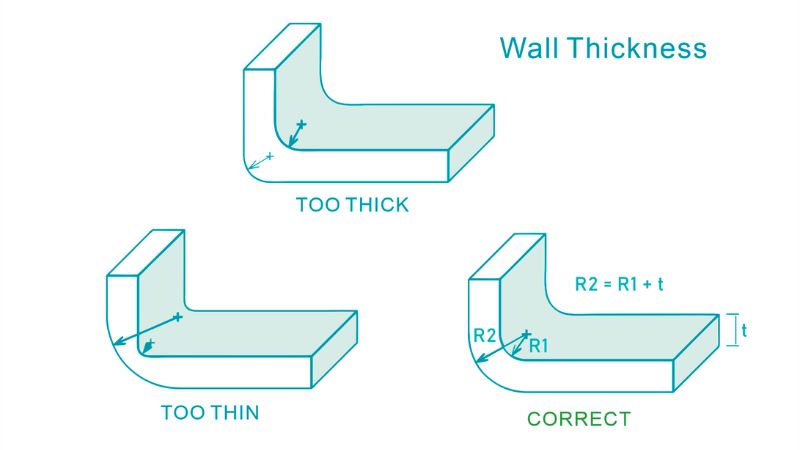
벽 두께의 기본 사항을 이해하는 것부터 재료별 고려 사항을 탐색하는 것까지, 이 가이드에서는 설계자, 엔지니어, 제조업체가 알아야 할 필수적인 측면을 다룹니다.
이 포괄적인 가이드는 사출 성형에서 적절한 벽 두께 설계의 중요성을 살펴보고, 모범 사례, 일반적인 과제 및 부품 생산 최적화 솔루션에 대한 통찰력을 제공합니다.
사출 성형에서 벽 두께란 무엇입니까?
벽 두께는 사출 성형 공정에서 중요한 설계 고려 사항으로, 성형되는 플라스틱 부품의 단면 두께를 나타냅니다.
이는 사출 성형에서 가장 중요한 설계 고려 사항 중 하나이며, 최종 부품의 제조 가능성, 비용, 품질 및 성능에 상당한 영향을 미치기 때문입니다.
벽 두께에 영향을 미치는 요소
사출성형 플라스틱 소재와 부품 구조의 벽 두께에는 두 가지 주요 요소가 영향을 미칩니다.
- 크기와 모양 – 일반적으로 큰 부품은 구조적 안정성을 위해 더 두꺼운 벽이 필요하지만, 작은 부품은 더 얇은 벽을 가질 수 있습니다. 복잡한 형상은 다양한 두께가 필요할 수 있습니다.
- 플라스틱 소재 – – 플라스틱마다 유동 특성과 냉각 속도가 다릅니다. 일반적으로 점도가 낮거나 용융 유동 속도가 높은 소재는 더 얇은 두께로 사용할 수 있습니다.
다양한 재료에 대한 최적의 벽 두께를 확인할 수 있는 차트는 다음과 같습니다.
재료 | 권장 벽 두께 범위 |
ABS | 0.045~0.140인치(1.14~3.56mm) |
아세탈(POM) | 0.030 – 0.120인치(0.76 – 3.05mm) |
아크릴(PMMA) | 0.025 – 0.500인치(0.64 – 12.7mm) |
나일론(PA) | 0.030 – 0.115인치(0.76 – 2.92mm) |
폴리카보네이트(PC) | 0.040 – 0.150인치(1.02 – 3.81mm) |
폴리에틸렌(PE) | 0.030 – 0.200인치(0.76 – 5.08mm) |
폴리프로필렌(PP) | 0.025 – 0.150인치(0.64 – 3.81mm) |
폴리스티렌(PS) | 0.035 – 0.150인치(0.89 – 3.81mm) |
벽 두께의 문제점은 무엇인가?
