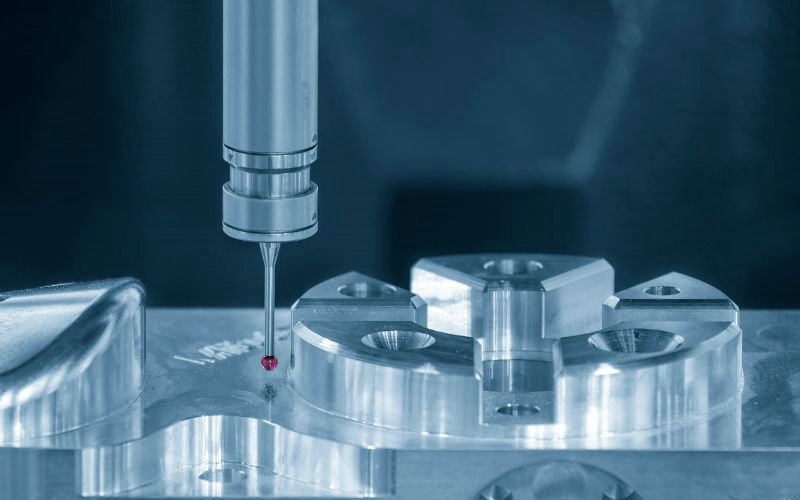
El moldeo por inyección es uno de los procesos de fabricación más utilizados para producir grandes volúmenes de piezas de plástico. Para garantizar una calidad constante de las piezas y una eficiencia de producción óptima, temperatura del molde es uno de los factores más críticos a controlar. La temperatura del molde tiene un impacto significativo en el comportamiento de flujo del plástico fundido durante el llenado y en la velocidad de enfriamiento de la pieza. Si el molde está demasiado frío, la masa fundida tendrá dificultades para llenar la cavidad por completo, lo que provocará disparos cortos u otros defectos. Por el contrario, si el molde está demasiado caliente, el plástico tardará más en solidificarse, lo que aumentará los tiempos del ciclo. En esta publicación, lo ayudaremos a obtener una visión más profunda de cómo la temperatura afecta el moldeo por inyección y medidas específicas para controlar mejor la temperatura del molde.
Explicación de los sistemas de control de temperatura del molde.
Componentes de un sistema de control de temperatura del molde
Un sistema de control de temperatura del molde consta de varios componentes clave que funcionan juntos:
- Sistema de control electrónico: procesa información de otros sistemas y emite comandos.
- Sistema mecánico (bomba de circulación): entrega calor desde el sistema de calefacción al molde.
- Sistema de monitoreo de nivel de líquido: monitorea los niveles de refrigerante y envía señales para recargas
- Sistema de calefacción: calienta el refrigerante a la temperatura establecida.
- Sistema de refrigeración: elimina el exceso de calor, a menudo utilizando intercambiadores de calor de placas para refrigeración indirecta.
- Sistema de detección de temperatura: Mide la temperatura del molde y transmite datos al sistema de control.
- Sistema de seguridad de alivio de presión: agota y alivia la presión si sube demasiado
Tipos de controladores de temperatura del molde
Hay dos tipos principales de controladores de temperatura del molde según el medio de calentamiento utilizado:
1. Controladores de temperatura del agua
– Rango de temperatura generalmente dentro de 180°C
– Tipo ordinario: hasta 120°C, tipo de alta temperatura: hasta 180°C
2. Controladores de temperatura del aceite
– Utilizado para temperaturas superiores a 180°C, hasta 350°C
– Tipo ordinario: hasta 200°C, tipo de alta temperatura: hasta 350°C
Principio de funcionamiento
A continuación se ofrece una explicación simplificada de cómo funciona un controlador de temperatura de molde tipo agua:
1. La bomba de circulación empuja agua a través del sistema.
2. El sistema de calefacción calienta el agua a la temperatura establecida.
3. El agua caliente fluye a través de los canales del molde, transfiriendo calor.
4. El sistema de detección de temperatura mide la temperatura del molde.
5. Si la temperatura es demasiado baja, el sistema de control le indica al calentador que se encienda.
6. Si la temperatura es demasiado alta, el sistema de enfriamiento elimina el exceso de calor.
7. El sistema de alivio de presión agota el refrigerante si la presión aumenta peligrosamente.
Al controlar con precisión la temperatura del molde, estos sistemas ayudan a minimizar los defectos, optimizar los tiempos de los ciclos y mejorar la calidad general y la consistencia de las piezas en el moldeo por inyección. Invertir en un buen sistema de control de temperatura del molde adaptado a sus requisitos de moldeo específicos puede generar importantes ganancias en la eficiencia de fabricación.
