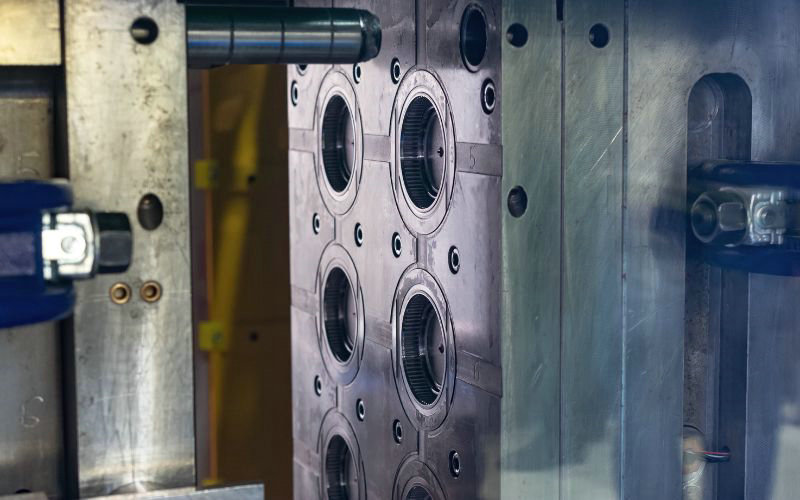
Principales tipos de tecnologías de moldeo por inyección
El moldeo por inyección es uno de los procesos de fabricación más utilizados para producir piezas de plástico de alta calidad en grandes volúmenes. Su versatilidad, eficiencia y capacidad para crear geometrías complejas la convierten en una tecnología esencial en diversas industrias, desde la automoción y la medicina hasta los bienes de consumo y la electrónica.
Sin embargo, no todos los procesos de moldeo por inyección son iguales. A lo largo de los años, han surgido varias tecnologías especializadas de moldeo por inyección para satisfacer requisitos de aplicaciones específicas, como resistencia mejorada, peso reducido o acabado superficial mejorado. Comprender las ventajas y desventajas de cada tipo de moldeo por inyección es crucial para seleccionar el proceso más adecuado para su proyecto.
En esta publicación de blog, exploraremos seis tipos principales de tecnologías de moldeo por inyección: moldeo por inyección asistido por gas, moldeo de paredes delgadas, moldeo por inyección de silicona líquida, moldeo por inyección de metal, impresión 3D y moldeo de espuma estructural. Profundizaremos en los beneficios y aplicaciones de cada proceso, ayudándole a tomar una decisión informada a la hora de elegir la técnica de moldeo por inyección adecuada para su producto.
Entonces, ya sea diseñador, ingeniero o fabricante de productos, únase a nosotros para descubrir el mundo de las tecnologías avanzadas de moldeo por inyección y descubrir cómo pueden revolucionar su proceso de desarrollo de productos.
Moldeo por inyección asistido por gas
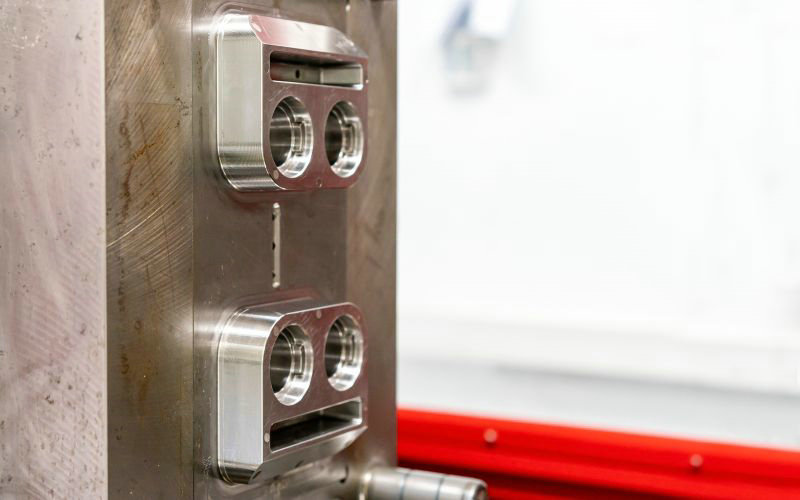
En el moldeo por inyección asistido por gas (GAIM), sus piezas de plástico se benefician de una menor tensión del material y mejores acabados superficiales. Este proceso fusiona el moldeo por inyección tradicional con la asistencia de gas a presión.
