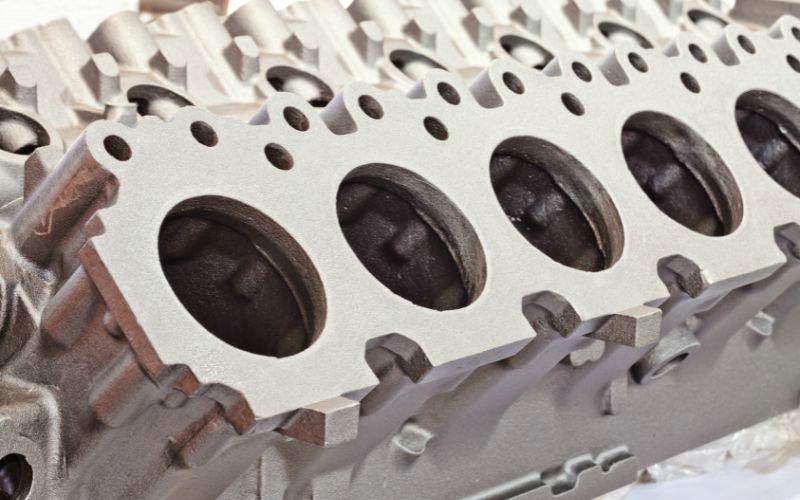
¿Qué es la fundición a presión?
La fundición a presión es un proceso de fabricación que implica verter o inyectar metal fundido en moldes, conocido como muere. El metal que normalmente se utiliza en este proceso puede incluir zinc, aluminio y sus aleaciones. El suyo es un viaje a través de un procedimiento ampliamente adoptado por su eficiencia en tiradas de producción de gran volumen.
Cuando se inicia la fundición a presión, el metal se funde en un horno y luego se inyecta en las matrices a alta presión. Este método es popular por su capacidad para producir piezas con precisión, detalles intrincados y un excelente acabado superficial, cualidades demandadas en sectores como el automotriz, el aeroespacial y el electrónico.
Los fabricantes buscan mucho la fundición a presión debido a su capacidad para producir piezas uniformes con una calidad constante. Ya sea que lo use para crear complejos componentes de cajas de cambios para vehículos o carcasas elegantes y duraderas para productos electrónicos, la fundición a presión es un pilar de la fabricación moderna, especialmente cuando la precisión y el volumen son esenciales.
Proceso de fundición a presión
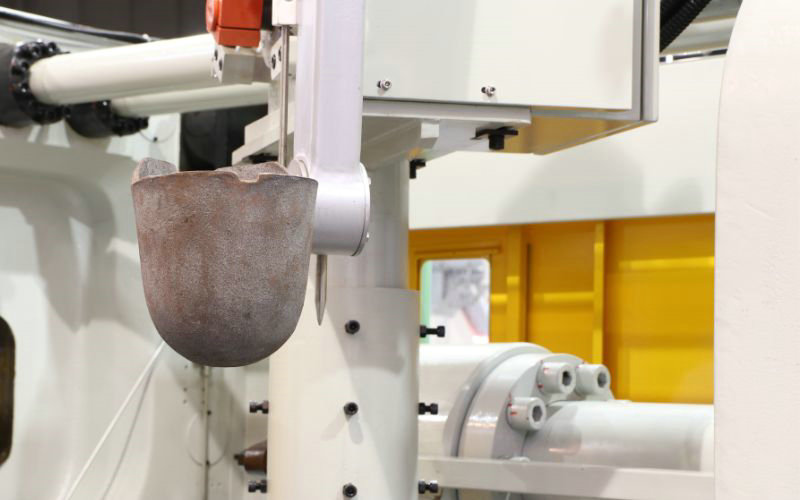
Hay tres tipos principales de procesos de fundición a presión: fundición a presión por gravedad, fundición a presión en cámara fría y fundición a presión en cámara caliente.
