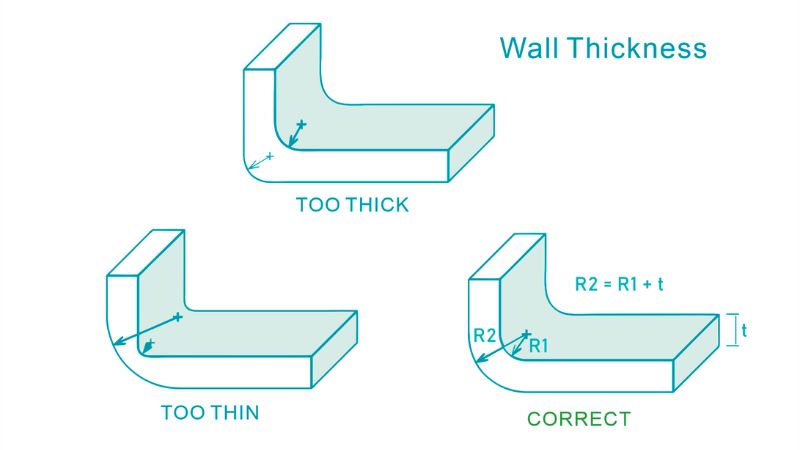
Desde la comprensión de los conceptos básicos del espesor de la pared hasta la navegación por consideraciones específicas del material, esta guía cubre aspectos esenciales que los diseñadores, ingenieros y fabricantes necesitan saber.
Esta guía completa explora la importancia del diseño del espesor de pared adecuado en el moldeo por inyección, ofreciendo información sobre las mejores prácticas, desafíos comunes y soluciones para optimizar la producción de piezas.
¿Qué es el espesor de la pared en el moldeo por inyección?
El espesor de la pared es una consideración de diseño crítica en el proceso de moldeo por inyección, que se refiere al espesor de la sección transversal de la pieza de plástico que se está moldeando.
Es una de las consideraciones de diseño más importantes en el moldeo por inyección porque afecta significativamente la capacidad de fabricación, el costo, la calidad y el rendimiento de la pieza final.
¿Qué influye en el espesor de la pared?
Dos factores clave influyen en el espesor de la pared del material plástico moldeado por inyección y en la estructura de las piezas.
- Tamaño y forma – Las piezas más grandes generalmente requieren paredes más gruesas para lograr integridad estructural, mientras que las piezas más pequeñas pueden tener paredes más delgadas. Las formas complejas pueden necesitar espesores variables.
- Material plástico – – Los distintos plásticos tienen distintas características de flujo y velocidades de enfriamiento. Los materiales con menor viscosidad o mayores velocidades de flujo de fusión generalmente se pueden utilizar con paredes más delgadas.
A continuación te mostramos una tabla para que puedas comprobar el espesor de pared óptimo para distintos materiales:
Material | Rango de espesor de pared recomendado |
abdominales | 0,045 – 0,140 pulgadas (1,14 – 3,56 mm) |
Acetal (POM) | 0,030 – 0,120 pulgadas (0,76 – 3,05 mm) |
Acrílico (PMMA) | 0,025 – 0,500 pulgadas (0,64 – 12,7 mm) |
Nailon (PA) | 0,030 – 0,115 pulgadas (0,76 – 2,92 mm) |
Policarbonato (PC) | 0,040 – 0,150 pulgadas (1,02 – 3,81 mm) |
Polietileno (PE) | 0,030 – 0,200 pulgadas (0,76 – 5,08 mm) |
Polipropileno (PP) | 0,025 – 0,150 pulgadas (0,64 – 3,81 mm) |
Poliestireno (PS) | 0,035 – 0,150 pulgadas (0,89 – 3,81 mm) |
¿Cuáles son los problemas con el espesor de la pared?
