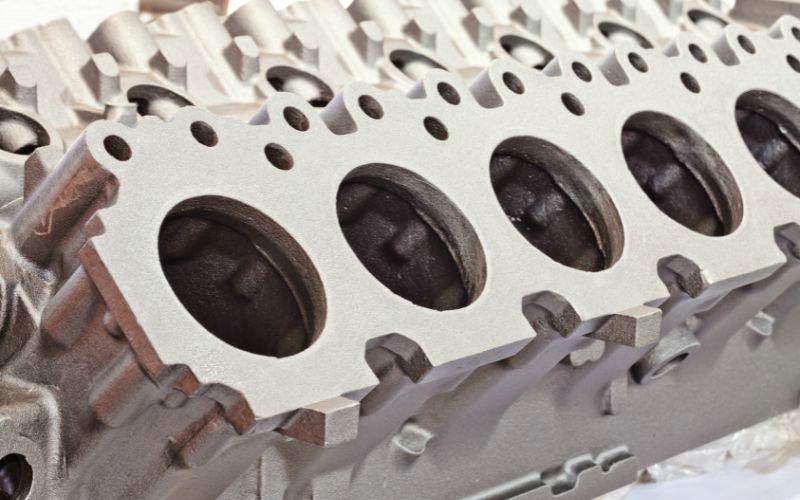
O que é fundição sob pressão?
A fundição sob pressão é um processo de fabricação que envolve derramar ou injetar metal fundido em moldes, conhecido como morre. O metal normalmente usado neste processo pode incluir zinco, alumínio e suas ligas. A sua jornada por um procedimento amplamente adotado por sua eficiência em produções de alto volume.
Quando você inicia a fundição sob pressão, o metal é derretido em um forno e depois injetado nas matrizes sob alta pressão. Este método é popular por sua capacidade de produzir peças com precisão, detalhes complexos e excelente acabamento superficial – qualidades exigidas em setores como automotivo, aeroespacial e eletrônico.
A fundição sob pressão é muito procurada pelos fabricantes devido à sua capacidade de produzir peças uniformes com qualidade consistente. Quer você a utilize para criar componentes complexos de caixas de câmbio para veículos ou carcaças elegantes e duráveis para eletrônicos, a fundição sob pressão é um pilar da fabricação moderna, especialmente quando a precisão e o volume são essenciais.
Processo de fundição sob pressão
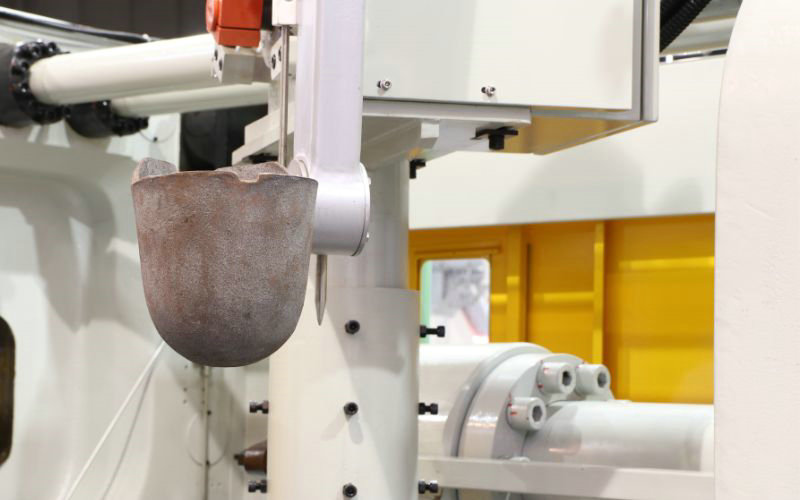
Existem três tipos principais de processos de fundição sob pressão: fundição sob pressão por gravidade, fundição sob pressão em câmara fria e fundição sob pressão em câmara quente.