Impacto de la temperatura del molde en el moldeo por inyección
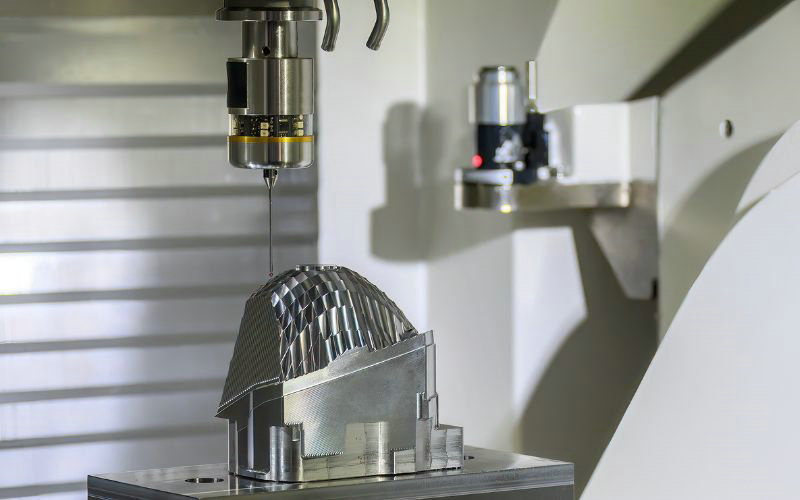
Efectos de la baja temperatura del molde
1. Mala apariencia y acabado de la superficie.
- Una temperatura baja del molde reduce la fluidez del plástico fundido, lo que puede provocar un llenado incompleto y un acabado superficial menos brillante, especialmente para materiales como el ABS.
- Si la temperatura del molde es demasiado baja para superficies texturizadas, es posible que la masa fundida no llene completamente los detalles finos de la textura, lo que provocará una mala replicación de la superficie del molde.
2. Aumento de las tensiones internas y la deformación.
- Una temperatura baja del molde provoca un rápido enfriamiento y "congelación" de las moléculas, lo que genera tensiones internas en la pieza.
- El enfriamiento y la contracción desiguales debido a las bajas temperaturas del molde pueden provocar deformaciones e inestabilidad dimensional de la pieza moldeada.
- Se pueden formar líneas de soldadura visibles en la superficie de la pieza, lo que reduce su resistencia.
3. Cambios en las propiedades mecánicas.
- Las bajas temperaturas del molde pueden reducir la resistencia a la tracción de la pieza moldeada en comparación con temperaturas más altas del molde.
- El enfriamiento rápido a bajas temperaturas puede aumentar la fragilidad de la pieza y reducir su resistencia al impacto y a la fatiga.
4. Tiempos de ciclo más largos
- Aunque las bajas temperaturas del molde pueden reducir el tiempo de enfriamiento, requieren presiones de inyección más altas para llenar la cavidad debido a la reducción de la fluidez del fundido.
- Esto puede aumentar el tiempo total del ciclo, especialmente para materiales cristalinos que requieren suficiente enfriamiento para la estabilidad dimensional.
Efectos de la alta temperatura del molde
1. Acabado y apariencia superficial mejorados
- Una temperatura más alta del molde permite que el plástico fluya más fácilmente y rellene los detalles finos de la superficie, lo que da como resultado un acabado superficial más brillante y atractivo, especialmente para materiales como el ABS.
- La composición plástica está más cerca de la superficie del molde a temperaturas más altas, lo que conduce a una mejor replicación de la textura.
2. Propiedades mecánicas mejoradas
- Las temperaturas más altas del molde pueden mejorar la resistencia a la tracción de la pieza moldeada en comparación con temperaturas más bajas del molde.
- Para los plásticos cristalinos, una temperatura alta del molde permite más tiempo para la cristalización, lo que aumenta la rigidez y la resistencia al calor de la pieza.
3. Reducción de tensiones internas y deformaciones.
- Las altas temperaturas del molde ralentizan el proceso de enfriamiento, lo que permite que las moléculas se relajen y se orienten de manera más uniforme, reduciendo las tensiones residuales en la pieza.
- Un enfriamiento más gradual a temperaturas más altas del molde minimiza la contracción diferencial y la deformación de la pieza moldeada.
4. Mayores tiempos de ciclo y potencial de defectos.
- El principal inconveniente de las altas temperaturas del molde es el mayor tiempo de enfriamiento requerido, lo que aumenta el tiempo total del ciclo y reduce la productividad.
- Las temperaturas excesivamente altas pueden hacer que el plástico se adhiera al molde, creando puntos brillantes u otros defectos en la superficie.
- Existe un mayor riesgo de que se formen rebabas y rebabas si la temperatura del molde es demasiado alta, ya que el plástico permanece fundido por más tiempo.
5. Posible degradación de las propiedades del material.
- Algunos polímeros pueden experimentar degradación térmica u oxidación si se procesan a temperaturas de molde excesivamente altas, lo que lleva a una reducción del peso molecular y de las propiedades mecánicas.
- La combinación de alta temperatura del molde, alta temperatura de fusión y un largo tiempo de residencia plantea el mayor riesgo de degradación del material durante el moldeo.
