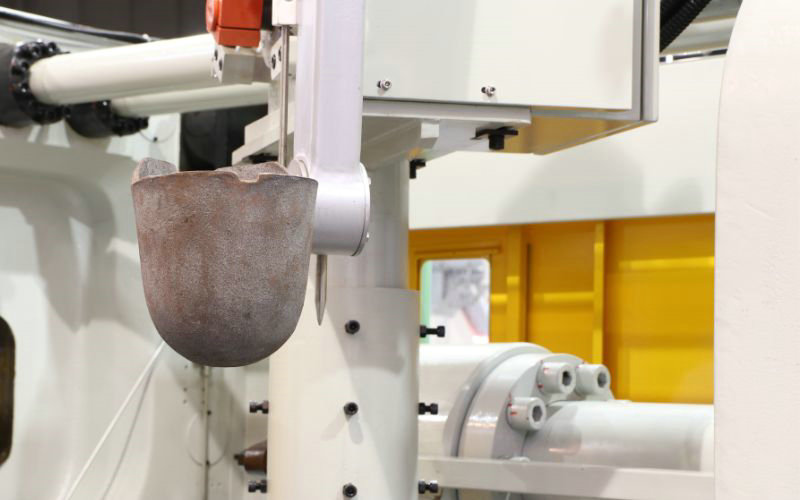
Постоје три главна типа процеса ливења под притиском: ливење под притиском, ливење у хладној комори и ливење у топлој комори.
Гравитационо ливење под притиском
У гравитационом ливењу под притиском, растопљени метал се сипа директно из кутлаче у полутрајну или трајну матрицу. Шупљина се не испуњава никаквом другом силом осим гравитацијом. Предности гравитационог ливења под притиском укључују могућност производње густих, висококвалитетних одливака са одличним механичким својствима погодним за термичку обраду. Исплативо је за производњу мале и средње количине.
ливење под притиском у хладној комори
Код ливења под притиском у хладној комори, пећ за топљење се налази одвојено од машине за ливење под притиском. За сваки циклус, прецизна количина растопљеног метала се улива у незагрејану комору машине; затим, хидраулични клип гура метал у калуп под високим притисцима између 2.000-20.000 пси. Ливење у хладној комори се користи за легуре са вишим тачкама топљења као што је алуминијум. Производи јаке, издржљиве делове, али има спорије време циклуса од вруће коморе.
ливење под притиском у врућој комори
Код ливења под притиском у врућој комори, механизам за убризгавање је потопљен у базену истопљеног метала, који се убацује у калуп кроз гуски врат и клип. На почетку сваког циклуса, клип се увлачи, омогућавајући гушчјој врату да се напуни растопљеним металом. Клип затим гура метал кроз гуски врат у калуп под притиском од 1.000-5.000 пси. Ливење у врућој комори се користи за легуре са ниским тачкама топљења као што су цинк и магнезијум. Омогућава краће време циклуса и може произвести сложене делове са смањеном порозношћу.
Примене за ливење под притиском
Аутомобили: Ливење под притиском се широко користи у аутомобилском сектору. Пронаћи ћете компоненте као што су блокови мотора, делови мењача и структурни елементи направљени кроз овај процес. Способност да се брзо и ефикасно произведу јаки, издржљиви делови чине ливење под притиском избором за аутомобилске инжењере.
- Мотор Цомпонентс
- Мењач
- Цар Фрамес
Ваздухопловство: Ваздухопловна индустрија цени ливење под притиском за стварање сложених делова који захтевају прецизност и може да издржи тешке услове. Компоненте као што су стајни трап, инструментација у кокпиту и делови мотора се обично ливеју под притиском.
- Кућишта за инструменте
- Делови стајног трапа
- Мотор Цомпонентс
Електроника: У електроници, ливење под притиском се користи за креирање предмета као што су конектори, кућишта и хладњаци. Ови делови имају користи од способности ливења под притиском да формирају сложене дизајне са високим нивоом топлотне проводљивости.
- Хеат Синкс
- Конектори
- Енцлосурес
Шта је бризгање метала?
