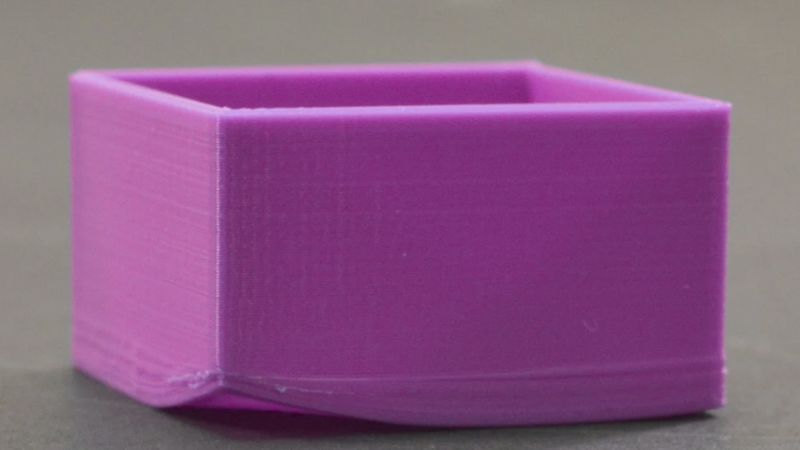
Le gauchissement peut être gênant. Pour les fabricants comme pour les concepteurs de produits, il est important de comprendre les causes profondes du gauchissement. La mise en œuvre de stratégies de prévention efficaces est essentielle pour maintenir une production de haute qualité et minimiser les coûts de production.
Dans ce guide complet, nous explorerons les principaux facteurs contribuant au gauchissement dans le moulage par injection et fournirons des solutions pratiques pour atténuer ce problème.
En appliquant ces connaissances, les fabricants peuvent améliorer l’efficacité de leur production, réduire les taux de rebut et, en fin de compte, fournir des pièces moulées par injection de qualité supérieure.
Qu'est-ce que le gauchissement du moulage
Le gauchissement est l’un des problèmes de qualité cruciaux dans le moulage par injection plastique, conduisant souvent à une instabilité dimensionnelle des pièces en plastique.
Le gauchissement désigne l'écart indésirable par rapport à la géométrie prévue du produit qui peut se produire dans les pièces en plastique pendant le processus de moulage par injection. Ce défaut se manifeste par des déformations telles que la torsion, la courbure ou le gondolement de la pièce moulée.
La gravité du gauchissement varie de légères déformations, à peine perceptibles à l'œil nu, à des distorsions importantes qui interfèrent avec la fonction ou l'assemblage de la pièce.
L'impact du gauchissement sur les produits moulés
La présence de déformations dans le moulage par injection a des conséquences importantes sur la qualité et la fonctionnalité des pièces en plastique :
- Qualité esthétique:L’attrait visuel est compromis, ce qui rend les produits finis moins compétitifs sur le marché.
- Stabilité dimensionnelle:Les pièces déformées peuvent ne pas s'adapter aux assemblages ou ne pas répondre aux dimensions précises requises pour l'interface avec d'autres composants.
- Déficiences fonctionnelles:Au-delà de l’esthétique, le gauchissement peut altérer les performances mécaniques et l’intégrité structurelle du composant.
Quelle est la cause du gauchissement dans le moulage par injection ?
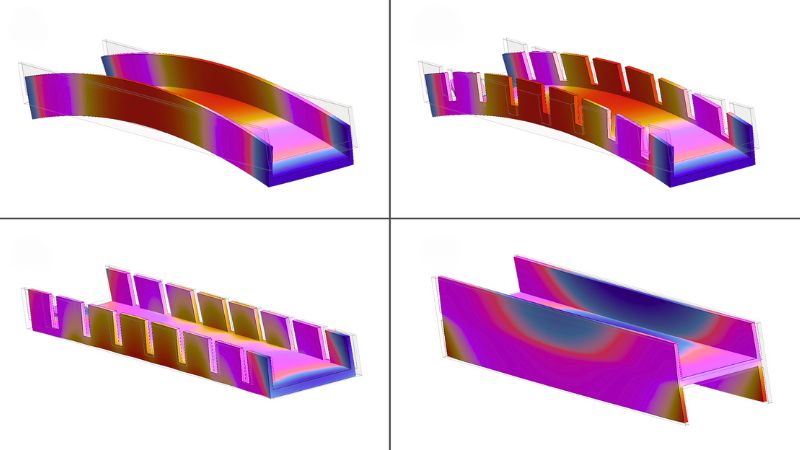
Cette section explore les subtilités de machine, moule, et facteurs matériels contribuant au gauchissement et fournit des solutions pratiques pour atténuer ces problèmes.
