Deux résines plastiques différentes sont moulées ensemble en un seul cycle d'usinage au cours du processus de moulage par double injection, également connu sous le nom de double injection, double injection, multi injection et surmoulage.
Une technique de fabrication de pointe appelée double injection, également connue sous le nom de moulage à deux matériaux, à deux injections ou moulage à deux K, est utilisée pour créer des pièces moulées complexes à partir de deux matériaux différents.
Lors du moulage par injection en deux temps, nous contrôlons soigneusement l'injection de nombreux matériaux, y compris deux types de résine distincts, dans un moule unique à plusieurs chambres en utilisant une technique hautement spécialisée et automatisée.
Processus de moulage à deux coups
Une machine de moulage par injection est utilisée dans le processus de moulage en deux étapes où deux matériaux sont « surmoulés » dans un cycle de moulage. La quantité de matière injectée dans la cavité de moulage est appelée « injection ».
Dans le moulage par injection à deux coups, une première section est moulée, et une fois terminée, une deuxième partie est injectée pour créer la partie finale du moulage. Les deux pièces doivent être comparables (chimiquement) pour que le processus de moulage en deux étapes réussisse et que le collage ait lieu.
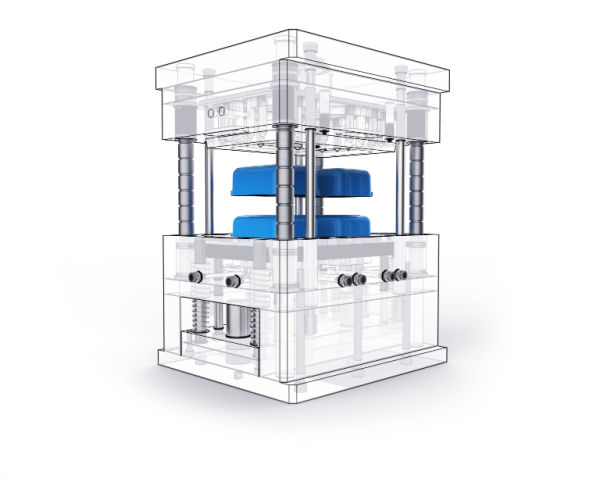
Une pièce en matériau dur peut être assemblée à une pièce en matériau souple par moulage par injection en deux temps. Dans un moule à deux cavités, la procédure combine le moulage de deux composants. Il peut améliorer considérablement l'attrait du produit en termes de toucher, de couleur, etc. Il existe de nombreuses possibilités de conception différentes avec le moulage en deux temps.
La technique de moulage par injection en deux temps est divisée en deux étapes. Le premier implique une injection de résine dans un moule, qui est ensuite refroidi pour créer un objet solide, un peu comme le moulage par injection traditionnel.
L'objet nouvellement moulé est transporté vers un deuxième moule dans la deuxième étape à l'aide d'un plateau rotatif ou d'un bras robotisé. Selon la conception, la pièce nouvellement moulée reçoit ensuite une deuxième injection de résine dans, à travers ou autour de zones spécifiques du premier moule.
Suite à la formation d'un lien moléculaire entre les deux résines plastiques, l'objet moulé multi-résines est refroidi et expulsé.
Bien que la procédure soit simple à comprendre, sa maîtrise est difficile. Même les erreurs les plus infimes peuvent entraîner des pertes financières importantes en raison des niveaux élevés de compétence technique et d'attention aux détails requis, en particulier dans les circonstances de fabrication à volume élevé.
C'est pourquoi il est important de choisir un fournisseur aux compétences exceptionnelles. D'excellents tableaux de bord de la qualité des fournisseurs ont établi des processus pour empêcher le flash, les lignes de flux, les plans courts et les plans de sauvegarde d'augmenter la capacité, car votre entreprise et vos besoins d'expansion de moulage à deux coups sont tout ce qu'il faut rechercher.
Ce processus rend le moulage en deux étapes idéal pour les interrupteurs, les boutons, les brosses à dents et les bouchons de conteneurs.
Applications du moulage à deux coups
Pour les produits en plastique complexes, de plusieurs couleurs et multi-matériaux, en particulier dans les circonstances de fabrication à grand volume, le moulage par injection en deux temps est la meilleure technique de moulage du plastique.
