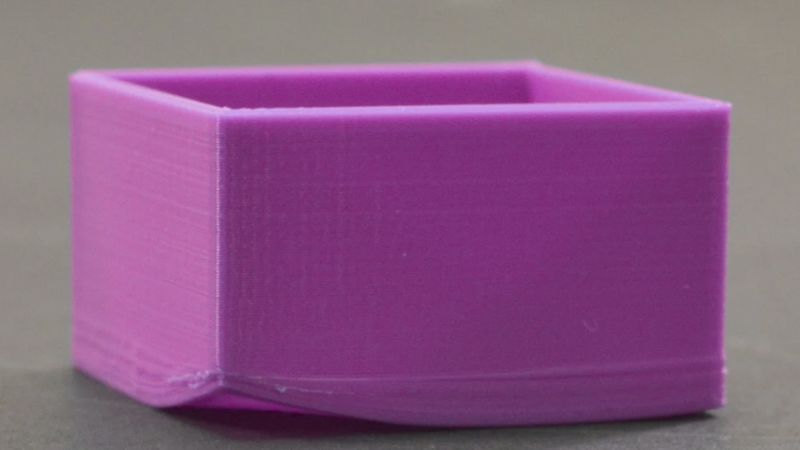
Las deformaciones pueden resultar molestas. Tanto para los fabricantes como para los diseñadores de productos, es importante comprender las causas fundamentales de las deformaciones y la implementación de estrategias de prevención eficaces es crucial para mantener una producción de alta calidad y minimizar los costos de producción.
En esta guía completa, exploraremos los principales factores que contribuyen a la deformación en el moldeo por inyección y brindaremos soluciones prácticas para mitigar este problema.
Al aplicar estos conocimientos, los fabricantes pueden mejorar su eficiencia de producción, reducir las tasas de desperdicio y, en última instancia, ofrecer piezas moldeadas por inyección de calidad superior.
¿Qué es la deformación del molde?
La deformación es uno de los problemas de calidad cruciales en el moldeo por inyección de plástico, y a menudo provoca inestabilidad dimensional en las piezas de plástico.
La deformación se refiere a la desviación indeseable de la geometría prevista del producto que puede ocurrir en las piezas de plástico durante el proceso de moldeo por inyección. Este defecto se manifiesta como distorsiones como torsiones, dobleces o curvaturas de la pieza moldeada.
La gravedad de la deformación varía desde ligeras deformaciones, apenas perceptibles a simple vista, hasta distorsiones importantes que interfieren en el funcionamiento o el montaje de la pieza.
El impacto de la deformación en los productos moldeados
La presencia de deformaciones en el moldeo por inyección tiene implicaciones sustanciales en la calidad y funcionalidad de las piezas de plástico:
- Calidad estética:El atractivo visual se ve comprometido, lo que hace que los productos finales sean menos competitivos en el mercado.
- Estabilidad dimensional:Es posible que las piezas deformadas no encajen en los conjuntos o no cumplan con las dimensiones precisas requeridas para interactuar con otros componentes.
- Deficiencias funcionales:Más allá de la estética, la deformación puede afectar el rendimiento mecánico y la integridad estructural del componente.
¿Cuál es la causa de la deformación en el moldeo por inyección?
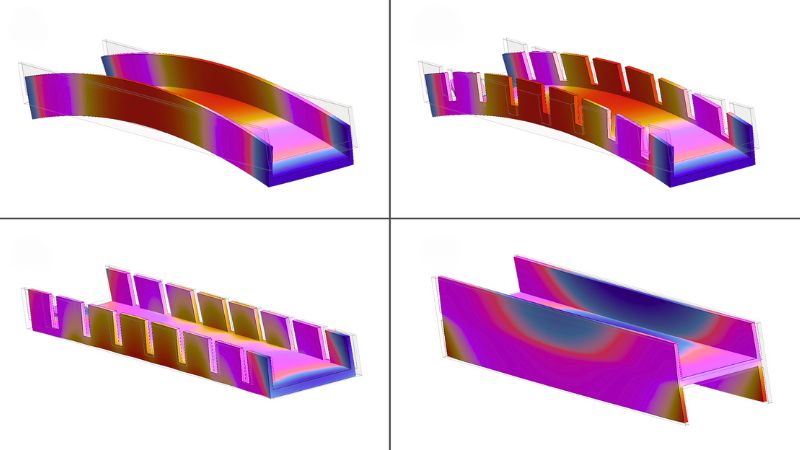
Esta sección explora las complejidades de máquina, molde, y factores materiales contribuyendo a la deformación y proporciona algunas soluciones prácticas para mitigar estos problemas.