Fundição por gravidade
Na fundição por gravidade, o metal fundido é derramado diretamente de uma concha em uma matriz semipermanente ou permanente. A cavidade é preenchida sem nenhuma força além da gravidade. As vantagens da fundição por gravidade incluem a capacidade de produzir peças fundidas densas e de alta qualidade com excelentes propriedades mecânicas adequadas para tratamento térmico. É econômico para produção de pequeno e médio volume.
Fundição sob pressão em câmara fria
Na fundição sob pressão em câmara fria, o forno de fusão está localizado separadamente da máquina de fundição sob pressão. Para cada ciclo, uma quantidade precisa de metal fundido é colocada na câmara de injeção não aquecida da máquina; então, um êmbolo hidráulico força o metal para dentro da matriz sob altas pressões entre 2.000-20.000 psi. A fundição sob pressão em câmara fria é usada para ligas com pontos de fusão mais elevados, como o alumínio. Produz peças fortes e duráveis, mas tem tempos de ciclo mais lentos do que uma câmara quente.
Fundição sob pressão de câmara quente
Na fundição sob pressão em câmara quente, o mecanismo de injeção é submerso em uma poça de metal fundido, que é alimentado na matriz através de um pescoço de ganso e um pistão. No início de cada ciclo, o pistão se retrai, permitindo que o pescoço de ganso se encha com metal fundido. O pistão então força o metal através do pescoço de ganso para dentro da matriz a pressões de 1.000 a 5.000 psi. A fundição sob pressão em câmara quente é usada para ligas com baixos pontos de fusão, como zinco e magnésio. Permite tempos de ciclo mais rápidos e pode produzir peças complexas com porosidade reduzida.
Aplicações de fundição sob pressão
Automotivo: A fundição sob pressão é amplamente utilizada no setor automotivo. Você encontrará componentes como blocos de motor, peças de transmissão e elementos estruturais feitos por meio desse processo. A capacidade de produzir peças fortes e duráveis de forma rápida e eficiente torna a fundição sob pressão uma escolha obrigatória para engenheiros automotivos.
- Componentes do motor
- Caixas de câmbio
- Quadros de carros
Aeroespacial: A indústria aeroespacial valoriza a fundição sob pressão para criar peças complexas que exigem precisão e pode suportar condições adversas. Componentes como trem de pouso, instrumentação da cabine e peças do motor são normalmente fundidos sob pressão.
- Carcaças de Instrumentação
- Peças do trem de pouso
- Componentes do motor
Eletrônicos: Na eletrônica, a fundição sob pressão é usada para criar itens como conectores, caixas e dissipadores de calor. Essas peças se beneficiam da capacidade da fundição sob pressão de formar designs complexos com alto nível de condutividade térmica.
- Dissipadores de calor
- Conectores
- Gabinetes
O que é moldagem por injeção de metal?
A Moldagem por Injeção de Metal (MIM) oferece um processo de fabricação para a produção de peças complexas em volumes médios a altos. MIM combina a liberdade de design e a complexidade das formas encontradas na moldagem por injeção de plástico com a excepcional resistência e integridade do metal.
Aqui está uma visão geral concisa do MIM:
- Materiais: Sua escolha de materiais em MIM normalmente inclui metais ferrosos, como aço inoxidável, que proporcionam resistência e durabilidade significativas ao produto final.
- Força e Precisão: As peças MIM são conhecidas por sua impressionante resistência e precisão. Eles mantêm tolerâncias restritas, tornando-os adequados para ambos industrial e médico formulários.
- Geometrias Complexas e Paredes Finas: Com o MIM, você pode criar peças com geometrias complexas e paredes finas, o que pode ser desafiador ou impossível por meio de processos tradicionais de usinagem de metal.
