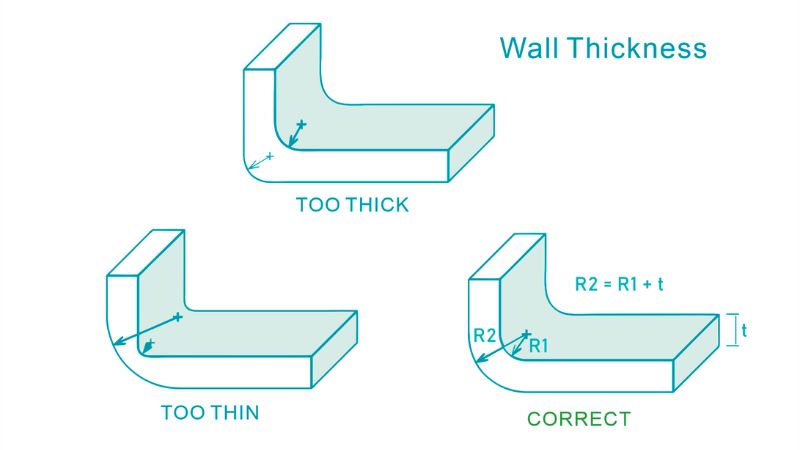
De la compréhension des bases de l'épaisseur des parois à la navigation dans les considérations spécifiques aux matériaux, ce guide couvre les aspects essentiels que les concepteurs, les ingénieurs et les fabricants doivent connaître.
Ce guide complet explore l’importance d’une conception appropriée de l’épaisseur de paroi dans le moulage par injection, offrant un aperçu des meilleures pratiques, des défis courants et des solutions pour optimiser la production de pièces.
Quelle est l'épaisseur de paroi dans le moulage par injection
L'épaisseur de la paroi est une considération de conception critique dans le processus de moulage par injection, qui fait référence à l'épaisseur de la section transversale de la pièce en plastique moulée.
Il s’agit de l’une des considérations de conception les plus importantes dans le moulage par injection, car elle a un impact significatif sur la fabricabilité, le coût, la qualité et les performances de la pièce finale.
Qu'est-ce qui influence l'épaisseur de la paroi
Deux facteurs clés influencent l'épaisseur de paroi des matières plastiques moulées par injection et la structure des pièces.
- Taille et forme – Les pièces de plus grande taille nécessitent généralement des parois plus épaisses pour assurer l'intégrité structurelle, tandis que les pièces plus petites peuvent avoir des parois plus fines. Les formes complexes peuvent nécessiter des épaisseurs variables.
- Matière plastique – – Les différents plastiques présentent des caractéristiques d'écoulement et des vitesses de refroidissement différentes. Les matériaux ayant une viscosité plus faible ou des vitesses d'écoulement plus élevées peuvent généralement être utilisés avec des parois plus fines.
Voici un tableau pour vous permettre de vérifier l'épaisseur de paroi optimale pour divers matériaux :
Matériel | Plage d'épaisseur de paroi recommandée |
abdos | 0,045 – 0,140 po (1,14 – 3,56 mm) |
Acétal (POM) | 0,030 – 0,120 po (0,76 – 3,05 mm) |
Acrylique (PMMA) | 0,025 – 0,500 po (0,64 – 12,7 mm) |
Nylon (PA) | 0,030 – 0,115 po (0,76 – 2,92 mm) |
Polycarbonate (PC) | 0,040 – 0,150 po (1,02 – 3,81 mm) |
Polyéthylène (PE) | 0,030 – 0,200 po (0,76 – 5,08 mm) |
Polypropylène (PP) | 0,025 – 0,150 po (0,64 – 3,81 mm) |
Polystyrène (PS) | 0,035 – 0,150 po (0,89 – 3,81 mm) |
Quels sont les problèmes liés à l’épaisseur des parois ?
