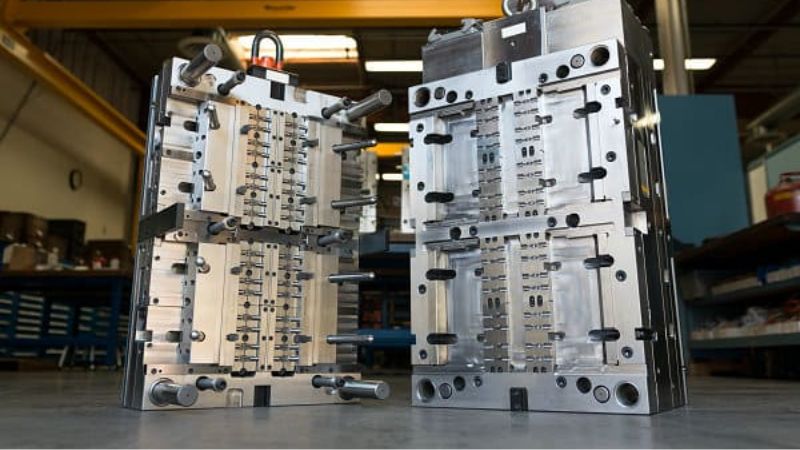
While both blow molding and injection molding serve the fundamental purpose of shaping plastic materials, they operate through distinct mechanisms and are suited to different applications.
Understanding the key differences between blow molding and injection molding is crucial for manufacturers aiming to optimize their production processes and achieve desired outcomes.
This article explores the unique characteristics, advantages, and ideal use cases of each method, providing a comprehensive comparison to guide informed decision-making in the manufacturing landscape.
What is Injection Molding
Plastic Injection molding is a molding process that involves injecting molten plastic into a detailed mold and then letting it cool and harden. It’s perfect for producing precise and complex solid parts, making it ideal for automotive components and medical devices.
What are the Types of Injection Molding
- Thermoplastic Injection Molding: This is the most common form of injection molding, and thermoplastics can be heated, melted, and reshaped multiple times without significant degradation.
- Thermoset Injection Molding: In contrast to thermoplastics, thermosetting plastics undergo a chemical change during the curing (heating) process, making them hard and irreversible. Once set, these materials cannot be melted again, making thermoset products more heat-resistant and durable.
- Metal Injection Molding (MIM): Metal injection molding (MIM) creates small, complex metal components. In this process, fine metal powders are mixed with a binder material to create a feedstock, which is then injected into a mold. After molding, a sintering process removes the binder and fuses the metal powders into a solid part.
- Liquid Silicone Rubber Injection Molding (LSR): Liquid Silicone Rubber (LSR) injection molding is a process designed for silicone parts. This process excels in producing flexible, elastic parts that can withstand extreme temperatures, making them ideal for medical applications, kitchen tools, and industrial seals.
- Gas-Assisted Injection Molding: In gas-assisted injection molding, gas (usually nitrogen) is injected into the molten plastic inside the mold, reducing the amount of material required and creating hollow sections within the molded part. This technique reduces material usage and allows for lighter, structurally sound products.
- Reaction Injection Molding (RIM): Used primarily for polyurethane and other thermosetting polymers, Reaction Injection Molding (RIM) involves mixing two liquid components that chemically react inside the mold to form the final solid part. This process is ideal for making lightweight and strong parts with varying thicknesses.
What is Blow Molding
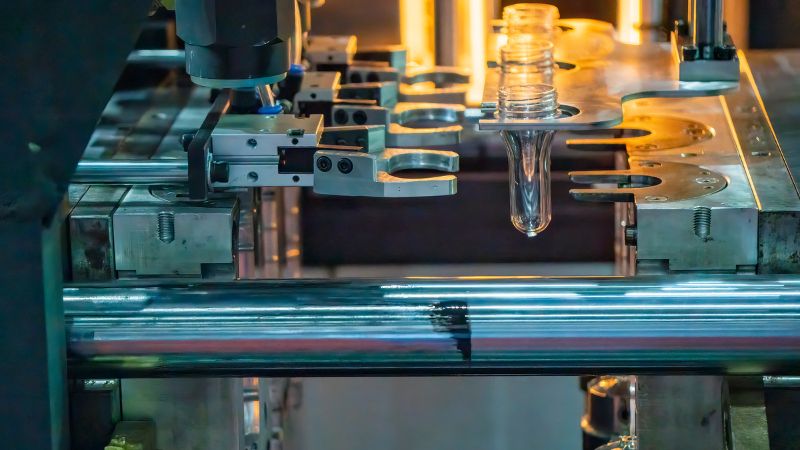
Blow molding starts by forming a hollow tube of plastic called a parison. Compressed air then expands this tube into the shape of the mold. This manufacturing process is mainly used for items like bottles and containers because of its ability to create uniform, hollow products quickly.