Processo de moldagem por injeção de metal
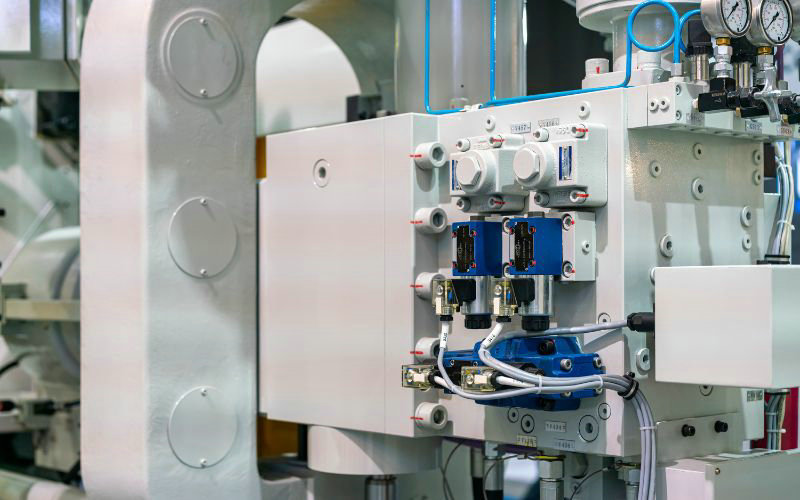
Sua compreensão do MIM começa com seu material primário — um matéria-prima que consiste em pó metálico fino e um material aglutinante polimérico. Os metais comuns usados neste processo incluem aço inoxidável, titânio, ligas de níquel e ligas de cobre. Em seus estágios iniciais, o MIM é semelhante à moldagem por injeção de plástico; a matéria-prima é aquecida até ficar viscosa e poder ser injetada na cavidade do molde.
Depois que a peça moldada estiver definida, o processo de desvinculação começa. Isto implica a remoção da maior parte do ligante, o que prepara a peça para a sinterização. Durante a sinterização, sua peça é exposta a altas temperaturas que unem as partículas metálicas e garantem a integridade.
Após a sinterização, você descobrirá que a peça encolheu significativamente — normalmente entre 15-20%. No entanto, o processo de sinterização permite obter excelente precisão dimensional e acabamento superficial, muitas vezes minimizando a necessidade de usinagem subsequente. O MIM é altamente econômico quando se trata de produzir peças pequenas em grandes volumes devido ao menor desperdício de material e à capacidade de manter tolerâncias rígidas sem extensos trabalhos de acabamento.
Em última análise, a moldagem por injeção de metal oferece uma combinação única de qualidade, eficiência e versatilidade nos processos de fabricação. Sua capacidade de usar uma variedade de metais e atingir características específicas do material — como dureza, resistência à tração e resistência à temperatura — torna-o um processo valioso em vários setores.
Aplicações de moldagem por injeção de metal (MIM)
A moldagem por injeção de metal (MIM) é precisa e econômica, e é especialmente adequada para a produção em massa de componentes de pequeno e médio porte. Você encontrará aplicações MIM em vários setores devido à sua capacidade de produzir formas complexas com excelente acabamento superficial.
Aeroespacial e Automotivo:
- O MIM é ideal para a fabricação de peças como maçanetas, dobradiças e componentes de motores devido à sua alta resistência e durabilidade.
Médica e Odontológica:
- A indústria médica se beneficia da precisão do MIM na criação de ferramentas cirúrgicas, implantes e braquetes que exigem biocompatibilidade.
Eletrônicos de consumo:
- Pequenos componentes, como peças de telefones celulares ou conjuntos de câmeras, exploram a habilidade do MIM em miniaturização e recursos de design detalhado.
Indústria de armas de fogo:
- O MIM é usado para fabricar vários componentes de armas de fogo, incluindo gatilhos, martelos e peças de mira que exigem tolerâncias e resistência estritas.
Equipamentos Industriais Gerais:
- Você encontrará o MIM na produção de componentes de bombas, conectores e válvulas devido à sua consistência e capacidade de produção em alto volume.