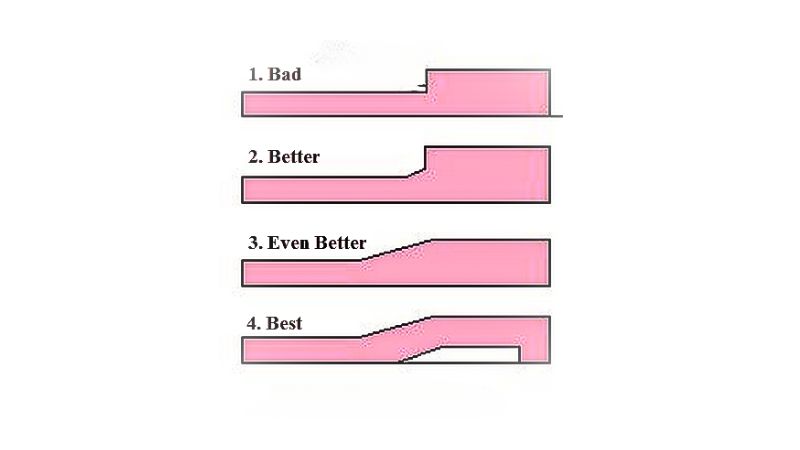
Un espesor de pared incorrecto para el moldeo por inyección puede provocar varios defectos en el producto final:
Defecto | Causa | Resultado |
Deformación | Espesor de pared desigual | Diferentes velocidades de enfriamiento generan tensiones internas que causan deformaciones o torsiones. |
Marcas de hundimiento | Secciones más gruesas | El enfriamiento lento permite que la superficie se hunda hacia adentro, creando pequeñas depresiones. |
Líneas de flujo | Variaciones en el espesor de la pared | Diferentes velocidades de flujo de plástico fundido provocan rayas o líneas visibles en la superficie. |
tiros cortos | Transiciones de fino a grueso | El enfriamiento prematuro impide el llenado completo de las zonas más gruesas. |
Vacíos | Secciones gruesas | Las bolsas de aire o de vacío forman huecos internos |
chorro | Paredes demasiado delgadas | El flujo rápido de plástico provoca patrones similares a serpientes en la superficie de la pieza. |
Debilidad estructural | Espesor de pared inconsistente | Comprometer la resistencia y la integridad de la pieza. |
Inexactitudes dimensionales | Variaciones de espesor | El enfriamiento desigual provoca que las piezas no cumplan con las dimensiones especificadas |
Aumento del estrés interno | Diferentes espesores de pared | Diferentes velocidades de enfriamiento dan como resultado tensiones internas más altas |
Defectos superficiales | Espesor de pared inadecuado | Provoca imperfecciones en la superficie, como ondulaciones o arrugas. |
Consideraciones de diseño para lograr un espesor de pared uniforme
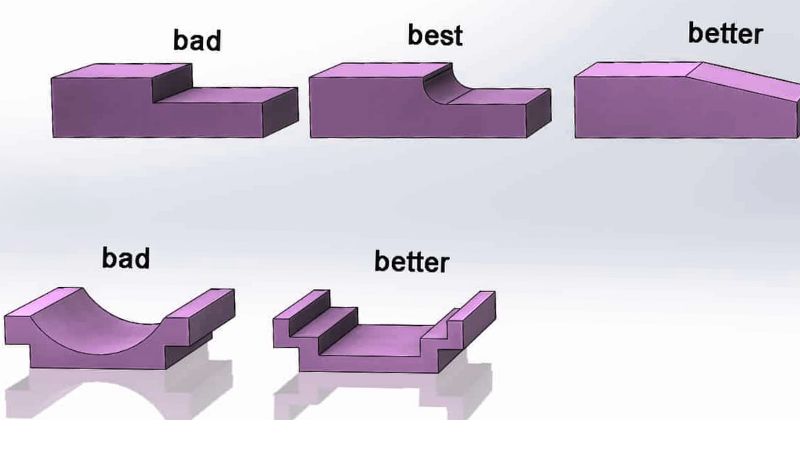
El análisis de diseño para fabricación (DFM) ayuda a identificar el espesor uniforme óptimo para minimizar la tensión interna y mejorar la consistencia.
Utilización de ángulos de inclinación para mejorar el llenado del molde
Los ángulos de desmoldeo son parte integral del diseño de componentes moldeados por inyección, ya que sirven para facilitar la extracción de la pieza terminada del molde. Incorporar un ángulo de desmoldeo no es solo una buena práctica, sino que es fundamental para promover un espesor de pared uniforme.