De plus, le processus de moulage en deux étapes est appliqué dans le secteur automobile pour fabriquer une large gamme de produits et de pièces. D'autres articles fabriqués à l'aide du processus de double tir comprennent des outils de pelouse et de jardin et du matériel agricole.
Les pièces moulées en deux parties sont utilisées dans presque toutes les industries, des biens de consommation à la construction, mais elles sont le plus souvent utilisées dans les situations nécessitant les éléments suivants :
- pièces ou composants pouvant bouger
- surfaces rigides avec poignées flexibles
- soit amortissement acoustique ou vibration
- explications ou identifications superficielles
- composants avec plusieurs matériaux ou couleurs
Idéalement, le processus de moulage par injection en deux temps est utilisé pour les pièces complexes comportant plusieurs composants.
Avantages du processus de moulage à deux coups
Les polymères plastiques sont utilisés dans une gamme de processus de production, tels que l'extrusion, le moulage thermodurcissable par compression et le moulage par injection en deux temps. Bien que chacune soit une méthode de fabrication réalisable, de nombreux fabricants de plastiques utilisent cette méthode en raison de plusieurs avantages.
Afin de créer le premier segment du produit, un matériau est d'abord injecté dans un moule. Une seconde injection d'un matériau secondaire compatible avec le premier s'ensuit. Il existe plusieurs raisons pour lesquelles de nombreuses entreprises choisissent de produire des plastiques ou des polymères de cette manière.
Voici quelques avantages du processus de moulage en deux étapes :
Polyvalent
Les fabricants de produits préfèrent le moulage par injection en deux temps pour une variété d'applications, y compris les pièces intérieures automobiles, l'équipement médical, les outils et les jouets. Il permet aux fabricants de mélanger une multitude de composants et de teintes pour produire un produit robuste et esthétique.
Des matériaux comme le silicone et les thermoplastiques, le nylon et les élastomères thermoplastiques, ou le nylon rigide et les matériaux doux au toucher sont quelques exemples de matériaux qui peuvent être mélangés avec succès avec cette procédure.
Rentable
Avec le premier moule tourné à l'écart et le deuxième moule placé autour du produit de sorte que le deuxième thermoplastique compatible puisse être injecté dans le deuxième moule, la procédure en deux étapes ne nécessite qu'un seul cycle de machine.
La méthode produit plus de produits à chaque fois pour moins d'argent et nécessite moins de travailleurs pour produire le produit fini car elle utilise un seul cycle de machine plutôt que plusieurs cycles de machine. De plus, il garantit une liaison solide entre les matériaux, éliminant ainsi le besoin d'un assemblage ultérieur.
Produit de haute qualité
La majorité des produits thermoplastiques bénéficient du moulage par injection en deux temps de nombreuses manières :
- Esthétique améliorée. Lorsque les produits sont fabriqués à partir de plastiques ou de polymères de différentes couleurs, ils sont plus beaux et plus attrayants pour les consommateurs. Le produit paraîtra plus cher si plus d'une couleur ou texture est utilisée.
- Meilleure ergonomie. La méthode permet des surfaces douces au toucher; ainsi, les produits finis peuvent avoir des poignées ou d'autres sections ergonomiques. Ceci est crucial pour les outils, les équipements médicaux et autres objets portables.
- Le joint est amélioré lorsque des polymères de silicone et d'autres matériaux caoutchouteux sont utilisés pour les joints et autres pièces qui nécessitent un joint étanche.
- Il permet aux polymères durs et mous de produire des articles de la plus petite taille qui offrent un confort et une utilité exceptionnels.
- Par rapport au surmoulage ou aux méthodes d'insertion plus conventionnelles, il peut réduire considérablement le nombre de désalignements.
- Il permet aux producteurs d'utiliser plusieurs matériaux qui ne peuvent pas être efficacement collés à l'aide d'autres procédures pour créer des modèles de moules plus complexes.
- La liaison formée est incroyablement forte, ce qui rend le produit final plus robuste, fiable et durable.
Le processus de moulage en deux étapes aide les fabricants à obtenir des produits de haute qualité.