Fundición a presión por gravedad
En la fundición a presión por gravedad, el metal fundido se vierte directamente desde una cuchara a una matriz permanente o semipermanente. La cavidad se llena sin más fuerza que la gravedad. Las ventajas de la fundición a presión por gravedad incluyen la capacidad de producir piezas fundidas densas y de alta calidad con excelentes propiedades mecánicas adecuadas para el tratamiento térmico. Es rentable para producción de volumen pequeño a mediano.
Fundición a presión en cámara fría
En la fundición a presión en cámara fría, el horno de fusión está situado separado de la máquina de fundición a presión. Para cada ciclo, se vierte una cantidad precisa de metal fundido en la cámara de perdigones sin calefacción de la máquina; luego, un émbolo hidráulico fuerza el metal hacia el interior del troquel bajo altas presiones de entre 2000 y 20 000 psi. La fundición a presión en cámara fría se utiliza para aleaciones con puntos de fusión más altos, como el aluminio. Produce piezas resistentes y duraderas, pero tiene tiempos de ciclo más lentos que una cámara caliente.
Fundición a presión en cámara caliente
En la fundición a presión en cámara caliente, el mecanismo de inyección se sumerge en un charco de metal fundido, que se introduce en la matriz a través de un cuello de cisne y un pistón. Al comienzo de cada ciclo, el pistón se retrae, permitiendo que el cuello de cisne se llene de metal fundido. Luego, el pistón fuerza el metal a través del cuello de cisne hacia el troquel a presiones de 1000 a 5000 psi. La fundición a presión en cámara caliente se utiliza para aleaciones con puntos de fusión bajos como el zinc y el magnesio. Permite tiempos de ciclo más rápidos y puede producir piezas complejas con porosidad reducida.
Aplicaciones de fundición a presión
Automotor: La fundición a presión se emplea ampliamente en el sector del automóvil. Encontrará componentes como bloques de motor, piezas de transmisión y elementos estructurales fabricados mediante este proceso. La capacidad de producir piezas resistentes y duraderas de forma rápida y eficiente hace que la fundición a presión sea la opción preferida de los ingenieros automotrices.
- Componentes del motor
- Cajas de cambios
- Marcos de coche
Aeroespacial: La industria aeroespacial valora la fundición a presión para crear piezas complejas que requieren precisión y puede soportar condiciones duras. Los componentes como el tren de aterrizaje, la instrumentación de la cabina y las piezas del motor suelen ser de fundición a presión.
- Cajas de instrumentación
- Piezas del tren de aterrizaje
- Componentes del motor
Electrónica: En electrónica, la fundición a presión se utiliza para crear elementos como conectores, carcasas y disipadores de calor. Estas piezas se benefician de la capacidad de la fundición a presión para formar diseños complejos con un alto nivel de conductividad térmica.
- Disipadores de calor
- Conectores
- Cerramientos
¿Qué es el moldeo por inyección de metales?
El moldeo por inyección de metal (MIM) le ofrece un proceso de fabricación para producir piezas complejas en volúmenes medianos a altos. MIM combina la libertad de diseño y la complejidad de las formas que se encuentran en el moldeo por inyección de plástico con la resistencia e integridad excepcionales del metal.
Aquí hay una descripción general concisa de MIM:
- Materiales: Su elección de materiales en MIM generalmente incluye metales ferrosos como el acero inoxidable, que proporciona resistencia y durabilidad significativas al producto final.
- Fuerza y precisión: Las piezas MIM son conocidas por su impresionante resistencia y precisión. Mantienen tolerancias estrictas, lo que los hace adecuados tanto para industrial y médico aplicaciones.
- Geometrías complejas y paredes delgadas: Con MIM, puede crear piezas con geometrías complejas y paredes delgadas, lo que podría resultar desafiante o imposible mediante los procesos tradicionales de trabajo del metal.