Beneficios
- Eficiencia de materiales: Ahorra en costes de material ya que GAIM utiliza menos plástico y mantiene la resistencia.
- Deformación reducida: Sus piezas tienen una deformación mínima debido a presiones internas más uniformes durante el moldeo.
- Diseño mejorado: Puede lograr geometrías complejas y diseños intrincados que quizás no sean posibles con el moldeo por inyección convencional.
- Tiempos de ciclo más rápidos: Disfrute de tiradas de producción más rápidas gracias a los tiempos de enfriamiento reducidos porque las piezas tienen menos plástico.
Aplicaciones
- Componentes automotrices: Los tableros y parachoques de su vehículo son candidatos ideales para que GAIM equilibre la durabilidad y el diseño liviano.
- Bienes de consumo: Los juguetes y electrodomésticos se benefician de las cualidades estéticas y funcionales que aporta GAIM.
- Dispositivos médicos: El proceso es adecuado para fabricar piezas ligeras y resistentes para diversos equipos médicos.
- Muebles: La tecnología también se utiliza para producir componentes de muebles resistentes pero livianos que requieren un buen acabado superficial.
Moldura de pared delgada
El moldeo de paredes delgadas es una forma altamente especializada de moldeo por inyección que se enfoca en producir piezas con dimensiones excepcionalmente delgadas. Este proceso exige un control preciso y velocidades de inyección rápidas.
Beneficios
- Eficiencia: Puede lograr tiempos de ciclo y enfriamiento más rápidos, ofreciendo una mayor eficiencia de producción.
- Ahorro de materiales: Reduce el uso de materiales, lo que reduce los costos y disminuye el impacto ambiental.
- Alto rendimiento: Las piezas producidas son livianas pero conservan una alta resistencia, adecuadas para aplicaciones exigentes.
Aplicaciones
- Electrónica: Ideal para producir piezas delgadas y livianas, como carcasas de teléfonos móviles.
- embalaje: Permite la creación de contenedores duraderos con un uso mínimo de material, como se ve a menudo en envases de alimentos.
- Dispositivos médicos: Ofrece componentes de precisión capaces de soportar estándares estrictos de la industria médica.
Moldeo por inyección de silicona líquida
El moldeo por inyección de silicona líquida es un proceso que se utiliza para crear piezas flexibles y duraderas con alta precisión. Este método implica caucho de alta consistencia que puede lograr tolerancias estrictas y diseños intrincados.
Beneficios
- Consistencia y Calidad: El proceso de moldeo por inyección de silicona líquida ofrece una notable consistencia en los productos fabricados. Esto se debe a la capacidad del material para mantener propiedades mecánicas estables durante toda su vida útil.
- Versatilidad: Las piezas producidas con silicona líquida pueden soportar temperaturas extremas, lo que las hace adecuadas para diversas aplicaciones.
Aplicaciones
- Dispositivos médicos: Encontrará componentes fabricados con moldeo por inyección de silicona líquida en aplicaciones médicas debido a su biocompatibilidad y esterilizabilidad.
- Piezas de automóviles: Debido a su durabilidad y resistencia al calor, la silicona líquida también se usa comúnmente para juntas, válvulas y sellos en la industria automotriz.
Moldeo por inyección de metales
El moldeo por inyección de metal (MIM) es un proceso sofisticado que combina la versatilidad del moldeo por inyección de plástico con la resistencia y la integridad de los metales forjados. Adecuado para la producción en masa de piezas pequeñas e intrincadas, MIM alcanza un nivel de precisión que las técnicas tradicionales de trabajo del metal luchan por alcanzar.
