Tolerâncias de moldagem por injeção definem os limites permitidos de variação dimensional em peças moldadas. Entender e gerenciar essas tolerâncias é crucial para garantir que as peças atendam às especificações de projeto e funcionem conforme o esperado.
Neste guia abrangente, exploraremos os fatores que influenciam as tolerâncias, a importância de manter tolerâncias precisas e estratégias para otimizá-las para obter componentes plásticos perfeitos.
Seja você um designer, engenheiro ou fabricante, este artigo lhe dará o conhecimento necessário para navegar pelas complexidades do processo de moldagem por injeção e melhorar a qualidade e a confiabilidade dos seus produtos.
O que são tolerâncias de moldagem por injeção?
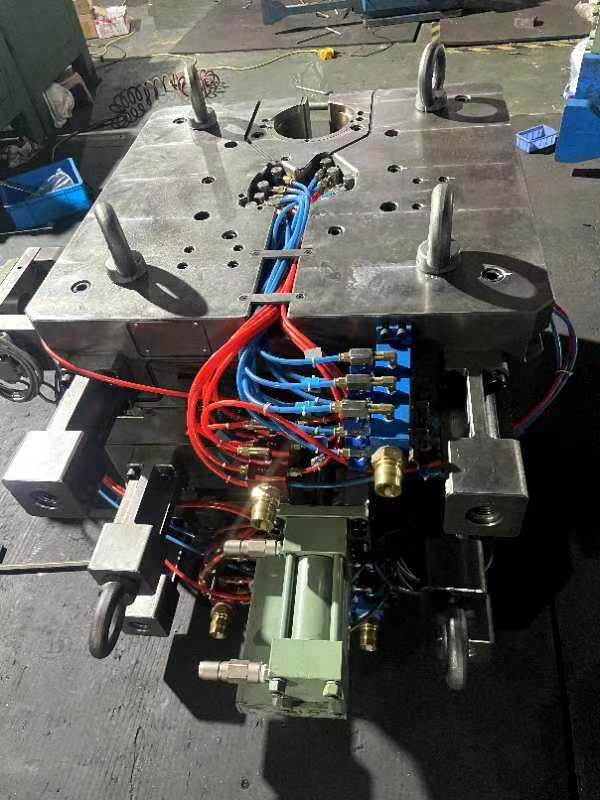
As tolerâncias de moldagem por injeção de plástico são expressas como valores de mais ou menos (±) em milímetros ou polegadas que especificam o desvio aceitável das dimensões nominais de uma peça. Elas são cruciais para garantir que as peças se encaixem e funcionem corretamente, especialmente ao montar vários componentes.
Existem dois tipos de tolerância: tolerância de usinagem e tolerância à resina.
A tolerância de usinagem refere-se à tolerância incorporada na própria ferramenta de molde. Normalmente, os moldes de injeção são usinados por CNC para tolerâncias de +/- 0,003 polegadas (0,076 mm). Isso representa a precisão das dimensões da cavidade do molde.
A tolerância da resina se refere à tolerância da peça moldada acabada, que é influenciada pelas propriedades do material e pelo processo de moldagem. A tolerância da resina é geralmente maior ou igual para +/- 0,002 polegadas por polegada (0,051 mm por mm).
Juntos, esses dois tipos de tolerâncias determinam a precisão dimensional geral alcançável para peças moldadas por injeção.
As tolerâncias realmente alcançáveis podem variar com base em diferentes fatores. No entanto, em geral, para aplicações não críticas, a taxa de tolerância típica é ±0,1 mm; para aplicações que exigem tolerâncias mais rigorosas (por exemplo, peças médicas) é ±0,025 ou melhor.
Por que as tolerâncias de moldagem por injeção são importantes?
Muitos setores, como automotivo, aeroespacial e de dispositivos médicos, têm requisitos de tolerância rigorosos para segurança e conformidade regulatória.
Tolerâncias determinam se as peças se encaixarão corretamente durante a montagem e funcionarão conforme o esperado. Mesmo pequenos desvios podem causar problemas com ajuste, alinhamento e desempenho, especialmente para montagens complexas.
O que afeta as tolerâncias de moldagem por injeção?
