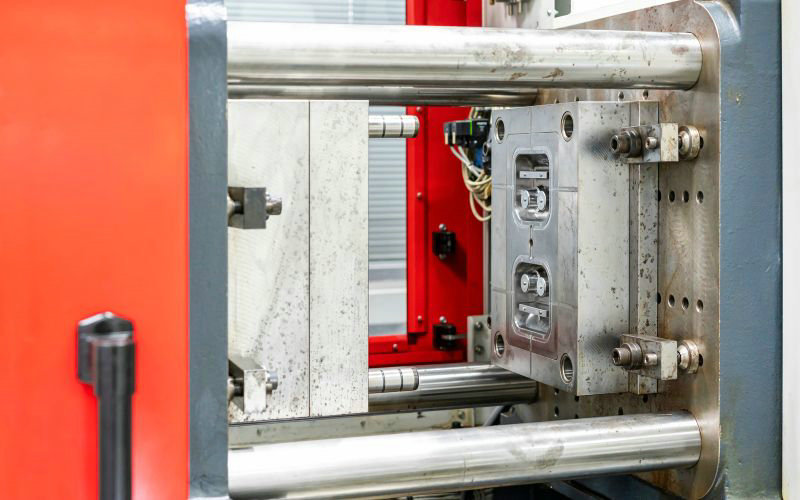
Classification des moules à injection
Si vous évaluez des moules à injection, il est essentiel de comprendre les Système de classification qui différencie leurs capacités et leurs applications. Dans cet article, nous vous fournirons un guide simple pour comprendre les différents types de moules :
- Par Géométrie
- Par Nombre de cavités
- Par Plaque de moule
- Par Principe d'éjection
- Par Matériau plastique
- Par Système d'alimentation
Votre choix parmi ces types de moules à injection équilibre souvent l’ampleur de votre projet, la complexité des pièces et les implications en termes de coûts opérationnels. Explorons ensemble différents types de moules d'injection plastique !
Par géométrie
- Géométries simples:
- Plus facile à concevoir et à fabriquer.
- Ils comportent souvent moins de sections creuses.
- Géométries complexes:
- Permet une plus grande flexibilité de conception.
- Peut accueillir des sections creuses nécessaires à des fonctions spécifiques.
Les pièces complexes incluent souvent des caractéristiques telles que des contre-dépouilles, qui sont des indentations ou des saillies qui peuvent compliquer la conception du moule. La conception des contre-dépouilles nécessite une attention particulière pour garantir que les composants du moule peuvent se séparer correctement pendant la phase d'éjection sans endommager la pièce.
Pour les conceptions de composants complexes, l'utilisation de technologies de moulage avancées, telles que des curseurs ou des élévateurs, peut s'avérer nécessaire pour créer et démouler avec succès la pièce. Bien que cette approche offre une grande flexibilité de conception, elle ajoute également à la complexité et au coût du moule.
Votre choix entre une géométrie de moule simple ou complexe dépendra en fin de compte de la conception de la pièce souhaitée, de la fonctionnalité, de la faisabilité du processus de fabrication du moule et du budget du projet. Équilibrez toujours le besoin de géométries complexes avec des considérations pratiques de production.
Par nombre de cavités
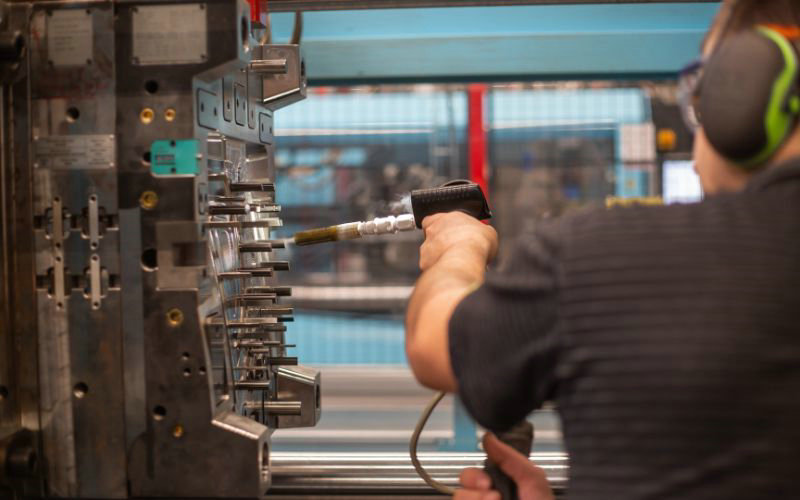
Moules à cavité unique
- Produire un seul produit par cycle d'injection
- Idéal pour les pièces volumineuses, complexes ou de faible volume
- Accorder plus d’attention aux pièces individuelles pour minimiser les défauts
- Coûts d'outillage réduits par rapport aux moules multi-empreintes pour la même pièce
- Convient au prototypage et à la fourniture de nouvelles conceptions
Moules multi-empreintes
- Contient plusieurs cavités identiques pour produire plusieurs pièces par cycle
- Permettre des délais de livraison plus courts et une efficacité de production accrue pour les volumes élevés
- Réduisez les coûts par pièce pour les grands lots
- Nécessite une conception soignée pour garantir un remplissage uniforme et une qualité constante dans toutes les cavités
- Peut avoir des coûts d'outillage initiaux plus élevés que les moules à empreinte unique
- Le nombre typique de cavités va de 2 à 64 ou plus, en fonction de la taille de la pièce et de l'application.