Beneficios
MIM le permite aprovechar varios beneficios:
- Precisión: cree piezas complejas y muy detalladas que son difíciles de producir mediante otros métodos.
- Fortaleza: Las piezas MIM son comparables en resistencia y densidad a las fabricadas con procesos tradicionales de trabajo del metal.
- Rentabilidad: Especialmente para producciones de volumen medio a alto, puede lograr ahorros sustanciales debido a la reducción de desperdicios y requisitos mínimos de acabado.
Aplicaciones
Es posible que su industria ya esté aprovechando MIM:
- Médico: Instrumentos quirúrgicos, aparatos de ortodoncia e implantables.
- Automotor: Componentes del motor, cajas de cambios y carcasas de sensores.
- Electrónica de consumo: Componentes de teléfonos móviles y hardware informático.
Impresión 3d
En el ámbito del moldeo por inyección, la impresión 3D ha surgido como un enfoque transformador, que permite la creación rápida de prototipos y la producción de moldes con geometrías complejas con las que luchan los métodos tradicionales.
Beneficios
- Eficiencia de costo: Encontrará importantes ahorros de costos debido al mínimo desperdicio de material y la eliminación de la necesidad de múltiples procesos de mecanizado. Obtenga más información sobre la rentabilidad en la impresión 3D.
- Velocidad: Los prototipos y moldes se pueden producir mucho más rápido que los métodos tradicionales, a menudo en horas o días, lo que reduce el tiempo total de comercialización.
Aplicaciones
- Creación de prototipos: La impresión 3D destaca por crear rápidamente prototipos detallados para probar la forma, el ajuste y la función.
- Producción: Aunque es menos común, es posible producir piezas finales con calidad de producción, especialmente para tiradas cortas donde construir un molde tradicional puede no ser rentable. También se utiliza para realizar diseños de moldes complejos que son difíciles de lograr con fresado CNC.
Moldura de espuma estructural
Cuando explora el moldeado de espuma estructural, está analizando un proceso distinto que crea piezas con un núcleo celular. Esto se logra integrando un agente espumante físico o químico dentro del material plástico. Como resultado, los productos fabricados mediante este método tienden a ser más robustos y livianos.
Beneficios
- Relación fuerza-peso mejorada: El núcleo celular único, característico de las piezas moldeadas de espuma estructural, proporciona una relación resistencia-peso superior. Esto hace que estas piezas sean ideales para aplicaciones que requieren un rendimiento sólido sin el peso de los plásticos sólidos.
- Uso reducido de materiales: Con el moldeado de espuma estructural, puede lograr las mismas dimensiones generales de la pieza utilizando menos material, gracias a la acción de la espuma, que crea una estructura celular dentro del componente y reduce la densidad.
- Flexibilidad de diseño: Este tipo de moldeado permite geometrías y diseños complejos que pueden resultar desafiantes o imposibles de crear con el moldeo por inyección tradicional. Al utilizar molduras de espuma estructural, los diseñadores tienen mayor libertad en los ángulos de inclinación y el espesor de las paredes.
- Estabilidad de alta dimensión: Debido al entorno de baja presión en el que opera el proceso de moldeo, hay menos tensión en las piezas, lo que genera una mayor estabilidad dimensional y una calidad superior de las piezas.
Aplicaciones
- Aeroespacial: La espuma estructural se utiliza para componentes interiores de aeronaves y aviones, piezas de satélites y grandes recintos de aviación debido a su alta relación resistencia-peso.
- Transporte: El proceso es ideal para producir piezas grandes y livianas, como componentes de vehículos comerciales, parachoques de vehículos todo terreno y estructuras de robots autónomos.
- Equipo industrial: La espuma estructural se utiliza para carros de basura y reciclaje, carcasas de equipos agrícolas, tarimas reutilizables, cubiertas para lavadoras de pisos comerciales y recintos para cajeros automáticos debido a su durabilidad y resistencia al impacto.
