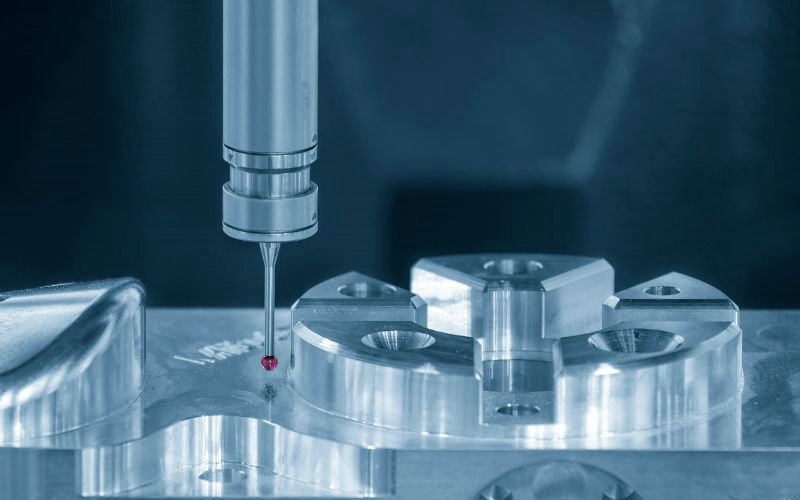
Le moulage par injection est l’un des procédés de fabrication les plus utilisés pour produire de grands volumes de pièces en plastique. Pour garantir une qualité constante des pièces et une efficacité de production optimale, température du moule est l’un des facteurs les plus critiques à contrôler. La température du moule a un impact significatif sur le comportement d'écoulement du plastique fondu lors du remplissage et sur la vitesse de refroidissement de la pièce. Si le moule est trop froid, la matière fondue aura du mal à remplir complètement la cavité, ce qui entraînera des tirs courts ou d'autres défauts. A l’inverse, si le moule est trop chaud, le plastique mettra plus de temps à se solidifier, augmentant ainsi les temps de cycle. Dans cet article, nous vous aiderons à mieux comprendre comment la température affecte le moulage par injection et les mesures spécifiques permettant de mieux contrôler la température du moule.
Explication des systèmes de contrôle de la température des moules
Composants d'un système de contrôle de la température des moules
Un système de contrôle de la température des moules se compose de plusieurs composants clés qui fonctionnent ensemble :
- Système de contrôle électronique : traite les informations provenant d’autres systèmes et émet des commandes
- Système mécanique (pompe de circulation) : Délivre la chaleur du système de chauffage au moule
- Système de surveillance du niveau de liquide : surveille les niveaux de liquide de refroidissement et signale les remplissages
- Système de chauffage : chauffe le liquide de refroidissement à la température réglée
- Système de refroidissement : élimine l'excès de chaleur, en utilisant souvent des échangeurs de chaleur à plaques pour un refroidissement indirect.
- Système de détection de température : mesure la température du moule et transmet les données au système de contrôle.
- Système de sécurité de décompression : évacue et relâche la pression si elle devient trop élevée
Types de contrôleurs de température de moule
Il existe deux principaux types de régulateurs de température de moule en fonction du fluide caloporteur utilisé :
1. Contrôleurs de température de l'eau
– Plage de température généralement inférieure à 180°C
– Type ordinaire : jusqu’à 120°C, type haute température : jusqu’à 180°C
2. Contrôleurs de température d'huile
– Utilisé pour des températures supérieures à 180°C, jusqu'à 350°C
– Type ordinaire : jusqu’à 200°C, type haute température : jusqu’à 350°C
Principe de fonctionnement
Voici une explication simplifiée du fonctionnement d'un contrôleur de température de moule à eau :
1. La pompe de circulation pousse l'eau à travers le système
2. Le système de chauffage chauffe l'eau à la température réglée
3. L'eau chaude circule dans les canaux du moule et transfère la chaleur.
4. Le système de détection de température mesure la température du moule
5. Si la température est trop basse, le système de contrôle signale au chauffage de s'allumer
6. Si la température est trop élevée, le système de refroidissement élimine l'excès de chaleur
7. Le système de décompression évacue le liquide de refroidissement si la pression devient dangereusement élevée.
En contrôlant avec précision la température du moule, ces systèmes contribuent à minimiser les défauts, à optimiser les temps de cycle et à améliorer la qualité globale et la cohérence des pièces dans le moulage par injection. Investir dans un bon système de contrôle de la température des moules adapté à vos besoins spécifiques en matière de moulage peut conduire à des gains d’efficacité de fabrication significatifs.
