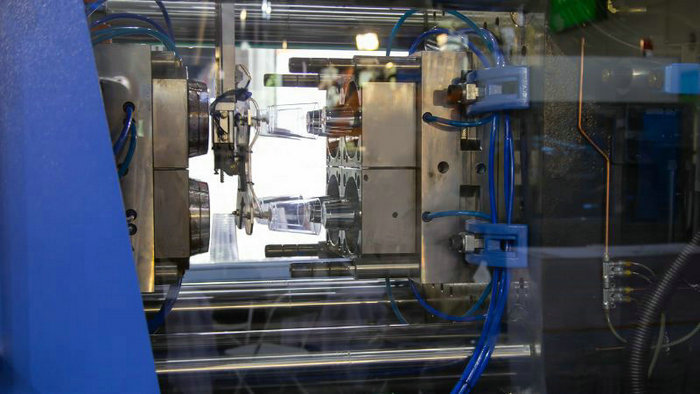
Introduction au moulage en polycarbonate
Le moulage du polycarbonate est une technique que vous pouvez utiliser pour fabriquer des objets combinant avec précision une excellente ténacité, clarté et résistance aux chocs. Ce matériau, le polycarbonate, est un thermoplastique amorphe largement célèbre pour ses propriétés remarquables.
Ce qui distingue le polycarbonate
Décrivons ce qui rend ce matériau si spécial.
Le polycarbonate est une forme de polymère thermoplastique réputé pour être exceptionnellement rigide et poids léger. Souvent désigné par son abréviation « PC », le polycarbonate possède plusieurs propriétés souhaitables qui le rendent utile pour diverses applications.
Chimiquement, ce plastique est constitué de groupes carbonate liés entre les cycles aromatiques le long de la chaîne polymère. Cette structure chimique confère au polycarbonate sa résistance et sa rigidité. Il est amorphe et transparent, laissant passer facilement la lumière. Pourtant, le polycarbonate est très résistant aux chocs et peut supporter des forces importantes sans se casser ni se fissurer.
La production de polycarbonate commence par la réaction du bisphénol A (BPA) et du phosgène pour former le squelette polymère. En fonction de son utilisation finale, il peut ensuite être transformé en feuilles solides ou moulé sous diverses formes.
Lors du moulage, le polycarbonate peut être façonné dans votre forme désirée tout en préservant son propriétés mécaniques comme la résistance à la flexion et aux chocs. Le matériel est résistant à la chaleur, ce qui ajoute à sa durabilité et le rend adapté aux produits soumis à des températures élevées.
De plus, l'optique clarté de ce plastique s'apparente à de la transparence, créant des pièces à la fois solides et claires. Ces caractéristiques en font un choix exceptionnel pour une variété d'applications, notamment les composants automobiles, l'électronique grand public et les équipements de sécurité.
Conception et ingénierie de moules
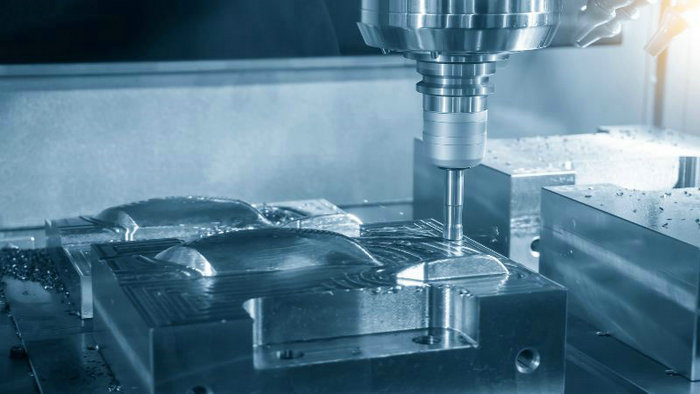
Avant de vous lancer dans le moulage de polycarbonate, vous constaterez que la conception et l'ingénierie des moules sont un facteur essentiel pour obtenir des pièces cohérentes et de haute qualité. Ce processus englobe une série de considérations techniques, depuis la sélection des bons matériaux jusqu'à l'utilisation de logiciels avancés pour une conception de précision.
