A maior quantidade de molde de injeção de plástico que pode ser injetada durante um ciclo de moldagem é conhecida como tamanho de injeção. Os pellets são alimentados no barril e no conjunto do parafuso através da tremonha.
Usando a técnica de moldagem por injeção, o material fundido é injetado na cavidade do molde para criar grandes quantidades de peças plásticas.
No processo de moldagem por injeção de plástico, a matéria-prima é introduzida no barril, derrete e o plástico é injetado na cavidade do molde para resfriamento e solidificação após o fechamento do molde. Por fim, o molde se abre e os componentes são expelidos.
Como Calcular o Tamanho do Shot
A duração dos tempos de residência é influenciada pelo tamanho do tiro e do cano, o que também pode afetar a qualidade do produto final. Longas durações de residência e degradação do polímero podem vir de pequenos tamanhos de tiro que requerem pouca capacidade de barril.
Pequenos tamanhos de granalha que ocupam menos de 20% da capacidade do barril freqüentemente resultam em tempos de residência prolongados, o que, por sua vez, causa degradação do polímero e controle inadequado do processo.
Por outro lado, tamanhos grandes e níveis de preenchimento de barril maiores que 50% podem causar derretimento desigual e recuperação lenta da rosca.
Além disso, parafusos maiores normalmente têm capacidades de pressão de plástico mais baixas. Grandes tamanhos de granalha, que ocupam mais de 65% da capacidade do barril, frequentemente causam problemas de qualidade do fundido, como não fusão, baixa uniformidade do fundido e longos tempos de recuperação da rosca.
Para estar seguro, você pode considerar fazer um pedido de dois barris. Ainda mais, moldes podem ser usados com dois barris. Quando você pede um segundo barril com a nova máquina, pode ficar agradavelmente satisfeito com seu baixo custo. Os barris podem ser trocados em menos de 30 minutos com as especificações corretas e um operador experiente, mesmo que o barril esteja quente.
Fórmula para tamanho de injeção de molde em moldagem por injeção
A fórmula mais simples para calcular o tamanho do molde é:
Encolhimento + volume do abeto + volume do produto + volume do corredor = tamanho do molde
Capacidade/tamanho do disparo da máquina de fórmula
O peso ou volume total que a rosca injeta durante um ciclo de moldagem é expresso como capacidade de injeção da máquina (g)/tamanho da injeção da máquina (mm), também conhecida como capacidade de injeção da máquina.
Seus cálculos ao considerar a pressão devem ser os seguintes:
Curso X Superfície do pistão parafuso = volume de injeção
Força de injeção/superfície do pistão do parafuso = pressão de injeção
Portanto:
Volume máximo de injeção por unidade cúbica X pressão máxima de injeção (bar por unidade cúbica)/1000 = capacidade de injeção da unidade de injeção.
Os cálculos ao usar o peso do parafuso e a densidade do material devem ser os seguintes:
Massa/densidade = volume
ᴨ*D2*Tamanho do tiro/4= Barril/Volume do tiro
Fatores que afetam o tamanho da injeção do produto
Existem vários fatores que você deve considerar ao calcular o tamanho de uma tomada. Esses fatores são os seguintes:
- Você deve considerar o volume do abeto, o volume do corredor e o volume do produto ao determinar o tamanho da injeção. Isso ocorre porque o polímero deve preencher o volume do abeto, canal e produto quando injetado no molde.
- Outra questão importante que afeta os cálculos do tamanho da granalha é a contração do polímero. O encolhimento resulta do resfriamento do polímero fundido. Devido às densidades variadas de polímeros, o encolhimento do molde varia.
- O tipo e a quantidade de aditivos de um polímero podem alterar sua densidade e características de fluxo.
Esses fatores podem ajudá-lo a estimar o tamanho do disparo, volume e capacidade do cano.
Unidade de Injeção
O objetivo da unidade de injeção é fundir o material plástico uniformemente antes de injetá-lo no molde a uma pressão e vazão predeterminadas. Essas são atividades exigentes porque os fluoropolímeros têm condutividade térmica limitada, alto calor específico e alta viscosidade de fusão.
