La mayor cantidad de molde de inyección de plástico que se puede inyectar durante un ciclo de moldeo se conoce como tamaño de inyección. Los pellets se introducen en el conjunto de barril y tornillo a través de la tolva.
Mediante la técnica de moldeo por inyección, se inyecta material fundido en la cavidad del molde para crear grandes cantidades de piezas de plástico.
En el proceso de moldeo por inyección de plástico, la materia prima se introduce en el cilindro, se funde y luego se inyecta plástico en la cavidad del molde para enfriarlo y solidificarlo después de que se cierra el molde. Finalmente, se abre el molde y se expulsan los componentes.
Cómo calcular el tamaño del disparo
La duración de los tiempos de residencia está influenciada por el tamaño del disparo y el cañón, lo que también puede afectar la calidad del producto final. Las duraciones de residencia prolongadas y la degradación del polímero pueden provenir de tamaños de disparo pequeños que requieren poca capacidad de barril.
Los tamaños de disparos pequeños que ocupan menos de 20% de la capacidad del barril frecuentemente dan como resultado tiempos de residencia prolongados, lo que a su vez provoca la degradación del polímero y un control inadecuado del proceso.
Por otro lado, los tamaños de perdigones grandes y los niveles de llenado del barril superiores a 50% pueden causar una fusión desigual y una recuperación lenta del tornillo.
Además, los tornillos más grandes suelen tener capacidades de presión plástica más bajas. Los tamaños de perdigones grandes, que ocupan más de 65% de la capacidad del barril, con frecuencia causan problemas de calidad de la fusión, como falta de fusión, mala uniformidad de la fusión y largos tiempos de recuperación del tornillo.
Para estar seguro, puede considerar realizar un pedido de dos barriles. Aún más, los moldes se pueden utilizar con dos barriles. Cuando ordena un segundo barril con la nueva máquina, puede estar gratamente complacido por su bajo costo. Los barriles se pueden cambiar en menos de 30 minutos con las especificaciones correctas y un operador experimentado, incluso si el barril está caliente.
Fórmula para el tamaño de inyección de molde en moldeo por inyección
La fórmula más simple para calcular el tamaño de la inyección del molde es:
Contracción + Volumen de abeto + Volumen de producto + Volumen de corredor = Tamaño de inyección de molde
Capacidad de disparo de la máquina de fórmula/Tamaño de disparo
El peso o volumen total que inyecta el tornillo durante un ciclo de moldeo se expresa como capacidad de inyección de la máquina (g)/tamaño de inyección de la máquina (mm), también conocida como capacidad de inyección de la máquina.
Sus cálculos al considerar la presión deben ser los siguientes:
Carrera X Superficie del pistón del tornillo = volumen de inyección
Fuerza de inyección/superficie del pistón de tornillo = presión de inyección
Por lo tanto:
Volumen máximo de inyección por unidad cúbica X presión máxima de inyección (bar por unidad cúbica)/1000 = capacidad de disparo de la unidad de inyección.
Los cálculos al usar el peso del tornillo y la densidad del material deben ser los siguientes:
Masa/densidad= volumen
ᴨ*D2*Tamaño de disparo/4= Barril/Volumen de disparo
Factores que afectan el tamaño de la inyección del producto
Hay varios factores que debe tener en cuenta al calcular el tamaño de una toma. Estos factores son los siguientes:
- Debe tener en cuenta el volumen de la picea, el volumen de la colada y el volumen del producto al determinar el tamaño de la inyección. Esto se debe a que el polímero debe llenar el volumen de la picea, la colada y el producto cuando se inyecta en el molde.
- Otro tema importante que afecta los cálculos del tamaño de la inyección es la contracción del polímero. La contracción resulta del enfriamiento del polímero fundido. Debido a las variadas densidades de los polímeros, la contracción del molde varía.
- El tipo y la cantidad de aditivos de un polímero pueden cambiar sus características de densidad y flujo.
Estos factores pueden ayudarlo a estimar el tamaño del disparo, el volumen y la capacidad del cañón.
Unidad de Inyección
El propósito de la unidad de inyección es fundir el material plástico de manera uniforme antes de inyectarlo en el molde a una presión y caudal predeterminados. Estas son actividades exigentes porque los fluoropolímeros tienen una conductividad térmica limitada, un alto calor específico y una alta viscosidad de fusión.
