Какво е повърхностно покритие при леене под налягане?
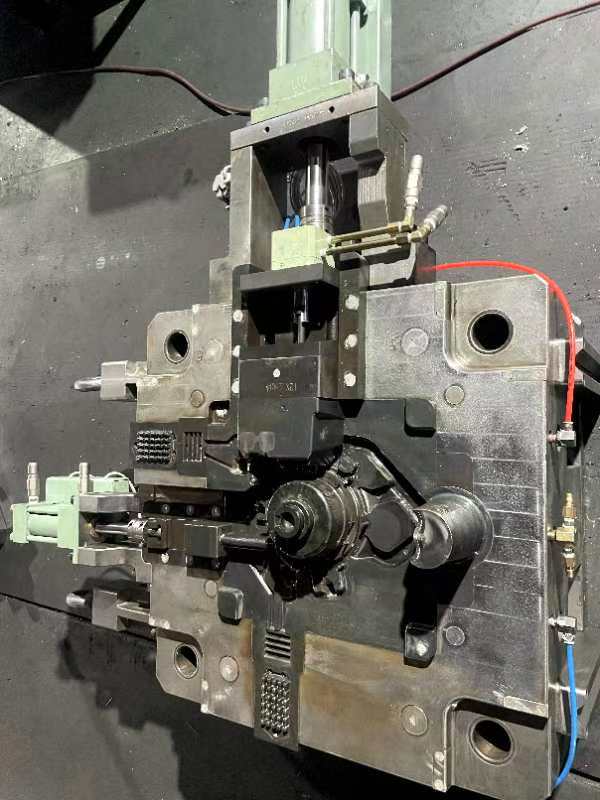
В областта на процеса на леене под налягане избраното повърхностно покритие може значително да повлияе както на външния вид, така и на функционалността на крайния продукт.
Определение за повърхностно покритие
А повърхностно покритие се отнася до текстурата на повърхността на част, която е била произведена чрез леене под налягане. Той включва нивото на гланц, грапавост и модел, придаден на повърхността на формованата част. Това покритие се определя от качеството на самата форма, както и от материалите, използвани в процеса на леене под налягане. Могат да бъдат постигнати различни повърхностни покрития, включително матови, текстурирани или силно лъскави покрития, които се постигат чрез различни процеси след формоване, като полиране или нанасяне на текстури върху формата преди производството.
Значение на повърхностното покритие при леене под налягане
Повърхностното покритие при леене под налягане е от първостепенно значение, тъй като влияе пряко върху външен вид и функционалност на частта.
Значение за визуалната привлекателност
- Гладко, лъскаво покритие (класове SPI A) осигурява висок клас, полиран вид, подходящ за козметични части, лещи и др.
- Полугланцовите (SPI B класове) и матовите (SPI C класове) покрития могат да скрият несъвършенства като линии на потока, заваръчни линии и следи от инструменти, за да подобрят външния вид.
- Текстурираните покрития (степени SPI D) предлагат уникални естетически опции като кожено зърно, дърво, геометрични шарки и др.
Значение за функционалността
- Текстурираните покрития могат да осигурят подобрено сцепление и устойчивост на приплъзване за продукти като преносими устройства, волани и др.
- Специфичните покрития могат да подобрят адхезията на боята и етикета върху повърхността на формованата част.
- Текстурирането позволява на газовете да излизат от матрицата и може да се използва за създаване на подрязвания.
- Грапавостта на повърхността влияе върху триенето и устойчивостта на износване, което може да е важно за механичните части.
Как се прилагат стандартите за повърхностно покритие SPI, VDI и Mold-tech?
Стандартите за повърхностно покритие като SPI и VDI определят козметичното качество и функционалността на формованите части, като определят параметрите за блясък, текстура и грапавост. Тези стандарти гарантират, че повърхностите отговарят на предварително определени критерии, които са от решаващо значение за производителността и естетическата привлекателност на продукта.