Moules familiaux
- Incorporez plusieurs cavités de formes différentes pour produire diverses pièces en un seul cycle
- Permettre le moulage de composants associés ou de variantes de produits en une seule fois
- Utile pour le prototypage ou la production de kits avec des pièces assorties
- Limité aux pièces utilisant le même matériau et la même couleur
- Remplissage souvent déséquilibré en raison de géométries différentes des cavités, augmentant le risque de défauts
- Nécessite plus de travail après moulage pour séparer et manipuler différentes pièces
Par plaque de moule
Moulage par injection à deux plaques
- Conception de moule à injection la plus simple et la plus courante, composée de deux parties principales (côté A et côté B)
- Possède une seule ligne de séparation où le moule se divise en deux moitiés
- Le côté cavité est fixe, tandis que le côté noyau est mobile pendant le processus de moulage.
- Le canal d'alimentation et la pièce sont situés sur le même plan de joint et éjectés ensemble
- Avantages : coût inférieur, temps de cycle plus courts, plus facile à installer et à utiliser
- Inconvénients : moins de flexibilité dans l'emplacement des portes, nécessite une délégation manuelle, risque de tirs courts dans les moules multi-empreintes
Moulage par injection à trois plaques
- Également connu sous le nom de moule à plaque de dévêtissage, il se compose de deux plans de séparation et se divise en trois sections.
- Possède une plaque flottante supplémentaire entre la cavité et le noyau pour accueillir le système de glissières
- Permet le dégazage automatique du canal de la pièce
- Offre plus de flexibilité dans l'emplacement des portes par rapport aux moules à deux plaques
- Avantages : convient aux grandes pièces nécessitant plusieurs portes, permet un débat automatique
- Inconvénients : plus complexe et coûteux, temps de cycle plus longs, moins stable en raison du plus grand nombre de pièces mobiles
Moulage par injection de pile
- Structure de moule spéciale avec plusieurs surfaces de séparation, chacune pouvant accueillir une ou plusieurs empreintes
- Se compose d'un moule mobile, d'un moule central et d'un moule fixe qui s'ouvrent simultanément
- Peut doubler la production d'un moule standard sans nécessiter de machines supplémentaires
- Convient à la production en grand volume de pièces plates à parois minces
- Avantages : productivité nettement accrue, coûts réduits, délais de fabrication plus courts
- Inconvénients : conception plus complexe, nécessite un équilibre minutieux entre le remplissage de la cavité et le refroidissement
Par principe d'éjection
1. Éjection des broches
- Utilise des éjecteurs pour pousser la pièce moulée hors de la cavité du moule
- Les broches sont situées dans la moitié d'éjection du moule et sont conçues pour résister aux forces d'éjection
- Le diamètre, la longueur, le matériau, l'emplacement et la forme des broches sont des considérations de conception critiques
- Convient à la plupart des pièces moulées par injection, mais peut laisser des marques visibles sur les éjecteurs.