Sélection des matériaux de moule
Votre choix de matériau du moule influence directement la qualité et le cycle de vie de vos produits en polycarbonate. Les aciers à outils sont couramment utilisés en raison de leur durabilité et de leur résistance à l'usure. Lors du choix, pensez à :
- Conductivité thermique: Affecte la vitesse de refroidissement et le temps de cycle.
- Dureté: Détermine la résistance aux défauts de surface et à l'abrasion.
Ingénierie de précision pour les moules
Réalisation tolérance stricte est primordial dans l’ingénierie des moules. L'usinage de précision garantit que les moules répondent aux spécifications exactes nécessaires à la forme et à la taille souhaitées de vos pièces. Comprendre que:
- Tolérances: Affecte l'ajustement et la fonction de vos pièces assemblées.
- Tailles des pièces: allant de la minute à la grande, tout dépend de la précision de vos moules.
Traitements de surface et finition
Le traitement de surface des moules est essentiel pour améliorer les propriétés de démoulage et réduire les défauts de surface. Les options de finition que vous rencontrerez incluent :
- Polissage : donne une surface lisse et brillante.
- Texturation : Fournit une surface mate ou à motifs, qui peut être fonctionnelle ou esthétique.
Ventilation et placement des portes
Approprié ventilation et placement de la porte sont cruciaux pour prévenir les défauts et garantir débit optimal des résines thermoplastiques. Gardez à l'esprit:
- Ventilation: Permet à l'air de s'échapper de la cavité du moule pour éviter les défauts d'air emprisonnés.
- Emplacements des portes: Influence l'écoulement de la résine et peut impacter l'apparence et l'intégrité de la pièce.
Logiciels de CAO et de conception de moules
L'utilisation de CAO (conception assistée par ordinateur) et d'un logiciel spécialisé de conception de moules facilite la processus de fabrication en vous permettant de :
- Conduire analyse de flux: Prédire et améliorer la répartition de la résine dans tout le moule.
- Visualiser emplacements des portes et formes des pièces: Aide à relever les défis potentiels de fabrication avant l’outillage.
Au cours de votre parcours de moulage du polycarbonate, ces subtilités de la conception et de l'ingénierie des moules façonnent le parcours depuis la matière première jusqu'au produit fini, fournissant ainsi un modèle clair de réussite.
Technique du processus de moulage par injection de polycarbonate
Les pièces en polycarbonate produites par moulage par injection présentent des qualités impressionnantes telles que la résistance aux chocs et à la chaleur. Néanmoins, le traitement du polycarbonate peut être complexe car certaines variantes présentent de faibles indices de fusion.
Lors du moulage du polycarbonate, le contrôle des paramètres du processus est crucial pour la qualité de votre produit final. Entrons dans les détails pour vous assurer d'obtenir les meilleurs résultats.
Préparez le polycarbonate
- Les qualités courantes de polycarbonate comprennent les polycarbonates à usage général, à haute température, stabilisés aux UV et ignifuges. La résine PC doit être séchée avant le moulage à une teneur en humidité inférieure à 0,02% pour éviter les défauts.
- Le séchage s'effectue généralement à 120°C pendant 2 à 4 heures.
Comment régler la machine de moulage par injection
- La force de serrage doit être de 0,7 à 0,8 tonne par pouce carré de surface de pièce projetée.
- La taille de la machine doit être 1,5 à 2 fois supérieure au poids de la pièce.
- La vis doit avoir un rapport L/D d'au moins 15:1, idéalement 20:1, avec une bague de contrôle et une transition progressive.
- L'ouverture de la buse doit être légèrement plus petite que la taille du portail.
Préparation du moule
- Le moule doit être nettoyé et recouvert d'un agent de démoulage pour faciliter l'éjection des pièces.
- Les évents doivent être dégagés pour permettre à l'air de s'échapper lorsque le moule est rempli.
- Les canaux de refroidissement doivent être optimisés pour un refroidissement uniforme et des temps de cycle réduits.
Paramètres du processus
- Température de fusion : 280-320°C selon qualité.
- Température du moule : 70-120°C. Plus élevé pour une meilleure finition de surface et une contrainte moindre.
