Наибольшее количество пластиковой формы для литья под давлением, которое может быть впрыснуто во время цикла формования, известно как размер порции. Пеллеты подаются в ствол и шнековый агрегат через бункер.
Используя технику литья под давлением, расплавленный материал впрыскивается в полость формы для создания большого количества пластиковых деталей.
В процессе литья пластмасс под давлением сырье вводится в цилиндр, плавится, а затем пластик впрыскивается в полость формы для охлаждения и затвердевания после закрытия формы. Наконец, форма открывается, и компоненты выталкиваются.
Как рассчитать размер выстрела
Продолжительность пребывания зависит от размера дроби и ствола, что также может повлиять на качество конечного продукта. Большая продолжительность пребывания и деградация полимера могут быть связаны с небольшими размерами дроби, для которых требуется небольшая емкость ствола.
Небольшие размеры дроби, которые занимают менее 20% емкости ствола, часто приводят к увеличению времени пребывания, что, в свою очередь, вызывает деградацию полимера и неадекватное управление технологическим процессом.
С другой стороны, крупные порции и уровень заполнения ствола выше 50% могут вызвать неравномерное плавление и медленное извлечение шнека.
Кроме того, более крупные винты обычно имеют более низкое пластическое давление. Впрыски больших размеров, которые занимают более 65% емкости ствола, часто вызывают проблемы с качеством расплава, такие как нерасплавление, плохая однородность расплава и длительное время восстановления шнека.
Чтобы быть в безопасности, вы можете рассмотреть возможность размещения заказа на два ствола. Более того, формы можно использовать с двумя бочками. Заказывая вторую бочку с новым станком, вы можете приятно порадоваться ее недорогой стоимости. Стволы можно заменить менее чем за 30 минут при наличии правильных характеристик и опытного оператора, даже если ствол горячий.
Формула для размера впрыска пресс-формы при литье под давлением
Простейшая формула для расчета размера порции пресс-формы:
Усадка + объем ели + объем продукта + объем желоба = размер впрыска формы
Формула Производительность машины / размер впрыска
Общий вес или объем, который впрыскивается шнеком во время одного цикла формования, выражается как производительность машины (г)/размер машины (мм), также известная как производительность машины.
Ваши расчеты при рассмотрении давления должны быть следующими:
Ход поршня X Поверхность винтового поршня = объем впрыска
Сила впрыска / поверхность винтового поршня = давление впрыска
Следовательно:
Максимальный объем впрыска на куб. единицу X максимальное давление впрыска (бар на куб. единицу) / 1000 = мощность впрыска установки впрыска.
Расчеты при использовании веса шурупа и плотности материала должны быть следующими:
Масса/плотность= объем
ᴨ*D2*Размер выстрела/4= Ствол/объем выстрела
Факторы, влияющие на размер порции продукта
Есть несколько факторов, которые вы должны учитывать при расчете размера выстрела. Эти факторы следующие:
- Вы должны учитывать объем ели, объем бегуна и объем продукта при определении размера выстрела. Это связано с тем, что полимер должен заполнить ель, желоб и объем изделия при впрыскивании в форму.
- Другим важным вопросом, влияющим на расчет размера впрыска, является усадка полимера. Усадка происходит в результате охлаждения расплава полимера. Из-за разной плотности полимеров усадка пресс-формы может быть разной.
- Тип полимера и количество добавок могут изменить его плотность и характеристики текучести.
Эти факторы могут помочь вам оценить размер выстрела, объем и емкость ствола.
Блок впрыска
Назначение блока впрыска состоит в том, чтобы равномерно расплавить пластиковый материал перед его впрыскиванием в форму при заданном давлении и скорости потока. Это сложная деятельность, поскольку фторполимеры имеют ограниченную теплопроводность, высокую удельную теплоемкость и высокую вязкость расплава.
Опять же, многочисленные варианты были разработаны для решения сложных проблем. Общую классификацию вариаций можно разделить на четыре концепции первичного впрыска:
- Одноступенчатый плунжер или поршень
- Двухступенчатый поршень
- Винт с одной ступенью
- Шнек/плунжер с двумя ступенями
Хотя он все еще существует в крошечных машинах и некотором специализированном оборудовании, одноступенчатый поршень по существу устарел из-за его неэффективности при нагреве, перемешивании и передаче давления. Его преимущество заключается в простоте и доступности.
Кроме того, двухступенчатый поршень почти устарел. Плунжер по-прежнему является неэффективным смесителем и нагревателем, несмотря на попытку улучшить его путем разделения операций нагрева и напорного потока.
Двухступенчатый шнековый/плунжерный блок дополнительно разделяет роли потока и тепла за счет использования плунжера для впрыска вместо шнека для смешивания и нагрева. Идея привлекательна, потому что оба являются эффективными инструментами для соответствующих задач.
Кроме того, блок впрыска часто оценивается с использованием максимального давления впрыска и доступного объема впрыска. Максимально возможное давление на выходном конце шнека называется давлением впрыска. Это зависит от диаметра винта и силы, действующей на него.
Однако убедитесь, что вы не путаете его с давлением в гидравлической линии, воздействующей на цилиндр впрыска, который приводит в движение винт, и не следует интерпретировать его как давление, необходимое для заполнения полостей пресс-формы. Из-за потерь давления в форсунках и системах подачи формы это существенно меньше.
Основной ряд действий узла впрыска следующий:
- Материал нагревается и расплавляется при вращении шнека, а затем транспортируется по виткам шнека к выходному концу шнека. Сопло ствола закрывается с помощью механического или термического клапана или за счет наличия более раннего литья.
