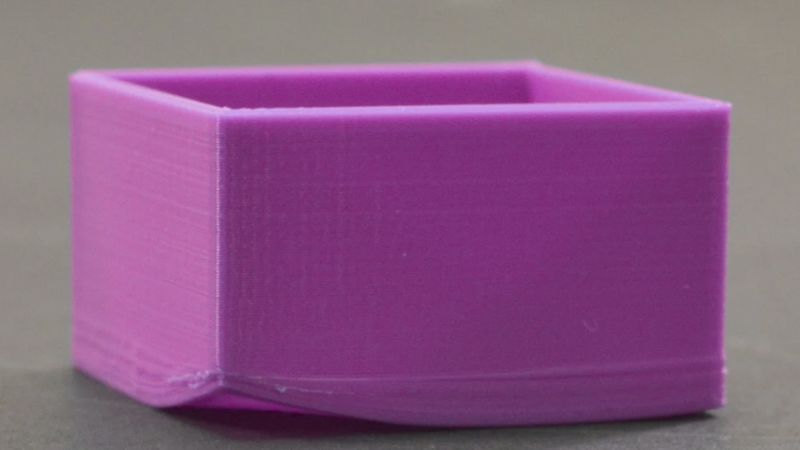
Deformácia môže byť nepríjemná. Pre výrobcov aj dizajnérov produktov je dôležité pochopiť základné príčiny deformácie a implementácia účinných preventívnych stratégií je rozhodujúca pre udržanie vysokokvalitného výstupu a minimalizáciu výrobných nákladov.
V tejto komplexnej príručke preskúmame primárne faktory, ktoré prispievajú k deformácii pri vstrekovaní a poskytneme praktické riešenia na zmiernenie tohto problému.
Uplatnením týchto poznatkov môžu výrobcovia zlepšiť efektivitu svojej výroby, znížiť mieru šrotu a v konečnom dôsledku dodať špičkové diely vstrekované do formy.
Čo je Molding Warpage
Deformácia je jedným z kľúčových problémov kvality pri vstrekovaní plastov, čo často vedie k rozmerovej nestabilite plastových dielov.
Deformácia označuje nežiaducu odchýlku od zamýšľanej geometrie produktu, ktorá sa môže vyskytnúť v plastových dieloch počas procesu vstrekovania. Táto chyba sa prejavuje deformáciami, ako je skrútenie, ohnutie alebo zvlnenie tvarovaného dielu.
Závažnosť deformácie sa pohybuje od miernych deformácií, ktoré sú sotva viditeľné voľným okom, až po výrazné deformácie, ktoré narúšajú funkciu alebo zostavu dielu.
Vplyv deformácie na lisované výrobky
Prítomnosť deformácie pri vstrekovaní má podstatný vplyv na kvalitu a funkčnosť plastových dielov:
- Estetická kvalita: Vizuálna príťažlivosť je ohrozená, čím sú konečné produkty menej konkurencieschopné na trhu.
- Rozmerová stabilita: Pokrivené časti nemusia zapadnúť do zostáv alebo spĺňať presné rozmery potrebné na prepojenie s inými komponentmi.
- Funkčné nedostatky: Okrem estetiky môže deformácia zhoršiť mechanický výkon a štrukturálnu integritu komponentu.
Čo je príčinou deformácie pri vstrekovaní?
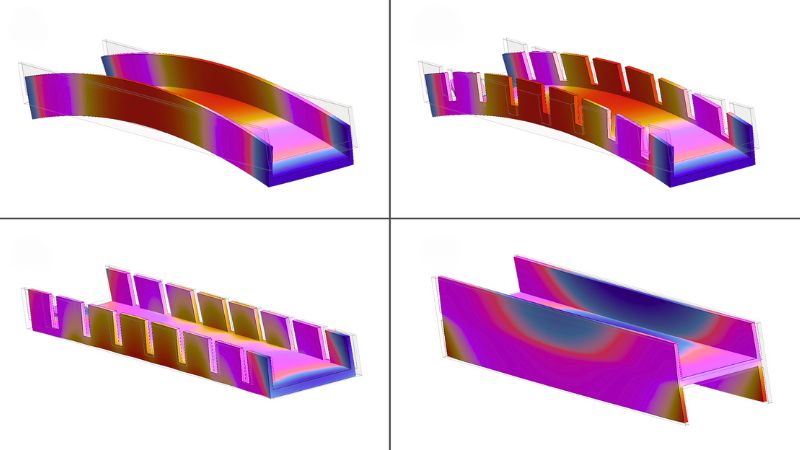
Táto časť skúma zložitosti stroj, forma, a materiálne faktory prispieva k deformácii a poskytuje niekoľko praktických riešení na zmiernenie týchto problémov.
