Най-голямото количество пластмаса във шприцформа, което може да бъде инжектирано по време на цикъл на формоване, е известно като размер на впръскване. Пелетите се подават в цилиндъра и шнековия възел през бункера.
Използвайки техниката на шприцване, разтопен материал се инжектира в кухината на матрицата, за да се създадат големи количества пластмасови части.
В процеса на шприцване на пластмаса, суровината се въвежда в цевта, разтопява се и след това пластмасата се инжектира в кухината на матрицата за охлаждане и втвърдяване, след като матрицата е затворена. Накрая матрицата се отваря и компонентите се изхвърлят.
Как да изчислим размера на дозата
Продължителността на престоя се влияе от размера на сачмата и цевта, което може да повлияе и на качеството на крайния продукт. Дългите периоди на престой и разграждането на полимерите могат да възникнат от малки размери на сачмите, които изискват малък капацитет на цевта.
Малките размери на изстрелите, които заемат по-малко от 20% от капацитета на цевта, често водят до удължено време на престой, което от своя страна причинява разграждане на полимера и неадекватен контрол на процеса.
От друга страна, големите размери на сачмите и нивата на пълнене на цевите, по-големи от 50%, могат да причинят неравномерно топене и бавно възстановяване на шнека.
Освен това, по-големите шнекове обикновено имат по-ниски възможности за пластично налягане. Големите размери на изстрелите, които заемат повече от 65% от капацитета на цевта, често причиняват проблеми с качеството на стопилката, като например неразтопяване, лоша еднородност на стопилката и дълго време за възстановяване на шнека.
За по-сигурно, можете да помислите за поръчка на две бъчви. Нещо повече, формите могат да се използват с две бъчви. Когато поръчате втора бъчва с новата машина, можете да бъдете приятно доволни от ниската ѝ цена. Бъчвите могат да бъдат сменени за по-малко от 30 минути с правилните спецификации и опитен оператор, дори ако бъчвата е гореща.
Формула за размер на матрицата при шприцване
Най-простата формула за изчисляване на размера на дозата във формата е:
Свиване + Обем на смърча + Обем на продукта + Обем на беглец = Размер на дозата във формата
Капацитет/размер на дозата на машината за формула
Общото тегло или обем, който шнекът инжектира по време на един цикъл на формоване, се изразява като капацитет на машинното впръскване (g)/размер на машинното впръскване (mm), известен също като капацитет на машинното впръскване.
Вашите изчисления, когато отчитате налягането, трябва да бъдат следните:
Ход X Повърхност на винтовото бутало = обем на впръскване
Сила на впръскване/ повърхност на винтово бутало = налягане на впръскване
Следователно:
Максимален обем на инжектиране на кубична единица X максимално налягане на инжектиране (бара на кубична единица) / 1000 = капацитет на инжектиране на инжекционния блок.
Изчисленията при използване на тегло на винта и плътност на материала трябва да бъдат следните:
Маса/плътност = обем
ᴨ*D2*Размер на изстрела/4=Цев/Обем на изстрела
Фактори, които влияят на размера на продуктовата снимка
Има няколко фактора, които трябва да вземете предвид, когато изчислявате размера на дозата. Тези фактори са следните:
- Трябва да вземете предвид обема на смърча, обема на канала и обема на продукта, когато определяте размера на впръскването. Това е така, защото полимерът трябва да запълни обема на смърча, канала и продукта, когато се инжектира във формата.
- Друг важен въпрос, който влияе върху изчисленията за размера на дозата, е свиването на полимера. Свиването е резултат от охлаждането на стопилката на полимера. Поради различната плътност на полимерите, свиването на матрицата варира.
- Видът и количеството на добавките в полимера могат да променят неговата плътност и характеристики на течливост.
Тези фактори могат да ви помогнат да оцените размера на изстрела, обема и капацитета на цевта.