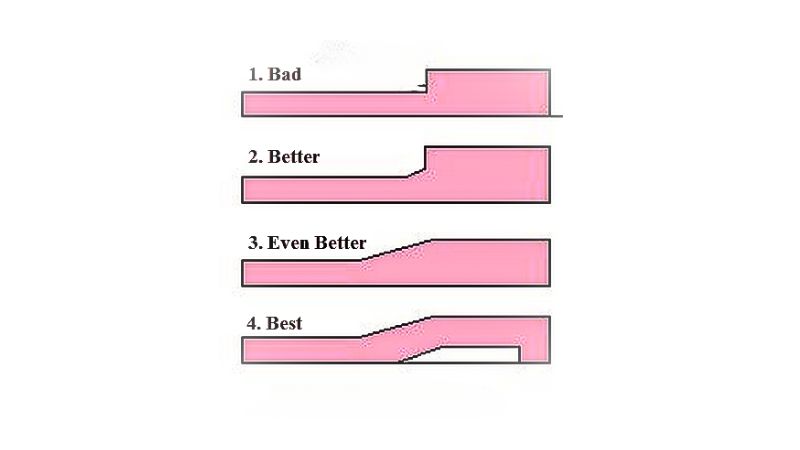
사출 성형에 적합한 벽 두께가 아니면 최종 제품에 여러 가지 결함이 생길 수 있습니다.
결함 | 원인 | 결과 |
뒤틀림 | 불균일한 벽 두께 | 냉각 속도의 차이로 인해 내부 응력이 발생하여 휘거나 뒤틀리는 현상이 발생합니다. |
싱크 마크 | 더 두꺼운 섹션 | 천천히 냉각하면 표면이 안쪽으로 가라앉아 작은 움푹 들어간 부분이 생깁니다. |
흐름선 | 벽 두께의 변화 | 용융 플라스틱의 흐름 속도가 다르면 표면에 눈에 띄는 줄무늬나 선이 나타납니다. |
짧은 샷 | 얇은 것에서 두꺼운 것으로의 전환 | 조기 냉각으로 인해 두꺼운 영역이 완전히 채워지지 않습니다. |
공극 | 두꺼운 섹션 | 공기 포집 또는 진공 포켓이 내부 공극을 형성합니다. |
제팅 | 너무 얇은 벽 | 빠른 플라스틱 흐름으로 인해 부품 표면에 뱀과 같은 패턴이 발생합니다. |
구조적 약점 | 일관되지 않은 벽 두께 | 부품의 강도와 무결성이 손상됩니다. |
치수 부정확성 | 두께 변화 | 불균일한 냉각으로 인해 부품이 지정된 치수를 충족하지 못하는 경우가 발생합니다. |
내부 스트레스 증가 | 다양한 벽 두께 | 냉각 속도가 다르면 내부 응력이 더 높아집니다. |
표면 결함 | 부적절한 벽 두께 | 잔물결이나 물결 모양과 같은 표면 결함을 유발합니다. |
균일한 벽 두께를 달성하기 위한 설계 고려 사항
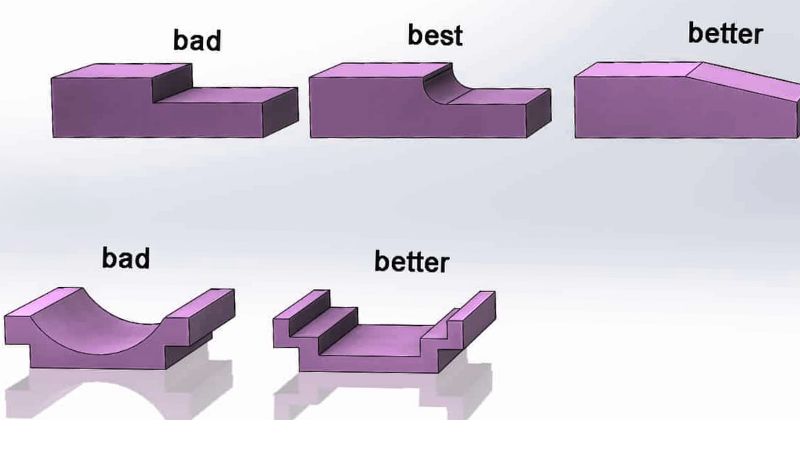
제조 가능성 설계(DFM) 분석은 내부 응력을 최소화하고 일관성을 개선하기 위한 최적의 균일한 두께를 식별하는 데 도움이 됩니다.
금형 충전 개선을 위한 드래프트 각도 활용
구배 각도는 사출 성형 부품 설계에 필수적이며, 완성된 부품을 금형에서 쉽게 분리할 수 있도록 도와줍니다. 구배 각도를 적용하는 것은 단순히 좋은 방법이 아니라, 균일한 벽 두께를 유지하는 데 매우 중요합니다.