Errores de la máquina
Presión o tiempo de inyección inadecuados
Una presión de inyección o un tiempo de retención insuficientes pueden provocar un llenado inadecuado del molde. Esto puede provocar que el material plástico se enfríe y se solidifique antes de que el molde se llene correctamente.
Ambos escenarios dan lugar a un movimiento descontrolado de moléculas durante el enfriamiento, lo que genera contracción y deformación desiguales.
Temperatura incorrecta del barril
Si la temperatura del barril es demasiado baja, la resina no alcanzará su temperatura de flujo adecuada, lo que provocará una solidificación prematura, un empaque inadecuado del molde y, en última instancia, una contracción y deformación desiguales.
Tiempo de residencia inadecuado
Un tiempo de residencia inadecuado impide la absorción uniforme del calor en toda la resina. Esto puede provocar que las partes del material que no se calentaron lo suficiente se endurezcan y se solidifiquen prematuramente, lo que da como resultado un empaquetamiento incompleto del molde y deformaciones.
Tensión interna excesiva
Las altas presiones de inyección pueden crear tensiones internas dentro de la pieza moldeada, que pueden manifestarse como deformación después de la expulsión del molde.
Tiempo de avance del tornillo incorrecto
Si el tiempo de avance del tornillo es demasiado largo, puede provocar un sobrellenado del molde, creando tensiones internas que resultan en deformaciones.
Tiempo de enfriamiento insuficiente
Un tiempo de enfriamiento insuficiente puede impedir que la pieza se enfríe de manera uniforme y completa antes de su expulsión, lo que genera una contracción desigual y deformación a medida que continúa enfriándose fuera del molde.
Errores de moho
Ubicación y diseño inadecuados de la puerta
La colocación incorrecta de la compuerta puede provocar un llenado y llenado desigual de la cavidad del molde, lo que genera una distribución de la presión y velocidades de enfriamiento inconsistentes, lo que provoca deformaciones.
Colocación inadecuada del pasador eyector
Los pasadores de expulsión mal colocados o insuficientes pueden provocar tensiones desiguales al expulsar la pieza del molde, lo que puede provocar deformaciones, especialmente en piezas con geometrías complejas.
Circuitos de refrigeración desequilibrados
Los circuitos de enfriamiento mal equilibrados pueden provocar un enfriamiento desigual en las cavidades, lo que genera deformaciones en algunas partes mientras que otras permanecen intactas.
Errores en la selección de materiales
Altas tasas de contracción
Los materiales con altas tasas de contracción son más propensos a deformarse.
Por ejemplo, los polímeros semicristalinos como el polietileno (PE) y el polipropileno (PP) tienen tasas de contracción más altas en comparación con los polímeros amorfos como el policarbonato (PC) o el poliestireno (PS).
Contracción inconsistente
Algunos materiales se encogen de forma diferente en la dirección del flujo que en la dirección transversal. Esta contracción anisotrópica puede provocar deformaciones, especialmente en piezas con trayectorias de flujo largas.
Cristalinidad
Los materiales altamente cristalinos son más susceptibles a la deformación debido a su tendencia a contraerse más durante el enfriamiento.
Sensibilidad a la humedad
Algunos materiales, como el nailon, son higroscópicos y pueden absorber la humedad del aire. Esto puede generar resultados de moldeado inconsistentes y posibles deformaciones si no se secan adecuadamente antes del procesamiento.
¿Cómo reducir la deformación en el moldeo por inyección?