2. Éjection du manchon
- Utilise un éjecteur en forme de manchon qui entoure le noyau pour éjecter la pièce
- Fournit une force d'éjection uniforme et stable sans laisser de marques visibles
- Convient aux produits cylindriques, à parois minces ou en forme de coquille
- Plus complexe et plus coûteux que l'éjection des broches
3. Éjection de la plaque de décapage
- Utilise une plaque à dénuder pour pousser la pièce hors du noyau
- La force d'éjection est élevée, uniforme et stable, minimisant la déformation de la pièce
- Idéal pour les pièces cylindriques, les récipients à parois minces et les produits en forme de coquille
- Évite les marques d'éjection visibles mais présente une structure de moule plus complexe et un coût plus élevé
4. Éjection de la lame
- Utilise des lames d'éjecteur rectangulaires au lieu de broches
- Convient aux pièces avec des géométries ou des exigences spécifiques
5. Éjection d'air
- Introduit de l'air comprimé entre la pièce et le moule pour éjecter la pièce
- Simplifie la structure du moule et permet l'éjection à n'importe quel endroit
- Souvent utilisé pour prendre en charge d'autres méthodes d'éjection pour les pièces de grande taille, à cavité profonde ou à paroi mince.
6. Éjection du poussoir
- Utilise des élévateurs qui se déplacent latéralement pour libérer les contre-dépouilles ou les caractéristiques internes
- Permet l'éjection de pièces avec des géométries complexes ou des actions secondaires
Par matière plastique
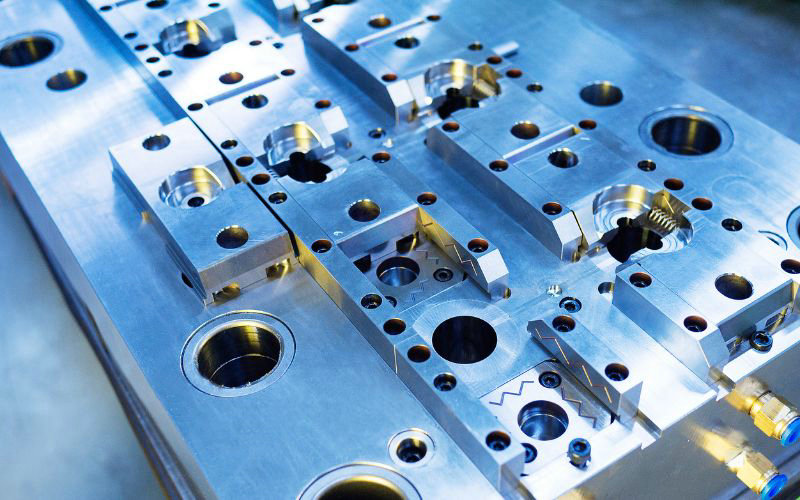
1. Acrylique (PMMA)
- Thermoplastique solide et transparent avec une excellente clarté optique et résistance aux UV
- Alternative légère et incassable au verre
- Utilisé pour les lentilles, les écrans, les panneaux et les dispositifs médicaux
2. Acrylonitrile Butadiène Styrène (ABS)
- Thermoplastique robuste, rigide et résistant aux chocs
- Bonne résistance chimique et facile à peindre ou à coller.
- Utilisé pour les pièces automobiles, les appareils électroménagers, les jouets et les boîtiers électroniques
3. Nylon (Polyamide, PA)
- Thermoplastique solide, flexible et résistant à l'usure
- Point de fusion élevé et bonne résistance chimique
- Utilisé pour les pièces automobiles, les engrenages, les roulements et les composants électriques
4. Polycarbonate (PC)
- Thermoplastique solide, transparent et résistant à la chaleur
- Bonne stabilité dimensionnelle et propriétés d'isolation électrique
- Utilisé pour les composants automobiles, les dispositifs médicaux et les lunettes de sécurité
5. Polyéthylène (PE)
- Thermoplastique léger, flexible et résistant aux produits chimiques
- Variantes haute densité (HDPE) et basse densité (LDPE) disponibles
- Utilisé pour les emballages, les conteneurs, les jouets et les composants automobiles
6. Polyoxyméthylène (POM)
- Thermoplastique solide, rigide et dimensionnellement stable
- Excellente résistance à l’usure et aux produits chimiques
- Utilisé pour les engrenages, les roulements et les pièces de précision
7. Polypropylène (PP)
- Thermoplastique léger, robuste et résistant aux produits chimiques
- Bonnes propriétés de résistance à la fatigue et d’isolation électrique
- Utilisé pour l'emballage, les pièces automobiles et les articles ménagers
8. Polystyrène (PS)
- Thermoplastique rigide, transparent et facile à mettre en œuvre\
- Faible coût et bonne stabilité dimensionnelle
- Utilisé pour les emballages, les couverts jetables et les jouets
9. Élastomères thermoplastiques (TPE) et polyuréthanes (TPU)
- Thermoplastiques flexibles de type caoutchouc avec une bonne résistance aux chocs et à l'abrasion
- Les TPU offrent une meilleure résistance aux produits chimiques et à la température que les TPE
- Utilisé pour les poignées, les joints, les joints et les chaussures doux au toucher.