- Dispositivos médicos: La tecnología se emplea para bandejas de carros móviles, bases, revestimientos, manijas, paneles y puertas de equipos de resonancia magnética y rayos X, recintos de equipos de laboratorio de diagnóstico y brazos quirúrgicos debido a su resistencia y moldeabilidad.
- Productos de consumo: El moldeado de espuma estructural crea piezas grandes y rígidas para vehículos recreativos, productos de consumo para exteriores como bandejas para parrilla y carretillas, y recintos para altavoces.
- Construcción: Los paneles grandes, carros y otros componentes de construcción se benefician de la capacidad de la espuma estructural para producir piezas livianas y de tamaño considerable.
Técnicas avanzadas y tendencias futuras
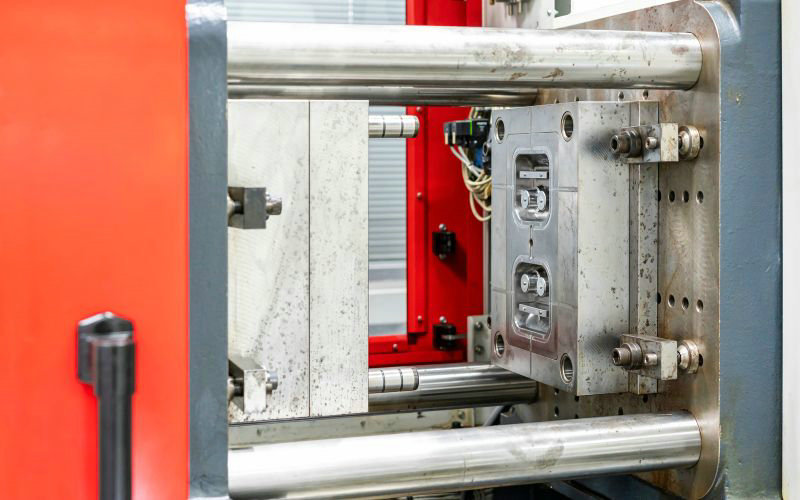
A medida que navega por el mundo del moldeo por inyección, en rápida evolución, descubrirá que el moldeo por inyección convencional ha allanado el camino para técnicas más innovadoras. Uno de esos avances es el moldeo por inserción, donde componentes como piezas metálicas se encapsulan dentro del plástico durante el moldeo, lo que ofrece mayor resistencia y función a sus productos.
La incorporación de la impresión 3D al moldeo por inyección ha revolucionado el desarrollo de prototipos, permitiendo un diseño detallado y flexible antes de la producción en masa. Esto puede reducir significativamente las consideraciones de costos, ya que le permite perfeccionar diseños sin herramientas costosas para tiradas cortas.
Adopte la automatización para aumentar la eficiencia y mantener un alto nivel de precisión. Los sistemas automatizados gestionan tareas desde el manejo de materias primas hasta el funcionamiento de la maquinaria de moldeo, lo que puede impactar positivamente el volumen y la consistencia de la producción.
Aquí hay una instantánea de las tendencias actuales:
- Impresión 3d: Creación rápida de prototipos y geometrías complejas
- Automatización: Consistencia y velocidad en la producción
- Consideraciones de costos: Reducción de residuos, uso optimizado de recursos
Para una gestión eficaz de la temperatura durante el moldeado, los diseñadores están innovando con canales de refrigeración que permiten que las piezas moldeadas se enfríen de forma más rápida y uniforme. Esto acelera la producción y mejora la cristalinidad de materiales como el poliestireno (PS).
La fuerza de sujeción juega un papel fundamental en el cierre del molde y la calidad de la pieza. Las máquinas modernas ofrecen un mayor control, optimizando esta fuerza en función del molde y material específicos, mejorando aún más las capacidades de los métodos de posprocesamiento para refinar y terminar sus productos.
En el dinámico campo del moldeo por inyección, estas tendencias emergentes prometen perfeccionar su proceso de producción y elevar la calidad de sus resultados. Abrácelos para mantenerse a la vanguardia de la industria.