Nessas aplicações, o MIM oferece benefícios que incluem:
- Materiais de alta densidade com ótimas propriedades mecânicas
- Capacidade de integrar recursos como roscas, engrenagens e canais internos sem operações secundárias
- Produção de peças próximas do formato final, minimizando desperdícios
Fundição sob pressão vs MIM: vantagens e desvantagens
Vantagens do MIM sobre a fundição sob pressão
1. A MIM pode produzir peças pequenas e complexas com características complexas e paredes finas que seriam desafiadoras ou impossíveis com a fundição sob pressão.
2. A MIM oferece uma gama mais ampla de materiais, incluindo metais ferrosos, aços inoxidáveis, titânio e ligas de níquel. A fundição sob pressão é normalmente limitada a metais não ferrosos como alumínio, zinco e magnésio.
3. As peças MIM possuem excelentes propriedades mecânicas, alta resistência e resistência ao desgaste devido ao processo de sinterização.
4. MIM fornece tolerâncias mais restritas e pode ter precisão de 0,3 mm.
5. O MIM praticamente não tem desperdício porque todo o material é injetado diretamente no molde.
Desvantagens do MIM em comparação com a fundição sob pressão
1. O MIM é geralmente mais caro do que a fundição sob pressão devido às ferramentas complexas e às múltiplas etapas de processamento.
2. O MIM tem uma vida útil menor (150 mil a 300 mil disparos) em comparação com a fundição sob pressão (mais de 1 milhão de disparos).
3. As peças MIM podem encolher significativamente (até 30%) durante a sinterização, exigindo um projeto de molde cuidadoso. A fundição sob pressão tem um encolhimento muito menor.
4. O MIM tem altos custos iniciais de automação e configuração.
Vantagens da fundição sob pressão sobre MIM
1. A fundição sob pressão é normalmente mais barata que o MIM, até 30% mais barato em alguns casos.
2. A fundição sob pressão tem uma vida útil mais longa (mais de 1 milhão de disparos) em comparação com o MIM (150 mil a 300 mil disparos).
3. A fundição sob pressão não requer operações secundárias após a peça ser ejetada do molde.
4. A fundição sob pressão pode acomodar inserções e peças feitas de outros materiais incorporados na peça fundida.
Desvantagens da fundição sob pressão em comparação com MIM
1. A fundição sob pressão tem dificuldade em produzir peças pequenas e complexas com características finas e paredes finas.
2. A fundição sob pressão é limitada principalmente a metais não ferrosos. Os metais ferrosos têm pontos de fusão muito elevados, o que reduz a vida útil da matriz.
3. A porosidade devido a gases aprisionados é um problema comum na fundição sob pressão, reduzindo a resistência mecânica.
4. A fundição sob pressão requer matrizes caras para suportar a alta pressão e as temperaturas do metal fundido.
Em resumo, o MIM se destaca na produção de peças pequenas e complexas com excelentes propriedades mecânicas em uma ampla variedade de materiais. No entanto, é mais caro e tem um tempo de ciclo mais longo do que a fundição sob pressão. A fundição sob pressão é mais econômica e adequada para peças maiores e mais simples em metais não ferrosos com tempos de produção mais rápidos, mas enfrenta problemas com características complexas e porosidade.