Преглед на стандартите за покритие на формите SPI
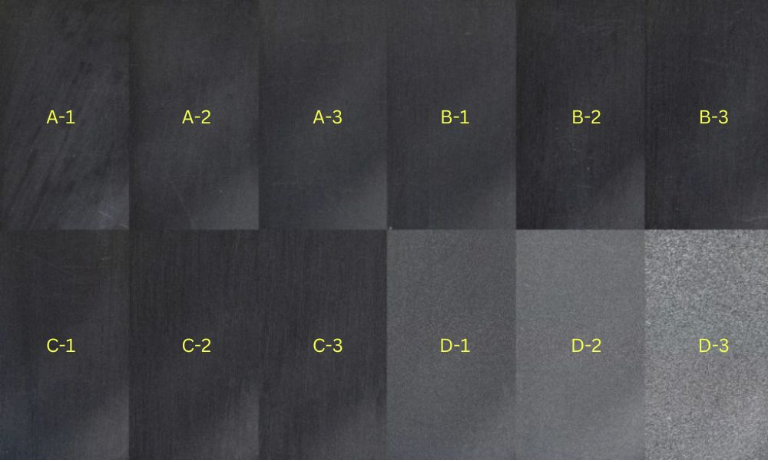
The Общество на пластмасовата индустрия (SPI) създаде класификационна система за повърхностни покрития на шприцформи. Тази система категоризира покритията в гланц (A), полугланц (B), матово (C), и текстурирани (D) степени, всяка с определени нива на гланц и грапавост:
- SPI A е върхът, осигуряващ силно полирани, лъскави покрития. Често включва трудоемко използване на диамантено полиране, подходящо за части, където първокласният вид е от първостепенно значение.
- SPI B предлага полугланцови покрития, постигнати чрез шлайфане с по-фини зърна и по-малко интензивно полиране. Тези покрития са баланс между естетическа привлекателност и рентабилност.
- SPI C отразява стандартно матово покритие, обикновено произведено с каменни абразиви.
- SPI D създава най-текстурираните, нелъскави повърхности, подходящи за части, където се изисква сцепление или неотражателни свойства.
В този спектър точните стойности на грапавостта се придават на повърхността на матрицата, като се гарантира, че частта поддържа планирания външен вид.
SPI стандарт | Завършване (клас) | Завършване (тип) | Метод на довършителни работи | Типична грапавост на повърхността (Ra µm) |
А-1 | Гланциран | Супер висок гланц | Степен #3, 6000 зърно Diamond Buff | 0,012 до 0,025 |
А-2 | Гланциран | Висок гланц | Клас #6, 3000 грит диамантен баф | 0,025 до 0,05 |
А-3 | Гланциран | Нормален лъскав | Степен #15, 1200 зърно Diamond Buff | 0,05 до 0,10 |
Б-1 | Полу-гланц | Фин полугланц | 600 зърнеста хартия | 0,05 до 0,10 |
Б-2 | Полу-гланц | Средно полугланц | 400 зърнеста хартия | 0,10 до 0,15 |
Б-3 | Полу-гланц | Нормален полугланц | 320 зърнеста хартия | 0,28 до 0,32 |
С-1 | Матово | Фин мат | 600 песъчинки | 0,35 до 0,40 |
С-2 | Матово | Средно матово | 400 песъчинки | 0,45 до 0,55 |
С-3 | Матово | Нормално матово | 320 песъчинки | 0,63 до 0,70 |
D-1 | Текстуриран | Сатенена текстура | Сухо бластно стъклено перло | 0,80 до 1,00 |
D-2 | Текстуриран | Скучна текстура | Сух бласт #240 оксид | 1,00 до 2,80 |
D-3 | Текстуриран | Груба текстура | Сух бласт #24 оксид | 3.20 до 18.0 |
Разбиране на стандартите VDI 3400
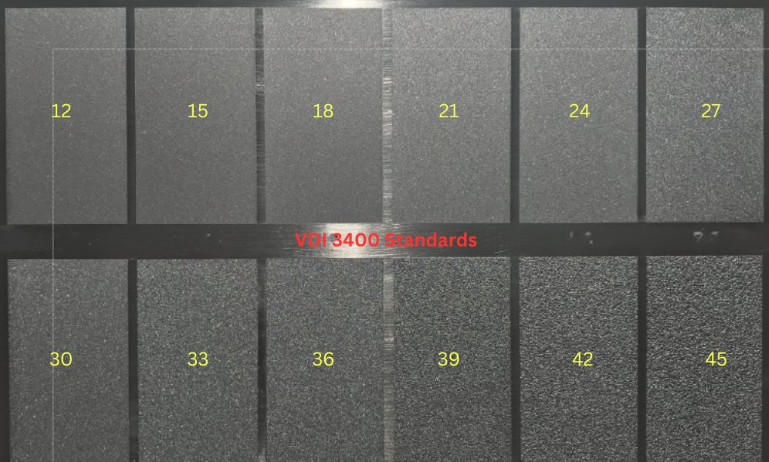
VDI 3400 стандартите произхождат от Verein Deutscher Ingenieure, Асоциацията на немските инженери. Тези стандарти капсулират набор от текстури от много гладка до силно текстурирана, което позволява прецизен контрол върху тактилните и визуални качества на шприцованата част. За разлика от SPI, VDI 3400 използва набор от 3D форми, които показват различни нива на грапавост, съответстващи на специфични степени, като напр. VDI 12 до VDI 45. Тези физически проби позволяват лесно сравнение и избор. Стандартите VDI 3400 се прилагат за различни материали и техники за обработка и са особено подходящи за постигане на сложни и детайлни текстури.