Par système d'alimentation
Moulage par injection de canaux froids
- Se compose de la carotte d'injection, des canaux d'alimentation, des canaux secondaires, des portes et des puits de limaces froides.
- Sprue délivre la matière fondue de la buse au système de canaux
- Les coureurs transportent la matière fondue de la carotte aux portes
- Les portes sont de petits orifices reliant le canal à la cavité
- Les puits à bouchons froids stockent le matériau froid initial produit pendant les intervalles d'injection
- Peut être divisé en systèmes de portes latérales et de portes ponctuelles
- Convient à la plupart des applications de moulage par injection
Moulage par injection de canaux chauds
- N'a pas de coureur principal ni de sous-coureur
- La fonte passe à travers une plaque collectrice et une buse chaude directement dans la cavité via des portes
- Utilise des moules à canaux isolés ou à canaux chauds
- Élimine le besoin d'un système de canaux froids traditionnel
- Réduit les déchets de matériaux et les temps de cycle par rapport aux systèmes à canaux froids
Moulage par injection sans coureur
- La matière fondue s'écoule directement de la buse dans la cavité sans système de canaux
- Conception du système d'alimentation la plus simple
Moulage par injection recommandé chez Moldie
Moldie est l'un des principaux fournisseurs de moules d'injection plastique et de services de moulage de précision et de haute qualité. Forte de plusieurs années d'expérience et d'une technologie de pointe, Moldie propose une large gamme de solutions de moulage par injection pour répondre à vos besoins spécifiques :
Moulage par injection de produits de moulage en plastique de précision
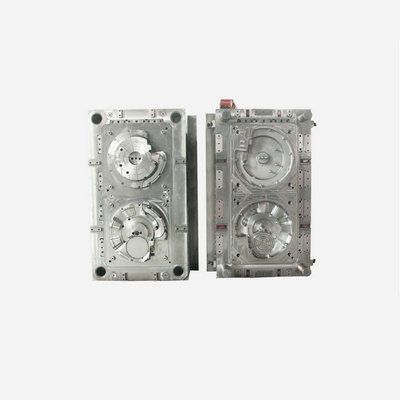
Découvrez des produits de moulage de plastique de précision offrant un choix de matériaux robustes, une expertise en canaux froids/chauds et la brillance des couleurs RAL PANTONE.
Pièces en plastique de haute précision sur mesure
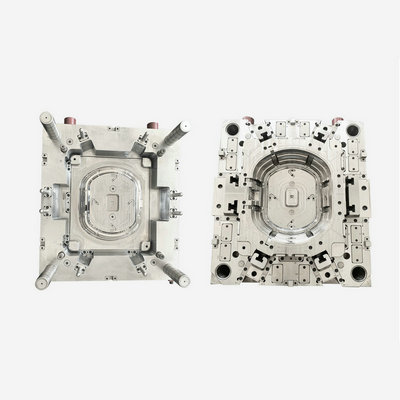
La complexité des opérations primaires, secondaires et de finition impliquées est la raison pour laquelle vous ne devez faire appel qu'aux services d'experts comme ceux de notre entreprise pour gérer votre processus de production.
Fabricant de moulures en plastique sur mesure
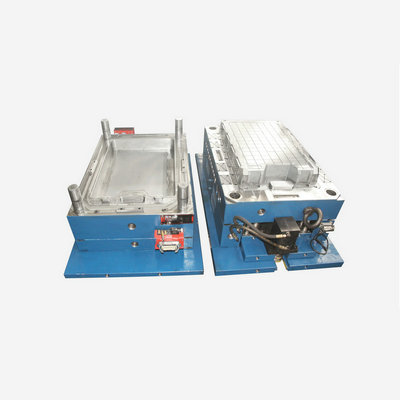
Avec des poids de moules allant de 50 kg à 15 tonnes et une compatibilité avec des machines d'injection jusqu'à 1 500 tonnes, l'adaptabilité est au cœur de ce que nous faisons.
Choisir moisi pour vos besoins de moulage par injection et découvrez la différence que peuvent faire la précision, l'expertise et un service centré sur le client. Contactez-nous dès aujourd'hui pour discuter de votre projet et découvrir comment nous pouvons vous aider à donner vie à votre vision.