El moldeo por inyección es un proceso de fabricación ampliamente utilizado para producir piezas de plástico mediante la inyección de material fundido en un molde. El proceso se basa en un componente crítico llamado compuerta, que controla el flujo de plástico fundido hacia la cavidad del molde. Tener el diseño de puerta correcto es esencial para el éxito de sus piezas moldeadas por inyección, ya que afecta su apariencia, tiempos de ciclo y diversas características.
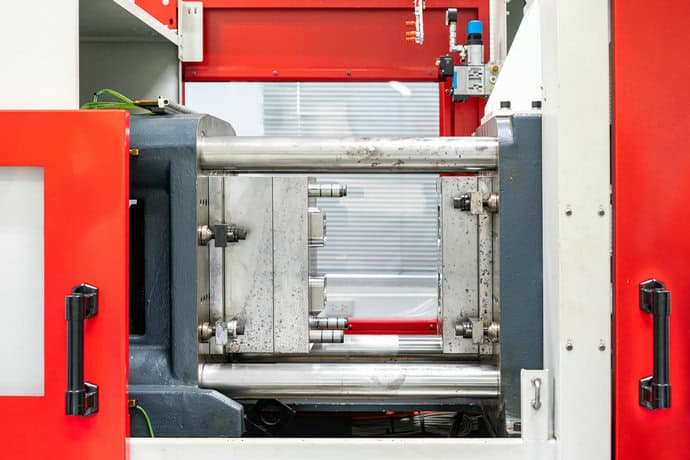
En el moldeo por inyección de compuerta, el plástico fundido fluye a través de una abertura diseñada específicamente, a menudo pequeña, antes de ingresar a la cavidad del molde. Esta puerta de enlace actúa como un camino para el material fundido desde la boquilla hasta el núcleo de la herramienta. El diseño de la compuerta de inyección debe adaptarse al proyecto específico para evitar posibles defectos y garantizar un producto final de alta calidad.
Conclusiones clave
- Las compuertas de moldeo por inyección controlan el flujo de plástico fundido hacia la cavidad del molde, lo que contribuye al éxito de las piezas moldeadas.
- El diseño correcto de la puerta garantiza productos finales de alta calidad y minimiza los posibles defectos.
- El moldeo por inyección de puerta afecta varios aspectos de una pieza, incluidos los cosméticos, los tiempos de ciclo y las características específicas.
Conceptos básicos del moldeo por inyección
El moldeo por inyección es un proceso de fabricación ampliamente utilizado en el que un material, normalmente plástico o resina, se funde y se inyecta en la cavidad de un molde a alta presión. El material se enfría y solidifica dentro del molde, tomando la forma de la cavidad. Una vez que la pieza se ha enfriado lo suficiente, se expulsa del molde y se repite el proceso para la siguiente pieza.
Se utilizan varios tipos de compuertas, como compuertas laterales, compuertas de disco o diafragma, compuertas de anillo y compuertas de radios. La elección del tipo de compuerta correcto depende de la geometría, la aplicación y la concentricidad requerida de la pieza.
Materiales juegan un papel importante en el proceso de moldeo por inyección. Los materiales comunes utilizados en este proceso incluyen polímeros termoplásticos, polímeros termoestables, elastómeros e incluso metales en algunos casos. La elección del material depende de factores como el diseño de la pieza, el uso previsto y las propiedades del material, como la resistencia, la flexibilidad y la resistencia a los productos químicos o al calor.
los calidad de la pieza moldeada está influenciada por varios factores, incluido el diseño del molde, la calidad del material utilizado y los parámetros del proceso. Una consideración cuidadosa de estos factores puede ayudar a garantizar un resultado exitoso, con piezas que cumplan con las características deseadas, como precisión dimensional, acabado superficial y propiedades mecánicas.
El moldeo por inyección se puede adaptar para satisfacer diversos requisitos de fabricación utilizando diferentes procesos, como el moldeo por coinyección, el moldeo por inyección con núcleo fusible, el moldeo por inyección asistido por gas y el moldeo por inyección-compresión. Cada proceso tiene ventajas y limitaciones, y la elección depende de factores como la complejidad de las piezas, los requisitos de materiales y los volúmenes de producción.