Consolidation de pièces
Le nombre de pièces dans un assemblage fini est réduit grâce au moulage par injection en deux étapes, ce qui permet d'économiser en moyenne $40K USD en dépenses de développement, d'ingénierie et de validation pour chaque numéro de pièce augmenté.
Efficace
Avec le moulage à deux coups, plusieurs composants peuvent être moulés avec un seul outil, ce qui nécessite moins de travail pour produire vos pièces et aucune soudure ou assemblage des composants après moulage.
Types de structures de moulage à deux coups
Choisir et se retrouver avec la structure de moule appropriée est essentiel pour économiser sur les coûts et garantir la qualité. Voici quelques types de structures de moulage à deux billes :
Moule à deux coups à bascule de base
Étant donné que le noyau et la cavité du moule n'ont pas besoin d'être déplacés, la procédure de moulage multi-coups à bascule du noyau est la plus simple. Alternativement, le déplacement du curseur modifiera la géométrie de la cavité du moule.
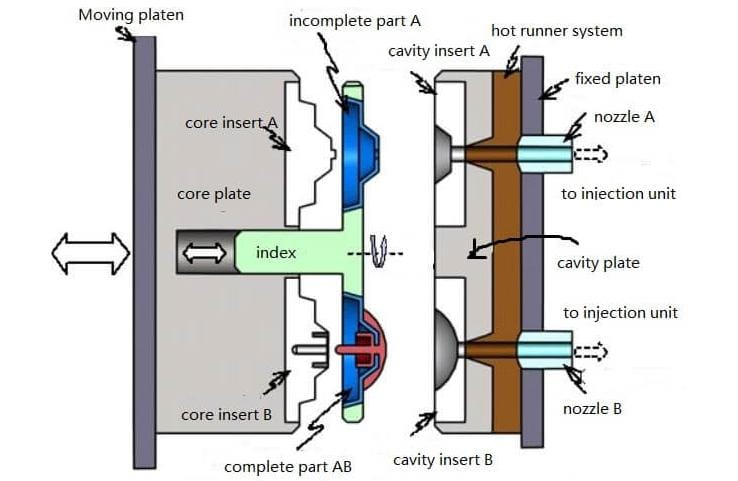
La substance A est d'abord injectée dans la cavité lorsque le curseur est dans sa position déployée pendant le processus de moulage par injection à l'aide du moule à deux coups à bascule centrale. Tirez ensuite le curseur vers l'arrière pour exposer une nouvelle zone de la cavité.
L'espace restant est rempli en déplaçant le curseur après que le matériau B a été injecté dans la cavité modifiée à travers une porte différente (au-dessus de la buse centrale).
Le composant en plastique est ensuite expulsé du moule après durcissement. Circulation dans le même ordre que ci-dessus pour poursuivre le moulage.
Bien que le prix de l'outil augmente lorsqu'un curseur est ajouté au moule, il peut toujours être nettement moins cher que les moules à plateau rotatif ou à arbre rotatif. Malheureusement, il est incapable de fabriquer des pièces en plastique complexes et multicolores.
Moule à deux coups à plateau rotatif
Sur la ligne médiane du plateau, qui est parallèle à l'axe de rotation, la plaque de noyau de moule a deux noyaux identiques qui sont des images miroir l'un de l'autre. Deux cavités avec diverses géométries sont incluses dans la plaque de cavité fixée au plateau fixe.
Le plateau rotatif complète la commutation des pièces moulées à chaque cycle, sans commutation humaine.
Le moule, qui peut contenir plus de matériaux, n'apparaît ici qu'avec les deux matériaux. Selon la quantité de matériau utilisée, le plateau rotatif peut être tourné de 90°, 120° ou 180°. Une machine d'injection spécifique est également nécessaire pour produire la rotation nécessaire côté cœur.
Structure de moule à deux coups de bascule
Avec un côté montant, l'autre descendant, et ainsi de suite, la structure de la dalle est composée de deux côtés tournant autour du centre. La plupart des conceptions de moules de clavier avec des chiffres et des lettres utilisent la structure en dents de scie.