Impact de la température du moule sur le moulage par injection
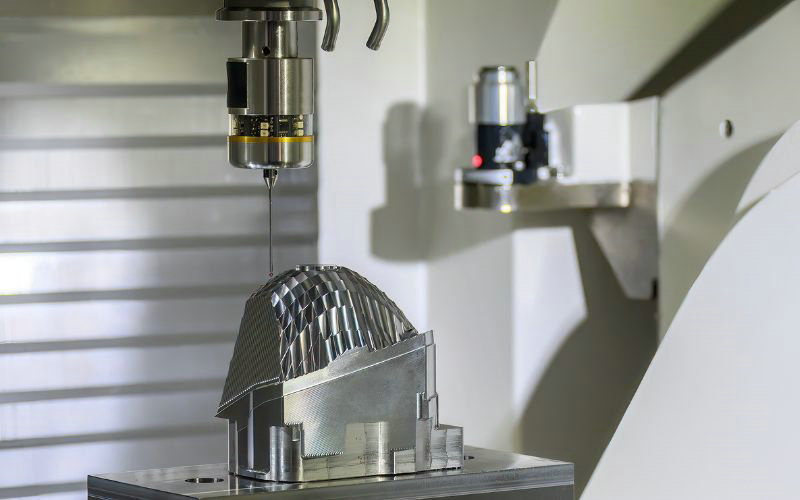
Effets de la basse température du moule
1. Mauvais aspect et finition de la surface
- Une basse température du moule réduit la fluidité du plastique fondu, ce qui peut entraîner un remplissage incomplet et une finition de surface moins brillante, en particulier pour des matériaux comme l'ABS.
- Si la température du moule est trop basse pour les surfaces texturées, la matière fondue risque de ne pas remplir complètement les détails fins de la texture, ce qui entraînera une mauvaise reproduction de la surface du moule.
2. Augmentation des contraintes internes et du gauchissement
- Une basse température du moule provoque un refroidissement rapide et un « gel » des molécules, créant ainsi des contraintes internes dans la pièce.
- Un refroidissement irrégulier et un retrait dus aux basses températures du moule peuvent entraîner une déformation et une instabilité dimensionnelle de la pièce moulée.
- Des lignes de soudure visibles peuvent se former sur la surface de la pièce, réduisant ainsi sa résistance.
3. Modifications des propriétés mécaniques
- Les basses températures du moule peuvent réduire la résistance à la traction de la pièce moulée par rapport aux températures plus élevées du moule.
- Un refroidissement rapide à basse température peut augmenter la fragilité de la pièce et réduire sa résistance aux chocs et à la fatigue.
4. Des temps de cycle plus longs
- Bien que les basses températures du moule puissent réduire le temps de refroidissement, elles nécessitent des pressions d'injection plus élevées pour remplir la cavité en raison de la fluidité réduite de la matière fondue.
- Cela peut augmenter la durée globale du cycle, en particulier pour les matériaux cristallins nécessitant un refroidissement suffisant pour assurer la stabilité dimensionnelle.
Effets de la température élevée du moule
1. Finition et apparence de surface améliorées
- Une température de moule plus élevée permet au plastique de s'écouler plus facilement et de remplir les détails fins de la surface, ce qui donne une finition de surface plus brillante et plus attrayante, en particulier pour des matériaux comme l'ABS.
- La composition plastique est plus proche de la surface du moule à des températures plus élevées, ce qui permet une meilleure reproduction de la texture.
2. Propriétés mécaniques améliorées
- Des températures de moule plus élevées peuvent améliorer la résistance à la traction de la pièce moulée par rapport à des températures de moule plus basses.
- Pour les plastiques cristallins, une température de moule élevée laisse plus de temps à la cristallisation, augmentant ainsi la rigidité et la résistance à la chaleur de la pièce.
3. Réduction des contraintes internes et du gauchissement
- Les températures élevées du moule ralentissent le processus de refroidissement, permettant aux molécules de se détendre et de s'orienter plus uniformément, réduisant ainsi les contraintes résiduelles dans la pièce.
- Un refroidissement plus progressif à des températures de moule plus élevées minimise le retrait différentiel et la déformation de la pièce moulée.
4. Augmentation des temps de cycle et risque de défauts
- Le principal inconvénient des températures élevées des moules est le temps de refroidissement plus long requis, ce qui augmente la durée globale du cycle et réduit la productivité.
- Des températures excessivement élevées peuvent faire adhérer le plastique au moule, créant des points lumineux ou d’autres défauts de surface.
- Il existe un plus grand risque de formation de bavures et de bavures si la température du moule est trop élevée, car le plastique reste fondu plus longtemps.
5. Dégradation possible des propriétés du matériau
- Certains polymères peuvent subir une dégradation thermique ou une oxydation s'ils sont traités à des températures de moule excessivement élevées, entraînant une réduction du poids moléculaire et des propriétés mécaniques.
- La combinaison d'une température élevée du moule, d'une température de fusion élevée et d'un long temps de séjour présente le plus grand risque de dégradation du matériau pendant le moulage.