En resumen, el moldeo por inyección es un proceso de fabricación versátil y eficiente para producir piezas a partir de diversos materiales, utilizando diferentes tipos de puertas y procesos adecuados para aplicaciones específicas. Al comprender los conceptos básicos del moldeo por inyección, estará mejor equipado para tomar decisiones informadas al diseñar y fabricar piezas con este proceso.
Componentes estructurales del moldeo por inyección
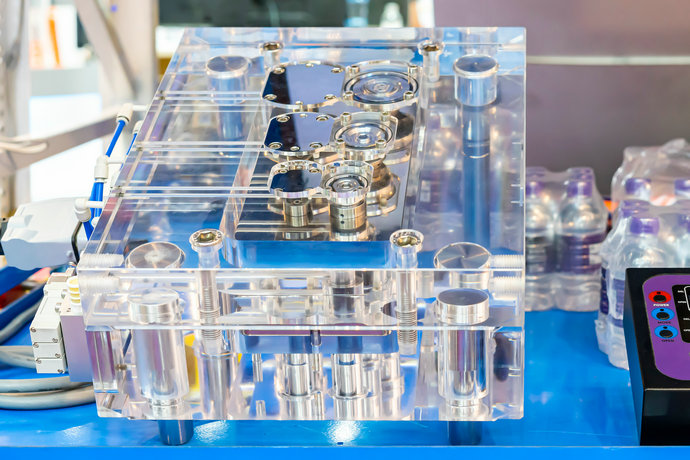
Cuando se trata de moldeo por inyección, es fundamental comprender claramente sus componentes fundamentales. Esta sección explorará los principales elementos estructurales, incluidos el molde, la cavidad, el bebedero, el canal y la cavidad del molde.
los moho Es fundamental en el proceso de moldeo por inyección, ya que le da al material plástico la forma deseada. Los moldes pueden tener una o varias cavidades, según la complejidad y el tamaño del producto final.
los cavidad es el espacio dentro del molde donde se inyecta el material plástico fundido. Aquí es donde el material plástico adquiere la forma del producto final. El número de cavidades en un molde afecta la tasa de producción y el costo total.
los bebedero es el pasaje que conecta la boquilla de la máquina de moldeo por inyección al sistema de canales. Se encarga de transportar el plástico fundido al interior del molde. Es fundamental tener un bebedero bien diseñado para garantizar un flujo adecuado y minimizar el riesgo de defectos del material.
corredores Son canales en el molde que guían el plástico fundido hacia las cavidades del molde. Desempeñan un papel crucial en la distribución uniforme del material y en el mantenimiento de una presión constante durante todo el proceso de moldeo. El sistema de canales puede diseñarse como canal caliente o frío, cada uno con ventajas y desventajas.
los cavidad del molde es donde el material plástico se solidifica y forma el producto final. Es vital diseñar la cavidad del molde considerando las dimensiones, tolerancias y acabados superficiales deseados del producto final. Esto afecta directamente la calidad y el rendimiento del producto.
Al obtener una comprensión sólida de estos componentes estructurales, puede asegurarse de que su proceso de moldeo por inyección sea eficiente, preciso y dé como resultado productos de alta calidad.
Entendiendo la puerta
En moldeo por inyección, puertas son componentes cruciales que garantizan el flujo adecuado de plástico fundido hacia la cavidad del molde. Estas compuertas, aberturas diseñadas específicamente, controlan el flujo, la apariencia y el enfriamiento de las piezas moldeadas por inyección. Elegir lo correcto puerta de moldeo por inyección es imperativo para mantener la calidad, la precisión y el rendimiento de su producto final.
Hay varios tipos de compuertas a considerar para su proyecto de moldeo por inyección, cada una con beneficios y aplicaciones específicas. Comprender estos diferentes tipos de puertas es esencial para seleccionar la opción más adecuada.