Proceso de moldeo por inyección de metal
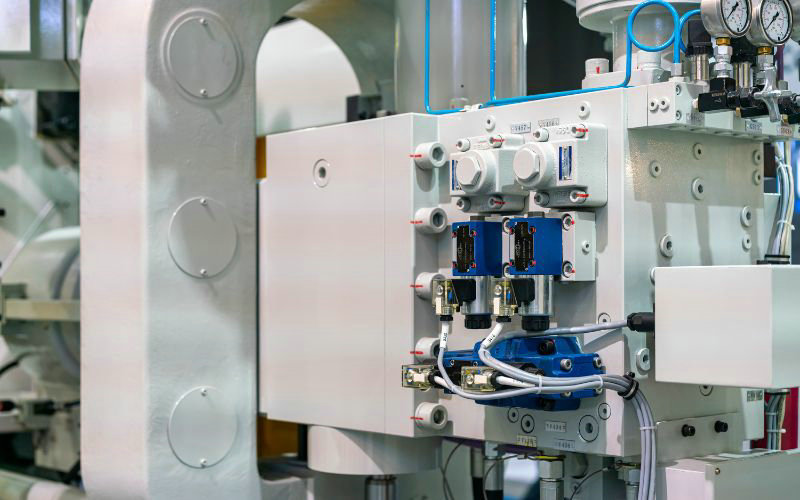
Su comprensión de MIM comienza con su material principal: un materia prima que consiste en un polvo metálico fino y un material aglutinante polimérico. Los metales comunes utilizados en este proceso incluyen acero inoxidable, titanio, aleaciones de níquel y aleaciones de cobre. En sus etapas iniciales, MIM es similar al moldeo por inyección de plástico; la materia prima se calienta hasta que se vuelve viscosa y puede inyectarse en la cavidad de un molde.
Una vez que la pieza moldeada esté fraguada, comienza el proceso de desaglomerado. Esto implica eliminar la mayor parte del aglutinante, lo que prepara la pieza para la sinterización. Durante la sinterización, su pieza está expuesta a altas temperaturas que unen las partículas de metal y garantizan su integridad.
Después de la sinterización, descubrirá que la pieza se ha encogido significativamente, normalmente entre 15 y 201 TP3T. Sin embargo, el proceso de sinterización le permite lograr una precisión dimensional y un acabado superficial excelentes, lo que a menudo minimiza la necesidad de mecanizado posterior. MIM es muy rentable cuando se trata de producir piezas pequeñas en grandes volúmenes debido al menor desperdicio de material y la capacidad de mantener tolerancias estrictas sin un trabajo de acabado extenso.
En última instancia, el moldeo por inyección de metal ofrece una combinación única de calidad, eficiencia y versatilidad dentro de los procesos de fabricación. Su capacidad para utilizar una variedad de metales y lograr características de materiales específicas, como dureza, resistencia a la tracción y resistencia a la temperatura, lo convierte en un proceso valioso en numerosas industrias.
Aplicaciones de moldeo por inyección de metal (MIM)
El moldeo por inyección de metal (MIM) es preciso y rentable, y es adecuado especialmente para la producción en masa de componentes de tamaño pequeño y mediano. Encontrará aplicaciones MIM en diversas industrias debido a su capacidad para producir formas complejas con un excelente acabado superficial.
Aeroespacial y Automotriz:
- MIM es ideal para fabricar piezas como manijas de puertas, bisagras y componentes de motores debido a su alta resistencia y durabilidad.
Médico y Dental:
- La industria médica se beneficia de la precisión de MIM en la creación de herramientas, implantes y soportes quirúrgicos que requieren biocompatibilidad.
Electrónica de consumo:
- Los componentes pequeños, como piezas de teléfonos móviles o conjuntos de cámaras, aprovechan la destreza de MIM en miniaturización y capacidades de diseño detallado.
Industria de armas de fuego:
- MIM se utiliza para fabricar diversos componentes de armas de fuego, incluidos gatillos, martillos y piezas de mira que exigen tolerancias y resistencia estrictas.
Equipos industriales generales:
- Encontrará MIM en la producción de componentes, conectores y válvulas de bombas debido a su consistencia y capacidad de producción de alto volumen.