Erreurs de la machine
Pression ou durée d'injection inadéquate
Une pression d'injection ou un temps de maintien insuffisants peuvent entraîner un remplissage inadéquat du moule. Cela peut entraîner le refroidissement et la solidification de la matière plastique avant que le moule ne soit correctement rempli.
Les deux scénarios entraînent un mouvement incontrôlé des molécules pendant le refroidissement, ce qui entraîne un rétrécissement et un gauchissement inégaux.
Température incorrecte du canon
Si la température du cylindre est trop basse, la résine n'atteindra pas sa température d'écoulement appropriée, ce qui entraînera une solidification prématurée, un remplissage inadéquat du moule et, finalement, un rétrécissement et un gauchissement inégaux.
Temps de séjour inapproprié
Un temps de séjour inadéquat empêche une absorption uniforme de la chaleur dans toute la résine. Cela peut entraîner le durcissement et la solidification prématurée des parties sous-chauffées du matériau, ce qui entraîne un remplissage incomplet du moule et un gauchissement.
Tension interne excessive
Des pressions d’injection élevées peuvent créer des contraintes internes dans la pièce moulée, qui peuvent se manifester par un gauchissement après l’éjection du moule.
Temps de marche avant de la vis incorrect
Si le temps d'avancement de la vis est trop long, cela peut entraîner un surremplissage du moule, créant des contraintes internes qui entraînent un gauchissement.
Temps de refroidissement insuffisant
Un temps de refroidissement insuffisant peut empêcher la pièce de refroidir uniformément et complètement avant l'éjection, ce qui entraîne un rétrécissement et un gauchissement inégaux à mesure qu'elle continue de refroidir à l'extérieur du moule.
Erreurs de moisissure
Emplacement et conception inappropriés de la porte
Un positionnement incorrect de la buse peut entraîner un remplissage et un compactage irréguliers de la cavité du moule. Cela entraîne une répartition de la pression et des taux de refroidissement irréguliers, provoquant des déformations.
Placement inadéquat de la goupille d'éjection
Des éjecteurs mal positionnés ou insuffisants peuvent entraîner des contraintes inégales lors de l'éjection de la pièce du moule. Cela peut entraîner un gauchissement, en particulier dans les pièces à géométrie complexe.
Circuits de refroidissement déséquilibrés
Des circuits de refroidissement mal équilibrés peuvent provoquer un refroidissement inégal dans les cavités, entraînant une déformation de certaines pièces tandis que d'autres restent inchangées.
Erreurs de sélection des matériaux
Taux de rétrécissement élevés
Les matériaux présentant des taux de retrait élevés sont plus sujets au gauchissement.
Par exemple, les polymères semi-cristallins comme le polyéthylène (PE) et le polypropylène (PP) ont des taux de rétrécissement plus élevés que les polymères amorphes comme le polycarbonate (PC) ou le polystyrène (PS).
Rétrécissement irrégulier
Certains matériaux se rétractent différemment dans le sens de l'écoulement et dans le sens transversal. Ce retrait anisotrope peut entraîner des déformations, en particulier dans les pièces présentant de longs trajets d'écoulement.
Cristallinité
Les matériaux hautement cristallins sont plus sensibles au gauchissement en raison de leur tendance à rétrécir davantage lors du refroidissement.
Sensibilité à l'humidité
Certains matériaux, comme le nylon, sont hygroscopiques et peuvent absorber l'humidité de l'air. Cela peut entraîner des résultats de moulage incohérents et une déformation potentielle s'ils ne sont pas correctement séchés avant le traitement.
Comment réduire le gauchissement dans le moulage par injection ?