Метал Ињецтион Молдинг (МИМ) нуди вам производни процес за производњу сложених делова у средњим до великим количинама. МИМ комбинује слободу дизајна и сложеност облика који се налазе у бризгању пластике са изузетном снагом и интегритетом метала.
Ево сажетог прегледа МИМ-а:
- Материјали: Ваш избор материјала у МИМ-у обично укључује црне метале као што је нерђајући челик, који обезбеђује значајну снагу и издржљивост коначном производу.
- Снага и прецизност: МИМ делови су познати по импресивној снази и прецизности. Одржавају чврсте толеранције, што их чини погодним за обоје индустријским и медицински апликације.
- Сложене геометрије и танки зидови: Са МИМ-ом, можете да креирате делове са сложеном геометријом и танким зидовима, што може бити изазовно или немогуће кроз традиционалне процесе обраде метала.
Процес бризгања метала
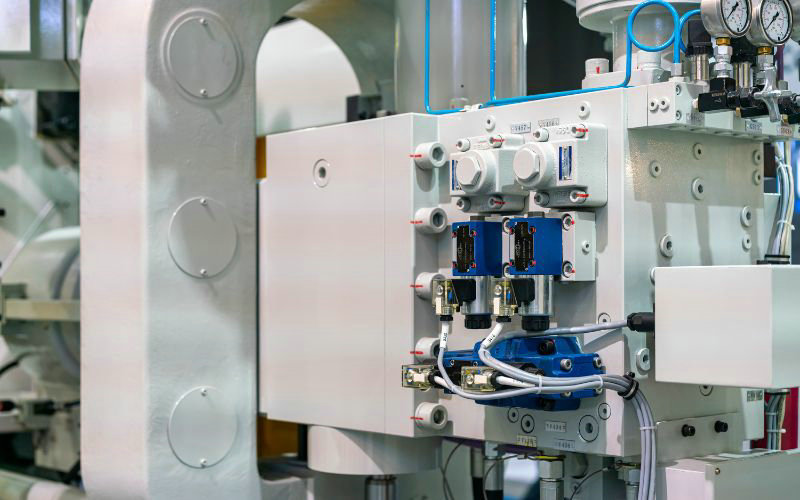
Ваше разумевање МИМ-а почиње са његовим примарним материјалом — а сировина који се састоји од финог металног праха и полимерног везивног материјала. Уобичајени метали који се користе у овом процесу укључују нерђајући челик, титанијум, легуре никла и легуре бакра. У својим почетним фазама, МИМ је сличан бризгању пластике; сировина се загрева док не постане вискозна и може се убризгати у шупљину калупа.
Када је ваш обликовани део постављен, почиње процес одвезивања. Ово подразумева уклањање већег дела везива, чиме се део припрема за синтеровање. Током синтеровања, ваш део је изложен високим температурама које спајају металне честице и обезбеђују интегритет.
Након синтеровања, видећете да се део значајно смањио — обично између 15-201ТП3Т. Међутим, процес синтеровања вам омогућава да постигнете одличну тачност димензија и завршну обраду површине, често минимизирајући потребу за накнадном машинском обрадом. МИМ је веома исплатив када је у питању производња малих делова у великим количинама због мањег отпада материјала и могућности одржавања чврстих толеранција без обимних завршних радова.
На крају крајева, бризгање метала нуди јединствен спој квалитета, ефикасности и свестраности у производним процесима. Његова способност да користи различите метале и постигне специфичне карактеристике материјала — као што су тврдоћа, затезна чврстоћа и температурна отпорност — чини га вредним процесом у бројним индустријама.
Примене за бризгање метала (МИМ).
Ињекционо бризгање метала (МИМ) је прецизно и исплативо, а посебно је погодно за масовну производњу малих и средњих компоненти. Наћи ћете МИМ апликације у различитим индустријама због његове способности да производи сложене облике са одличном завршном обрадом површине.
Ваздухопловство и аутомобилска индустрија:
- МИМ је идеалан за производњу делова као што су ручке на вратима, шарке и компоненте мотора због своје високе чврстоће и издржљивости.