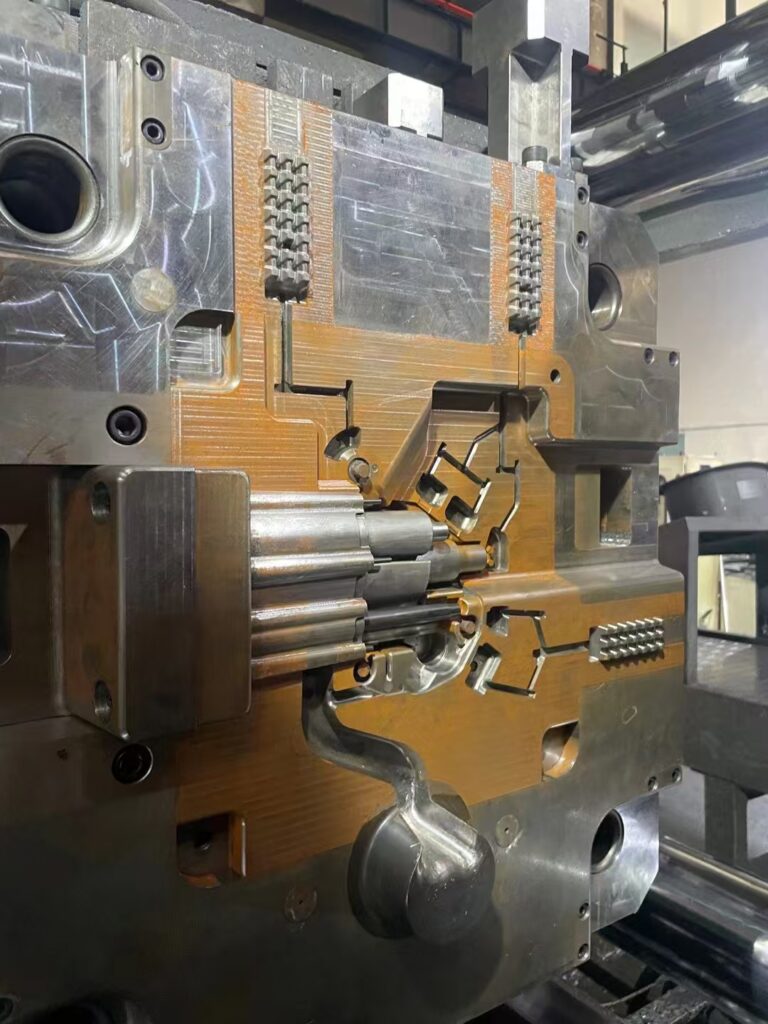
As tolerâncias de moldagem por injeção são influenciadas por vários fatores, que podem afetar a precisão dimensional e a consistência das peças moldadas. Aqui estão os principais fatores baseados em:
- Encolhimento: Diferentes materiais têm diferentes taxas de contração, o que impacta a capacidade de atingir tolerâncias apertadas. Materiais cristalinos geralmente têm maiores taxas de contração em comparação a materiais amorfos devido a mudanças de fase durante o resfriamento. Isso afeta o volume e as dimensões da peça final.
- Deformação: Conforme a resina esfria no molde, todas as peças sofrem encolhimento. Peças com espessura de parede uniforme tendem a encolher uniformemente, o que ajuda a evitar empenamento e marcas de afundamento. Em contraste, peças com espessuras de parede não uniformes esfriam e encolhem em taxas variadas, levando a uma maior probabilidade de empenamento devido ao design.
- Expansão térmica: Plásticos geralmente apresentam altas taxas de expansão térmica, o que pode causar mudanças dimensionais quando as temperaturas flutuam. Isso é especialmente crucial quando as peças são usadas em ambientes com variações de temperatura ou são combinadas com materiais como metais.
- Design de peças: A geometria, o tamanho e a espessura da parede de uma peça influenciam significativamente o controle de tolerância. Peças maiores ou aquelas com seções espessas podem apresentar diferentes taxas de encolhimento, tornando mais desafiador manter tolerâncias apertadas. Espessura de parede uniforme e recursos de design estratégico podem ajudar a gerenciar esses problemas.
- Complexidade da Parte: Peças complexas podem afetar o fluxo de material e o design da ferramenta, impactando a capacidade de manter tolerâncias rígidas. O gerenciamento adequado da pressão de injeção, viscosidade da resina e tempo de preenchimento do molde é essencial para garantir qualidade consistente da peça.
- ferramentas: O design e o material do molde, bem como o número de cavidades, afetam a capacidade de atingir as tolerâncias desejadas. Resfriamento e aquecimento consistentes são cruciais para manter tolerâncias apertadas. Ferramentas multicavidades ou familiares exigem design e suporte cuidadosos para evitar erros devido a variações de pressão ou temperatura.