VDI стойност | Описание | Приложения | Грапавост на повърхността (Ra µm) |
VDI 12 | 600 камък | Ниско полирани части | 0.40 |
VDI 15 | 400 камък | Ниско полирани части | 0.56 |
VDI 18 | Сухо бластно стъклено перло | Сатенено покритие | 0.80 |
VDI 21 | Сух бласт # 240 оксид | Тъп завършек | 1.12 |
VDI 24 | Сух бласт # 240 оксид | Тъп завършек | 1.60 |
VDI 27 | Сух бласт # 240 оксид | Тъп завършек | 2.24 |
VDI 30 | Сух бласт # 24 оксид | Тъп завършек | 3.15 |
VDI 33 | Сух бласт # 24 оксид | Тъп завършек | 4.50 |
VDI 36 | Сух бласт # 24 оксид | Тъп завършек | 6.30 |
VDI 39 | Сух бласт # 24 оксид | Тъп завършек | 9.00 |
VDI 42 | Сух бласт # 24 оксид | Тъп завършек | 12.50 |
VDI 45 | Сух бласт # 24 оксид | Тъп завършек | 18.00 |
Mold-tech Стандарти за повърхностно покритие
Серия | Номер на текстурата | Дълбочина на текстурата (инчове) | Дълбочина на текстурата (mm) | Минимален ъгъл на газене | Описание |
MT-A | МТ-11010 | 0.001″ | 0,0254 мм | 1,5° | Фин матов пясъчен завършек |
MT-A | МТ-11020 | 0.0015″ | 0.0381 мм | 2,5° | Средно матово покритие |
MT-A | МТ-11030 | 0.002″ | 0,0508 мм | 3° | Грубо матово покритие |
MT-A | МТ-11040 | 0.003″ | 0.0762 мм | 4,5° | Много грубо матово покритие |
MT-A | МТ-11050 | 0.0045″ | 0.1143 мм | 6,5° | Агресивен матов финиш |
MT-B | МТ-11200 | 0.003″ | 0.0762 мм | 4,5° | Геометричен модел |
MT-B | МТ-11210 | 0.0035″ | 0,0889 мм | 5,5° | Геометричен модел |
MT-B | МТ-11220 | 0.004″ | 0,1016 мм | 6° | Геометричен модел |
MT-D | МТ-11550 | 0.0045″ | 0.1143 мм | 6,5° | Дървесна шарка |
MT-D | MT-11555 | 0.006″ | 0.1524 мм | 9° | Десен с груби дървесни зърна |
Как текстурата на мухъл влияе върху шприцованата част?
Текстурата на матрицата играе решаваща роля при определянето на естетиката и функционалността на формованите под налягане части. Той пряко влияе върху грапавостта на повърхността и може да доведе до различни производствени предизвикателства, ако не се управлява правилно.
Роля на повърхността на матрицата при инжекциите
The повърхност на матрица е от първостепенно значение при определяне на качеството на шприцована част. По време на процеса на формоване разтопеният пластмасов материал предава текстурата на повърхността на формата на крайния продукт. Степента на полиране върху повърхността на формата може да повлияе на адхезията на боята; силно полирана повърхност води до гланцово покритие, което може да е по-трудно за прилепване на боята, докато текстурирана повърхност предлага по-добро свързване на боята. По същия начин определени текстури могат да сведат до минимум появата на несъвършенства като линии на потока, които са видими линии на повърхността на формованата част, причинени от променливите скорости, с които тече разтопената пластмаса.