Медицина и стоматологија:
- Медицинска индустрија има користи од МИМ-ове прецизности у креирању хируршких алата, имплантата и бравица који захтевају биокомпатибилност.
Потрошачка електроника:
- Мале компоненте као што су делови мобилних телефона или склопови камера искоришћавају МИМ-ову снагу у минијатуризацији и могућностима детаљног дизајна.
Индустрија ватреног оружја:
- МИМ се користи за производњу различитих компоненти ватреног оружја, укључујући окидаче, чекиће и делове нишана који захтевају строге толеранције и снагу.
Општа индустријска опрема:
- Наћи ћете МИМ у производњи компоненти пумпи, конектора и вентила због његових производних могућности и конзистентности великог обима.
У овим апликацијама, МИМ пружа предности које укључују:
- Материјали високе густине са одличним механичким својствима
- Способност интеграције функција као што су навоји, зупчаници и унутрашњи канали без секундарних операција
- Производња делова близу коначног облика, минимизирајући отпад
Ливење под притиском против МИМ: предности и недостаци
Предности МИМ-а у односу на ливење под притиском
1. МИМ може да произведе мале, сложене делове са сложеним карактеристикама и танким зидовима који би били изазовни или немогући ливењем под притиском.
2. МИМ нуди шири спектар материјала, укључујући црне метале, нерђајући челик, титанијум и легуре никла. Ливење под притиском је обично ограничено на обојене метале као што су алуминијум, цинк и магнезијум.
3. МИМ делови имају одличне механичке особине, високу чврстоћу и отпорност на хабање због процеса синтеровања.
4. МИМ обезбеђује веће толеранције и може бити тачан до 0,3 мм.
5. МИМ практично нема отпада јер се сав материјал убризгава директно у калуп.
Недостаци МИМ-а у поређењу са ливењем под притиском
1. МИМ је генерално скупљи од ливења под притиском због сложене алатке и вишеструких корака обраде.
2. МИМ има краћи век трајања калупа (150к-300к снимака) у поређењу са ливењем под притиском (преко 1 милион снимака).
3. МИМ делови могу значајно да се скупе (до 301ТП3Т) током синтеровања, што захтева пажљив дизајн калупа. Ливење под притиском има много мање скупљање.
4. МИМ има високе почетне трошкове аутоматизације и подешавања.
Предности ливења под притиском у односу на МИМ
1. ливење под притиском је обично јефтиније од МИМ-а, до 301ТП3Т јефтиније у неким случајевима.
2. ливење под притиском има дужи век трајања (преко 1 милион снимака) у поређењу са МИМ (150к-300к снимака).
3. Ливење под притиском не захтева никакве секундарне операције након што се део избаци из калупа.
4. ливење под притиском може да прими уметке и делове направљене од других материјала уграђених у ливење.
Недостаци ливења под притиском у поређењу са МИМ-ом
1. ливење под притиском се бори са производњом малих, замршених делова са финим карактеристикама и танким зидовима.
2. ливење под притиском ограничено је углавном на обојене метале. Гвоздени метали имају веома високе тачке топљења, што смањује животни век матрице.
3. Порозност због заробљених гасова је чест проблем код ливења под притиском, смањујући механичку чврстоћу.
4. Ливење под притиском захтева скупе калупе да издрже висок притисак и температуре растопљеног метала.
Укратко, МИМ се истиче у производњи малих, сложених делова са одличним механичким својствима у широком спектру материјала. Међутим, скупљи је и има дужи циклус од ливења под притиском. Ливење под притиском је економичније и погодније за једноставније, веће делове од обојених метала са бржим временом производње, али се бори са сложеним карактеристикама и порозношћу.