- Pression d'injection : Aussi haut que possible, typiquement 850-1400 bar. Aide à remplir le moule rapidement.
- Vitesse d'injection : Plus lent pour les portails petits/bordés, plus rapide sinon.
- Pression d'emballage : Aussi bas que possible pour minimiser les contraintes résiduelles.
Procédures post-moulage
- Les pièces en plastique sont éjectées lorsqu'elles sont suffisamment froides pour supporter les contraintes de démoulage.
- Les marques de porte sont supprimées par rognage.
- Un recuit à 120-130°C pendant 30 minutes à 1 heure peut soulager les contraintes résiduelles.
- Des contrôles dimensionnels et des inspections visuelles sont effectués pour garantir la qualité des pièces.
Détails du mécanisme d'éjection
La éjection Le processus doit être soigneusement contrôlé pour éviter d’endommager les pièces moulées en polycarbonate solidifié.
- Broches d'éjection : Assurez-vous que les broches sont positionnées pour répartir uniformément les forces d’éjection.
- Vitesse d'éjection : Ajustez la vitesse pour éviter que la pièce ne colle ou ne se déforme.
En prêtant attention à ces spécificités techniques, vous serez mieux équipé pour gérer le processus complexe de moulage par injection de polycarbonate.
Techniques avancées de moulage par injection de plastique polycarbonate
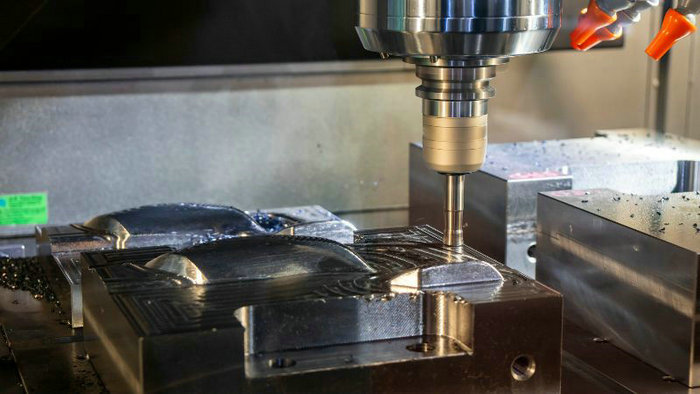
Au cours de votre parcours pour maîtriser le moulage du polycarbonate, vous découvrirez que des techniques avancées peuvent jouer un rôle essentiel dans l'amélioration de la résistance, de l'esthétique et de la fonctionnalité. Explorons comment ces méthodes innovantes peuvent améliorer vos produits.
Moulage par injection-compression
Dans le moulage par injection-compression, le polycarbonate est d'abord injecté dans un moule légèrement ouvert, puis comprimé davantage, améliorant ainsi l'uniformité du produit. Cette méthode combine les principes de moulage par injection et Moulage par compression, garantissant une réduction des contraintes tout en obtenant des composants plus fins et plus précis.
Moulage par injection assisté par gaz et par injection d'eau
Moulage par injection assisté par gaz introduit de l'azote gazeux dans la cavité du moule après l'injection, créant des canaux internes et réduisant l'utilisation de matériaux sans compromettre l'intégrité structurelle. D'un autre côté, moulage par injection assisté par eau obtient des résultats similaires avec de l'eau, améliorant le processus de refroidissement et la durée du cycle.
- Avantages:
- Perte de poids
- Force accrue
- Temps de cycle plus rapides
Moulage multimatériaux et co-injection
Passer à moulage multi-matériaux (bi-composants), vous pouvez mouler du polycarbonate avec différents matériaux en un seul cycle pour des structures composites. Moulage par co-injection, un sous-ensemble de cette technique, consiste à injecter deux polymères distincts dans un moule, l'un après l'autre, pour créer une pièce aux propriétés superposées.
- Composition des pièces composites:
- Matériau de base : généralement le matériau le moins cher ou le moins robuste.
- Matériau de la peau : généralement le matériau le plus durable qui recouvre la pièce.
Chaque méthode joue un rôle essentiel dans l'adaptation de vos composants en polycarbonate pour répondre à des exigences spécifiques – des aspects structurels aux caractéristiques esthétiques. Grâce à ces techniques avancées, vos produits en polycarbonate non seulement répondront, mais dépasseront les attentes des applications les plus difficiles.