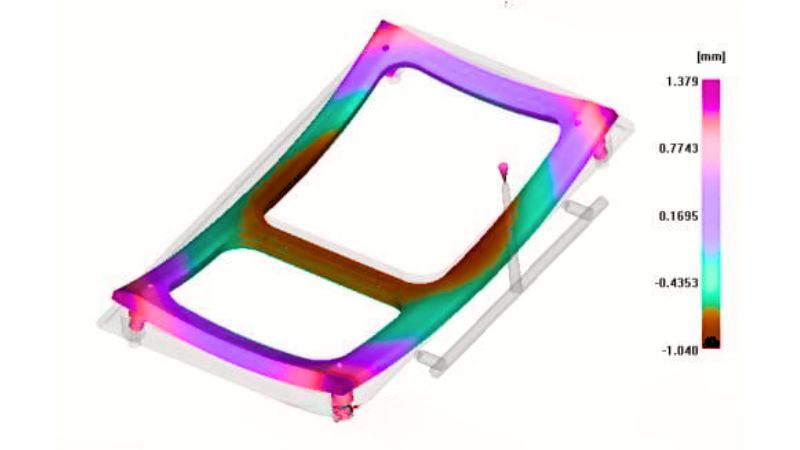
La optimización de los parámetros de procesamiento es fundamental, empezando por ajustar la presión de inyección y el tiempo de retención para garantizar un llenado adecuado de la cavidad del molde. Esto limita las moléculas de plástico y evita el movimiento descontrolado durante el enfriamiento.
Aumentar el tiempo de enfriamiento permite un enfriamiento completo y uniforme, lo que ayuda a prevenir tasas de contracción diferenciales que a menudo provocan deformaciones.
Ajustar la configuración de temperatura es igualmente importante: aumentar la temperatura del barril garantiza un flujo adecuado del material, mientras que ajustar la temperatura del molde según las recomendaciones del proveedor de resina promueve la uniformidad.
Siempre que sea posible, la implementación de canales de enfriamiento conformes puede mejorar aún más el enfriamiento uniforme en toda la pieza.
Consideraciones sobre el diseño de moldes y materiales
La optimización de compuertas y canales mediante el uso de tipos de compuertas adecuados para plásticos y diseños de productos específicos, la implementación de múltiples compuertas para piezas planas y la ampliación de compuertas y canales pueden mejorar significativamente el llenado del molde.
La colocación correcta del pasador de expulsión también es crucial: garantizar que sea lo suficientemente ancho, esté bien distribuido y ubicado cerca de las áreas con mayor resistencia a la expulsión puede evitar deformaciones durante la extracción de la pieza.
La selección y el manejo de los materiales son factores clave. Elegir resinas menos propensas a deformarse, como plásticos amorfos como el policarbonato y el poliestireno en lugar de plásticos cristalinos, puede marcar una diferencia sustancial.
Para las piezas que utilizan insertos de metal, precalentarlos a alrededor de 100 °C ayuda a adaptarse a las diferencias de contracción entre el metal y el plástico, lo que reduce la tensión y la posible deformación.
Optimización del diseño y control de calidad
La optimización del diseño de la pieza es otro aspecto fundamental. Mantener un espesor de pared uniforme en toda la pieza promueve un enfriamiento y una contracción uniformes, mientras que agregar nervaduras de refuerzo puede mejorar la rigidez de la pieza y reducir la tendencia a la deformación.
Cooperar con profesionales — Moldie
Trabajando con moho Puede generar calidad y eficiencia en el proceso de inyección de plástico moldeado. Contamos con la experiencia necesaria para manejar una amplia variedad de materiales plásticos, lo que garantiza que los productos plásticos resultantes combinen durabilidad y estética.
Moldie pone énfasis en la precisión en sus técnicas de fabricación. Nuestro enfoque implica:
- Diseño avanzado de moldesAl optimizar el tamaño y la forma de la compuerta, Moldie ayuda a mantener un flujo y un enfriamiento uniformes, lo que genera menos estrés interno y reduce la deformación.
- Selección de materiales:Su conocimiento de diversos plásticos permite una elección informada del material, adaptando las propiedades a la aplicación prevista y mitigando los defectos.
- Optimización de procesosMoldie ajusta con precisión la temperatura del molde y las velocidades de enfriamiento, ya que estas variables juegan un papel fundamental en la producción de componentes de alta calidad y sin deformaciones.
Creemos que dicha colaboración puede elevar significativamente el estándar de los componentes plásticos producidos, mejorando en última instancia la funcionalidad y la apariencia del producto final.