Chyby stroja
Nedostatočný vstrekovací tlak alebo čas
Nedostatočný vstrekovací tlak alebo doba zdržania môžu viesť k nedostatočnému zabaleniu formy. To môže spôsobiť, že plastový materiál vychladne a stuhne skôr, ako sa forma správne naplní.
Oba scenáre vedú k nekontrolovanému pohybu molekúl počas chladenia, čo vedie k nerovnomernému zmršťovaniu a deformácii.
Nesprávna teplota suda
Ak je teplota valca príliš nízka, živica nedosiahne svoju správnu prietokovú teplotu, čo vedie k predčasnému stuhnutiu, nedostatočnému zabaleniu formy a nakoniec k nerovnomernému zmršťovaniu a deformácii.
Nesprávny čas pobytu
Nedostatočná doba zotrvania zabraňuje rovnomernej absorpcii tepla v celej živici. To môže spôsobiť, že nedostatočne zahriate časti materiálu stuhnú a predčasne stuhnú, čo má za následok neúplné balenie formy a deformáciu.
Nadmerné vnútorné napätie
Vysoké vstrekovacie tlaky môžu vytvárať vnútorné napätia vo výlisku, ktoré sa môže prejaviť ako deformácia po vysunutí z formy.
Nesprávny čas skrutky
Ak je čas posúvania skrutky príliš dlhý, môže to viesť k preplneniu formy, čím sa vytvorí vnútorné napätie, ktoré vedie k deformácii.
Nedostatočný čas chladenia
Nedostatočný čas chladenia môže zabrániť rovnomernému a úplnému ochladzovaniu dielu pred vysunutím, čo vedie k nerovnomernému zmršťovaniu a deformácii, keď sa chladí mimo formy.
Chyby plesní
Nesprávne umiestnenie a dizajn brány
Nesprávne umiestnenie brány môže viesť k nerovnomernému vyplneniu a zabaleniu dutiny formy. To má za následok nekonzistentné rozloženie tlaku a rýchlosti chladenia, čo spôsobuje deformáciu.
Neadekvátne umiestnenie vyhadzovacieho kolíka
Zle umiestnené alebo nedostatočné vyhadzovacie kolíky môžu spôsobiť nerovnomerné napätie pri vysúvaní dielu z formy. To môže viesť k deformácii, najmä v častiach so zložitou geometriou.
Nevyvážené chladiace okruhy
Nesprávne vyvážené chladiace okruhy môžu spôsobiť nerovnomerné chladenie v dutinách, čo vedie k deformácii niektorých častí, zatiaľ čo iné zostávajú nedotknuté.
Chyby pri výbere materiálu
Vysoká miera zmrštenia
Materiály s vysokou mierou zmrštenia sú náchylnejšie na deformáciu.
Napríklad semikryštalické polyméry, ako je polyetylén (PE) a polypropylén (PP), majú vyššiu rýchlosť zmrštenia v porovnaní s amorfnými polymérmi, ako je polykarbonát (PC) alebo polystyrén (PS).
Nekonzistentné zmršťovanie
Niektoré materiály sa zmršťujú odlišne v smere toku a v smere priečneho toku. Toto anizotropné zmršťovanie môže viesť k deformácii, najmä v častiach s dlhými dráhami toku.
Kryštalinita
Vysoko kryštalické materiály sú náchylnejšie na deformáciu kvôli ich tendencii sa počas chladenia viac zmršťovať.
Citlivosť na vlhkosť
Niektoré materiály, ako napríklad nylon, sú hygroskopické a môžu absorbovať vlhkosť zo vzduchu. To môže viesť k nekonzistentným výsledkom formovania a potenciálnemu zdeformovaniu, ak nie je pred spracovaním riadne vysušené.
Ako znížiť deformáciu pri vstrekovaní?