Постигане на желаната грапавост на повърхността
Процесите на текстуриране създават специфични шарки върху матрицата, които се пренасят върху повърхността на детайла. Тези модели могат да варират от много фини текстури, които леко променят блясъка на частта до тежки текстури, които създават забележима грапавост. Изборът на текстура трябва да съответства на предназначението на частта и очакванията за качество на крайния продукт. Например, подобна на кожа текстура може да се използва в автомобилни интериори за подобрено сцепление и луксозно усещане.
Често срещани проблеми и решения с покритието на матрицата
Линии на потока
Линиите на потока се появяват като вълнообразни шарки или разноцветни ивици по повърхността на формованата част. Те са причинени от вариации в скоростта на охлаждане на материала, докато тече през матрицата с различни скорости.
Решения:
- Увеличете скоростта на впръскване, налягането и температурата на материала, за да сте сигурни, че формата се запълва преди охлаждане
- Закръглете ъглите на матрицата, където дебелината на стената се увеличава, за да поддържате постоянен поток
- Преместете вратите на формата, за да създадете повече разстояние от охлаждащата течност на формата, за да предотвратите преждевременно охлаждане по време на потока
Струя
Струята се проявява като червееобразни завихряния близо до дебелите зони на вратата. Причинява се от температурни промени в потока на материала, често поради твърде малки затвори или твърде високи скорости на инжектиране.
Решения:
- Увеличете размера на портата и променете страничните порти на порти в скута
- Намалете скоростта на инжектиране, за да предотвратите прекомерно нагряване на материала при срязване
Марки от мивка
Следите от мивка са малки вдлъбнатини или трапчинки, които се появяват в по-дебели напречни сечения на детайла. Те възникват, когато вътрешната част се охлади и се свие по-бързо от външната част.
Решения:
- Увеличете налягането на впръскване и налягането на задържане, за да осигурите правилно опаковане
- Увеличете размера на портата или променете позицията ѝ
- Препроектирайте частта, за да има по-равномерна дебелина на стената, с ребра и издатини, които не надвишават 60% от номиналната дебелина
Как да изберете правилното повърхностно покритие за вашата шприцована част?
Съответствие на повърхностното покритие с изискванията на продукта
Крайната употреба на продукта диктува опции за повърхностно покритие. За елементи, изискващи висока естетика, като потребителски продукти, може да е необходимо гланцово покритие. Обратно, индустриалните части могат да се възползват от текстурирани покрития за подобрено сцепление или прилепване на боята. SPI завършва (Стандартите на Обществото на пластмасовата индустрия) като SPI A-2 често се използват, когато е необходим висок лак, докато покритието SPI C-1 може да е достатъчно за некозметични компоненти.
Ъгъл на газене
Включването на подходящия ъгъл на теглене в дизайна на частта не подлежи на обсъждане, за да се осигури правилно освобождаване на формата. По-стръмен ъгъл на газене ще улесни по-лесното изваждане от формата, което може да позволи използването на по-агресивни текстури, без да се рискува целостта на частта.
Материал за формоване
Избраният формовъчен материал влияе върху постижимото покритие на повърхността. По-твърдите пластмаси могат да постигнат по-високи нива на гланц, докато по-меките материали може да изискват различен подход за постигане на подобни ефекти. Дизайнерите на части трябва да разберат как материалът взаимодейства с финала, за да постигнат желаното качество.
Разходи за инструменти
По-високите нива на повърхностно покритие повишават разходите за инструменти поради увеличеното време за обработка и полиране. Продуктовите дизайнери трябва да балансират естетическите изисквания с икономическата осъществимост, като имат предвид, че някои покрития изискват по-сложни и трудоемки процеси на инструментална екипировка.
Материал на инструмента за мухъл
Материалът на инструмента за матрицата определя неговата дълготрайност и нивото на детайлност, което може да придаде. За дълги производствени серии или много детайлни покрития здравата инструментална стомана е от полза. В сценарии, при които спестяването на разходи е от първостепенно значение, могат да се използват алуминиеви форми, с предупреждението, че те могат да се износват по-бързо или да не постигнат същото ниво на детайлност като стоманата.