Инжекционен блок
Целта на инжекционния агрегат е да разтопи равномерно пластмасовия материал, преди да го инжектира във формата при предварително определено налягане и дебит. Това са взискателни дейности, тъй като флуорополимерите имат ограничена топлопроводимост, висока специфична топлина и висок вискозитет на стопилката.
Отново са разработени множество вариации за справяне със сложните проблеми. Обща класификация на вариациите може да се направи в четири основни концепции за инжекционни устройства:
- Едностъпално бутало или бутало
- Двустепенен овен
- Винт с един етап
- Винт/рама с два етапа
Въпреки че все още съществува в малки машини и някои специализирани съоръжения, едностепенният бутален агрегат е по същество остарял поради неефективността си при нагряване, смесване и предаване на налягане. Той се отличава с простота и достъпност.
Освен това, двустепенният бутален механизъм е почти остарял. Бубалникът все още е неефективен смесител и нагревател, въпреки опитите за подобряване чрез разделяне на операциите по нагряване и налягане на потока.
Двустепенният шнек/бутален агрегат допълнително разделя ролите на потока и топлината, като използва бутало за впръскване вместо шнек за смесване и нагряване. Идеята е привлекателна, защото и двата са ефективни инструменти за съответните си задачи.
Освен това, инжекционният агрегат често се оценява, като се използва максималното налягане на инжектиране и наличният обем на инжектиране. Най-голямото възможно налягане в края на шнека надолу по течението се нарича налягане на инжектиране. Това зависи от диаметъра на шнека и силата, която го натиска.
Внимавайте обаче да не го бъркате с налягането в хидравличната линия, действащо върху инжекционния цилиндър, който задвижва шнека, нито пък трябва да се тълкува като налягане, необходимо за запълване на кухините на матрицата. Поради загубите на налягане в дюзите и системите за подаване на матрицата, това е значително по-малко.
Основната серия от действия на инжекционния блок е следната:
- Материалът се нагрява и разтопява, докато шнекът се върти, след което се транспортира по витките на шнека до края му надолу по течението. Дюзата на цилиндъра се затваря с помощта на механичен или термичен клапан или чрез наличието на по-ранно формоване.
Докато се натрупа достатъчно стопилка за производството на следващата отливка, събиращата се стопилка притиска все още въртящия се винт назад срещу контролирано съпротивление (противоналягане). Въртенето на винта спира тук. Време е да сте готови за стопилката.
- Когато дюзата на цилиндъра се отвори, шнекът се движи напред в аксиална посока, без да се върти, действайки като бутало. В резултат на това стопилката, събрана пред низходящия край на шнека, се впръсква (инжектира) през дюзата и във формата.
За да се предотврати връщането на стопилката обратно по шнековите витки, в края на шнека надолу по течението може да се монтира клапанна система. Това е етапът на шприцване или пълнене на матрицата.
- След като формата е напълнена, налягането на шнека се поддържа за кратко време, за да компенсира обемното свиване на охлаждащата се стопилка във формата. Сега е фазата на пълнене или задържане.
- Накрая се стига до фазата на задържане, където цикълът на шприцващия агрегат се възобновява с въртене на шнека и подготовка на стопилката, докато формата се държи затворена, за да може тя да се охлади до температурата на изхвърляне.
Има значителни загуби на налягане, когато пластмасовата стопилка се вкарва в дюзата за инжектиране и впоследствие през системата за подаване на матрицата и кухините. Не могат да се използват прости правила за изчисляване на тези загуби на налягане.
Затягащ блок
Затварянето на матрицата се поддържа срещу сили, създадени, когато пластмасата се избутва в затворена матрица чрез шприцване, използвайки затягащ механизъм за IMM. Той има задвижваща система, която може да движи движещата се плоча на машината за шприцване в поне една посока.