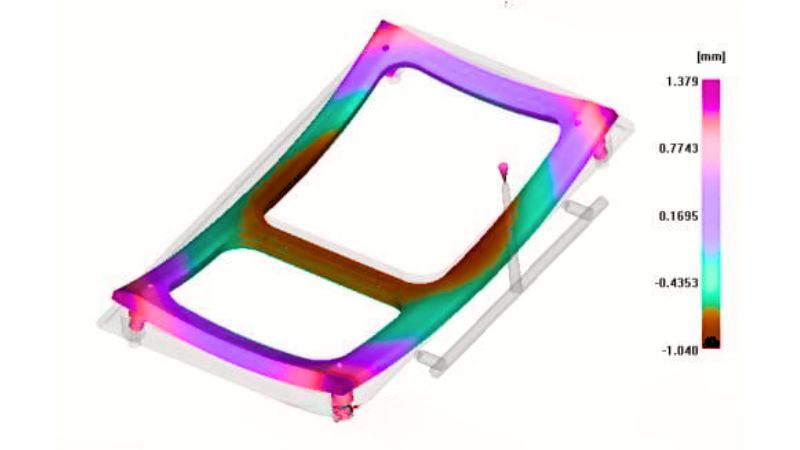
L'optimisation des paramètres de traitement est cruciale, en commençant par le réglage de la pression d'injection et du temps de maintien pour assurer un remplissage correct de la cavité du moule. Cela contraint les molécules de plastique et empêche tout mouvement incontrôlé pendant le refroidissement.
L'augmentation du temps de refroidissement permet un refroidissement complet et uniforme, contribuant ainsi à éviter les taux de retrait différentiels qui conduisent souvent à des déformations.
Le réglage précis de la température est tout aussi important ; l’augmentation de la température du cylindre garantit un flux de matériau adéquat tandis que le réglage de la température du moule en fonction des recommandations du fournisseur de résine favorise l’uniformité.
Dans la mesure du possible, la mise en œuvre de canaux de refroidissement conformes peut encore améliorer le refroidissement uniforme de la pièce.
Conception des moules et considérations sur les matériaux
L'optimisation des portes et des canaux en utilisant des types de portes appropriés pour des plastiques et des conceptions de produits spécifiques, la mise en œuvre de plusieurs portes pour les pièces plates et l'élargissement des portes et des canaux peuvent améliorer considérablement le remplissage du moule.
Le placement correct des broches d'éjection est également crucial ; s'assurer qu'elles sont suffisamment larges, bien réparties et situées à proximité des zones présentant la plus grande résistance à l'éjection peut empêcher le gauchissement lors du retrait des pièces.
Le choix et la manipulation des matériaux sont des facteurs clés. Le choix de résines moins sujettes à la déformation, comme les plastiques amorphes comme le polycarbonate et le polystyrène au lieu des plastiques cristallins, peut faire une différence substantielle.
Pour les pièces utilisant des inserts métalliques, le préchauffage à environ 100 °C permet de s'adapter aux différences de retrait entre le métal et le plastique, réduisant ainsi les contraintes et les déformations potentielles.
Optimisation de la conception et contrôle de la qualité
L'optimisation de la conception des pièces est un autre aspect essentiel. Le maintien d'une épaisseur de paroi uniforme sur toute la pièce favorise un refroidissement et un retrait uniformes, tandis que l'ajout de nervures de renforcement peut améliorer la rigidité de la pièce et réduire la tendance au gauchissement.
Coopérer avec un professionnel — Moldie
Travailler avec moisi peut conduire à la qualité et à l'efficacité dans le processus d'injection de plastique moulé. Nous sommes dotés de l'expertise nécessaire pour manipuler une gamme diversifiée de matières plastiques, garantissant que les produits en plastique résultants allient durabilité et esthétique.
Moldie met l'accent sur la précision dans ses techniques de fabrication. Notre approche comprend :
- Conception de moules avancée:En optimisant la taille et la forme de la porte, Moldie contribue à maintenir un flux et un refroidissement uniformes, ce qui entraîne moins de contraintes internes et une réduction du gauchissement.
- Sélection des matériaux:Leur connaissance des différents plastiques permet un choix éclairé du matériau, en adaptant les propriétés à l’application prévue et en atténuant les défauts.
- Optimisation du processus:Moldie ajuste avec précision la température du moule et les taux de refroidissement, car ces variables jouent un rôle essentiel dans la production de composants de haute qualité et sans déformation.
Nous pensons qu'une telle collaboration peut considérablement élever le niveau des composants en plastique produits, améliorant ainsi la fonctionnalité et l'apparence du produit final.