Mais uma vez, inúmeras variações foram desenvolvidas para abordar as questões complexas em questão. Uma classificação geral das variações pode ser feita em quatro conceitos primários de unidade de injeção:
- êmbolo ou êmbolo de estágio único
- Aríete de estágio duplo
- Parafuso com um estágio
- Parafuso / carneiro com dois estágios
Embora ainda exista em máquinas minúsculas e em alguns equipamentos especializados, a unidade de pistão de estágio único é essencialmente obsoleta devido à sua ineficácia no aquecimento, mistura e transmissão de pressão. Beneficia da simplicidade e acessibilidade.
Além disso, o carneiro de dois estágios está praticamente obsoleto. O ram ainda é um misturador e aquecedor ineficaz, apesar de uma tentativa de melhorá-lo, separando as operações de aquecimento e fluxo de pressão.
A unidade parafuso/ram de dois estágios separa ainda mais as funções de fluxo e calor usando um ram para injeção em vez de um parafuso para mistura e aquecimento. A ideia é atraente porque ambos são ferramentas eficazes para suas respectivas tarefas.
Além disso, a unidade de injeção geralmente é classificada usando a pressão de injeção máxima e o volume de injeção disponível. A maior pressão possível na extremidade a jusante do parafuso é chamada de pressão de injeção. Isso depende do diâmetro do parafuso e da força que o empurra.
Porém, cuidado para não confundi-la com a pressão na linha hidráulica que atua no cilindro de injeção, que aciona a rosca, nem deve ser interpretada como a pressão necessária para preencher as cavidades do molde. Devido às perdas de pressão nos sistemas de alimentação do bico e do molde, isso é substancialmente menor.
A principal série de ações da unidade de injeção é a seguinte:
- O material é aquecido e derretido à medida que a rosca gira e, em seguida, transportado ao longo dos lances da rosca até a extremidade a jusante da rosca. O bico do barril é fechado por meio de válvula mecânica ou térmica ou pela existência de uma moldagem anterior.
Até que o material fundido suficiente se acumule para fabricar a próxima moldagem, o material fundido coletado força o parafuso ainda girando para trás contra uma resistência controlada (a contrapressão). A rotação do parafuso pára aqui. É hora de estar pronto para o derretimento.
- Quando o bocal do barril é aberto, o parafuso avança na direção axial sem girar, agindo como um aríete. Como resultado, o fundido reunido na frente da extremidade a jusante do parafuso é forçado (injetado) através do bico e no molde.
Para impedir que o derretimento flua de volta para os segmentos da rosca, um sistema de válvula pode ser instalado na extremidade a jusante da rosca. Esta é a fase de injeção ou enchimento do molde.
- Após o preenchimento do molde, a pressão do parafuso é mantida por um curto período de tempo para compensar a contração volumétrica do fundido de resfriamento dentro do molde. A fase de embalagem ou retenção é agora.
- Por fim, chega-se à fase de espera, onde o ciclo da unidade de injeção é retomado com rotação da rosca e preparação do fundido enquanto o molde é mantido fechado para permitir que o molde esfrie até a temperatura de ejeção.
Há quedas de pressão significativas quando o plástico fundido é forçado para dentro do bico de injeção e subsequentemente através do sistema de alimentação do molde e das cavidades. Regras simples não podem ser usadas para calcular essas perdas de pressão.
Unidade de aperto
O fechamento do molde é mantido contra as forças criadas quando o plástico é empurrado para um molde fechado pela pressão de injeção usando uma unidade de fixação para um IMM. Possui um sistema de acionamento que pode mover a placa móvel da máquina de moldagem por injeção em pelo menos uma direção.