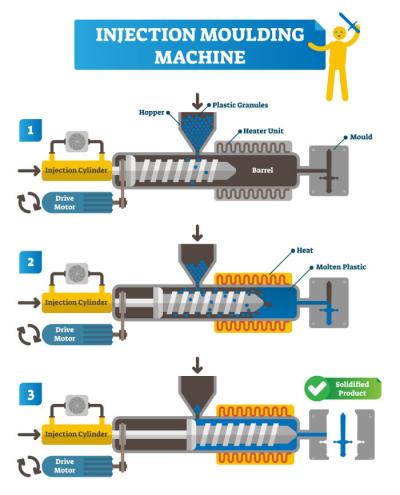
Видове затягащи устройства
В процеса на шприцване има няколко вида затягащи устройства. Те са следните:
Затягане тип превключвател
Механично устройство, което усилва сила, е превключвател. В формовъчна машина два пръта са свързани и завършват с шарнир. Единият край на пръта е свързан с неподвижна плоча, а другият е свързан с подвижна плоча. Превключвателят има V-образна форма, когато формата е отворена. Двата пръта образуват права линия, когато върху шарнира се приложи натиск.
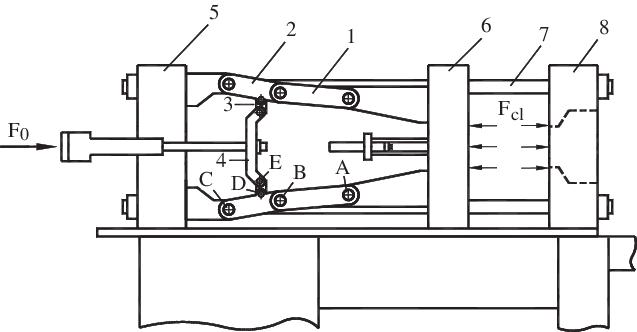
Предимствата на затягането с лостов механизъм включват, че изисква по-малко пари и мощност и осигурява позитивен план на матрицата. Освен това, недостатъците на затягането с лостов механизъм са, че изисква висока поддръжка и е трудно за изпълнение.
Хидравлично затягане
В този случай, RAM (опорната част) на хидравличната система е свързана с подвижната плоча, а затягащ блок, задвижван от хидравличен цилиндър, е директно свързан със затворената подвижна форма. Хидравличният цилиндър има две секции: вход за масло и изход за масло.
Маслото избутва RAM-а напред, когато той влезе в цилиндъра под налягане, което води до затваряне на движещата се плоча и матрицата. Освен това, връщащият механизъм на RAM-а и матрицата са отворени, когато маслото се освободи от цилиндъра.
Някои предимства на хидравличното затягане включват лесно управление на скоростта на затягане и опора под всякакъв ъгъл, просто измерване на силата на затягане, лесна настройка на режима и регулиране на силата на затягане, както и лекота на поддръжка.
Недостатъците на този вид затягане са, че струва повече и е по-скъпо от превключваща система и скоба с положително съществително име.
Магнитен затягащ модул
Магнитни модули вътре в магнитните затягащи плочи или плочи за матрици създават силата на затягане. Интерфейсният панел може да контролира затягането на матрицата, смяната на матрицата, както и намагнитването и размагнитването на плочите.
Предимствата на това затягащо устройство включват необходимостта от електричество само по време на фазите на намагнитване и размагнетизиране, а не по време на затягане, измерване на силата на затягане в реално време с много функции за безопасност и безплатна поддръжка.
Тегло на изстреляната форма
Количеството материал, инжектирано във формата за запълване на формата, включително системата за подаване, е известно като „тегло на впръскването на формата“ или „тегло на впръскването на продукта“. Теглото на смърча, канала и шибъра, от друга страна, са компонентите на теглото на впръскването. Разстоянието, което шнекът изминава, за да запълни продукта, включително системата за подаване, е известно като размер на впръскването на формата/продукта.
Заключение
С помощта на техниката на шприцване, суровата пластмаса се разтопява, инжектира се във формата, оставя се да се охлади и втвърди, след което готовият обект се изстрелва. Размерът на дозата е от решаващо значение, защото предотвратява недопълването на полимера и избухването му. Други фактори, като например капацитетът на цевта, също влияят върху общия процес на шприцване.