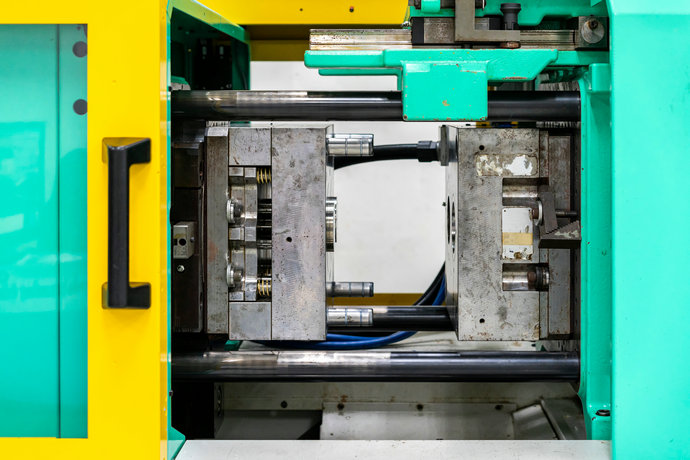
- Puerta del bebedero: Este es el tipo de compuerta más simple, que conecta la pieza moldeada directamente a la boquilla de la máquina de inyección. Si bien es fácil de diseñar y usar, puede generar una gran tensión y podría ser mejor para piezas complejas o grandes debido al desperdicio de material.
- Puerta submarina (también conocida como puerta de túnel): Este tipo de compuerta está diseñada para cortar automáticamente la pieza moldeada durante la expulsión. Son ventajosos para la automatización y requieren un trabajo mínimo de posmoldeo, lo que los hace ideales para producción de gran volumen.
- Puerta del ventilador: Esta compuerta, llamada así por su forma de abanico, permite una distribución más uniforme del material fundido, lo que reduce la probabilidad de defectos en las piezas.
- Puerta de borde: Colocada en el borde de la pieza moldeada, esta compuerta garantiza un mejor flujo dentro de la cavidad del molde y es ideal para piezas planas y delgadas.
- Puerta de pestaña: Similar a una compuerta de borde, este tipo reduce la posibilidad de fuga de material y a menudo se usa para piezas planas y delgadas que necesitan un flujo más concentrado.
- Puerta de diafragma (puerta de anacardo): Esta compuerta controla el flujo de material desde el centro de una pieza moldeada, lo que permite un mejor control sobre la contracción y deformación de la pieza. Se utiliza comúnmente para piezas de precisión con geometrías complejas.
- Puerta circular: Utilizadas para moldear piezas con forma de tubo, las compuertas anulares controlan el flujo del material alrededor de toda la circunferencia de la pieza, proporcionando una distribución uniforme.
Además de estos tipos de puertas principales, existen sub-puertas (puertas más pequeñas utilizadas junto con una puerta principal), compuertas de válvula, que ayudan a controlar el flujo a través de medios más precisos, y puertas de punta caliente, que utilizan una boquilla calentada para aplicaciones especializadas de alta precisión.
Un bien seleccionado sistema de puerta y diseño Puede distinguir entre un proyecto de moldeo por inyección exitoso y uno plagado de defectos en las piezas, desperdicio de material e ineficiencias. Comprender estos tipos de puertas y su impacto potencial en sus piezas moldeadas por inyección le permitirá tomar decisiones informadas y lograr resultados óptimos.
Factores que influyen en el rendimiento de la puerta
Cuando se trabaja con moldeo por inyección de compuerta, es esencial considerar varios factores que pueden influir en el rendimiento de la compuerta. Al prestar atención a estos factores, puede garantizar la calidad de sus componentes moldeados y optimizar la eficacia de su proceso.
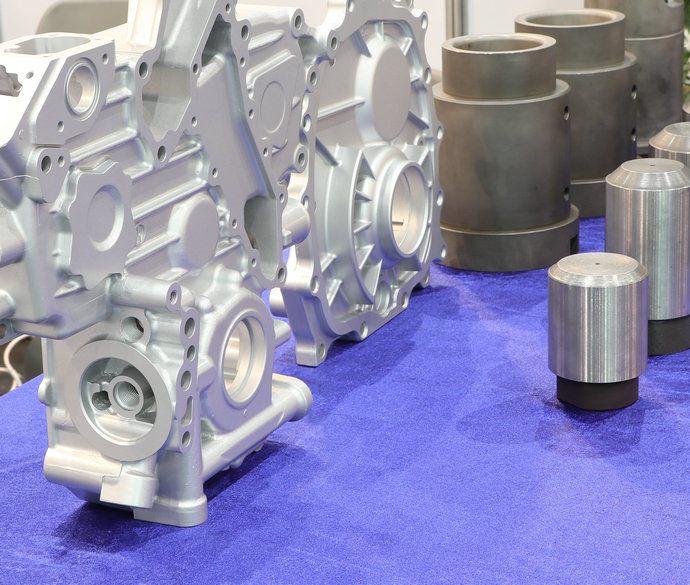
Control de presión y temperatura: El control adecuado de la presión y la temperatura de inyección es fundamental, ya que estos parámetros afectan el flujo del plástico hacia el molde. Encontrar el equilibrio adecuado entre estos dos factores es esencial para lograr un llenado consistente y evitar defectos como deformaciones o marcas de hundimiento.