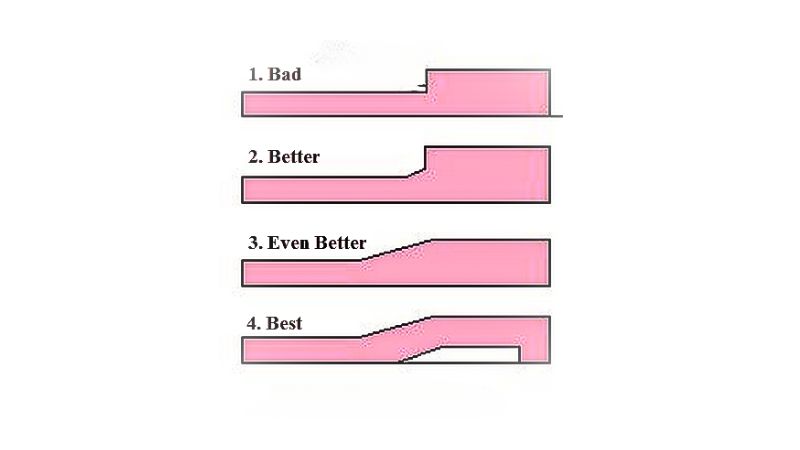
Une épaisseur de paroi incorrecte pour le moulage par injection peut entraîner plusieurs défauts dans le produit final :
Défaut | Cause | Résultat |
Déformation | Épaisseur de paroi inégale | Des taux de refroidissement différents entraînent des contraintes internes, provoquant des déformations ou des torsions. |
Marques d'évier | Sections plus épaisses | Le refroidissement lent permet à la surface de s'enfoncer vers l'intérieur, créant de petites dépressions |
Lignes d'écoulement | Variations d'épaisseur de paroi | Différents débits de plastique fondu provoquent des stries ou des lignes visibles sur la surface |
Coups courts | Transitions du fin au épais | Un refroidissement prématuré empêche le remplissage complet des zones plus épaisses |
Vides | Sections épaisses | Les poches d'air ou de vide forment des vides internes |
Jet | Murs trop fins | L'écoulement rapide du plastique provoque des motifs en forme de serpent sur la surface de la pièce |
Faiblesse structurelle | Épaisseur de paroi inégale | Compromet la résistance et l'intégrité des pièces |
Inexactitudes dimensionnelles | Variations d'épaisseur | Un refroidissement inégal conduit à des pièces qui ne répondent pas aux dimensions spécifiées |
Augmentation du stress interne | Différentes épaisseurs de paroi | Des taux de refroidissement différents entraînent des contraintes internes plus élevées |
Défauts de surface | Épaisseur de paroi incorrecte | Provoque des imperfections de surface telles que des ondulations ou des ondulations |
Considérations de conception pour obtenir une épaisseur de paroi uniforme
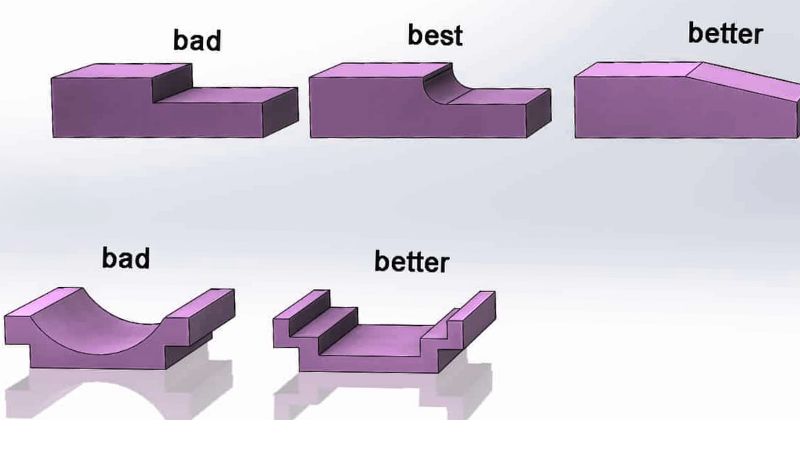
L'analyse de conception pour la fabricabilité (DFM) aide à identifier l'épaisseur uniforme optimale pour minimiser les contraintes internes et améliorer la cohérence.
Utilisation des angles de dépouille pour améliorer le remplissage du moule
Les angles de dépouille font partie intégrante de la conception des composants moulés par injection, car ils permettent de faciliter le démoulage de la pièce finie. L'intégration d'un angle de dépouille n'est pas seulement une bonne pratique ; elle est essentielle pour favoriser une épaisseur de paroi uniforme.