Como reduzir o impacto dos fatores que afetam as tolerâncias de moldagem por injeção
Para reduzir o impacto de fatores que afetam as tolerâncias de moldagem por injeção, várias estratégias podem ser empregadas:
- Design para Manufaturabilidade (DFM):
- Envolva-se em práticas de DFM no início do processo de design do molde para antecipar potenciais variações e evitar reprojetos dispendiosos. Isso envolve projetar peças com espessuras de parede consistentes e ângulos de inclinação apropriados e considerar o posicionamento de recursos como saliências e nervuras para minimizar empenamento e encolhimento.
- Seleção de materiais:
- Escolha materiais com taxas de contração adequadas para a aplicação. Considere as propriedades de expansão térmica e como diferentes materiais podem interagir, especialmente em montagens multimateriais. Aumente as dimensões do molde para compensar a contração do material.
- Considerações sobre ferramentas:
- Projete moldes com ferramentas precisas para garantir dimensões consistentes de peças plásticas. Isso inclui otimizar os locais de passagem para fluxo uniforme de material, usar canais de resfriamento para resfriamento uniforme e colocar pinos ejetores para minimizar empenamentos e defeitos de superfície.
- Controle de Processo:
- Implemente controles de processo eficazes para gerenciar variáveis como temperatura, pressão e tempo de resfriamento. Use sensores para monitorar esses parâmetros em tempo real, permitindo ajustes rápidos para manter tolerâncias consistentes.
- Prototipagem e Testes Rápidos:
- Utilize prototipagem rápida para testar e refinar designs antes da produção em larga escala. Isso permite que ajustes sejam feitos no design ou processo para melhorar as tolerâncias e a qualidade das peças.
Normas de tolerâncias de moldagem por injeção
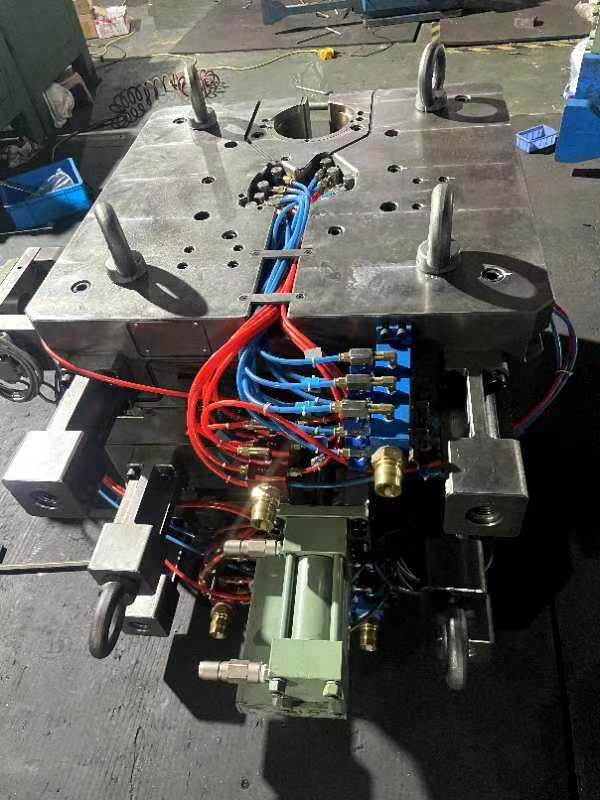
Aqui está uma tabela visualizando as tolerâncias dimensionais em milímetros (mm):
Material | Faixa de Dimensões | Tolerância Comercial | Tolerância de Precisão |
abdômen | 1 a 20 | ±0,100 | ±0,050 |
21 a 100 | ±0,150 | ±0,100 | |
101 a 160 | ±0,325 | ±0,100 | |
Mistura ABS/PC | 1 a 20 | ±0,100 | ±0,050 |
21 a 100 | ±0,150 | ±0,100 | |
GPS | 1 a 20 | ±0,075 | ±0,050 |
21 a 100 | ±0,150 | ±0,080 | |
PEAD | 1 a 20 | ±0,125 | ±0,075 |
21 a 100 | ±0,170 | ±0,110 | |
PEBD | 1 a 20 | ±0,125 | ±0,075 |
21 a 100 | ±0,170 | ±0,110 | |
Mod PPO/EPI | 1 a 20 | ±0,100 | ±0,050 |
21 a 100 | ±0,150 | ±0,100 | |
PA | 1 a 20 | ±0,075 | ±0,030 |
21 a 100 | ±0,160 | ±0,130 | |
PA 30% GF | 1 a 20 | ±0,060 | ±0,030 |
21 a 100 | ±0,120 | ±0,100 | |
PBT 30% GF | 1 a 20 | ±0,060 | ±0,030 |
21 a 100 | ±0,120 | ±0,100 | |
computador | 1 a 20 | ±0,060 | ±0,030 |
21 a 100 | ±0,120 | ±0,100 | |