До тех пор, пока не накопится достаточное количество расплава для изготовления следующей отливки, собирающийся расплав отталкивает все еще вращающийся шнек, преодолевая регулируемое сопротивление (противодавление). Здесь вращение винта останавливается. Пришло время быть готовым к плавлению.
- Когда ствол ствола открыт, винт движется вперед в осевом направлении, не вращаясь, действуя подобно ползунку. В результате расплав, собранный перед выходным концом шнека, продавливается (впрыскивается) через сопло в форму.
Чтобы расплав не стекал обратно по виткам шнека, на конце шнека, расположенном ниже по потоку, может быть установлена система клапанов. Это стадия впрыска или заливки формы.
- После заполнения формы давление шнека сохраняется в течение короткого времени, чтобы компенсировать объемную усадку остывающего расплава внутри формы. Фаза упаковки или выдержки сейчас.
- Наконец, он переходит к фазе выдержки, где цикл узла впрыска возобновляется с вращением шнека и подготовкой расплава, в то время как форма остается закрытой, чтобы дать отливке остыть до температуры выталкивания.
Существуют значительные перепады давления, когда расплав пластмассы нагнетается в сопло для впрыска, а затем через систему подачи пресс-формы и полости. Для расчета этих потерь давления нельзя использовать простые правила.
Зажимной узел
Закрытие формы поддерживается против сил, возникающих, когда пластик проталкивается в закрытую форму за счет давления впрыска с использованием зажимного устройства для IMM. Он имеет систему привода, которая может перемещать подвижную плиту машины для литья под давлением по крайней мере в одном направлении.
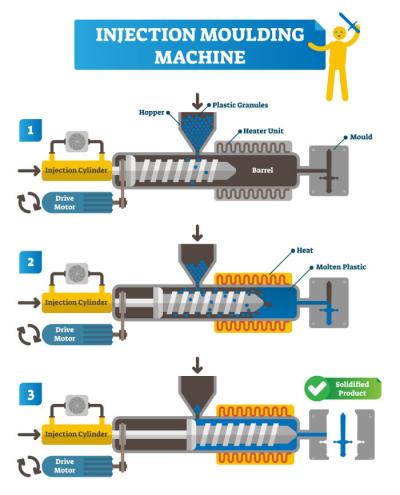
Типы зажимных устройств
В процессе литья под давлением используется несколько типов зажимных устройств. Они следующие:
Зажим типа Toggle
Механическое устройство, усиливающее силу, представляет собой тумблер. Два стержня соединены и заканчиваются шкворнем в формовочной машине. Один конец стержня соединен с неподвижной плитой, а другой - с подвижной плитой. Тумблер имеет V-образную форму, когда форма открыта. Два стержня образуют прямую линию, когда на ось оказывается давление.
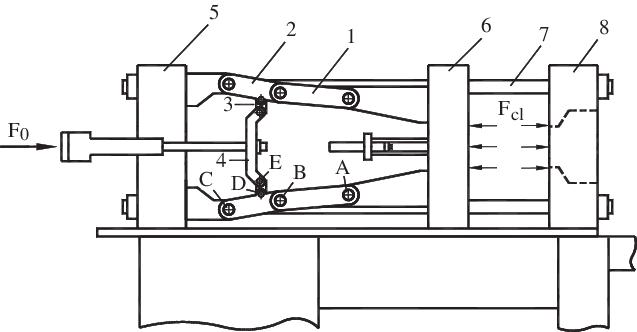
Преимущества зажима рычажного типа заключаются в том, что он требует меньше денег и мощности и обеспечивает положительный план пресс-формы. Кроме того, недостатки зажима рычажного типа заключаются в том, что он требует тщательного обслуживания и его трудно выполнить.
Гидравлический зажим
В этом случае ползун гидравлической системы привязан к подвижной плите, а узел смыкания, приводимый в действие гидроцилиндром, напрямую связан с закрытой подвижной формой. Гидроцилиндр имеет две секции: вход масла и выход.
Масло толкает поршень вперед, когда оно входит в цилиндр под давлением, в результате чего подвижная плита и пресс-форма закрываются. Кроме того, возврат поршня и пресс-форма открываются, когда масло выходит из цилиндра.
Некоторые преимущества гидравлического зажима включают простое управление скоростью зажима и поддержку под любым углом, простое измерение усилия зажима, простую настройку режима и регулировку усилия зажима, а также простоту обслуживания.
Недостатки этого типа зажима заключаются в том, что он стоит дороже и дороже, чем рычажная система и зажим с положительным существительным.
Зажим магнитного типа
Магнитные модули внутри зажимных плит или плит магнитной формы создают зажимное усилие. Интерфейсная панель может управлять зажимом пресс-формы, сменой пресс-формы, а также намагничиванием и размагничиванием плит.
К преимуществам этого зажимного устройства относятся электроэнергия, которая требуется только на этапах намагничивания и размагничивания, а не во время зажима, измерение силы зажима в режиме реального времени, множество функций безопасности и бесплатное техническое обслуживание.
Масса впрыска пресс-формы
Количество материала, впрыскиваемого в форму для заполнения формы, включая систему подачи, известно как «масса впрыска формы» или «масса впрыска продукта». С другой стороны, ель, полозья и вес ворот являются составляющими веса дроби. Расстояние, которое проходит шнек для заполнения продукта, включая систему подачи, называется размером впрыска формы/продукта.
Заключение
Используя технику литья под давлением, сырой пластик расплавляют, впрыскивают в форму, дают остыть и затвердевать, а затем готовый объект выталкивается. Размер впрыска имеет решающее значение, поскольку он предотвращает недолив полимера и образование вспышек. Другие факторы, такие как емкость цилиндра, также влияют на общий процесс литья под давлением.