El corazón de Moldeo por inyección En el interior del molde se encuentra el núcleo del molde, un componente fundamental que da forma a las características internas del producto moldeado. Comprender los aspectos esenciales de los núcleos de moldeo por inyección es vital para optimizar tanto el diseño como la calidad del producto.
Este artículo analiza en profundidad los aspectos fundamentales de los núcleos de moldes y explora cómo influyen en el proceso de fabricación y el rendimiento del producto final. Al examinar consideraciones clave como la selección de materiales y las estrategias de diseño, nuestro objetivo es proporcionar información valiosa para los ingenieros y fabricantes que buscan lograr las mejores prácticas en las operaciones de moldeo por inyección.
Primero, presentemos el proceso básico del moldeo por inyección.
El proceso básico de moldeo por inyección implica varios pasos clave que transforman los materiales plásticos en productos terminados. A continuación, se ofrece una descripción simplificada:
- Reprimición:El proceso comienza cerrando el molde, que normalmente está formado por dos mitades. Estas mitades se sujetan firmemente para prepararlas para la inyección.
- Inyección:Los gránulos o pellets de plástico se introducen en un barril calentado donde se funden. Luego, el plástico fundido se inyecta en la cavidad del molde a través de una boquilla, llenando el espacio por completo.
- Vivienda:Se aplica presión para garantizar que el plástico fundido llene cada parte de la cavidad del molde, asegurando que el producto coincida con el diseño del molde.
- Enfriamiento:Se deja enfriar el molde, lo que permite que el plástico se solidifique en la forma de la cavidad del molde.
- Apertura del molde:Una vez enfriado, las mitades del molde se abren para revelar la parte solidificada.
- Expulsión:Los pasadores eyectores u otros mecanismos empujan la pieza terminada fuera del molde, lista para cualquier procesamiento o empaquetado adicional.
¿Qué es el núcleo de moldeo por inyección?
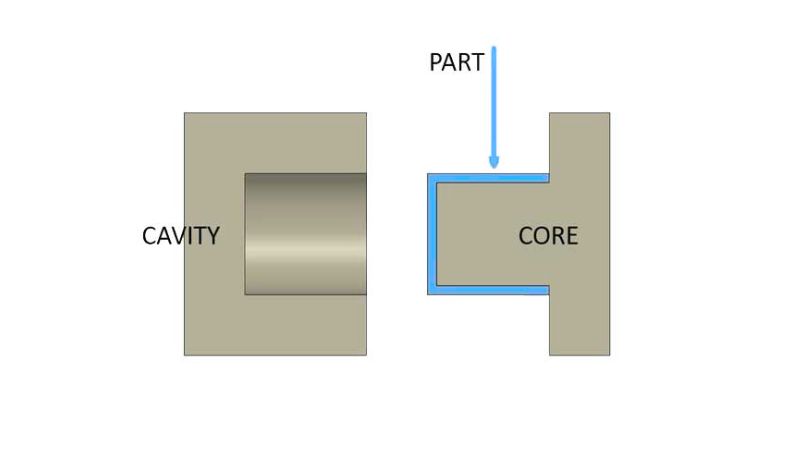
El núcleo de moldeo por inyección es un componente sólido o móvil dentro del molde que forma las características internas o los huecos de la pieza moldeada final. Representa la forma y la geometría de las características internas deseadas de la pieza, como porciones huecas o estructuras internas complejas.
¿Cuál es la diferencia entre cavidad y núcleo en el molde?
Como núcleo, la cavidad es otro componente clave del molde en el moldeo por inyección de plástico, que a menudo se pule hasta obtener un acabado que represente el acabado superficial final deseado de la pieza. Ambos elementos trabajan juntos para dar forma a la pieza moldeada final.
El núcleo da forma a las características internas, mientras que la cavidad da forma a las características externas de la pieza.
El núcleo de moldeo se encuentra en la mitad móvil (lado B), que a menudo participa en el proceso de expulsión, y la cavidad se encuentra en la mitad fija (lado A), mientras que la cavidad participa de forma menos directa.
¿Cómo fabricar el núcleo de moldeo por inyección?
Elegir el material adecuado
Elección de materiales porque el núcleo es imprescindible ya que debe soportar las altas temperaturas y presiones del plástico fundido sin deformarse.
El rendimiento del núcleo afecta directamente no solo a la calidad sino también a la eficiencia del proceso de moldeo por inyección, dando lugar a piezas que cumplen especificaciones estrictas.
- Acero:El acero de alta calidad es una opción popular por su durabilidad y resistencia al desgaste, lo que lo hace ideal para la producción en grandes volúmenes. Incluye tipos como el acero inoxidable, el P20 y el H13.
- Aluminio:El aluminio, conocido por sus propiedades ligeras y de calentamiento y enfriamiento más rápido, se utiliza a menudo para herramientas de prototipos o producción de bajo volumen.
- Aleaciones de berilio y cobre:Se utiliza en áreas del molde que requieren una rápida eliminación de calor o en partes del molde con geometrías intrincadas.
- Acero preendurecido:Una opción rentable que se utiliza en aplicaciones menos exigentes; no requiere tratamiento térmico adicional.
- Acero para herramientas:Para aplicaciones de alto desgaste, se utilizan aceros para herramientas como D2 o A2, que ofrecen robustez y longevidad.
Proceso de fabricación y precisión
Las técnicas de mecanizado avanzadas, como el fresado CNC y el mecanizado por descarga eléctrica (EDM), son fundamentales para lograr los altos niveles de precisión requeridos para los núcleos.
- Fresado CNC:Ofrece precisión a través del mecanizado controlado por computadora.
- Electroerosión:Se utiliza para detalles intrincados y geometrías complejas.