La structure contient des caractères numériques ou alphabétiques fermés tels que 0, 4, 8, A, B, D et O. Le matériau secondaire ne peut entrer facilement dans la région confinée que lorsqu'une construction à bascule est utilisée, créant une belle apparence.
La structure en dents de scie fonctionne comme suit :
- Après une injection, le moule est ouvert.
- L'aiguille cassée est abaissée par la tige de poussée, ce qui fait tourner la bascule autour de l'arbre rotatif.
- La plaque supérieure est poussée vers le haut en poussant la bascule, ce qui fait sortir l'aiguille cassée du moule.
Un trou brisé est créé lorsque l'aiguille s'élève au bord de la partie scellée du produit primaire. Pour percer le matériau secondaire dans la zone fermée à partir du trou cassé, l'aiguille est déplacée plus bas par la goupille de retour de la plaque fracturée pendant le processus de moulage par double injection.
Structure coulissante de la cavité
La cavité du modèle mâle glisse sous l'influence du moteur lors de l'ouverture du moule après une injection. Une distance spécifiée est utilisée pour aligner le moule avec le moule maître avant le deuxième processus de moulage par injection.
Facteurs à prendre en compte lors de l'utilisation du moulage à deux injections
Les facteurs suivants sont pris en compte lors de l'utilisation d'un moulage à double injection :
Sélection des matériaux
La résistance physique, mécanique, chimique, thermique, électrique, à l'inflammabilité et aux UV sont toutes des considérations importantes lors de la sélection d'un matériau pour votre composant. Vous devrez fournir des réponses à un certain nombre de questions afin de cibler votre sélection de matériaux, notamment :
- À quelles températures votre produit sera-t-il soumis ?
- Dans quelle mesure avez-vous besoin que le matériau soit flexible ou rigide pour le pliage ?
- Résistance aux chocs : Quelle doit être la robustesse de sa surface ?
- Dans quelle mesure résiste-t-il à de grosses charges en termes de résistance à la compression ?
- Le composant sera-t-il exposé aux rayons UV, comme ceux que l'on trouve à l'extérieur ?
- La pièce sera-t-elle exposée à des produits chimiques qui affecteront son bon fonctionnement, en particulier au fil du temps ?
- Quelle sorte de durée de conservation est requise pour la pièce?
Compatibilité matérielle
La chimie des matériaux est cruciale à prendre en compte lors du choix de ceux à utiliser pour le moulage en deux temps. Alors que certains matériaux se lient imparfaitement, d'autres fonctionnent bien ensemble et créent une adhérence moléculaire solide.
Effectuez un test d'adhérence avant de commencer la fabrication lorsque la propriété adhésive de deux composés n'est pas claire. Lorsque la liaison est insuffisante, des correctifs peuvent être incorporés dans la conception, tels que des contre-dépouilles, des rainures ou des épaulements, pour augmenter l'adhérence et verrouiller les deux composés ensemble.
Un tableau de compatibilité des matériaux est examiné pour déterminer quels polymères s'accrocheront les uns aux autres et quels polymères sont incompatibles. De plus, cela élimine la possibilité de contamination, ce qui est un problème lors de l'utilisation de deux moules différents.
De plus, par rapport à la production d'un produit ou d'une pièce identique à l'aide de deux processus de moulage différents, la procédure de moulage en deux étapes permet d'obtenir une liaison beaucoup plus solide. La possibilité de fabriquer des produits en plastique multicolores à l'aide de la méthode de moulage en deux temps est l'un des avantages supplémentaires du procédé par rapport à la peinture, qui peut perdre de son efficacité avec le temps.
Vous pouvez créer des éléments plus utiles et sophistiqués en utilisant l'approche en deux temps. De plus, du plastique plus mou peut être mélangé avec du plastique dur. Le produit a une intégrité nettement supérieure. Les produits de moulage en plastique à deux injections sont souvent beaucoup plus durables et résistants aux chocs.
La méthode est également excellente pour fabriquer des poignées souples pour les équipements électriques, les joints et les joints de climatisation et les surfaces antidérapantes. Avec cette méthode, des logos peuvent être créés qui, contrairement aux logos peints, ne s'effaceront jamais.