PC 20% Vidro | 1 a 20 | ±0,050 | ±0,030 |
21 a 100 | ±0,100 | ±0,080 | |
PMMA | 1 a 20 | ±0,075 | ±0,050 |
21 a 100 | ±0,120 | ±0,070 | |
POM | 1 a 20 | ±0,075 | ±0,030 |
21 a 100 | ±0,160 | ±0,130 | |
PP, 20% Talco | 1 a 20 | ±0,100 | ±0,050 |
21 a 100 | ±0,120 | ±0,100 | |
EPI/OPP | 1 a 20 | ±0,080 | ±0,050 |
21 a 100 | ±0,100 | ±0,080 | |
PPS, 30% GF | 1 a 20 | ±0,050 | ±0,050 |
21 a 100 | ±0,080 | ±0,080 | |
São | 1 a 20 | ±0,080 | ±0,050 |
21 a 100 | ±0,100 | ±0,080 |
A tabela a seguir visualiza as dimensões de Tolerâncias de concentricidade/ovalidade (em mm)
Material | Faixa de Dimensões | Tolerância Comercial | Tolerância de Precisão |
abdômen | até 100 | ±0,230 | ±0,130 |
Mistura ABS/PC | até 100 | ±0,230 | ±0,130 |
GPS | até 100 | ±0,250 | ±0,150 |
PEAD | até 100 | ±0,250 | ±0,150 |
PEBD | até 100 | ±0,250 | ±0,150 |
PA | até 100 | ±0,250 | ±0,150 |
PA, 30% GF | até 100 | ±0,150 | ±0,100 |
PBT, 30% GF | até 100 | ±0,150 | ±0,100 |
computador | até 100 | ±0,130 | ±0,080 |
PC, 20% GF | até 100 | ±0,130 | ±0,080 |
PMMA | até 100 | ±0,250 | ±0,150 |
POM | até 100 | ±0,250 | ±0,150 |
PP | até 100 | ±0,250 | ±0,150 |
PP, 20% Talco | até 100 | ±0,250 | ±0,150 |
EPI/OPP | até 100 | ±0,230 | ±0,130 |
PPS, 30% GF | até 100 | ±0,130 | ±0,080 |
São | até 100 | ±0,230 | ±0,130 |
Tolerâncias de Retidão/Planicidade (mm)
Material | Tamanho do recurso | Tolerância Comercial | Tolerância fina |
abdômen | 0–100 mm | ±0,380 | ±0,250 |
101–160 milímetros | ±0,800 | ±0,500 | |
Mistura ABS/PC | 0–100 mm | ±0,380 | ±0,250 |
101–160 milímetros | ±0,800 | ±0,500 | |
PA | 0–100 mm | ±0,300 | ±0,150 |
101–160 milímetros | ±0,500 | ±0,250 | |
PA GF 30% | 0–100 mm | ±0,150 | ±0,080 |
101–160 milímetros | ±0,200 | ±0,100 | |
POM | 0–100 mm | ±0,300 | ±0,150 |
101–160 milímetros | ±0,500 | ±0,250 | |
PP | 0–100 mm | ±0,850 | ±0,500 |
101–160 milímetros | ±1.500 | ±0,850 | |
São | 0–100 mm | ±0,380 | ±0,250 |
101–160 milímetros | ±0,800 | ±0,500 |
Tolerâncias de profundidade de furo cego (mm)
Material | Alcance de profundidade | Tolerância Comercial | Tolerância fina |
abdômen | até 100 mm | ±0,200 | ±0,100 |
Mistura ABS/PC | até 100 mm | ±0,200 | ±0,100 |
PA | até 100 mm | ±0,150 | ±0,080 |
PA GF 30% | até 100 mm | ±0,100 | ±0,050 |
POM | até 100 mm | ±0,150 | ±0,080 |
PP | até 100 mm | ±0,250 | ±0,150 |
São | até 100 mm | ±0,200 | ±0,100 |
Tolerâncias de diâmetro de furo (mm)
Material | Faixa de diâmetro | Tolerância Comercial | Tolerância fina |
abdômen | até 100 mm | ±0,100 | ±0,050 |
Mistura ABS/PC | até 100 mm | ±0,100 | ±0,050 |
PA | até 100 mm | ±0,080 | ±0,040 |
PA GF 30% | até 100 mm | ±0,050 | ±0,025 |
POM | até 100 mm | ±0,080 | ±0,040 |
PP | até 100 mm | ±0,120 | ±0,060 |
São | até 100 mm | ±0,100 | ±0,050 |