¿Cómo afecta el núcleo del molde a la calidad del producto?
La variabilidad de la calidad del núcleo y del molde en el moldeo por inyección se puede atribuir a varios factores que afectan el rendimiento y la consistencia de las piezas moldeadas:
Causa | Descripción |
Cambio de núcleo | Desalineación del núcleo del molde durante la inyección, lo que genera imprecisiones dimensionales. |
Pega | El núcleo permanece alojado en la pieza durante la expulsión, a menudo debido a ángulos de inclinación insuficientes o a una fricción excesiva. |
Pandeo | Las distorsiones dimensionales son causadas por la deformación del núcleo bajo ciclos de alta temperatura y presión. |
Agrietamiento o rotura | Los daños en el núcleo se deben a tensiones y presiones, a menudo resultantes del uso de materiales menos duraderos. |
Desgaste | La abrasión y la erosión por el uso continuo provocan una disminución de la calidad de la superficie y de la integridad dimensional. |
Problemas de enfriamiento | Un enfriamiento o transmisión de calor ineficiente provoca tiempos de ciclo más largos y posibles deformaciones o cambios dimensionales. |
Problemas de ventilación | Ventilación inadecuada que atrapa aire y gases, lo que genera fallas en la superficie, huecos o llenado incompleto de las piezas. |
Variabilidad de materiales y diseño | Variabilidad en las propiedades del material y complejidad del diseño que afectan la vida útil y el rendimiento del molde. |
Desafíos de mantenimiento | La falta de mantenimiento regular conduce a problemas como corrosión, contaminación o deterioro, lo que afecta el rendimiento del molde y la calidad del producto. |
¿Qué es el ángulo de tiro?
El ángulo de desmoldeo que mencionamos en la sección anterior se refiere a una ligera conicidad aplicada a las superficies verticales de una pieza en el moldeo por inyección. Esta conicidad ayuda a que la pieza se desmolde fácilmente sin causar daños.
Por lo general, se recomienda un ángulo de inclinación de 1 a 2 grados para la mayoría de las piezas, aunque se necesitan más ángulos de inclinación para superficies más profundas o texturizadas.
Existen ángulos de inclinación positivos y negativos. Un ángulo de inclinación positivo significa que el ángulo es mayor que el ángulo de referencia, lo que facilita la liberación de la pieza. Un ángulo de inclinación negativo puede complicar el diseño del molde, ya que puede requerir que el molde se separe en varias partes para retirar la pieza.
¿Cómo elegir la ubicación del núcleo y la cavidad en el moldeo por inyección?
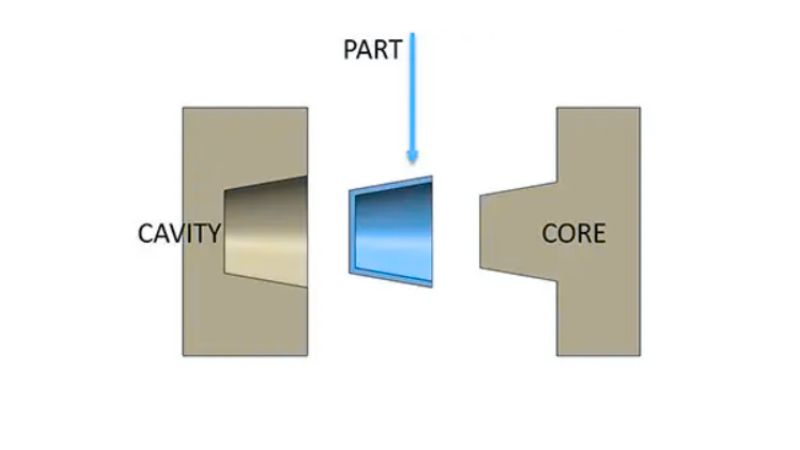
¿Qué afecta la colocación del núcleo y la cavidad?
La colocación del núcleo y la cavidad en el moldeo por inyección está influenciada por varios factores clave:
Diseño de piezas
La complejidad y la geometría de la pieza, incluidas características como orificios y huecos, determinan la ubicación del núcleo y la cavidad. Las características salientes suelen requerir núcleos, mientras que las características hundidas se forman mediante cavidades.
Propiedades del material
La disposición del núcleo y la cavidad en un molde está influenciada por la tasa de contracción del material, las características de flujo y la velocidad de inyección. Si un material tiene una tasa de contracción baja, puede resultar difícil garantizar que la pieza permanezca del lado de los pasadores de expulsión, lo que requiere ajustes de diseño especiales.
Si bien la mayoría de los plásticos se encogen significativamente, es fundamental comprender cómo las propiedades del material pueden afectar la ubicación del núcleo y la cavidad.
Disposición del sistema de eyección
Después de la etapa de enfriamiento, cuando se abre el molde, la pieza inyectada debe permanecer siempre adherida al lado con los pasadores expulsores.
El diseño y la forma del sistema de expulsión influyen en la ubicación del núcleo y la cavidad para garantizar una expulsión consistente y confiable de la pieza.
Simetría y ubicación de la puerta
La colada es el canal principal que lleva el plástico fundido desde la máquina de moldeo por inyección hasta el molde. Normalmente, va directamente al molde, pero a veces puede ir directamente a la cavidad del molde, en cuyo caso se denomina compuerta de colada directa.
Los canales son conductos más pequeños que se ramifican desde la matriz para distribuir el plástico fundido a diferentes partes del molde. Esta configuración permite la producción de varias piezas a la vez, lo que resulta rentable, especialmente para artículos pequeños.
Las compuertas son pequeñas aberturas por donde el plástico ingresa a la cavidad del molde desde los canales. Son más estrechas que los canales y ayudan a controlar el flujo de plástico hacia el molde.