Espesor y Relleno: El grosor de la puerta juega un papel crucial en la rapidez y uniformidad con la que el plástico llena la cavidad del molde. Una puerta más gruesa puede dar lugar a un llenado más rápido, pero puede aumentar el esfuerzo cortante y posibles daños a la pieza de plástico. Por otro lado, una puerta más delgada puede provocar un llenado más lento y posibles disparos cortos.
Ubicación del cono y de la puerta: El diseño de la puerta también puede afectar el flujo de plástico. Una compuerta cónica permite un flujo más suave, lo que puede ayudar a prevenir puntos débiles o fracturas en la pieza final. Además, elegir la ubicación correcta de la puerta es esencial para minimizar defectos como rebabas del moldeo por inyección o espesores desiguales.
Colocación de la puerta: La colocación correcta de la puerta es vital para garantizar un buen flujo y un llenado adecuado de la cavidad del molde. Colocar la puerta en un lugar que permita que el plástico fluya alrededor de las características del molde puede ayudar a evitar defectos y crear una pieza más uniforme.
Resinas de flujo rápido: El uso de resinas de flujo rápido puede mejorar la eficiencia del proceso de moldeo por inyección al reducir el tiempo del ciclo. Sin embargo, trabajar con resinas de flujo rápido puede requerir un control más preciso de la presión, la temperatura y otros parámetros del proceso para lograr los resultados deseados y evitar defectos.
Al considerar estos factores, puede optimizar el rendimiento de su proceso de moldeo por inyección de compuerta y lograr componentes moldeados de alta calidad. Encontrar el equilibrio adecuado entre presión, temperatura, espesor de la compuerta y ubicación es esencial para el éxito en esta área de fabricación especializada.
Defectos de puerta y control de calidad
En el moldeo por inyección, los defectos en la puerta pueden afectar significativamente la calidad de la pieza terminada. Comprender diversos problemas relacionados con la entrada e implementar las medidas de control de calidad adecuadas son cruciales para obtener un producto final de alta calidad.
Un defecto común en la puerta es la presencia de vestigios. Los vestigios son restos de la cancela que quedan en la pieza acabada tras el recorte, que pueden resultar antiestéticos y afectar negativamente a su aspecto final. Para minimizar los vestigios, asegúrese de que su puerta esté recortada de forma limpia y precisa. Elegir el tipo de puerta adecuado, como una puerta de punta caliente o una puerta submarina, también puede ayudar a reducir la apariencia de vestigios.
El chorro es otro defecto del moldeo por inyección que a veces se asocia con el diseño de la puerta. El chorro se produce cuando el material fundido se dispara hacia el molde a altas velocidades, lo que hace que se solidifique prematuramente y provoque imperfecciones o puntos débiles en la pieza terminada. Ajuste la velocidad de inyección o modifique los canales de flujo dentro del diseño de su compuerta para abordar los problemas de inyección.
Los tiempos de ciclo juegan un papel crucial en el control de la calidad de las piezas moldeadas por inyección. Los tiempos de ciclo más prolongados pueden provocar un aumento de las fracturas por tensión, mientras que los ciclos más cortos pueden provocar un llenado incompleto, creando imperfecciones y afectando negativamente la calidad de las piezas. Equilibrar los tiempos de sus ciclos puede ayudar a garantizar que sus piezas cumplan con los estándares de calidad deseados.
La inspección y el seguimiento meticulosos de su proceso de moldeo por inyección pueden ayudar a identificar los defectos relacionados con la compuerta desde el principio, lo que le permitirá abordarlos rápidamente y mantener una calidad óptima de las piezas.
Además, la implementación de varios métodos de control de calidad, como inspecciones visuales, sistemas de inspección automatizados y pruebas destructivas o no destructivas, proporcionará información valiosa sobre la eficacia del proceso de diseño y moldeado de su puerta.
Preguntas frecuentes
1. ¿Cuáles son los diferentes tipos de puertas en el moldeo por inyección?