Una vez más, se han desarrollado numerosas variaciones para abordar los problemas complejos en cuestión. Se puede hacer una clasificación general de las variaciones en cuatro conceptos de unidad de inyección primaria:
- Émbolo o ariete de una sola etapa
- ariete de doble etapa
- Tornillo con una etapa
- Tornillo/pistón con dos etapas
Aunque todavía existe en máquinas diminutas y algunos equipos especializados, la unidad de ariete de una sola etapa es esencialmente obsoleta debido a su ineficacia en el calentamiento, la mezcla y la transmisión de presión. Se beneficia de la simplicidad y la asequibilidad.
Además, el ariete de dos etapas es casi obsoleto. El ariete sigue siendo un mezclador y calentador ineficaz a pesar de un intento de mejorarlo separando las operaciones de flujo de presión y calentamiento.
La unidad de pistón/tornillo de dos etapas separa aún más las funciones de flujo y calor mediante el uso de un pistón para inyección en lugar de un tornillo para mezclar y calentar. La idea es atractiva porque ambos son herramientas efectivas para sus respectivas tareas.
Además, la unidad de inyección a menudo se clasifica utilizando la presión de inyección máxima y el volumen de inyección disponible. La mayor presión posible en el extremo aguas abajo del tornillo se denomina presión de inyección. Esto depende del diámetro del tornillo y de la fuerza que empuja contra él.
Sin embargo, asegúrese de no confundirla con la presión en la línea hidráulica que actúa sobre el cilindro de inyección, que acciona el tornillo, ni debe interpretarse como la presión requerida para llenar las cavidades del molde. Debido a las pérdidas de presión en los sistemas de alimentación de boquillas y moldes, esto es sustancialmente menor.
La serie principal de acciones de la unidad de inyección es la siguiente:
- El material se calienta y se funde a medida que gira el tornillo, luego se transporta a lo largo de los tramos del tornillo hasta el extremo aguas abajo del tornillo. La boquilla del cañón se cierra mediante válvula mecánica, térmica o por la existencia de un moldeo anterior.
Hasta que se haya acumulado suficiente masa fundida para fabricar la siguiente pieza moldeada, la masa fundida que se acumula fuerza al tornillo que aún gira hacia atrás contra una resistencia controlada (la contrapresión). La rotación del tornillo se detiene aquí. Es hora de estar listo para el derretimiento.
- Cuando se abre la boquilla del cilindro, el tornillo avanza en dirección axial sin girar, actuando como un ariete. Como resultado, la masa fundida reunida frente al extremo de aguas abajo del tornillo es forzada (inyectada) a través de la boquilla y dentro del molde.
Para evitar que el material fundido fluya hacia abajo por los tramos del tornillo, se puede instalar un sistema de válvula en el extremo aguas abajo del tornillo. Esta es la etapa de inyección o llenado del molde.
- Una vez que se ha llenado el molde, la presión del tornillo se mantiene durante un breve período de tiempo para compensar la contracción volumétrica de la masa fundida de enfriamiento dentro del molde. La fase de embalaje o mantenimiento es ahora.
- Finalmente, se llega a la fase de espera, donde se reanuda el ciclo de la unidad de inyección con la rotación del tornillo y se derrite la preparación mientras el molde se mantiene cerrado para permitir que el moldeado se enfríe a la temperatura de eyección.
Hay caídas de presión significativas cuando el plástico fundido se introduce a la fuerza en la boquilla de inyección y, posteriormente, a través del sistema de alimentación del molde y las cavidades. No se pueden utilizar reglas simples para calcular estas pérdidas de presión.
Unidad de sujeción
El cierre del molde se mantiene contra las fuerzas creadas cuando el plástico se empuja dentro de un molde cerrado mediante presión de inyección utilizando una unidad de sujeción para una IMM. Tiene un sistema de accionamiento que puede mover el plato móvil de la máquina de moldeo por inyección en al menos una dirección.