Поређење: бризгање метала у односу на ливење под притиском
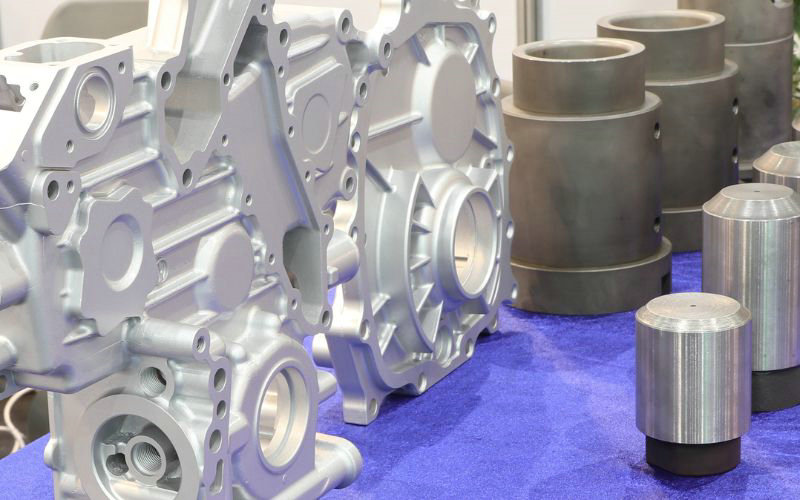
1. Тачност и толеранције
бризгање метала (МИМ): МИМ постиже веома прецизне делове са релативно малим толеранцијама, обично тачно до 0,3 мм. Ова прецизност је захваљујући коришћеном фином металном праху који омогућава детаљне и сложене геометрије.
Дие Цастинг: ливење под притиском генерално нуди добру тачност димензија, али не тако високу као МИМ. Типична толеранција за ливење под притиском је око ±0,0005 инча, што је мање прецизно у поређењу са МИМ-овим могућностима. Варијације у димензијама често захтевају додатно обрезивање да би се испуниле спецификације.
2. Потребни материјали
бризгање метала (МИМ): МИМ може да користи широк спектар материјала, укључујући црне и обојене метале, нерђајући челик, титанијум и легуре никла. Ова свестраност омогућава производњу делова са специфичним својствима прилагођених различитим применама.
Дие Цастинг: Првенствено користи обојене метале као што су алуминијум, цинк и магнезијум. Док ливење под притиском може да користи црне метале, ови материјали имају веома високе тачке топљења, што може значајно смањити век трајања калупа.
3. Поређење брзине
бризгање метала (МИМ): МИМ процес укључује више корака, укључујући мешање, бризгање, уклањање везивања и синтеровање, што га чини генерално споријим од ливења под притиском. Међутим, када се производња успостави, МИМ може ефикасно да производи велике количине делова.
Дие Цастинг: Познато по својој брзој производној способности, ливење под притиском је брже, посебно погодно за велике серије производње. Процес омогућава брзо стварање великих делова захваљујући техникама убризгавања под високим притиском.
4. Завршна обрада
бризгање метала (МИМ): Обично пружа висококвалитетну завршну обраду површине која често не захтева додатну накнадну обраду. Процес синтеровања помаже у постизању глатке завршне обраде.
Дие Цастинг: Делови обично излазе из калупа са добром завршном обрадом површине, али може бити потребно одрезање вишка метала. Квалитет површине се генерално сматра средњим у поређењу са МИМ-ом.
5. Трошкови производње
бризгање метала (МИМ): Иако почетно подешавање и трошкови алата могу бити високи, МИМ може бити исплатив за производњу сложених делова у великим количинама због смањеног отпада и минималних потреба за накнадном обрадом.
Дие Цастинг: Генерално јефтиније у смислу почетних трошкова и исплативије је за веће делове и производњу великог обима. Међутим, економичност се смањује за веома сложене или мање делове.
6. Разлике у калупу
бризгање метала (МИМ): Калупи који се користе у МИМ-у могу бити мање издржљиви у поређењу са ливењем под притиском, обично подржавају око 150.000 до 300.000 снимака. Међутим, МИМ калупи омогућавају већу сложеност у дизајну делова.
Дие Цастинг: Калупи су дизајнирани да издрже високе притиске и температуре, што их чини издржљивијим, са животним веком од преко 1 милион снимака. Међутим, они нуде мању флексибилност у смислу сложености делова у поређењу са МИМ калупима.