En estas aplicaciones, MIM proporciona beneficios que incluyen:
- Materiales de alta densidad con grandes propiedades mecánicas.
- Capacidad de integrar funciones como roscas, engranajes y canales internos sin operaciones secundarias
- Producción de piezas cercanas a su forma final, minimizando el desperdicio.
Fundición a presión vs MIM: ventajas y desventajas
Ventajas de MIM sobre la fundición a presión
1. MIM puede producir piezas pequeñas y complejas con características intrincadas y paredes delgadas que serían desafiantes o imposibles con la fundición a presión.
2. MIM ofrece una gama más amplia de materiales, incluidos metales ferrosos, aceros inoxidables, titanio y aleaciones de níquel. La fundición a presión suele limitarse a metales no ferrosos como aluminio, zinc y magnesio.
3. Las piezas MIM tienen excelentes propiedades mecánicas, alta resistencia y resistencia al desgaste debido al proceso de sinterización.
4. MIM proporciona tolerancias más estrictas y puede tener una precisión de 0,3 mm.
5. MIM prácticamente no tiene desperdicio porque todo el material se inyecta directamente en el molde.
Desventajas de MIM en comparación con Die Casting
1. MIM es generalmente más costoso que la fundición a presión debido a las complejas herramientas y los múltiples pasos de procesamiento.
2. MIM tiene una vida útil más baja (entre 150.000 y 300.000 disparos) en comparación con la fundición a presión (más de 1 millón de disparos).
3. Las piezas MIM pueden encogerse significativamente (hasta 30%) durante la sinterización, lo que requiere un diseño cuidadoso del molde. La fundición a presión tiene una contracción mucho menor.
4. MIM tiene altos costos iniciales de automatización y configuración.
Ventajas de la fundición a presión sobre MIM
1. La fundición a presión suele ser más barata que la MIM, hasta 30% menos costosa en algunos casos.
2. La fundición a presión tiene una vida útil más larga (más de 1 millón de disparos) en comparación con MIM (150.000-300.000 disparos).
3. La fundición a presión no requiere operaciones secundarias después de que la pieza es expulsada del molde.
4. La fundición a presión puede acomodar inserciones y piezas hechas de otros materiales incrustadas en la fundición.
Desventajas de la fundición a presión en comparación con el MIM
1. La fundición a presión tiene dificultades para producir piezas pequeñas e intrincadas con características finas y paredes delgadas.
2. La fundición a presión se limita principalmente a metales no ferrosos. Los metales ferrosos tienen puntos de fusión muy altos, lo que reduce la vida útil del troquel.
3. La porosidad debida a los gases atrapados es un problema común en la fundición a presión, lo que reduce la resistencia mecánica.
4. La fundición a presión requiere matrices costosas para soportar la alta presión y las temperaturas del metal fundido.
En resumen, MIM destaca en la producción de piezas pequeñas y complejas con excelentes propiedades mecánicas en una amplia gama de materiales. Sin embargo, es más caro y tiene un tiempo de ciclo más largo que la fundición a presión. La fundición a presión es más económica y adecuada para piezas más simples y más grandes en metales no ferrosos con tiempos de producción más rápidos, pero tiene problemas con las características complejas y la porosidad.