En el moldeo por inyección se utilizan varios tipos de compuertas, como compuertas directas o de bebedero, compuertas de borde, compuertas submarinas y compuertas de abanico. Cada tipo tiene ventajas y aplicaciones únicas, según el diseño y los requisitos del componente.
2. ¿Cómo impacta el diseño de la puerta en el proceso de moldeo?
El diseño de la compuerta juega un papel crucial en el moldeo al determinar el flujo de plástico fundido hacia la cavidad del molde. Una compuerta bien diseñada garantiza un llenado eficiente, minimiza los defectos de moldeo y reduce el tiempo del ciclo. Los diferentes tipos de compuertas tienen distintos beneficios, como promover un flujo más rápido, controlar las marcas de hundimiento o permitir una mejor ventilación.
3. ¿Qué factores determinan la ubicación de la puerta en el moldeo por inyección?
Varios factores afectan la ubicación de la compuerta en el moldeo por inyección, incluida la geometría de la pieza, la selección del material y la ruta de flujo deseada. Generalmente, la compuerta debe colocarse en un área que permita un llenado uniforme y una presión mínima del material, reduciendo defectos y deformaciones. La ubicación de la puerta también debe minimizar la tensión en áreas críticas y garantizar que las líneas de soldadura estén en secciones no críticas.
4. ¿Cuáles son las principales funciones de las compuertas en el moldeo por inyección?
Las puertas cumplen múltiples funciones en el moldeo por inyección, como controlar el flujo de plástico fundido hacia la cavidad del molde, garantizar un llenado adecuado y permitir que el plástico se solidifique a un ritmo óptimo. Las compuertas también son responsables de minimizar los defectos de moldeo, como trampas de aire, marcas de hundimiento y disparos cortos, al dirigir el plástico fundido de manera eficiente.
5. ¿Cómo influye el tamaño de la puerta en el producto final?
El tamaño de la puerta puede afectar significativamente la calidad y apariencia del producto final. Una compuerta más pequeña normalmente da como resultado un caudal más lento, lo que reduce el riesgo de marcas de hundimiento y deformaciones. Sin embargo, también puede aumentar el tiempo del ciclo y provocar un llenado incompleto en escenarios específicos. Por otro lado, una compuerta más grande permite un flujo más rápido y un llenado del molde más rápido, pero puede causar tensiones adicionales o defectos dentro de la pieza.
6. ¿Cuáles son las ventajas de utilizar el moldeo por inyección de compuerta?
El moldeo por inyección de compuerta ofrece varios beneficios, como un mayor control sobre el flujo de plástico fundido, tiempos de ciclo reducidos y defectos minimizados. Elegir el diseño y la ubicación de la puerta adecuados le permite optimizar su proceso de moldeo para producir componentes de alta calidad con menos problemas. Además, una compuerta adecuada puede ayudar a reducir el desperdicio de material y mejorar la eficiencia general de la producción.
Solicite piezas de inyección de plástico de alta calidad con nosotros
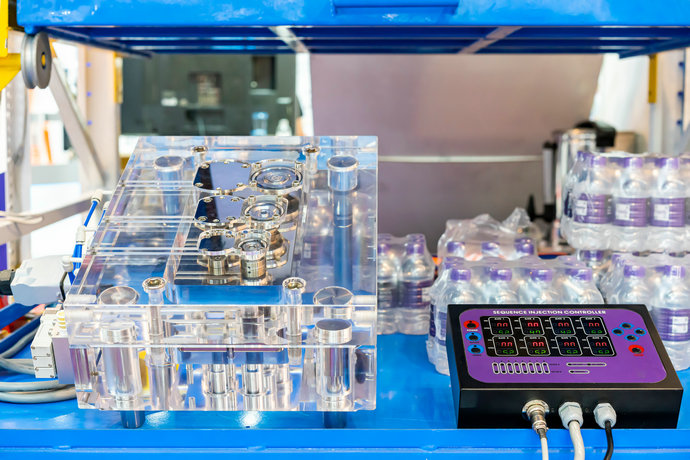
Vendemos diferentes tipos de piezas de plástico moldeadas por inyección a granel. Para realizar el pedido, sólo necesita enviarnos un mensaje a través del formulario de contacto con el cliente en nuestro sitio web. Entregamos productos de moldeo por inyección de plástico a nivel mundial y esperamos iniciar una relación comercial gratificante con su empresa.