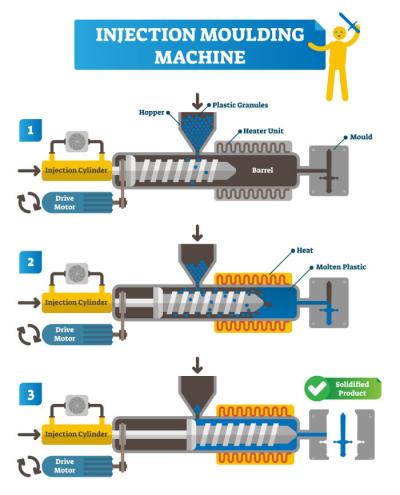
Tipos de Unidades de Fixação
Existem vários tipos de unidades de fixação no processo de moldagem por injeção. Eles são os seguintes:
Alternar Tipo de Fixação
Um dispositivo mecânico que amplifica a força é uma alavanca. Duas barras são conectadas e terminam com um pivô em uma máquina de moldagem. A extremidade de uma barra é conectada a uma placa fixa, enquanto a outra é conectada a uma placa móvel. A alavanca tem uma forma em V quando o molde é aberto. As duas barras formam uma linha reta quando a pressão é aplicada ao pivô.
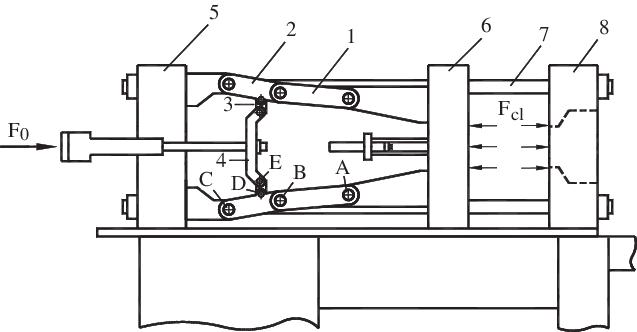
Os benefícios da fixação tipo alternância incluem que requer menos dinheiro e potência para ser feito e fornece um plano positivo do molde. Além disso, as desvantagens da fixação do tipo articulada são que ela requer muita manutenção e é difícil de fazer.
Fixação Hidráulica
Neste caso, o RAM do sistema hidráulico é amarrado ao prato móvel e uma unidade de fixação acionada por um cilindro hidráulico é conectada diretamente ao molde móvel fechado. O cilindro hidráulico tem duas seções: a entrada de óleo e a saída.
O óleo empurra o RAM para frente quando ele entra no cilindro sob pressão, fazendo com que a placa móvel e o molde se fechem. Além disso, o retorno do RAM e o molde são abertos quando o óleo é liberado do cilindro.
Algumas vantagens da fixação hidráulica incluem fácil controle da velocidade de fixação e suporte em qualquer ângulo, medição simples da força de fixação, fácil configuração do modo e ajuste da força de fixação e sua simplicidade na manutenção.
As desvantagens desse tipo de fixação são que custa mais e é mais caro do que um sistema de alternância e um grampo de substantivo positivo.
Unidade de fixação do tipo magnético
Módulos magnéticos dentro das placas magnéticas de fixação do molde ou placas produzem a força de fixação. O painel de interface pode controlar a fixação do molde, a troca do molde e a magnetização e desmagnetização das placas.
Os benefícios desta unidade de fixação incluem eletricidade sendo necessária apenas durante as fases de magnetização e desmagnetização, não durante a fixação, medição da força de fixação em tempo real com muitos recursos de segurança e manutenção gratuita.
Peso do Tiro do Molde
A quantidade de material injetado no molde para preenchê-lo, incluindo o sistema de alimentação, é conhecida como “peso do molde” ou “peso do produto”. O peso do abeto, do corredor e do portão são os componentes do peso do tiro, por outro lado. A distância que a rosca percorre para encher o produto, incluindo o sistema de alimentação, é conhecida como tamanho do molde/injeção do produto.
Conclusão
Usando a técnica de moldagem por injeção, o plástico bruto é derretido, injetado no molde, deixado esfriar e solidificar e, em seguida, o objeto acabado é expelido. O tamanho do disparo é crucial porque evita preenchimento insuficiente de polímero e rebarba. Outros fatores, como a capacidade do barril, também afetam o processo geral de moldagem por injeção.