El diseño adecuado de las nervaduras es esencial para lograr una resistencia óptima de la pieza y, al mismo tiempo, mantener la viabilidad de fabricación y la rentabilidad. Cuando se implementan estratégicamente, las nervaduras pueden evitar deformaciones, dar soporte a elementos aislados, reducir el consumo de material y mejorar el flujo del molde. Sin embargo, el diseño de nervaduras eficaces requiere un conocimiento profundo de las propiedades de los materiales, los procesos de moldeo y los principios de diseño.
Este artículo profundiza en los aspectos básicos del diseño de nervaduras de moldeo por inyección y explora consideraciones clave como la geometría de las nervaduras, la selección de materiales y las pautas de diseño. Al dominar estos aspectos esenciales, los ingenieros y diseñadores pueden crear piezas que no solo cumplan con los requisitos de resistencia, sino que también optimicen la eficiencia de producción y la calidad del producto.
¿Qué es la costilla?
Las nervaduras son una característica de diseño importante en el moldeo por inyección de plástico que aumenta la resistencia y el soporte de las piezas sin aumentar el espesor general de la pared.
Las nervaduras son estructuras delgadas similares a paredes que se extienden perpendicularmente a una pared o plano en piezas moldeadas por inyección, que sirven para agregar soporte y rigidez a la pieza, aumentar la resistencia sin aumentar el espesor de la pared y reemplazar secciones de pared gruesas para evitar defectos como marcas de hundimiento, deformaciones y huecos.
¿Cuál es el propósito de las nervaduras en el diseño de moldes?
Las nervaduras en el moldeo por inyección cumplen varias funciones críticas en el Diseño de piezas de plástico:
- Prevenir deformaciones:Las nervaduras ayudan a prevenir la deformación al reforzar las paredes delgadas. Las paredes gruesas pueden provocar un enfriamiento desigual, lo que provoca tensiones internas que resultan en deformaciones. Al usar nervaduras, las piezas pueden tener paredes más delgadas que se enfrían de manera más uniforme, lo que reduce el riesgo de deformación.
- Admite otras funciones:Las costillas brindan soporte estructural a elementos aislados, como salientes, que se utilizan como puntos de sujeción. Estos elementos requieren soporte adicional para mantener la integridad estructural, y las costillas los conectan a las paredes laterales o brindan refuerzo cuando están demasiado lejos de las paredes laterales.
- Reducir el uso de materiales:Las nervaduras ubicadas estratégicamente pueden aumentar la rigidez en áreas críticas sin aumentar el espesor general de la pieza. Esto permite un diseño liviano que utiliza menos material y al mismo tiempo cumple con los requisitos de resistencia.
- Mejorar el flujo del molde:Las nervaduras diseñadas correctamente pueden mejorar el flujo del plástico fundido en el molde, lo que garantiza un mejor llenado y reduce la probabilidad de defectos. Esta doble función de mejorar el flujo del molde y al mismo tiempo agregar resistencia hace que las nervaduras sean una característica de diseño esencial.
¿Cuáles son las diferencias entre costillas y refuerzos?
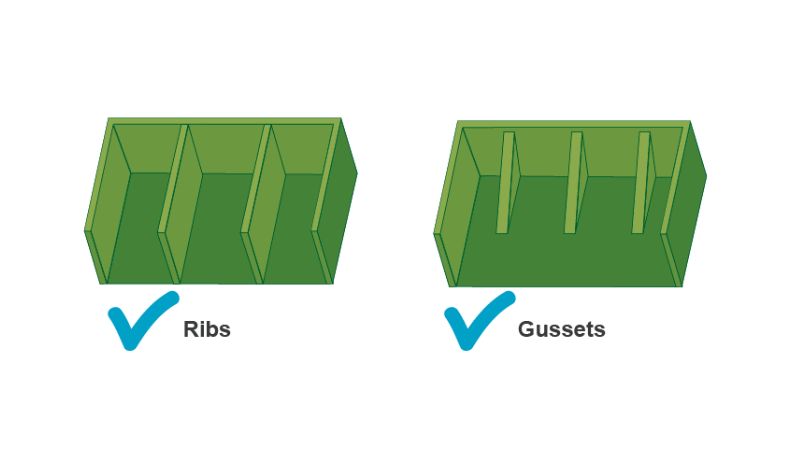
Los refuerzos son como piezas de material resistentes que se utilizan para hacer que las esquinas, las paredes y las conexiones de las estructuras sean mucho más resistentes. Piense en ellos como nervaduras especiales diseñadas para soportar la tensión y distribuirla de manera uniforme.
Los refuerzos, que generalmente tienen forma de triángulos o rectángulos, actúan como conectores fuertes que mantienen unidas las piezas y hacen que las uniones sean mucho más estables.
Los refuerzos se encuentran a menudo en elementos como puentes (vigas de celosía) y edificios (sistemas de arriostramiento lateral), donde unen partes diagonales y ayudan a soportar cargas pesadas. También se utilizan en objetos de plástico para reforzar puntos débiles.
En resumen, si bien tanto las nervaduras como los refuerzos se utilizan para mejorar la integridad estructural de una pieza, las nervaduras principalmente añaden soporte a las superficies planas. Por el contrario, los refuerzos se centran en reforzar las juntas y conexiones entre los diferentes componentes.