권장되는 외부 드래프트 각도는 0.5~1.5도, 내부 각도는 0.5도이며, 이는 금형 충전 공정을 크게 향상시킬 수 있습니다.
이러한 미세한 각도는 재료가 더 원활하게 흐르게 하고, 부품 내 다양한 결함의 근원이 되는 불균일한 벽 두께 형성을 방지합니다.
불균일한 벽 두께로 인한 내부 응력 해결
벽 두께의 차이는 부품이 냉각되고 응고될 때 내부 응력으로 이어질 수 있습니다. 벽 두께가 두꺼운 부분은 냉각 속도가 느려 수축률 차이가 발생하여 부품이 휘거나 변형될 수 있습니다.
이러한 응력을 균등하게 분산시키고 잠재적인 품질 문제를 방지하려면 제품 전체의 두께가 균일해야 합니다.
부품을 설계할 때는 고위험 영역을 고려하고 일관된 벽 두께를 적용하여 내부 응력 형성을 완화해야 합니다.
권장 두께 - 최소
최소 벽 두께는 사용되는 특정 플라스틱 소재와 부품의 크기/복잡성에 따라 달라집니다.
일반적으로:
소형 부품과 효율적인 대량 생산의 경우 최소 0.025~0.030인치(0.64~0.76mm)의 벽 두께가 권장됩니다.
더 큰 부품의 경우 최소 0.040~0.050인치(1.0~1.3mm)가 제안됩니다.
기존 사출 성형의 실제 최소 벽 두께는 0.030~0.040인치(0.76~1.0mm)입니다.
일부 특수 박벽 성형 분야에서는 0.010인치(0.25mm)만큼 얇은 벽을 만들 수 있지만, 이를 위해서는 높은 압력이 필요하고 부품 크기가 제한됩니다.
권장 두께 - 최대
가능하다면 사출 성형에서 지나치게 두꺼운 벽은 피해야 합니다. 지나치게 두꺼운 벽은 결함과 비효율성을 초래할 수 있기 때문입니다.
일반적인 지침은 다음과 같습니다.
대부분의 사출 성형 부품의 최대 벽 두께는 0.125~0.250인치(3.2~6.4mm)입니다.
0.250인치(6.4mm)보다 두꺼운 벽은 싱크 마크, 공동, 잔류 응력 및 뒤틀림의 위험이 더 높습니다.
일부 특수 응용 분야에서는 최대 4.5인치(114mm)의 벽 두께가 가능하지만 매우 긴 사이클 시간이 필요합니다.
효율성과 품질을 위한 모범 사례로, 대부분 부품에 대해 최대 벽 두께를 0.125~0.160인치(3.2~4.0mm)로 하는 것이 좋습니다.
성형 부품의 벽 두께 문제를 해결하는 방법
사출 성형 부품의 두꺼운 벽 부분 처리
이를 완화하려면 빠른 냉각을 용이하게 하면서도 충분한 강도를 제공하는 두께를 유지하는 것이 좋습니다. 예를 들어, 두께 8mm PA6 소재의 경우 총 사출 성형 사이클은 약 93초이며, 냉각에는 약 70초가 소요됩니다.
두꺼운 벽으로 인해 사이클 시간이 길어지는 문제를 극복하기 위해 코어 아웃(core out)이라는 기술을 사용하는 것이 효과적일 수 있습니다. 코어 아웃은 부품의 무결성이나 강도를 손상시키지 않으면서 두꺼운 벽에 빈 공간을 만드는 기술입니다.
부품 무결성을 손상시키지 않고 얇은 벽을 처리하는 방법
제품 설계자는 부품의 무결성을 손상시키지 않으면서 필요한 최소한의 벽 두께로 부품을 설계하는 것이 좋습니다.
더 얇은 벽을 설계하려면 결함을 방지하기 위해 재료의 흐름 특성을 철저히 이해해야 합니다.
사출 압력, 금형 온도, 리브나 거셋과 같은 디자인 요소를 포함하는 등의 요소는 얇은 벽의 부품을 지지하는 데 도움이 되어 성형성을 향상시키고 뒤틀림, 가라앉음 또는 기포 발생 가능성을 줄일 수 있습니다.