Comparação: Moldagem por Injeção de Metal vs. Fundição sob Pressão
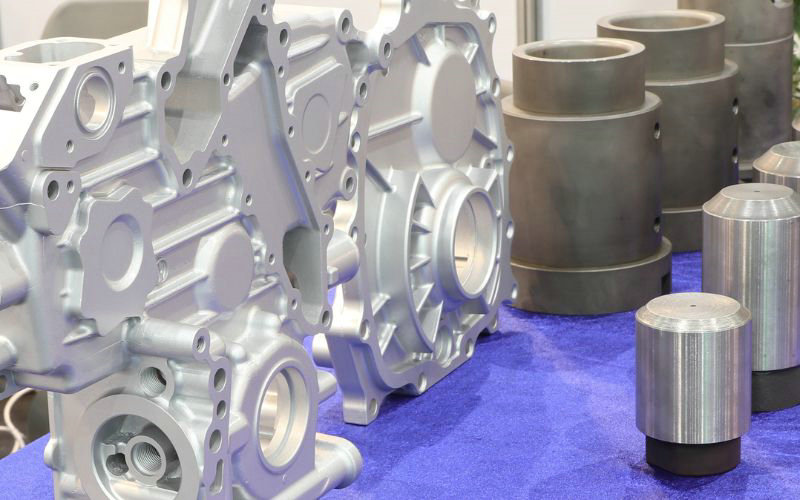
1. Precisão e tolerâncias
Moldagem por injeção de metal (MIM): MIM obtém peças muito precisas com tolerâncias relativamente restritas, normalmente com precisão de 0,3 mm. Essa precisão se deve aos finos pós metálicos utilizados, que permitem geometrias detalhadas e complexas.
Fundição sob pressão: A fundição sob pressão geralmente oferece boa precisão dimensional, mas não tão alta quanto MIM. A tolerância típica para fundição sob pressão é de cerca de ±0,0005 polegadas, o que é menos preciso em comparação com as capacidades do MIM. Variações nas dimensões geralmente exigem cortes adicionais para atender às especificações.
2. Materiais necessários
Moldagem por injeção de metal (MIM): O MIM pode utilizar uma ampla variedade de materiais, incluindo metais ferrosos e não ferrosos, aços inoxidáveis, titânio e ligas de níquel. Esta versatilidade permite a produção de peças com propriedades específicas adaptadas a diversas aplicações.
Fundição sob pressão: utiliza principalmente metais não ferrosos, como alumínio, zinco e magnésio. Embora a fundição sob pressão possa usar metais ferrosos, esses materiais têm pontos de fusão muito altos, o que pode reduzir significativamente a vida útil do molde.
3. Comparação de velocidade
Moldagem por injeção de metal (MIM): O processo MIM envolve várias etapas, incluindo mistura, moldagem por injeção, desligação e sinterização, o que o torna geralmente mais lento do que a fundição sob pressão. No entanto, uma vez estabelecida a produção, o MIM pode produzir com eficiência grandes volumes de peças.
Fundição sob pressão: Conhecida por sua rápida capacidade de produção, a fundição sob pressão é mais rápida, particularmente adequada para produção de alto volume. O processo permite a criação rápida de peças grandes devido às suas técnicas de injeção de alta pressão.
4. Acabamento de superfície
Moldagem por injeção de metal (MIM): normalmente fornece um acabamento superficial de alta qualidade que muitas vezes não requer pós-processamento adicional. O processo de sinterização auxilia na obtenção de um acabamento liso.
Fundição sob pressão: As peças geralmente saem do molde com um bom acabamento superficial, mas podem exigir algum corte do excesso de metal. A qualidade da superfície é geralmente considerada média em comparação com MIM.
5. Custos de Fabricação
Moldagem por injeção de metal (MIM): Embora os custos iniciais de configuração e ferramentas possam ser altos, o MIM pode ser econômico para a produção de peças complexas em grandes volumes devido à redução de desperdício e às necessidades mínimas de pós-processamento.
Fundição sob pressão: Geralmente mais barato em termos de custos iniciais e mais econômico para peças maiores e produção em alto volume. No entanto, a relação custo-benefício diminui para peças altamente complexas ou menores.
6. Diferenças de molde
Moldagem por injeção de metal (MIM): Os moldes usados em MIM podem ser menos duráveis em comparação com a fundição sob pressão, normalmente suportando cerca de 150.000 a 300.000 disparos. No entanto, os moldes MIM permitem maior complexidade no design das peças.
Fundição sob pressão: Os moldes são projetados para suportar altas pressões e temperaturas, tornando-os mais duráveis, com expectativa de vida de mais de 1 milhão de disparos. No entanto, oferecem menos flexibilidade em termos de complexidade das peças em comparação com os moldes MIM.