Arrêts
Pour former des trous, des fonctions d'encliquetage et de longs trous traversants, le moule ferme ces endroits pour empêcher le plastique de s'écouler dans ces endroits.
Dans ces situations, les deux moitiés du moule se scellent l'une contre l'autre. De ce fait, les faces d'étanchéité du moule peuvent s'ouvrir et se fermer sans se heurter. Trois à cinq degrés devraient être l'angle de dépouille minimum. Plus la moisissure vit longtemps, plus le dégagement est élevé et plus le tirage est important.
Type de porte
La résine fondue pénètre dans la chambre du moule par un canal de porte lors de l'utilisation du moulage par injection. Pour obtenir les proportions idéales des pièces et l'aspect esthétique tout en empêchant le gauchissement, le type de portail, la conception et l'emplacement doivent être pris en compte.
Les portes à languettes et à canaux chauds sont les deux types de portes les plus fréquemment utilisées dans le moulage par injection :
- Les portes les plus populaires et les plus efficaces sont les portes à onglets ; cependant, parce qu'ils sont si simples, ils pourraient ne pas être adaptés à vos besoins.
- Les portes à pointe chaude comportent de minuscules ouvertures elliptiques. La résine est maintenue suffisamment chaude pour passer à travers le trou de porte étroit par le réchauffeur contrôlé par thermostat fixé à l'arrière du moule.
Liaison chimique moléculaire
Pour qu'une liaison moléculaire forte soit possible, votre substrat et la résine de seconde injection doivent idéalement être chimiquement compatibles. La jambe ou la surface la plus longue est idéale pour le joint entre les deux résines. Le deuxième coup est presque impossible à supprimer en sélectionnant les matériaux et la conception de joint idéaux.
Même lorsqu'une liaison chimique de haut niveau peut être obtenue, nous vous conseillons fortement d'utiliser une liaison mécanique appropriée si la liaison est importante pour votre application.
Emplacement de la porte
Ceci est essentiel pour produire des cosmétiques à surface solide et un moule homogène. Dans le moulage par injection monocoup, la masse fondue peut pénétrer par la partie la plus épaisse de l'ouverture avant de s'écouler vers les zones plus petites, grâce au placement de la porte.
Suggestions pour le moulage à deux coups
Voici quelques recommandations pour le moulage à deux coups :
Numéro 1
Le plastique souple est moulé une seconde fois après avoir été moulé pour la première fois en plastique dur. La première fois est transparente ; la deuxième fois non. Le premier moulage se fait avec un plastique haute température, tandis que le double moulage se fait avec un plastique basse température.
Numéro 2
Testez le moule pour créer un produit fini avant la production réelle.
Numéro 3
Avant la fabrication du moule, trouvez tous les défauts potentiels et corrigez-les.
Numéro 4
Prendre en compte le rétrécissement des deux matériaux. De manière générale, le matériau initialement créé affecte le retrait.
Numéro 5
Une deuxième injection ne peut être administrée qu'une fois que la première a pleinement fait effet.
Numéro 6
Pour éviter tout dommage pendant le processus de moulage, considérez la position moulée.
Numéro 7
Laissez le bord de la première pièce moulée par injection être excessivement grand. Cela garantit que la deuxième injection aura une pression plus élevée.
Numéro 8
Vérifiez que les paramètres de l'unité d'injection donnent la pression, le débit et la capacité de refroidissement nécessaires.
Numéro 9
Assurez-vous que l'intégrité structurelle de la première pièce moulée peut survivre à la pression d'injection du second moulage.
Conclusion
Les personnes qui ne sont pas familiarisées avec le moulage par injection en deux temps pourraient penser que c'est difficile. Cela implique un deuxième matériau et une deuxième procédure, ce qui ajoute un autre facteur à la création de composants, mais c'est relativement facile.
Le moulage en deux temps peut être effectué à l'aide d'un plateau rotatif, d'un noyau mobile ou d'un surmoulage, entre autres options. Les deux premiers nécessitent deux processus, deux systèmes de canaux et une seconde unité d'injection.
Ce dernier utilise souvent deux moules différents, un pour chaque matériau, mais peut également être réalisé à l'aide d'un seul moule, de deux systèmes de canaux et d'un transfert de pièces manuel ou automatisé.