Mesures pour mieux contrôler la température des moules
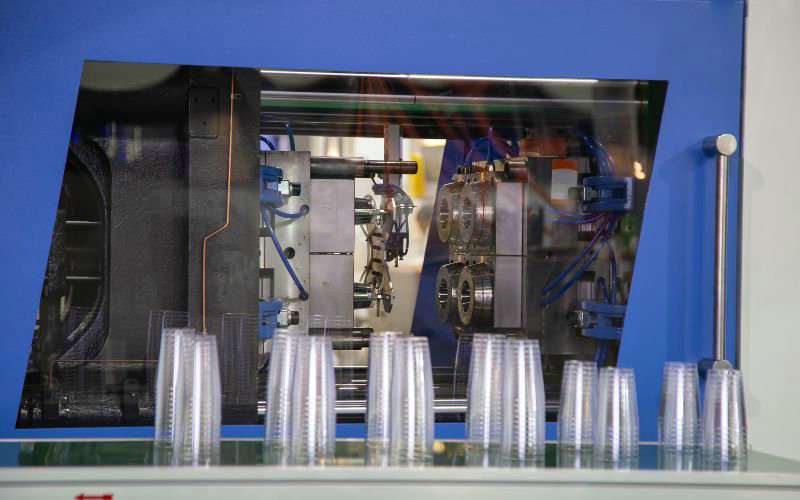
1. Utiliser des contrôleurs de température de moule
- Les contrôleurs de température des moules sont des appareils essentiels qui régulent et maintiennent des températures précises des moules. Ils fonctionnent à la fois à des fins de chauffage et de refroidissement.
- Sélectionnez un contrôleur de température de moule doté de capacités de débit et de pression suffisantes pour répondre aux besoins de votre moule spécifique.
2. Surveiller les débits du liquide de refroidissement
- Un débit de liquide de refroidissement adéquat est essentiel car il détermine la rapidité avec laquelle le moule peut être refroidi, influençant à la fois la qualité du produit et la durée du cycle.
- Vérifiez que le débit n'est ni trop faible, ce qui peut entraîner un mauvais contrôle de la température, ni trop élevé, ce qui peut être inutile et inefficace.
3. Établir un contrôle du gradient de température
- Maintenez une température constante dans tout le moule pour éviter les défauts. Un contrôle approprié du gradient de température minimise les contraintes internes à l'intérieur de la pièce moulée.
- Les concepteurs de moules doivent s'efforcer d'obtenir un différentiel de température ne dépassant pas 5 °C entre le noyau et l'empreinte afin de réduire le gauchissement.
4. Optimiser la conception des canaux de refroidissement
- L'emplacement, la profondeur et l'inclinaison des canaux de refroidissement ont un impact significatif sur l'uniformité de la température de la surface du moule.
- Visez une température de surface du moule uniforme en optimisant la profondeur du canal de refroidissement (idéalement 1 à 2,5 fois le diamètre du canal) et le pas (2,5 à 3 fois le diamètre du canal).
5. Sélectionnez les matériaux de moule appropriés
- Le matériau du moule a un impact profond sur l’échange thermique. Tenez compte de la conductivité thermique lors de la sélection des matériaux de moule.
- Pour les applications à haute tolérance, les alliages de cuivre peuvent être nécessaires pour maintenir un faible différentiel de température et réduire le gauchissement, tandis que des matériaux moins coûteux comme l'acier H13 peuvent être utilisés pour les pièces à faible tolérance.
6. Mettre en œuvre des techniques de chauffage et de refroidissement rapides
- Le moulage par cycle thermique rapide (RHCM) consiste à chauffer rapidement le moule au-dessus du point de fusion pour faciliter l'écoulement du plastique, puis à le refroidir rapidement pour accélérer la solidification.
- Le RHCM peut améliorer la qualité et la précision des surfaces, mais il est gourmand en énergie et doit être réservé à des applications spéciales.
En mettant en œuvre ces mesures et en surveillant en permanence les performances de température du moule, les mouleurs par injection peuvent obtenir un contrôle plus strict sur ce paramètre critique du processus. Cela conduit à une qualité améliorée des pièces, à une réduction des défauts et à des temps de cycle optimisés pour une plus grande efficacité de fabrication.
Température de moulage par injection pour différents plastiques
Le tableau suivant résume les températures de moulage par injection recommandées pour différents plastiques :
Type de plastique | Matériel | Température de fusion (°C) | Température du moule (°C) |
---|---|---|---|
Plastiques amorphes | abdos | 210-275 | 50-90 |
PS | 170-280 | 10-60 | |
PMMA | 180-260 | 50-80 | |
PC | 280-320 | 80-120 | |
Plastiques semi-cristallins | PP | 200-280 | 30-80 |
PEHD | 210-300 | 20-70 | |
PEBD | 160-260 | 20-70 | |
POM | 160-280 | 50-120 | |
PA6 | 230-290 | 40-120 | |
PA66 | 260-300 | 40-120 | |
PBT | 240-275 | 60-100 | |
Plastiques haute température | PSE | 330-380 | 120-180 |
COUP D'OEIL | 340-390 | 120-160 |
Remarque : La plage de températures de moulage optimale dépend de la qualité spécifique, des additifs, de la géométrie de la pièce, de l'équilibre souhaité des propriétés et du temps de cycle. Un contrôle minutieux de la température de fusion et de la température du moule est essentiel pour obtenir une qualité élevée des pièces et une efficacité de fabrication dans le moulage par injection.