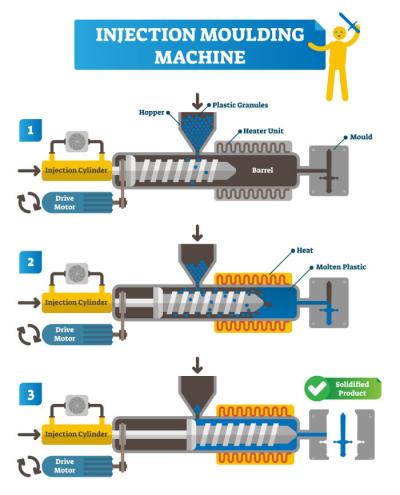
Tipos de unidades de sujeción
Hay varios tipos de unidades de sujeción en el proceso de moldeo por inyección. Son los siguientes:
Sujeción tipo palanca
Un dispositivo mecánico que amplifica la fuerza es una palanca. Dos barras están conectadas y terminan con un pivote en una máquina de moldeo. El extremo de una barra está conectado a un plato fijo, mientras que el otro está conectado a un plato móvil. La palanca tiene forma de V cuando se abre el molde. Las dos barras forman una línea recta cuando se aplica presión al pivote.
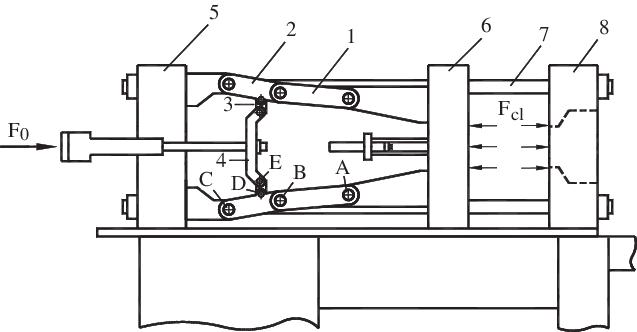
Los beneficios de la sujeción del tipo de palanca incluyen que requiere menos dinero y menos caballos de fuerza y proporciona un plan positivo del molde. Además, los contratiempos de la sujeción del tipo de palanca son que requiere un alto mantenimiento y es difícil de realizar.
Sujeción Hidráulica
En este caso, el RAM del sistema hidráulico está ligado al plato móvil, y una unidad de sujeción accionada por un cilindro hidráulico está conectada directamente al molde móvil cerrado. El cilindro hidráulico tiene dos secciones: la entrada de aceite y la salida.
El aceite empuja el RAM hacia adelante cuando ingresa al cilindro bajo presión, lo que hace que se cierren la placa móvil y el molde. Además, el retorno de RAM y el molde están abiertos cuando se libera aceite del cilindro.
Algunas ventajas de la sujeción hidráulica incluyen el fácil control de la velocidad de sujeción y el soporte en cualquier ángulo, la medición simple de la fuerza de sujeción, la configuración sencilla del modo y el ajuste de la fuerza de sujeción, y su simplicidad en el mantenimiento.
Los inconvenientes de este tipo de sujeción son que cuesta más y es más caro que un sistema de palanca y una abrazadera de nombre positivo.
Unidad de sujeción de tipo magnético
Los módulos magnéticos dentro de las placas o platos magnéticos de sujeción del molde producen la fuerza de sujeción. El panel de interfaz puede controlar la sujeción de moldes, el cambio de moldes y la magnetización y desmagnetización de las platinas.
Los beneficios de esta unidad de sujeción incluyen que solo se requiere electricidad durante las fases de magnetización y desmagnetización, no durante la sujeción, medición de la fuerza de sujeción en tiempo real con muchas funciones de seguridad y mantenimiento gratuito.
Peso de inyección de molde
La cantidad de material inyectado en el molde para llenarlo, incluido el sistema de alimentación, se conoce como "peso de la inyección del molde" o "peso de la inyección del producto". Por otro lado, el peso de la picea, el corredor y la puerta son los componentes del peso del tiro. La distancia que cubre el tornillo para llenar el producto, incluido el sistema de alimentación, se conoce como tamaño de inyección del molde/producto.
Conclusión
Usando la técnica de moldeo por inyección, el plástico crudo se funde, se inyecta en el molde, se deja enfriar y solidificar, y luego se expulsa el objeto terminado. El tamaño de la inyección es crucial porque evita que el polímero se llene por debajo de lo normal y que se derrame. Otros factores, como la capacidad del barril, también afectan el proceso general de moldeo por inyección.