Comparación: moldeo por inyección de metal versus fundición a presión
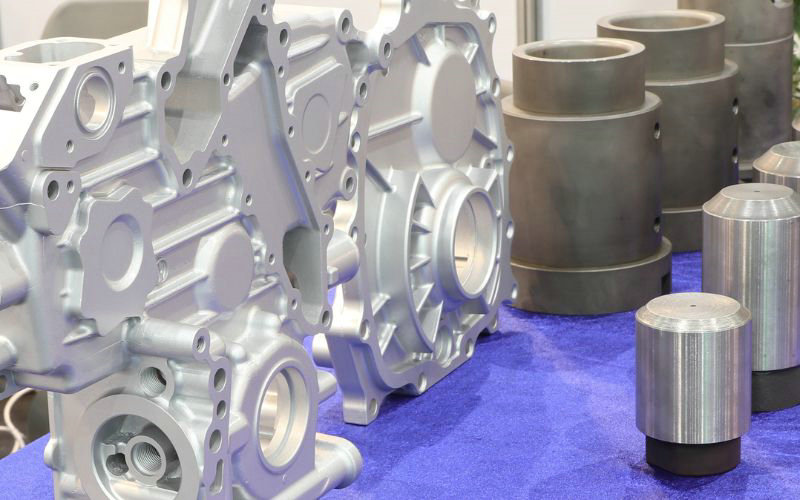
1. Precisión y tolerancias
Moldeo por inyección de metales (MIM): MIM logra piezas muy precisas con tolerancias relativamente ajustadas, normalmente con una precisión de 0,3 mm. Esta precisión se debe a los finos polvos metálicos utilizados, que permiten geometrías detalladas y complejas.
fundición a presión: La fundición a presión generalmente ofrece una buena precisión dimensional, pero no tan alta como MIM. La tolerancia típica para la fundición a presión es de alrededor de ±0,0005 pulgadas, lo que es menos preciso en comparación con las capacidades de MIM. Las variaciones en las dimensiones a menudo requieren recortes adicionales para cumplir con las especificaciones.
2. Materiales necesarios
Moldeo por inyección de metales (MIM): MIM puede utilizar una amplia gama de materiales, incluidos metales ferrosos y no ferrosos, aceros inoxidables, titanio y aleaciones de níquel. Esta versatilidad permite la producción de piezas con propiedades específicas adaptadas a diversas aplicaciones.
fundición a presión: Utiliza principalmente metales no ferrosos como aluminio, zinc y magnesio. Si bien la fundición a presión puede utilizar metales ferrosos, estos materiales tienen puntos de fusión muy altos, lo que puede reducir significativamente la vida útil del molde.
3. Comparación de velocidades
Moldeo por inyección de metales (MIM): El proceso MIM implica múltiples pasos, que incluyen mezcla, moldeo por inyección, desaglomerado y sinterización, lo que lo hace generalmente más lento que la fundición a presión. Sin embargo, una vez establecida la producción, MIM puede producir de manera eficiente grandes volúmenes de piezas.
fundición a presión: Conocida por su rápida capacidad de producción, la fundición a presión es más rápida y especialmente adecuada para tiradas de producción de gran volumen. El proceso permite la creación rápida de piezas de gran tamaño gracias a sus técnicas de inyección a alta presión.
4. Acabado superficial
Moldeo por inyección de metales (MIM): Normalmente proporciona un acabado superficial de alta calidad que a menudo no requiere posprocesamiento adicional. El proceso de sinterización ayuda a lograr un acabado suave.
fundición a presión: Las piezas normalmente salen del molde con un buen acabado superficial, pero es posible que sea necesario recortar el exceso de metal. La calidad de la superficie se considera generalmente media en comparación con MIM.
5. Costos de fabricación
Moldeo por inyección de metales (MIM): Si bien los costos iniciales de configuración y herramientas pueden ser altos, MIM puede ser rentable para producir piezas complejas en grandes volúmenes debido a la reducción de desperdicios y las mínimas necesidades de posprocesamiento.
fundición a presión: Generalmente es menos costoso en términos de costos iniciales y es más rentable para piezas más grandes y producción de gran volumen. Sin embargo, la rentabilidad disminuye para piezas muy complejas o más pequeñas.
6. Diferencias de moho
Moldeo por inyección de metales (MIM): Los moldes utilizados en MIM pueden ser menos duraderos en comparación con la fundición a presión y, por lo general, soportan entre 150 000 y 300 000 disparos. Sin embargo, los moldes MIM permiten una mayor complejidad en el diseño de piezas.
fundición a presión: Los moldes están diseñados para soportar altas presiones y temperaturas, lo que los hace más duraderos, con una vida útil de más de 1 millón de disparos. Sin embargo, ofrecen menos flexibilidad en términos de complejidad de las piezas en comparación con los moldes MIM.