Un ángulo de inclinación externo recomendado de 0,5 a 1,5 grados y un ángulo interno de 0,5 grados pueden mejorar en gran medida el proceso de llenado del molde.
Estos ligeros ángulos permiten que el material fluya más suavemente y evitan la formación de espesores de pared inconsistentes, que a menudo son la raíz de varios defectos dentro de la pieza.
Cómo abordar las tensiones internas causadas por un espesor de pared no uniforme
Las disparidades en el espesor de las paredes pueden generar tensiones internas en la pieza a medida que se enfría y se solidifica. Las secciones con paredes más gruesas se enfrían a un ritmo más lento, lo que provoca velocidades de contracción diferenciales que pueden deformar o distorsionar la pieza.
Un espesor uniforme en toda la pieza es imprescindible para distribuir uniformemente estas tensiones y evitar posibles problemas de calidad.
Al diseñar piezas, se deben considerar las áreas de alto riesgo y aplicar un espesor de pared consistente para mitigar la formación de tensión interna.
Espesor recomendado – Mínimo
El espesor mínimo de la pared depende del material plástico específico que se utilice y del tamaño/complejidad de la pieza.
En general:
Para piezas pequeñas y una producción eficiente de alto volumen, se recomienda un espesor de pared mínimo de 0,025 a 0,030 pulgadas (0,64 a 0,76 mm).
Para piezas más grandes, se sugiere un mínimo de 0,040 a 0,050 pulgadas (1,0 a 1,3 mm).
El espesor de pared mínimo práctico para el moldeo por inyección convencional varía entre 0,030 y 0,040 pulgadas (0,76 y 1,0 mm).
Algunas aplicaciones especializadas de moldeo de paredes delgadas pueden lograr paredes tan delgadas como 0,010 pulgadas (0,25 mm), pero esto requiere altas presiones y limita el tamaño de la pieza.
Espesor recomendado – Máximo
Siempre que sea posible, se deben evitar paredes excesivamente gruesas en el moldeo por inyección, ya que pueden provocar defectos e ineficiencias.
Las pautas generales son:
La mayoría de las piezas moldeadas por inyección tienen un espesor de pared máximo de 0,125 a 0,250 pulgadas (3,2 a 6,4 mm).
Las paredes con un espesor superior a 0,250 pulgadas (6,4 mm) tienen un mayor riesgo de hundimientos, huecos, tensiones residuales y deformaciones.
En algunas aplicaciones especializadas, son posibles espesores de pared de hasta 4,5 pulgadas (114 mm), pero requieren tiempos de ciclo muy largos.
Como práctica recomendada para la eficiencia y la calidad, se recomienda un espesor de pared máximo de 0,125 a 0,160 pulgadas (3,2 a 4,0 mm) para la mayoría de las piezas.
Cómo solucionar problemas de espesor de pared en piezas moldeadas
Cómo trabajar con secciones de paredes gruesas en piezas moldeadas por inyección
Para mitigar esto, es recomendable mantener un espesor de pared que facilite un enfriamiento rápido pero que también proporcione suficiente resistencia. Por ejemplo, con material PA6 de 8 mm de espesor, el ciclo total de moldeo por inyección es de aproximadamente 93 segundos, y el enfriamiento demora alrededor de 70 segundos.
Para superar el desafío de los tiempos de ciclo prolongados debido a paredes más gruesas, puede resultar beneficioso emplear una técnica conocida como "core out", que implica crear secciones huecas en la pared gruesa sin comprometer la integridad ni la resistencia de la pieza.
Cómo manipular paredes delgadas sin comprometer la integridad de las piezas
Se recomienda a los diseñadores de productos que diseñen piezas con el espesor de pared mínimo necesario sin comprometer la integridad de la pieza.
El diseño de paredes más delgadas requiere una comprensión profunda de las características de flujo del material para evitar defectos.
Factores como la presión de inyección, la temperatura del molde y la inclusión de elementos de diseño como nervaduras o refuerzos pueden ayudar a sostener piezas de paredes delgadas, mejorando su moldeabilidad y reduciendo la posibilidad de deformaciones, hundimientos o burbujas.