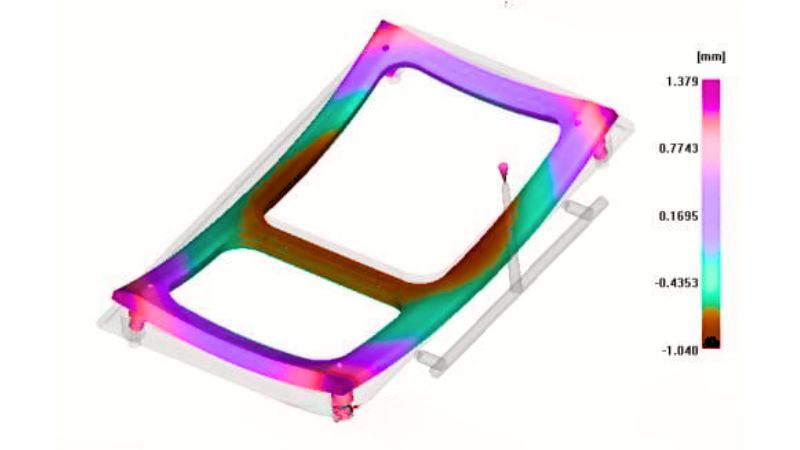
Optimalizácia parametrov spracovania je rozhodujúca, počnúc úpravou vstrekovacieho tlaku a doby zdržania, aby sa zabezpečilo správne balenie dutiny formy. To obmedzuje molekuly plastov a zabraňuje nekontrolovanému pohybu počas chladenia.
Predlžujúci sa čas chladenia umožňuje úplné a rovnomerné chladenie, čo pomáha predchádzať rozdielnym rýchlostiam zmršťovania, ktoré často vedú k deformácii.
Rovnako dôležité je jemné doladenie nastavenia teploty; zvýšenie teploty valca zaisťuje správny tok materiálu, zatiaľ čo nastavenie teploty formy na základe odporúčaní dodávateľa živice podporuje jednotnosť.
Ak je to možné, implementácia konformných chladiacich kanálov môže ďalej zlepšiť rovnomerné chladenie naprieč dielom.
Dizajn formy a materiálové úvahy
Optimalizácia brán a žľabov pomocou vhodných typov brán pre špecifické plasty a dizajn produktov, implementácia viacerých brán pre ploché diely a rozšírenie brán a žľabov môže výrazne zlepšiť plnenie foriem.
Dôležité je aj správne umiestnenie vyhadzovacieho kolíka; Zabezpečenie, že sú dostatočne široké, dobre rozmiestnené a umiestnené v blízkosti oblastí s najväčším odporom proti vysunutiu, môže zabrániť deformácii počas odstraňovania dielov.
Výber materiálu a manipulácia sú kľúčovými faktormi. Výber živíc menej náchylných na deformáciu, ako sú amorfné plasty ako polykarbonát a polystyrén namiesto kryštalických plastov, môže mať zásadný rozdiel.
V prípade dielov s kovovými vložkami ich predhriatie na približne 100 °C pomáha vyrovnať sa s rozdielmi v zmrštení medzi kovom a plastom, čím sa znižuje napätie a potenciálne deformácie.
Optimalizácia dizajnu a kontrola kvality
Optimalizácia návrhu dielu je ďalším kritickým aspektom. Udržiavanie rovnomernej hrúbky steny v celej časti podporuje rovnomerné chladenie a zmršťovanie, zatiaľ čo pridanie spevňujúcich rebier môže zlepšiť tuhosť časti a znížiť tendenciu k deformácii.
Spolupracujte s profesionálom — Moldie
Práca s Moldie môže viesť ku kvalite a účinnosti v procese vstrekovania lisovaných plastov. Sme vybavení odbornými znalosťami potrebnými na manipuláciu s rôznymi plastovými materiálmi, čím zaisťujeme, že výsledné plastové výrobky sa snúbia s trvanlivosťou a estetikou.
Moldie kladie dôraz na presnosť vo svojich výrobných technikách. Náš prístup zahŕňa:
- Pokročilý dizajn foriem: Optimalizáciou veľkosti a tvaru brány pomáha Moldie udržiavať rovnomerný prietok a chladenie, čo vedie k menšiemu vnútornému namáhaniu a zníženiu deformácie.
- Výber materiálu: Ich znalosť rôznych plastov umožňuje informovaný výber materiálu, prispôsobenie vlastností zamýšľanej aplikácii a zmiernenie chýb.
- Optimalizácia procesov: Moldie dolaďuje teplotu formy a rýchlosť chladenia, pretože tieto premenné hrajú kľúčovú úlohu pri výrobe vysoko kvalitných komponentov bez deformácií.
Veríme, že takáto spolupráca môže výrazne zvýšiť štandard vyrábaných plastových komponentov a v konečnom dôsledku zlepšiť funkčnosť a vzhľad konečného produktu.