What are the Types of Blow Molding
- Extrusion Blow Molding (EBM): Extrusion blow molding is the simplest and most common form of blow molding. In this process, a molten tube of plastic (parison) is extruded downward vertically into an open mold. Once the mold closes around the parison, compressed air is blown into the tube, expanding the plastic to conform to the mold’s shape.
- Injection Blow Molding (IBM): Injection blow molding combines injection molding and blow molding to create highly precise and uniform hollow parts. The process starts with injection molding a preform or parison in the shape of a test tube. This preform is then transferred to a blow molding station, where it is reheated and blown into its final shape.
- Stretch Blow Molding (SBM): Stretch blow molding is often used to produce lightweight, clear, and strong plastic bottles, such as those used for beverages. The material is first injection molded into a preform. The preform is then reheated and stretched axially and radially while air is blown into it. The stretching process aligns the polymer chains, improving the strength and clarity of the final product.
- Co-Extrusion Blow Molding: Co-extrusion blow molding is a variation of extrusion blow molding that allows for the extrusion of multiple layers of plastic material at the same time. This helps achieve specific properties such as improved barrier performance, strength, or appearance by combining different materials into the same part.
- Injection Stretch Blow Molding (ISBM): An advanced version of stretch blow molding, Injection Stretch Blow Molding (ISBM) is a two-step process. It begins with injection molding, where a preform is created in precise dimensions. The preform is then transferred to a blow-molding machine where it is stretched and blown in a single operation. The stretching orientation maximizes material strength and clarity.
- Continuous Blow Molding: Continuous blow molding involves the continuous extrusion of the parison (plastic tube) as parts are ejected from the mold. This is often used for high-output operations where production is ongoing, and the molds are cycled rapidly to meet fast production needs.
Key Differences Between Injection Molding and Blow Molding
Materials and Applications
In injection molding, materials like thermoplastics and elastomers are commonly used. These materials can withstand high pressure and heat, creating solid items.
For blow molding, popular materials include polyethylene, especially HDPE, and polyvinyl chloride (PVC). HDPE is widely used for its strength and durability, while PVC offers flexibility. Blow molding is often used in consumer goods production.
Mold Design and Complexity
In injection molding, molds are crafted from steel or aluminum. The mold has one or more cavities shaped like the product you want. The melted plastic is pressed into these cavities.
Blow molding, including extrusion and injection blow molding, also uses molds. These molds can be simpler, especially in extrusion blow molding. The mold shapes a hollow part by expanding a heated plastic parison using air. Stretch blow molding needs a more complex mold for precise dimensions that is suitable for making clear bottles.
Tooling costs are usually higher for injection molding because of the detailed mold design.
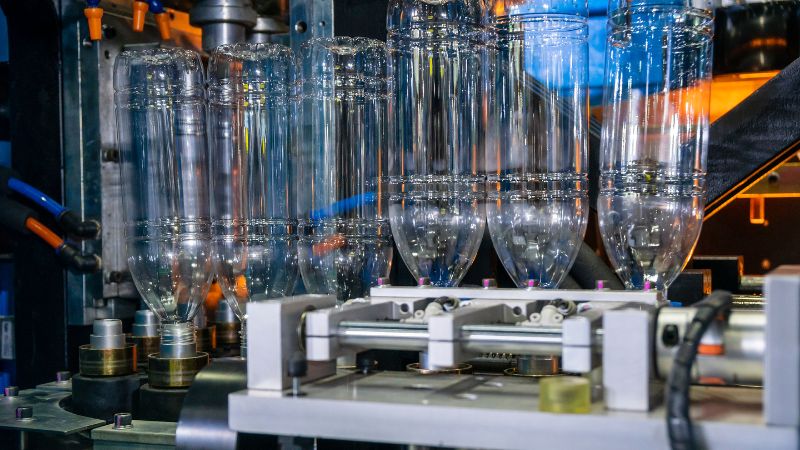
Production Equipment Types
The injection molding machine features an injection unit and a mold clamping unit. The injection unit melts the plastic and forces it into the mold. These machines need high pressure but allow for high precision, making them excellent for complex plastic parts.
There are several types of blow molding, such as extrusion blow molding and injection blow molding. Extrusion blow molding machines create a tube (parison) and then form it with air pressure. Stretch blow molding uses a heated preform, stretched into shape. These machines are less complex, often leading to lower costs for simple plastic products.