¿Cuáles son las pautas de diseño de costillas de plástico?
Grosor de la costilla
El espesor de las costillas no debe superar los 60% del espesor nominal de la pared. En el caso de materiales brillantes, puede ser necesario reducirlo a 40% para evitar defectos en la superficie, ya que las costillas más gruesas pueden provocar problemas como deformaciones o marcas de hundimiento, mientras que las costillas más delgadas pueden no rellenarse correctamente debido a la viscosidad del plástico.
Si es necesario variar el espesor de una costilla, la transición debe ser gradual para minimizar las concentraciones de tensión y las variaciones de enfriamiento, que pueden causar deformaciones. Además, la distancia de transición debe ser al menos tres veces el cambio de espesor.
Perforación de costillas
En el caso de costillas gruesas inevitables, se puede utilizar la perforación para reducir posibles defectos.
Altura de la costilla
Limite la altura de las costillas a tres veces el grosor de las costillas para evitar que queden demasiado pequeñas. Si es necesario, utilice varias costillas más pequeñas en lugar de una sola grande.
Espaciado entre costillas
Coloque varias costillas con una separación de al menos 2 a 3 veces el espesor nominal de la pared. Un patrón escalonado puede ayudar a reducir la deformación durante el enfriamiento.
Ángulo de tiro de la costilla
Aplique un ángulo de desmoldeo de 0,5 a 1,5 grados para facilitar la expulsión de la pieza. Solo se deben fabricar nervaduras de compresión sin ángulo de desmoldeo.
Radios de costillas
Incluya un radio donde la nervadura se interseca con la base o la pared lateral, normalmente de 0,5 a 1 vez el espesor de la pared, para reducir las concentraciones de tensión y mejorar la resistencia.
El ángulo de intersección
Las costillas no siempre deben intersecarse con las paredes laterales en un ángulo de 90 grados. Las intersecciones en ángulo pueden mejorar la rigidez sin aumentar el espesor de las costillas. Recuerde que se debe tener cuidado para evitar un espesor excesivo en las intersecciones, lo que puede provocar marcas de hundimiento en la superficie opuesta.
¿Qué materiales se utilizan para fabricar costillas?
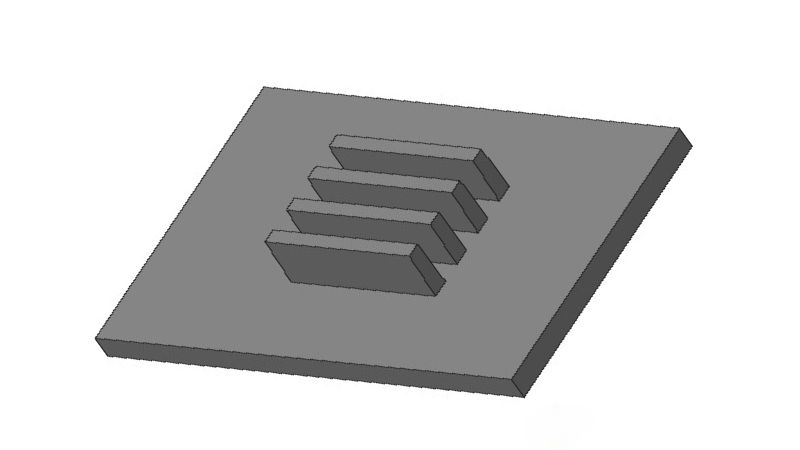
Al seleccionar materiales para las nervaduras en piezas moldeadas por inyección, la elección a menudo depende de los requisitos específicos de la aplicación, como resistencia, flexibilidad y resistencia ambiental.
Los materiales comunes utilizados para fabricar costillas incluyen:
- ABS (Acrilonitrilo Butadieno Estireno):
- Conocido por su buena resistencia al impacto y tenacidad.
- Adecuado para aplicaciones que requieren resistencia y rigidez.
- Policarbonato (PC):
- Ofrece alta resistencia al impacto y claridad.
- Se utiliza en aplicaciones donde se necesita transparencia y dureza.
- Polipropileno (PP):
- Proporciona excelente resistencia química y flexibilidad.
- Ideal para piezas que requieren resistencia a la fatiga y baja absorción de humedad.
- Nailon (poliamida, PA):
- Conocido por su alta resistencia y resistencia al desgaste.
- Adecuado para piezas expuestas a esfuerzos mecánicos y que requieran durabilidad.
- PBT (tereftalato de polibutileno):
- Ofrece buena resistencia química y estabilidad dimensional.
- Se utiliza en aplicaciones automotrices y eléctricas.
- Poliestireno (PS):
- Proporciona buena rigidez y facilidad de procesamiento.
- Adecuado para aplicaciones menos exigentes donde el costo es una preocupación principal.
- Polisulfona (PSU):
- Conocido por su alta resistencia a la temperatura y a los productos químicos.
- Se utiliza en aplicaciones que requieren estabilidad térmica y tenacidad.
El diseño eficaz de las nervaduras es un aspecto crucial para crear piezas moldeadas por inyección resistentes, eficientes y de alta calidad. Al comprender y aplicar los principios descritos en este artículo, los ingenieros y diseñadores pueden mejorar significativamente la integridad estructural de sus componentes plásticos y, al mismo tiempo, optimizar el uso del material y la capacidad de fabricación.