Medidas para controlar mejor la temperatura del molde
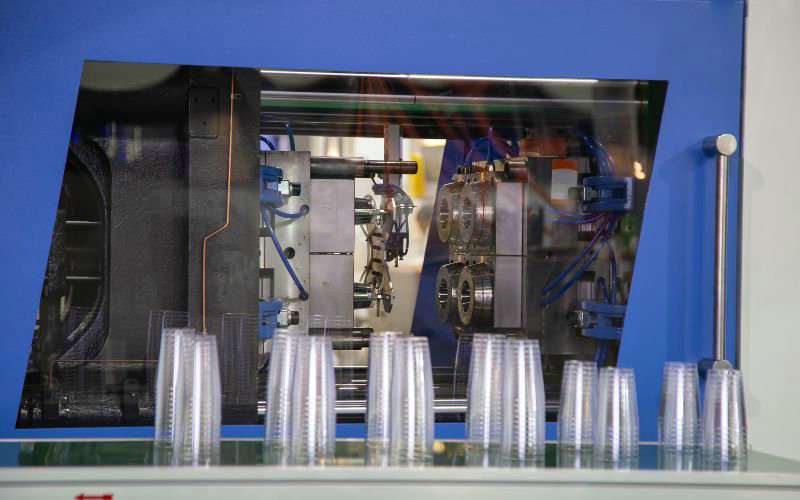
1. Utilice controladores de temperatura del molde
- Los controladores de temperatura del molde son dispositivos esenciales que regulan y mantienen temperaturas precisas del molde. Funcionan tanto para calefacción como para refrigeración.
- Seleccione un controlador de temperatura del molde con suficientes capacidades de caudal y presión para satisfacer las necesidades de su molde específico.
2. Monitorear los caudales de refrigerante
- Un caudal de refrigerante adecuado es fundamental, ya que determina la rapidez con la que se puede enfriar el molde, lo que influye tanto en la calidad del producto como en el tiempo del ciclo.
- Compruebe que el caudal no sea ni demasiado bajo, lo que puede provocar un control deficiente de la temperatura, ni demasiado alto, lo que puede suponer un desperdicio y una ineficiencia.
3. Establecer control del gradiente de temperatura
- Mantenga una temperatura constante en todo el molde para evitar defectos. Un control adecuado del gradiente de temperatura minimiza las tensiones internas dentro de la pieza moldeada.
- Los diseñadores de moldes deben esforzarse por lograr una diferencia de temperatura de no más de 5°C entre el núcleo y la cavidad para reducir la deformación.
4. Optimice el diseño del canal de enfriamiento
- La ubicación, la profundidad y la inclinación de los canales de enfriamiento afectan significativamente la uniformidad de la temperatura de la superficie del molde.
- Apunte a una temperatura uniforme de la superficie del molde optimizando la profundidad del canal de enfriamiento (idealmente entre 1 y 2,5 veces el diámetro del canal) y el paso (entre 2,5 y 3 veces el diámetro del canal).
5. Seleccione los materiales de molde adecuados
- El material del molde tiene un profundo impacto en el intercambio de calor. Considere la conductividad térmica al seleccionar materiales para el molde.
- Para aplicaciones de alta tolerancia, pueden ser necesarias aleaciones de cobre para mantener un diferencial de baja temperatura y reducir la deformación, mientras que se pueden usar materiales menos costosos como el acero H13 para piezas de menor tolerancia.
6. Implementar técnicas rápidas de calentamiento y enfriamiento
- El moldeo por ciclo de calor rápido (RHCM) implica calentar rápidamente el molde por encima del punto de fusión para facilitar el flujo del plástico y luego enfriarlo rápidamente para acelerar la solidificación.
- RHCM puede mejorar la calidad y la precisión de la superficie, pero consume mucha energía y debe reservarse para aplicaciones especiales.
Al implementar estas medidas y monitorear continuamente el rendimiento de la temperatura del molde, los moldeadores por inyección pueden lograr un control más estricto sobre este parámetro crítico del proceso. Esto conduce a una mejor calidad de las piezas, una reducción de los defectos y tiempos de ciclo optimizados para una mayor eficiencia de fabricación.
Temperatura de moldeo por inyección para diferentes plásticos
La siguiente tabla resume las temperaturas de moldeo por inyección recomendadas para diferentes plásticos:
Tipo de plástico | Material | Temperatura de fusión (°C) | Temperatura del molde (°C) |
---|---|---|---|
Plásticos amorfos | abdominales | 210-275 | 50-90 |
PD | 170-280 | 10-60 | |
PMMA | 180-260 | 50-80 | |
ordenador personal | 280-320 | 80-120 | |
Plásticos semicristalinos | PÁGINAS | 200-280 | 30-80 |
PEAD | 210-300 | 20-70 | |
PEBD | 160-260 | 20-70 | |
POM | 160-280 | 50-120 | |
PA6 | 230-290 | 40-120 | |
PA66 | 260-300 | 40-120 | |
PBT | 240-275 | 60-100 | |
Plásticos de alta temperatura | PES | 330-380 | 120-180 |
OJEADA | 340-390 | 120-160 |
Nota: El rango de temperatura de moldeo óptimo depende del grado específico, los aditivos, la geometría de la pieza, el equilibrio deseado de propiedades y el tiempo del ciclo. El control cuidadoso de la temperatura del molde y de la masa fundida es fundamental para lograr una alta calidad de las piezas y eficiencia de fabricación en el moldeo por inyección.