Production Volume and Efficiency
Injection molding is perfect for large-scale production. If high-volume production is what you’re aiming for, this technique can meet your needs with ease. It’s known for its ability to pump out thousands of identical pieces in a short time.
Blow molding is also efficient, especially for making hollow items like bottles. Cost can be lower for high-volume tasks because of simpler tooling. Plus, blow molding excels in producing large quantities quickly without much waste.
Production efficiency is a key factor in both methods. Injection molding often has a higher upfront cost due to complex molds, but that pays off in speed and volume. Blow molding, with its simpler setup, might be more cost-effective for less intricate shapes. Choosing the right method impacts your manufacturing efficiency in a big way.
Repeatability and Precision
Injection molding offers high repeatability, meaning you get the same result each time. For products with intricate designs or small parts, it provides the accuracy you need. Every detail is captured, making it ideal for complex components.
Blow molding, on the other hand, might not reach the same level of precision. It’s better suited for simpler shapes where extreme detail isn’t necessary. However, it does ensure good repeatability for hollow and larger items.
Cost Considerations
Injection molding usually has high initial setup costs. Molds and machines for this process can be expensive. However, once set up, injection molding is cost-effective for producing large quantities. This means that for high-volume runs, you might save money over time.
Blow molding, on the other hand, often involves lower initial costs. The tooling is generally less expensive, and this process can be more affordable for smaller production runs. Keep in mind, though, that blow molding may not be as efficient for very large volumes as injection molding.
Design and Complexity
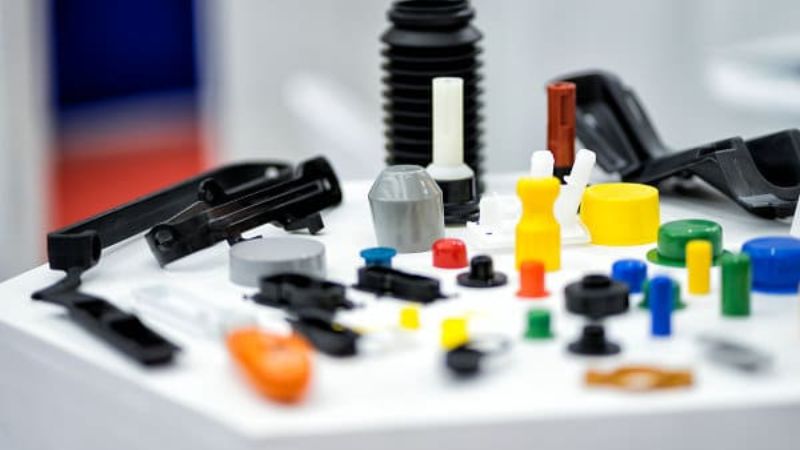
Injection molding offers incredible design flexibility. You can create complex shapes and detailed designs with high precision. This makes it ideal for parts requiring intricate details and tight tolerances. You can produce components with multiple features in a single process, which can be a significant advantage if your parts need such complexity.
Blow molding is excellent for hollow, one-piece objects like bottles and containers. While it doesn’t support the same level of complex designs as injection molding, it excels at producing uniform, strong, and lightweight items. If your product design isn’t too intricate, blow molding might be the way.
Here is a table provides a quick comparison of the key aspects of blow molding and injection molding, highlighting their differences in process, applications, and capabilities. You can have a quick check.
Aspect | Injection Molding | Blow Molding |
Product Type | Solid plastic parts | Hollow plastic parts |
Typical Products | Handles, housings, toys, intricate components | Bottles, containers, tanks |
Process | Melted plastic injected into mold under high pressure | Plastic parison inflated with air in the mold |
Complexity | Can produce complex, detailed parts | Generally simpler designs |
Wall Thickness | Precise control, uniform thickness | Variable thickness, less precise |
Material Usage | Generally uses more material | Uses less material, produces lighter parts |
Tooling Cost | Higher, due to complex molds and high pressure requirements | Lower, simpler mold design |
Production Speed | Fast for small parts | Fast for large hollow plastic parts |
Precision | High precision and tight tolerances | Lower precision, especially for wall thickness |
Material Options | Wide range of materials, including engineering plastics | More limited, mainly thermoplastics |
Applications | Automotive, electronics, consumer goods | Packaging, containers, large hollow products |
Volume Production | Ideal for high-volume production of small parts | Suitable for high-volume production of hollow parts |
Design Flexibility | Highly flexible for solid parts | Limited to hollow designs |
Quality Control | Fewer issues with proper mold design | May face issues like wall thinning, air leaks |
Cost Efficiency | Injection molding cost is higher, efficient for large volumes | Lower initial costs, efficient for hollow parts |