Durabilité et impact environnemental
Lorsque vous explorez le monde du polycarbonate, il est essentiel de comprendre non seulement ses applications pratiques, mais également l'impact de sa production et de son cycle de vie sur l'environnement. Dans cette section, nous examinerons de plus près comment le recyclage et l'efficacité de ses processus de production contribuent à la durabilité.
Recyclage et réutilisation du polycarbonate
La nature robuste du polycarbonate permet son utilisation dans divers produits, des verres de lunettes au verre pare-balles. Cependant, lorsque ces éléments atteignent la fin de leur cycle de vie, recyclage et réutilisation le polycarbonate devient primordial pour réduire les déchets environnementaux. Heureusement, le polycarbonate peut être recyclé mécaniquement pour diminuer son empreinte écologique. Le processus implique :
- Affûtage: Les produits en polycarbonate sont broyés en morceaux plus petits.
- Nettoyage: Les contaminants sont éliminés pour préparer la réintégration.
- Fusion: Les chutes de polycarbonate propres sont rapidement chauffées et remodelées en nouveaux produits ou feuilles de polycarbonate.
En convertissant les déchets de polycarbonate en granulés par extrusion, ils peuvent être ajoutés à d'autres produits en plastique, prolongeant ainsi efficacement leur utilité et empêchant la pollution.
Efficacité énergétique dans la production
Pour améliorer la durabilité, il est crucial de se concentrer sur efficacité énergétique de produire du polycarbonate. Le processus de fabrication implique généralement un chauffage rapide et un contrôle précis pour produire des feuilles ou des produits en polycarbonate de haute qualité. Pour économiser de l’énergie, des avancées ont été mises en œuvre :
- Optimiser les processus: Ajuster les paramètres de production pour minimiser le gaspillage d’énergie.
- Intégrer la technologie verte: Utiliser des équipements économes en énergie et des sources d’énergie renouvelables lorsque cela est possible.
Cet effort d'amélioration continue vise à réduire la consommation globale d'énergie et l'empreinte carbone associées à la production de polycarbonate. En donnant la priorité à ces pratiques, vous pouvez participer à des initiatives plus respectueuses de l'environnement au sein de l'industrie.
Questions fréquemment posées
Quelles températures sont nécessaires pour le moulage par injection de polycarbonate ?
Pour un moulage par injection réussi, le contrôle de la température est très important. Le polycarbonate nécessite généralement des températures allant de -40°C/-40°F à 120°C/248°F. Ces paramètres garantissent que le polycarbonate conserve sa résistance et sa stabilité pendant le processus.
Quels sont les problèmes courants dans le moulage par injection de polycarbonate et comment peuvent-ils être résolus ?
Les problèmes courants incluent la déformation, les bulles et un mauvais remplissage. Résolvez-les en optimisant les exigences de ventilation, en contrôlant les paramètres du processus et en maintenant une épaisseur de paroi uniforme.
Quel est le processus de drapage des feuilles de polycarbonate ?
Le drapage consiste à chauffer la feuille de polycarbonate à une température souple, puis à la draper sur un moule pour obtenir la forme souhaitée. Le refroidissement préserve la forme.
Quelles sont les étapes impliquées dans le traitement des matériaux en polycarbonate ?
Le traitement du polycarbonate consiste à chauffer le matériau à la température recommandée, à l'injecter dans des moules, à le refroidir pour le solidifier, puis à éjecter les pièces finales moulées par injection.
Quelle est la méthodologie de thermoformage du polycarbonate ?
Le thermoformage du polycarbonate consiste à chauffer la feuille jusqu'à son point de ramollissement, à l'étirer sur un moule, puis à la refroidir pour former un produit fini rigide et façonné.
Quels sont les inconvénients du moulage par injection de polycarbonate ?
La viscosité plus élevée du polycarbonate entraîne des cycles de moulage plus lents, des pressions de moulage plus élevées et la nécessité de moules plus robustes, ce qui peut avoir un impact sur le coût du moulage par injection. La gestion des défauts est également plus critique.