Un angle de dépouille externe recommandé de 0,5 à 1,5 degrés et un angle interne de 0,5 degrés peuvent grandement améliorer le processus de remplissage du moule.
Ces angles légers permettent au matériau de s'écouler plus facilement et empêchent la formation d'épaisseurs de paroi irrégulières, qui sont souvent à l'origine de divers défauts au sein de la pièce.
Traitement des contraintes internes causées par une épaisseur de paroi non uniforme
Les différences d'épaisseur de paroi peuvent entraîner des contraintes internes au sein de la pièce lors de son refroidissement et de sa solidification. Les sections de paroi plus épaisses refroidissent plus lentement, ce qui entraîne des taux de retrait différentiels qui peuvent déformer la pièce.
Une épaisseur uniforme sur toute la pièce est impérative pour répartir uniformément ces contraintes et éviter d’éventuels problèmes de qualité.
Lors de la conception des pièces, il faut tenir compte des zones à haut risque et appliquer une épaisseur de paroi uniforme pour atténuer la formation de contraintes internes.
Épaisseur recommandée – Minimum
L'épaisseur minimale de la paroi dépend du matériau plastique spécifique utilisé et de la taille/complexité de la pièce.
En général:
Pour les petites pièces et la production efficace en grande quantité, une épaisseur de paroi minimale de 0,025 à 0,030 pouce (0,64 à 0,76 mm) est recommandée.
Pour les pièces plus grandes, un minimum de 0,040 à 0,050 po (1,0 à 1,3 mm) est suggéré.
L'épaisseur de paroi minimale pratique pour le moulage par injection conventionnel varie de 0,030 à 0,040 pouce (0,76 à 1,0 mm).
Certaines applications de moulage à parois minces spécialisées peuvent atteindre des parois aussi fines que 0,010 po (0,25 mm), mais cela nécessite des pressions élevées et limite la taille des pièces.
Épaisseur recommandée – maximale
Dans la mesure du possible, il convient d'éviter les parois trop épaisses lors du moulage par injection, car elles peuvent entraîner des défauts et des inefficacités.
Les lignes directrices générales sont les suivantes :
La plupart des pièces moulées par injection ont une épaisseur de paroi maximale de 0,125 à 0,250 pouce (3,2 à 6,4 mm).
Les murs d'une épaisseur supérieure à 0,250 po (6,4 mm) présentent un risque plus élevé de retombées, de vides, de contraintes résiduelles et de déformation.
Dans certaines applications spécialisées, des épaisseurs de paroi allant jusqu'à 4,5 pouces (114 mm) sont possibles mais nécessitent des temps de cycle très longs.
En tant que meilleure pratique en matière d'efficacité et de qualité, une épaisseur de paroi maximale de 0,125 à 0,160 po (3,2 à 4,0 mm) est recommandée pour la plupart des pièces.
Comment résoudre les problèmes d'épaisseur de paroi dans les pièces moulées
Traitement des sections à parois épaisses dans les pièces moulées par injection
Pour atténuer ce problème, il est conseillé de maintenir une épaisseur de paroi qui facilite un refroidissement rapide mais offre également une résistance suffisante. Par exemple, avec un matériau PA6 d'une épaisseur de 8 mm, le cycle de moulage par injection total est d'environ 93 secondes, avec un refroidissement prenant environ 70 secondes.
Pour surmonter le défi des temps de cycle prolongés en raison de parois plus épaisses, il peut être avantageux d'utiliser une technique appelée « core out ». Cela consiste à créer des sections creuses dans la paroi épaisse sans compromettre l'intégrité ou la résistance de la pièce.
Comment manipuler des parois minces sans compromettre l'intégrité des pièces
Il est recommandé aux concepteurs de produits de concevoir des pièces avec l’épaisseur de paroi minimale nécessaire sans compromettre l’intégrité de la pièce.
La conception de parois plus minces nécessite une compréhension approfondie des caractéristiques d'écoulement du matériau pour éviter les défauts.
Des facteurs tels que la pression d'injection, la température du moule et l'inclusion d'éléments de conception tels que des nervures ou des goussets peuvent aider à soutenir les pièces à parois minces, améliorant ainsi leur moulabilité et réduisant le risque de déformation, d'affaissement ou de bulles.